What is a Ceramic PCB?
A ceramic PCB is a printed circuit board that uses a ceramic substrate instead of the more common FR-4 or other organic materials. The ceramic substrate is typically made from alumina (Al2O3), which is a high-purity aluminum oxide. Ceramic PCBs can be single-layer or multi-layer, depending on the complexity of the circuit design and the application requirements.
Advantages of Ceramic PCBs
- High thermal conductivity
- Excellent electrical insulation
- Superior temperature resistance
- Low dielectric loss
- High mechanical strength
- Dimensional stability
- Corrosion resistance
Applications of Ceramic PCBs
- High-power electronics
- RF and microwave circuits
- Aerospace and defense systems
- Automotive electronics
- Medical devices
- LED lighting
The 7 Ceramic PCB Manufacturing Processes
The ceramic PCB manufacturing process involves several steps that are distinct from the fabrication of traditional PCBs. These steps ensure the high quality and reliability of the final product. Let’s take a closer look at each of the seven processes involved in ceramic PCB manufacturing.
1. Substrate Preparation
The first step in ceramic PCB manufacturing is to prepare the ceramic substrate. The most common ceramic material used is alumina, which is a high-purity aluminum oxide. The alumina powder is mixed with a binder and other additives to form a slurry. The slurry is then cast into thin sheets using a tape casting process or a doctor blade method. The green ceramic sheets are dried and cut to the desired size.
2. Via Hole Formation
Via holes are created in the ceramic substrate to allow for electrical connections between layers in multi-layer ceramic PCBs. There are two main methods for forming via holes in ceramic substrates:
- Mechanical drilling: A diamond-tipped drill bit is used to create holes in the green ceramic sheet.
- Laser drilling: A high-power laser is used to ablate the ceramic material and create precise via holes.
After drilling, the via holes are filled with a conductive paste, typically containing tungsten or molybdenum.
3. Conductor Printing
The next step is to print the conductive traces and pads on the ceramic substrate. This is typically done using a screen printing process. A conductive paste, usually containing tungsten or molybdenum, is forced through a patterned screen onto the ceramic surface. The printed pattern is then dried and fired in a high-temperature furnace to sinter the conductive material and form a strong bond with the ceramic substrate.
4. Stacking and Lamination
For multi-layer ceramic PCBs, the individual printed ceramic layers are stacked and aligned using registration holes. The stacked layers are then laminated together under high pressure and temperature to form a solid, monolithic structure. During the lamination process, the ceramic layers and conductive traces are fused together, creating a strong mechanical and electrical bond.
5. Co-firing
After lamination, the ceramic PCB undergoes a co-firing process. The entire assembly is placed in a high-temperature furnace and fired at temperatures ranging from 1,500°C to 1,800°C. During the co-firing process, the ceramic substrate and the conductive traces are sintered simultaneously. This high-temperature firing process ensures a strong bond between the ceramic and the conductive materials, resulting in a dense and homogeneous structure.
6. Surface Finishing
Once the co-fired ceramic PCB has cooled, it undergoes surface finishing to improve its electrical and mechanical properties. Common surface finishing techniques for ceramic PCBs include:
- Nickel plating: A thin layer of nickel is electroplated onto the conductive traces and pads to improve solderability and protect against oxidation.
- Gold plating: A thin layer of gold is electroplated over the nickel to further enhance solderability and provide excellent electrical conductivity.
- Solder mask application: A solder mask is applied to the surface of the ceramic PCB to protect against solder bridging and provide electrical insulation between adjacent conductive traces.
7. Singulation and Inspection
The final step in the ceramic PCB manufacturing process is singulation and inspection. The large ceramic panel is cut into individual PCBs using a dicing saw or a laser cutting machine. Each individual PCB is then inspected for defects, such as cracks, voids, or electrical shorts. Optical and electrical testing methods are used to ensure the quality and functionality of the final product.
