What is a Composite Material?
A composite material is a combination of two or more materials with different physical and chemical properties that, when combined, create a material with unique characteristics that differ from the individual components. The primary purpose of creating a composite is to achieve a material with enhanced properties, such as increased strength, stiffness, or thermal resistance, compared to the individual constituent materials.
Composites typically consist of a matrix (the main material) and reinforcement (the material that provides additional strength or other desired properties). The matrix can be a polymer, metal, or ceramic, while the reinforcement can be fibers, particles, or whiskers.
The Composition of FR4
FR4 is a composite material made up of two main components:
- Epoxy resin matrix
- Glass fiber reinforcement
Epoxy Resin Matrix
The epoxy resin used in FR4 is a thermoset polymer that provides excellent electrical insulation, chemical resistance, and dimensional stability. When heated and mixed with a hardener, the epoxy resin undergoes a cross-linking reaction, forming a rigid, three-dimensional network structure. This cross-linked structure gives FR4 its superior mechanical and thermal properties.
Glass Fiber Reinforcement
The glass fibers used in FR4 are typically E-glass, which is a low-alkali borosilicate glass. These fibers are woven into a fabric and impregnated with the epoxy resin to create the FR4 laminate. The glass fibers provide the following benefits to the composite:
- Increased mechanical strength and stiffness
- Improved dimensional stability
- Enhanced thermal resistance
- Reduced coefficient of thermal expansion (CTE)
The glass fiber reinforcement is the key component that makes FR4 a composite material, as it significantly enhances the properties of the epoxy resin matrix.
Properties of FR4
FR4 exhibits several desirable properties that make it an ideal choice for PCBs and other electronic applications:
Mechanical Properties
- High tensile strength
- High flexural strength
- Good impact resistance
- Low creep
Thermal Properties
- Glass transition temperature (Tg) around 130-140°C
- Continuous operating temperature up to 130°C
- Low coefficient of thermal expansion (CTE)
Electrical Properties
- Excellent dielectric strength
- High insulation resistance
- Low dielectric constant and dissipation factor
Chemical Properties
- Resistant to various chemicals, including acids, alkalis, and solvents
- Flame retardant (self-extinguishing)
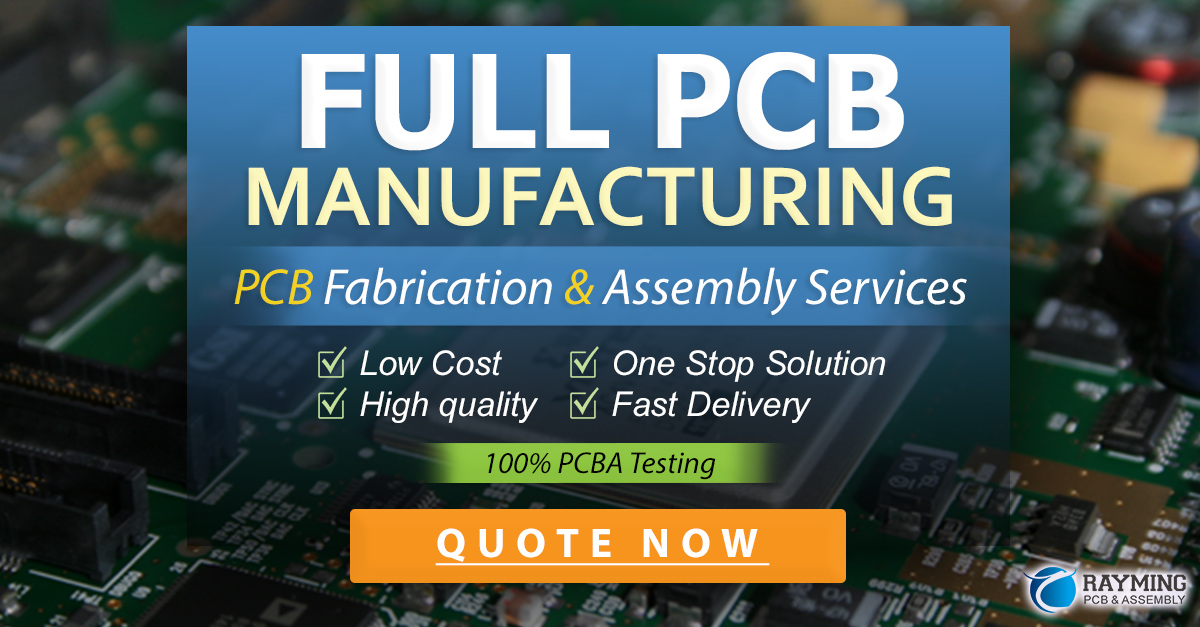
Advantages of FR4 as a Composite
The combination of epoxy resin and glass fiber reinforcement in FR4 offers several advantages over other PCB materials:
- Enhanced mechanical strength and stiffness, enabling thinner and more compact PCB designs
- Improved thermal stability, allowing for higher operating temperatures and better heat dissipation
- Excellent electrical insulation properties, minimizing signal loss and cross-talk
- Good chemical resistance, ensuring long-term reliability in various environments
- Flame retardancy, meeting safety standards and reducing the risk of fire
Applications of FR4
FR4 is widely used in various industries due to its superior properties and versatility. Some common applications include:
- Printed Circuit Boards (PCBs)
- Consumer electronics
- Automotive electronics
- Industrial control systems
- Medical devices
-
Telecommunications equipment
-
Structural Insulation
- Electrical insulation panels
-
Thermal insulation barriers
-
Aerospace and Defense
- Avionics systems
- Radar components
- Satellite communications
FR4 Variants and Grades
There are several variants and grades of FR4 available, each tailored to specific applications or requirements:
Grade | Description | Applications |
---|---|---|
Standard FR4 | General-purpose grade with balanced properties | Consumer electronics, industrial control systems |
High Tg FR4 | Higher glass transition temperature (up to 170°C) | Automotive, aerospace, and military applications |
Halogen-free FR4 | Eco-friendly, halogen-free flame retardants | Green electronics, RoHS-Compliant products |
Low-loss FR4 | Lower dielectric constant and dissipation factor | High-frequency applications, telecommunications |
High-speed FR4 | Optimized for high-speed signal transmission | High-speed digital circuits, servers, and routers |
Manufacturing Process of FR4
The manufacturing process of FR4 involves several steps:
-
Glass Fabric Weaving: E-glass fibers are woven into a fabric with a specific pattern and thickness.
