What is FR4?
FR4 is a type of material used in the manufacturing of printed circuit boards (PCBs). It is a composite material made up of woven fiberglass cloth with an epoxy resin binder that is flame resistant. The “FR” in FR4 stands for “Flame Retardant”, while the “4” represents the woven glass reinforcement used in the material.
FR4 has become the primary insulating substrate upon which the vast majority of rigid PCBs are produced. The material is known for its excellent mechanical, electrical, and thermal properties, making it ideal for use in a wide range of electronic applications.
Composition of FR4
FR4 is composed of two main components:
- Woven fiberglass cloth
- Epoxy resin binder
The fiberglass cloth provides the material with its strength and dimensional stability, while the epoxy resin acts as a binder and provides the material with its flame-retardant properties.
Woven Fiberglass Cloth
The woven fiberglass cloth used in FR4 is typically made from E-glass, which is a type of glass that is known for its excellent electrical insulation properties. The fiberglass is woven into a cloth that is then impregnated with the epoxy resin binder.
Epoxy Resin Binder
The epoxy resin binder used in FR4 is a thermoset polymer that is mixed with a hardener and other additives to provide the material with its desired properties. The epoxy resin is what gives FR4 its flame-retardant properties, as well as its excellent mechanical and thermal stability.
Properties of FR4
FR4 has several properties that make it an ideal material for use in PCBs:
- Excellent electrical insulation properties
- High mechanical strength and stiffness
- Good thermal stability
- Flame retardant
- Resistant to moisture and chemicals
Property | Value |
---|---|
Dielectric Constant @ 1 MHz | 4.7 |
Dissipation Factor @ 1 MHz | 0.02 |
Dielectric Strength (kV/mm) | 20 |
Thermal Conductivity (W/m·K) | 0.3 |
Glass Transition Temperature (°C) | 135 |
Flexural Strength (MPa) | 415 |
Density (g/cm³) | 1.85 |
These properties make FR4 suitable for use in a wide range of applications, including:
- Consumer electronics
- Automotive electronics
- Aerospace electronics
- Medical devices
- Industrial controls
Is FR4 a Polyimide?
While FR4 and polyimide are both used in the manufacturing of PCBs, they are not the same material. FR4 is a composite material made up of woven fiberglass cloth and an epoxy resin binder, while polyimide is a type of polymer that is known for its excellent thermal and mechanical properties.
What is Polyimide?
Polyimide is a type of polymer that is known for its excellent thermal and mechanical properties. It is a thermoplastic material that is often used in high-temperature applications, such as in the aerospace and automotive industries.
Polyimide has several properties that make it an attractive material for use in PCBs:
- High glass transition temperature (Tg)
- Excellent thermal stability
- High mechanical strength and stiffness
- Good electrical insulation properties
- Resistant to chemicals and radiation
Property | Value |
---|---|
Glass Transition Temperature (°C) | 360-410 |
Thermal Decomposition Temperature (°C) | 520-620 |
Dielectric Constant @ 1 MHz | 3.5 |
Dissipation Factor @ 1 MHz | 0.002 |
Dielectric Strength (kV/mm) | 22 |
Tensile Strength (MPa) | 231 |
Elongation at Break (%) | 72 |
Density (g/cm³) | 1.42 |
Differences Between FR4 and Polyimide
While both FR4 and polyimide are used in the manufacturing of PCBs, they have some key differences:
-
Composition: FR4 is a composite material made up of woven fiberglass cloth and an epoxy resin binder, while polyimide is a type of polymer.
-
Thermal Properties: Polyimide has a higher glass transition temperature and thermal decomposition temperature than FR4, making it more suitable for high-temperature applications.
-
Mechanical Properties: Polyimide has higher mechanical strength and stiffness than FR4, but FR4 has better dimensional stability.
-
Cost: FR4 is generally less expensive than polyimide, making it a more cost-effective choice for many applications.
-
Processing: FR4 is easier to process than polyimide, as it can be drilled and machined using standard PCB manufacturing techniques. Polyimide requires specialized processing techniques due to its high temperature resistance.
Applications of FR4 and Polyimide in PCBs
Both FR4 and polyimide are used in the manufacturing of PCBs, but they are typically used in different applications.
Applications of FR4 in PCBs
FR4 is the most commonly used material in the manufacturing of rigid PCBs. It is used in a wide range of applications, including:
- Consumer electronics (e.g. smartphones, laptops, televisions)
- Automotive electronics (e.g. engine control units, infotainment systems)
- Industrial controls (e.g. PLCs, sensors, actuators)
- Medical devices (e.g. patient monitors, imaging equipment)
FR4 is preferred in these applications due to its excellent electrical insulation properties, high mechanical strength and stiffness, and good thermal stability. It is also relatively inexpensive compared to other PCB materials, making it a cost-effective choice for many applications.
Applications of Polyimide in PCBs
Polyimide is typically used in high-temperature and high-reliability applications where the PCB needs to withstand extreme environmental conditions. Some examples of applications where polyimide is used include:
- Aerospace electronics (e.g. satellite systems, aircraft avionics)
- Automotive electronics (e.g. under-the-hood applications, brake systems)
- Oil and gas exploration (e.g. downhole drilling equipment)
- High-temperature industrial applications (e.g. power electronics, motor drives)
Polyimide is preferred in these applications due to its excellent thermal stability, high mechanical strength and stiffness, and resistance to chemicals and radiation. However, it is more expensive than FR4 and requires specialized processing techniques, which can limit its use in some applications.
