What is FR4?
FR4 is a type of material widely used in the electronics industry for the production of printed circuit boards (PCBs). It is a composite material made from woven fiberglass cloth with an epoxy resin binder that is flame resistant. The “FR” in FR4 stands for “Flame Retardant,” and the “4” indicates the woven glass reinforcement used in the material.
Composition of FR4
FR4 is composed of two main components:
- Woven fiberglass cloth: This provides the structural strength and dimensional stability to the material.
- Epoxy resin: This acts as a binder and fills the spaces between the fiberglass threads, creating a solid and durable material.
The combination of these components results in a material with excellent mechanical, electrical, and thermal properties, making it suitable for various applications in the electronics industry.
Properties of FR4
FR4 has several key properties that make it an ideal choice for PCB manufacturing:
- Flame resistance: FR4 is designed to be flame retardant, which is crucial for safety in electronic devices.
- Electrical insulation: The material has excellent electrical insulation properties, preventing short circuits and ensuring proper functioning of electronic components.
- Mechanical strength: FR4 has high tensile and flexural strength, making it resistant to bending and cracking.
- Dimensional stability: The material maintains its shape and size under various environmental conditions, such as temperature changes and humidity.
- Heat resistance: FR4 can withstand high temperatures, allowing it to be used in soldering processes and other high-temperature applications.
Is FR4 a Plastic?
While FR4 is often referred to as a “plastic” in informal contexts, it is not a pure plastic material in the strict sense of the term. Plastics are typically synthetic materials made from organic polymers, such as polyethylene, polypropylene, or polystyrene. These materials are entirely composed of a single polymer or a blend of polymers.
In contrast, FR4 is a composite material that combines woven fiberglass cloth with an epoxy resin binder. The epoxy resin is indeed a type of thermoset plastic, but the presence of the fiberglass reinforcement sets FR4 apart from conventional plastics.
Thermoset vs. Thermoplastic
Plastics can be broadly categorized into two types: thermosets and thermoplastics. The epoxy resin used in FR4 is a thermoset plastic, which means that it undergoes an irreversible chemical reaction during the curing process. Once cured, thermoset plastics cannot be melted or reshaped, unlike thermoplastics.
Thermoplastics, on the other hand, can be melted and reshaped multiple times without significant changes to their chemical structure. Common examples of thermoplastics include polyethylene, polypropylene, and nylon.
Composite Material Classification
FR4 is more accurately classified as a composite material rather than a plastic. Composite materials are made by combining two or more distinct materials to achieve specific properties that are superior to those of the individual components. In the case of FR4, the combination of woven fiberglass and epoxy resin results in a material with enhanced mechanical, electrical, and thermal properties compared to either component alone.
Other examples of composite materials include:
- Carbon fiber reinforced polymers (CFRP)
- Glass fiber reinforced polymers (GFRP)
- Metal matrix composites (MMC)
- Ceramic matrix composites (CMC)
Applications of FR4
FR4 is widely used in the electronics industry, particularly in the manufacturing of printed circuit boards (PCBs). PCBs are essential components in almost all electronic devices, from smartphones and computers to industrial control systems and aerospace equipment.
PCB Manufacturing
In PCB manufacturing, FR4 serves as the substrate material upon which conductive copper traces and electronic components are mounted. The process of creating a PCB using FR4 involves several steps:
- Cutting the FR4 board to the desired size and shape
- Applying a layer of copper foil to one or both sides of the board
- Printing the circuit pattern onto the copper foil using a photoresist and UV light exposure
- Etching away the unwanted copper, leaving only the desired circuit traces
- Drilling holes for component placement and vias (interconnections between layers)
- Applying a solder mask and silkscreen for protection and labeling
- Mounting electronic components onto the board and soldering them in place
The use of FR4 in PCB manufacturing offers several advantages:
- Provides a stable and durable substrate for the electronic components
- Ensures proper electrical insulation between conductive traces
- Allows for the creation of multi-layer PCBs by laminating multiple FR4 sheets together
- Withstands the high temperatures involved in soldering processes
- Offers excellent dimensional stability, preventing warping or twisting of the PCB
Other Applications
Apart from PCB manufacturing, FR4 finds applications in various other areas within the electronics industry:
- Insulation spacers and washers: FR4 can be used to create insulating spacers and washers for electronic components, helping to prevent short circuits and maintain proper spacing.
- Structural support: In some cases, FR4 can be used as a structural support material for electronic assemblies, providing rigidity and stability.
- Prototype development: FR4 is often used in the creation of prototype PCBs and electronic devices, allowing for quick and cost-effective testing and iteration.
- High-frequency applications: The material’s good dielectric properties make it suitable for use in high-frequency applications, such as radio frequency (RF) circuits and antennas.
