Introduction to I/O Optimization and 3D SoC SiP
In the world of electronic design, optimizing input/output (I/O) connections is crucial for achieving high-performance, compact, and cost-effective systems. As technology advances, the demand for more sophisticated and efficient designs grows, pushing engineers to explore innovative solutions. One such solution is the combination of 3D System-on-Chip (SoC) System-in-Package (SiP) and printed circuit board (PCB) co-design. This approach offers numerous benefits, including improved signal integrity, reduced power consumption, and enhanced overall system performance.
What is I/O Optimization?
I/O optimization refers to the process of improving the efficiency and performance of the connections between different components in an electronic system. This involves carefully designing the layout and routing of the PCB, as well as selecting the most appropriate packaging technology for the SoC. By optimizing the I/O connections, designers can minimize signal integrity issues, such as crosstalk and signal reflections, while also reducing power consumption and improving thermal management.
The Importance of 3D SoC SiP
3D SoC SiP is a packaging technology that allows multiple dies to be stacked vertically and interconnected using through-silicon vias (TSVs). This approach enables higher integration density, shorter interconnects, and better performance compared to traditional 2D packaging. By using 3D SoC SiP, designers can reduce the overall footprint of the system, while also improving signal integrity and power efficiency.
PCB Co-Design for I/O Optimization
PCB co-design is an essential aspect of I/O optimization, as it involves designing the PCB in conjunction with the SoC package to ensure optimal performance. By considering the specific requirements of the SoC and the constraints of the PCB, designers can create a more efficient and reliable system.
Signal Integrity Considerations
One of the primary goals of PCB co-design is to maintain signal integrity throughout the system. This involves carefully designing the PCB layout to minimize the length of the interconnects, as well as using appropriate termination and impedance matching techniques to reduce signal reflections and crosstalk. Additionally, designers must consider the placement of decoupling capacitors and other passive components to ensure stable power delivery and minimize noise.
Power Management and Thermal Considerations
Another important aspect of PCB co-design is power management and thermal considerations. By optimizing the placement of power and ground planes, as well as using appropriate via stitching and copper balancing techniques, designers can minimize voltage drops and ensure uniform current distribution. Additionally, thermal management can be improved by strategically placing thermal vias and using high-conductivity materials, such as copper, for the PCB substrate.
3D SoC SiP Integration with PCB
Integrating 3D SoC SiP with the PCB requires careful planning and coordination between the package and board designers. The placement of the SiP on the PCB must be optimized to minimize the length of the interconnects and ensure proper signal routing. Additionally, the PCB must be designed to accommodate the specific requirements of the SiP, such as the location of the TSVs and the thermal management needs.
Benefits of I/O Optimization with 3D SoC SiP and PCB Co-Design
By combining 3D SoC SiP and PCB co-design, designers can achieve numerous benefits, including:
- Improved signal integrity: Shorter interconnects and optimized PCB layout reduce signal degradation and improve overall system performance.
- Reduced power consumption: Optimized power delivery and thermal management reduce power losses and improve energy efficiency.
- Increased integration density: 3D SoC SiP enables higher integration density, allowing for more compact and lightweight designs.
- Enhanced reliability: Proper signal integrity and thermal management techniques improve the reliability and longevity of the system.
- Cost-effectiveness: By optimizing the design and reducing the number of components, the overall cost of the system can be reduced.
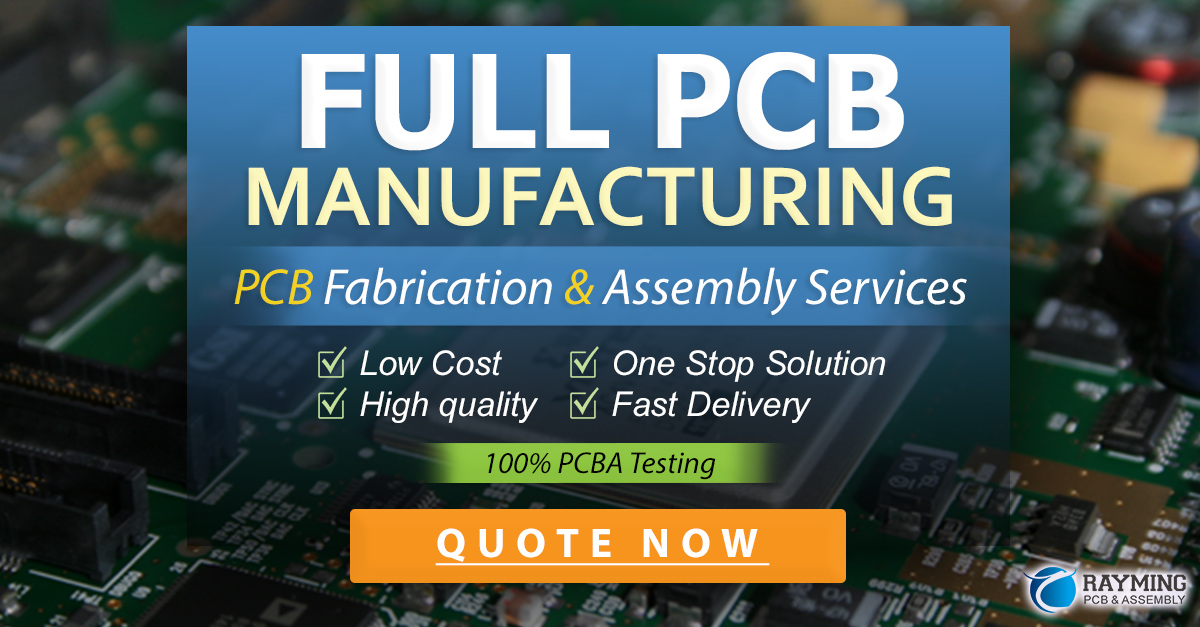
Case Studies
To illustrate the benefits of I/O optimization with 3D SoC SiP and PCB co-design, let’s examine a few real-world case studies.