Ceramic PCB Manufacturing vs. Traditional PCB Manufacturing
Ceramic PCB manufacturing differs from traditional PCB manufacturing in several key aspects. The following table highlights the main differences between the two processes:
Aspect | Ceramic PCB Manufacturing | Traditional PCB Manufacturing |
---|---|---|
Substrate Material | Alumina (Al2O3) | FR-4, polyimide, or other organic materials |
Thermal Conductivity | High | Low |
Temperature Resistance | High (up to 1,800°C) | Low (up to 260°C) |
Dielectric Loss | Low | Higher |
Mechanical Strength | High | Lower |
Manufacturing Process | Tape casting, screen printing, co-firing | Etching, plating, lamination |
Cost | Higher | Lower |
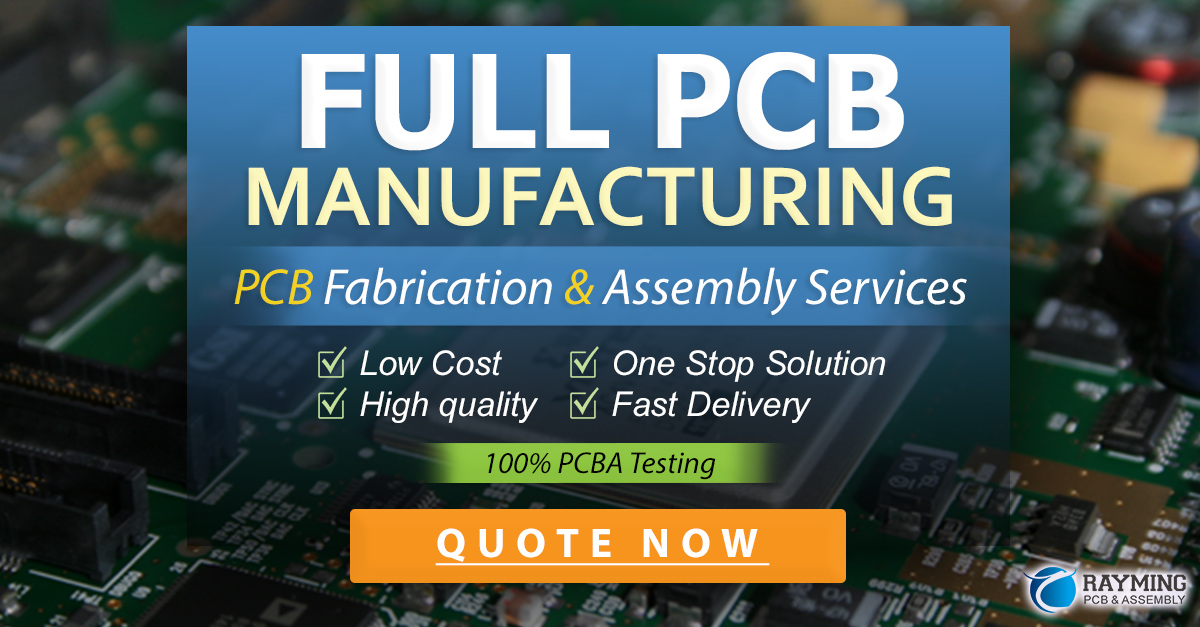
Frequently Asked Questions (FAQ)
-
Q: What is the main advantage of using ceramic PCBs over traditional PCBs?
A: The main advantage of using ceramic PCBs is their excellent thermal conductivity and high temperature resistance, which make them suitable for applications in harsh environments and high-power electronics. -
Q: How do multi-layer ceramic PCBs differ from single-layer ceramic PCBs?
A: Multi-layer ceramic PCBs consist of multiple ceramic layers with conductive traces and via holes connecting the layers, allowing for more complex circuit designs. Single-layer ceramic PCBs have conductive traces on only one side of the ceramic substrate. -
Q: What are the most common surface finishing techniques for ceramic PCBs?
A: The most common surface finishing techniques for ceramic PCBs are nickel plating, gold plating, and solder mask application. These finishes improve solderability, protect against oxidation, and provide electrical insulation. -
Q: Can ceramic PCBs be used in high-frequency applications?
A: Yes, ceramic PCBs are well-suited for high-frequency applications, such as RF and microwave circuits, due to their low dielectric loss and excellent electrical insulation properties. -
Q: Are ceramic PCBs more expensive than traditional PCBs?
A: Yes, ceramic PCBs are generally more expensive than traditional PCBs due to the specialized materials and manufacturing processes involved. However, their superior performance characteristics justify the higher cost in many applications.
Conclusion
Ceramic PCBs offer unique properties and advantages that make them ideal for applications in harsh environments, high-power electronics, and RF/microwave circuits. The seven ceramic PCB manufacturing processes – substrate preparation, via hole formation, conductor printing, stacking and lamination, co-firing, surface finishing, and singulation and inspection – ensure the high quality and reliability of the final product.
While ceramic PCBs are more expensive than traditional PCBs, their superior thermal conductivity, temperature resistance, and electrical insulation properties make them an essential component in many advanced electronic systems. As technology continues to evolve, the demand for ceramic PCBs is likely to grow, driving further innovations in ceramic PCB manufacturing processes.
No responses yet