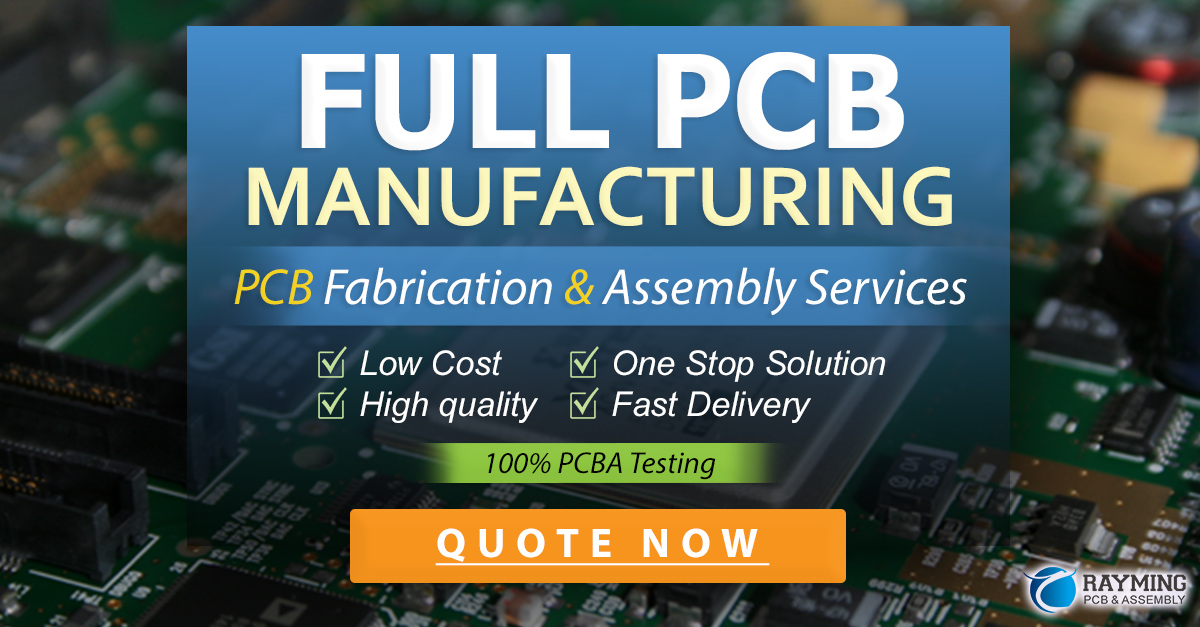
Advantages of FR4 over Other Materials
FR4 has several advantages over other materials used in the electronics industry:
- Cost-effectiveness: FR4 is relatively inexpensive compared to other high-performance materials, such as polytetrafluoroethylene (PTFE) or polyimide.
- Ease of machining: The material can be easily drilled, cut, and shaped using standard PCB manufacturing equipment.
- Wide availability: FR4 is widely available from numerous suppliers, ensuring a stable supply chain for electronics manufacturers.
- Proven reliability: FR4 has been used in the electronics industry for decades and has a proven track record of reliability and durability.
Comparison with Other PCB Materials
Several other materials are used in PCB manufacturing, each with its own set of advantages and disadvantages. Some common alternatives to FR4 include:
- Polyimide: Polyimide is a high-performance polymer that offers excellent thermal stability and chemical resistance. However, it is more expensive than FR4 and can be more difficult to process.
- PTFE: Polytetrafluoroethylene, also known as Teflon, is a fluoropolymer with excellent dielectric properties and low loss tangent. It is often used in high-frequency applications but is more expensive than FR4 and can be challenging to work with.
- Aluminum: Aluminum PCBs are used in applications that require high thermal conductivity, such as LED lighting and power electronics. However, they are more expensive than FR4 and require specialized manufacturing processes.
- Flexible PCBs: Flexible PCBs are made using thin, flexible substrates such as polyimide or polyester. They are used in applications that require the PCB to bend or flex, such as wearable electronics or automotive applications.
Material | Advantages | Disadvantages |
---|---|---|
FR4 | Cost-effective, easy to machine, widely available, proven reliability | Limited thermal conductivity, not suitable for extreme high-frequency applications |
Polyimide | High thermal stability, chemical resistance | More expensive, difficult to process |
PTFE | Excellent dielectric properties, low loss tangent | More expensive, challenging to work with |
Aluminum | High thermal conductivity | More expensive, requires specialized manufacturing |
Flexible PCBs | Can bend and flex | Limited thermal conductivity, more expensive |
Environmental Considerations
As environmental concerns continue to grow, the electronics industry is increasingly focusing on the sustainability and environmental impact of the materials used in manufacturing processes.