-
Impregnation: The glass fabric is impregnated with the epoxy resin and partially cured (B-stage).
-
Layup: The impregnated glass fabric layers are stacked and aligned according to the desired thickness and properties.
-
Pressing: The stacked layers are pressed under high temperature and pressure to fully cure the epoxy resin and consolidate the laminate.
-
Cutting and Machining: The cured FR4 laminate is cut and machined to the required dimensions and shapes.
-
Surface Finishing: Copper foils are laminated onto the FR4 surface for PCB applications, and additional surface treatments may be applied as needed.
Comparison with Other PCB Materials
FR4 is not the only material used for PCBs. Other common materials include:
- Polyimide (PI): Higher temperature resistance and flexibility, but more expensive
- PTFE (Teflon): Lower dielectric constant and dissipation factor, but more difficult to process
- Aluminum: Excellent thermal conductivity, but limited electrical insulation properties
- Ceramics: High thermal stability and dielectric strength, but brittle and expensive
Compared to these materials, FR4 offers a balanced combination of mechanical, thermal, electrical, and cost properties, making it the most widely used material for PCBs.
Future Trends and Developments
As the electronics industry continues to evolve, there is a growing demand for improved materials that can meet the challenges of higher frequencies, faster data transmission, and more extreme environments. Some future trends and developments in FR4 and related composite materials include:
-
High-frequency compatible FR4: Modified FR4 formulations with lower dielectric constant and dissipation factor for 5G and millimeter-wave applications.
-
Thermally conductive FR4: Incorporation of thermally conductive fillers (e.g., ceramic particles, carbon nanotubes) to enhance heat dissipation in high-power electronics.
-
Bio-based and recyclable FR4: Development of eco-friendly FR4 variants using bio-based epoxy resins and recyclable glass fibers to reduce environmental impact.
-
Multifunctional FR4 composites: Integration of additional functionalities, such as electromagnetic shielding or embedded sensors, into FR4 laminates for smart electronics.
Frequently Asked Questions (FAQ)
-
Q: Is FR4 a thermoplastic or thermoset material?
A: FR4 is a thermoset material. The epoxy resin in FR4 undergoes a cross-linking reaction during the curing process, forming a permanent, irreversible three-dimensional network structure. -
Q: Can FR4 be recycled?
A: Recycling FR4 is challenging due to its thermoset nature and the difficulty in separating the glass fibers from the epoxy resin. However, research is ongoing to develop more recyclable FR4 variants and recycling technologies. -
Q: What is the maximum operating temperature of FR4?
A: Standard FR4 has a continuous operating temperature of up to 130°C. High Tg FR4 variants can offer higher operating temperatures, up to 170°C. -
Q: Is FR4 suitable for high-frequency applications?
A: Standard FR4 may not be the best choice for high-frequency applications due to its relatively high dielectric constant and dissipation factor. However, low-loss and high-speed FR4 variants are available for improved high-frequency performance. -
Q: Can FR4 be used in flexible PCBs?
A: FR4 is primarily used in rigid PCBs due to its high stiffness. For flexible PCBs, materials like polyimide (PI) or flexible polyester are more commonly used.
Conclusion
In conclusion, FR4 is indeed a composite material, consisting of an epoxy resin matrix reinforced with glass fibers. This combination of materials results in a laminate with excellent mechanical, thermal, electrical, and chemical properties, making it the most widely used material for PCBs and various other electronic applications.
As the electronics industry continues to advance, FR4 and its variants will likely evolve to meet the growing demands for higher performance, sustainability, and multifunctionality. By understanding the composition, properties, and advantages of FR4 as a composite material, engineers and designers can make informed decisions when selecting materials for their electronic products.
No responses yet