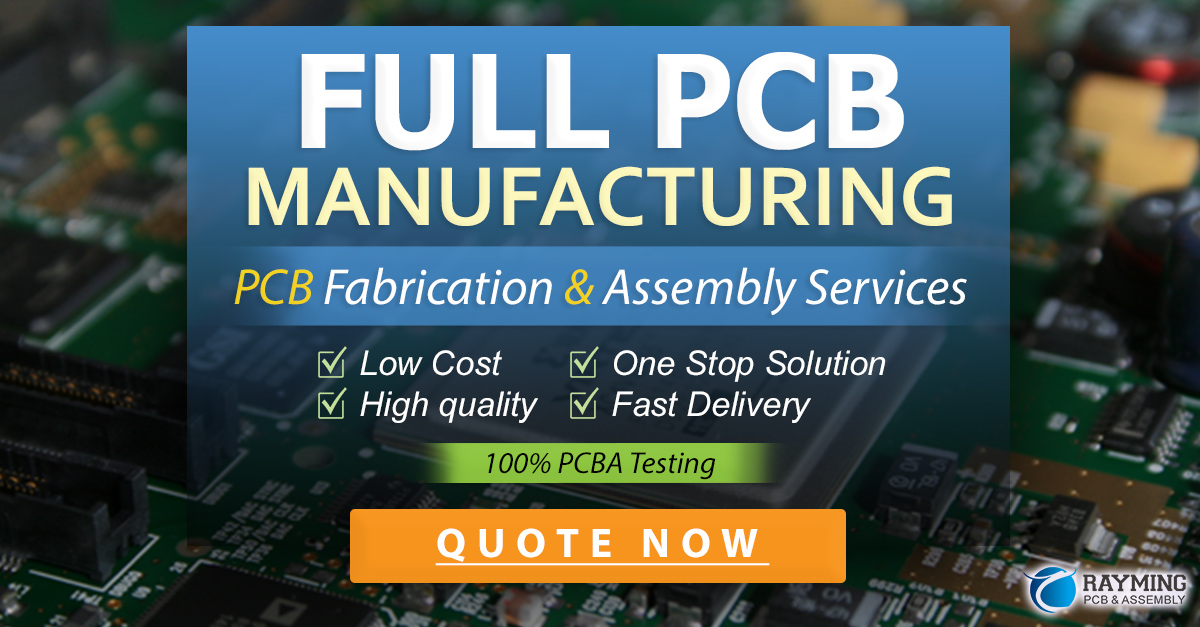
FAQ
-
What does FR4 stand for?
FR4 stands for “Flame Retardant 4”, where the “4” represents the woven glass reinforcement used in the material. -
What is the difference between FR4 and polyimide?
FR4 is a composite material made up of woven fiberglass cloth and an epoxy resin binder, while polyimide is a type of polymer. Polyimide has a higher glass transition temperature and thermal decomposition temperature than FR4, making it more suitable for high-temperature applications. However, FR4 is less expensive and easier to process than polyimide. -
What are the key properties of FR4?
The key properties of FR4 include excellent electrical insulation, high mechanical strength and stiffness, good thermal stability, flame retardance, and resistance to moisture and chemicals. -
What are the typical applications of FR4 in PCBs?
FR4 is commonly used in consumer electronics, automotive electronics, industrial controls, and medical devices due to its excellent properties and cost-effectiveness. -
What are the advantages of using polyimide in PCBs?
Polyimide is preferred in high-temperature and high-reliability applications due to its excellent thermal stability, high mechanical strength and stiffness, and resistance to chemicals and radiation. It is commonly used in aerospace electronics, automotive electronics, oil and gas exploration, and high-temperature industrial applications.
Conclusion
In conclusion, while FR4 and polyimide are both used in the manufacturing of PCBs, they are not the same material. FR4 is a composite material made up of woven fiberglass cloth and an epoxy resin binder, while polyimide is a type of polymer known for its excellent thermal and mechanical properties.
FR4 is the most commonly used material in the manufacturing of rigid PCBs due to its excellent electrical insulation properties, high mechanical strength and stiffness, good thermal stability, and cost-effectiveness. It is used in a wide range of applications, including consumer electronics, automotive electronics, industrial controls, and medical devices.
Polyimide, on the other hand, is typically used in high-temperature and high-reliability applications where the PCB needs to withstand extreme environmental conditions. It is preferred in aerospace electronics, automotive electronics, oil and gas exploration, and high-temperature industrial applications due to its excellent thermal stability, high mechanical strength and stiffness, and resistance to chemicals and radiation.
When selecting between FR4 and polyimide for a PCB application, it is important to consider the specific requirements of the application, including the operating temperature range, mechanical and thermal stresses, and environmental conditions. By understanding the properties and differences between these two materials, designers can make informed decisions and select the best material for their specific application.
No responses yet