Recycling and Disposal of FR4
One of the challenges associated with FR4 is the difficulty in recycling and disposing of the material. The composite nature of FR4, combining fiberglass and epoxy resin, makes it challenging to separate and recycle the individual components.
However, efforts are being made to develop more sustainable alternatives to traditional FR4. Some researchers are exploring the use of bio-based epoxy resins derived from renewable sources, such as vegetable oils or lignin. These bio-based resins could potentially reduce the environmental impact of FR4 production and disposal.
Additionally, some electronics manufacturers are implementing take-back programs and recycling initiatives to help manage the end-of-life disposal of PCBs and other electronic components containing FR4.
REACH and RoHS Compliance
FR4 manufacturers must also ensure compliance with international regulations regarding the use of hazardous substances in electronic products. Two key regulations in this area are:
- REACH (Registration, Evaluation, Authorization, and Restriction of Chemicals): This European Union regulation aims to improve the protection of human health and the environment from the risks posed by chemicals.
- RoHS (Restriction of Hazardous Substances): This directive restricts the use of certain hazardous substances, such as lead, mercury, and cadmium, in electrical and electronic equipment.
FR4 manufacturers must ensure that their products meet the requirements of these regulations, which may involve the use of alternative flame retardants or the elimination of certain additives from the manufacturing process.
Future Developments and Research
As the electronics industry continues to evolve, researchers are exploring new materials and manufacturing techniques that could potentially replace or enhance traditional FR4.
High-Frequency Materials
With the growing demand for high-speed, high-frequency electronic devices, there is a need for materials that can offer better dielectric properties and lower loss tangents than FR4. Some promising alternatives include:
- Low-loss tangent materials: These materials, such as Rogers RO4000 series or Taconic TLX, offer lower dielectric loss and better high-frequency performance than FR4.
- Ceramic-filled composites: By incorporating ceramic fillers into the epoxy resin, researchers are developing materials with improved thermal conductivity and dielectric properties.
3D Printing of PCBs
Additive manufacturing, or 3D printing, is emerging as a potential alternative to traditional PCB manufacturing processes. Researchers are exploring the use of conductive inks and filaments to print PCBs directly, potentially reducing waste and enabling faster prototyping.
However, 3D-printed PCBs currently face challenges in terms of conductivity, resolution, and durability compared to traditional FR4-based PCBs. Further research and development are needed to make 3D-printed PCBs a viable alternative for large-scale production.
Frequently Asked Questions (FAQ)
-
Q: Is FR4 fireproof?
A: FR4 is flame retardant, but not entirely fireproof. It is designed to self-extinguish and prevent the spread of flames, but it can still burn under extreme conditions. -
Q: Can FR4 be used in high-temperature applications?
A: FR4 can withstand temperatures up to 130°C continuously and up to 170°C for short periods. For higher temperature applications, alternative materials like polyimide or ceramic-based substrates may be more suitable. -
Q: Is FR4 toxic?
A: FR4 itself is not considered toxic, but some of the additives used in its production, such as flame retardants, may have potential health and environmental concerns. Manufacturers must ensure compliance with regulations like REACH and RoHS to minimize the use of hazardous substances. -
Q: How does FR4 compare to other PCB materials in terms of cost?
A: FR4 is generally more cost-effective than high-performance materials like polyimide or PTFE. However, it may be more expensive than some lower-performance materials, such as phenolic paper or CEM-1. -
Q: Can FR4 be recycled?
A: Recycling FR4 is challenging due to its composite nature, combining fiberglass and epoxy resin. While some initiatives are in place to recycle PCBs and electronic waste, the process is not yet widely adopted. Researchers are exploring more sustainable alternatives, such as bio-based resins, to improve the recyclability of FR4.
Conclusion
FR4 is a crucial material in the electronics industry, widely used in the production of printed circuit boards and other electronic components. While often referred to as a “plastic,” FR4 is more accurately classified as a composite material, combining woven fiberglass cloth with an epoxy resin binder.
The unique properties of FR4, including its flame resistance, electrical insulation, mechanical strength, and dimensional stability, make it an ideal choice for a wide range of applications. Its cost-effectiveness and ease of machining have contributed to its widespread adoption in the electronics industry.
However, as environmental concerns grow, the industry must address the challenges associated with recycling and disposing of FR4. Researchers are exploring alternative materials and manufacturing techniques that could potentially enhance or replace traditional FR4 in the future.
As the demand for high-performance, high-frequency electronic devices continues to rise, FR4 manufacturers must continue to innovate and adapt to meet the evolving needs of the industry while ensuring compliance with environmental regulations.
No responses yet