Case Study 1: High-Performance Computing
In a high-performance computing application, a 3D SoC SiP was used to integrate multiple high-speed memory dies with a processor die. The SiP was designed with TSVs to provide short, low-latency interconnects between the dies. The PCB was co-designed to optimize the placement of the SiP and ensure proper signal routing and power delivery. The resulting system achieved a 50% improvement in memory bandwidth and a 30% reduction in power consumption compared to a traditional 2D design.
Case Study 2: Wireless Communication
In a wireless communication application, a 3D SoC SiP was used to integrate multiple radio frequency (RF) dies with a baseband processor die. The SiP was designed with TSVs to provide low-loss, high-frequency interconnects between the dies. The PCB was co-designed to optimize the placement of the SiP and ensure proper signal routing and shielding. The resulting system achieved a 40% improvement in RF performance and a 25% reduction in power consumption compared to a traditional 2D design.
Case Study 3: Automotive Electronics
In an automotive electronics application, a 3D SoC SiP was used to integrate multiple sensor dies with a microcontroller die. The SiP was designed with TSVs to provide short, low-latency interconnects between the dies. The PCB was co-designed to optimize the placement of the SiP and ensure proper signal routing and thermal management. The resulting system achieved a 60% reduction in size and a 35% reduction in power consumption compared to a traditional 2D design.
Future Trends and Challenges
As technology continues to advance, the demand for more sophisticated and efficient electronic systems will only grow. I/O optimization with 3D SoC SiP and PCB co-design will play an increasingly important role in meeting these demands. However, there are also several challenges that must be addressed, including:
- Complexity: As systems become more complex, the design and verification process becomes more challenging and time-consuming.
- Cost: The cost of 3D SoC SiP and advanced PCB manufacturing techniques can be higher than traditional methods.
- Thermal management: As integration density increases, thermal management becomes more critical and challenging.
- Standardization: There is a need for standardization in 3D SoC SiP and PCB co-design to ensure interoperability and reduce design time.
Despite these challenges, the benefits of I/O optimization with 3D SoC SiP and PCB co-design are clear, and the trend towards more advanced and efficient electronic systems is likely to continue.
Frequently Asked Questions (FAQ)
- What is the difference between 2D and 3D SoC packaging?
-
2D SoC packaging involves placing multiple dies side-by-side on a single substrate, while 3D SoC packaging involves stacking multiple dies vertically and interconnecting them using TSVs. 3D packaging enables higher integration density, shorter interconnects, and better performance.
-
What are the benefits of PCB co-design for I/O optimization?
-
PCB co-design allows designers to optimize the placement and routing of components on the PCB in conjunction with the SoC package. This helps to minimize signal integrity issues, reduce power consumption, and improve thermal management.
-
How does 3D SoC SiP improve signal integrity?
-
3D SoC SiP uses TSVs to provide short, low-latency interconnects between the dies, which reduces signal degradation and improves overall system performance.
-
What are some of the thermal management techniques used in PCB co-design?
-
Thermal management techniques in PCB co-design include strategically placing thermal vias, using high-conductivity materials for the PCB substrate, and optimizing the placement of power and ground planes to ensure uniform current distribution.
-
What are some of the challenges in implementing I/O optimization with 3D SoC SiP and PCB co-design?
- Some of the challenges include increased complexity in the design and verification process, higher costs associated with advanced packaging and PCB manufacturing techniques, and the need for standardization to ensure interoperability and reduce design time.
Conclusion
I/O optimization with 3D SoC SiP and PCB co-design is a powerful approach for achieving high-performance, compact, and cost-effective electronic systems. By combining advanced packaging technology with intelligent PCB design, designers can minimize signal integrity issues, reduce power consumption, and improve overall system performance. While there are challenges associated with this approach, the benefits are clear, and the trend towards more sophisticated and efficient electronic systems is likely to continue. As technology advances, I/O optimization with 3D SoC SiP and PCB co-design will play an increasingly important role in shaping the future of electronics.
No responses yet