Introduction to PCB assembly
Printed Circuit Board (PCB) assembly is the process of populating a bare PCB with electronic components to create a functional circuit board. The PCB assembly process involves several steps, including solder paste application, component placement, reflow soldering, inspection, and testing. In this article, we will explore the PCB assembly process in detail, covering each step and the best practices to ensure a high-quality final product.
Key Components of PCB Assembly
- Bare PCB
- Electronic components (resistors, capacitors, ICs, etc.)
- Solder paste
- Pick-and-place machines
- Reflow soldering equipment
- Inspection tools (AOI, X-ray, etc.)
PCB Assembly Process Steps
Step 1: Solder Paste Application
The first step in the PCB assembly process is applying solder paste to the bare PCB. Solder paste is a mixture of tiny solder particles and flux that helps to create a strong bond between the electronic components and the PCB pads. There are two primary methods for applying solder paste:
Stencil Printing
Stencil printing is the most common method for applying solder paste in high-volume PCB assembly. A stainless steel or polyester stencil with openings corresponding to the PCB pads is placed over the bare PCB. Solder paste is then applied using a squeegee, which forces the paste through the stencil openings onto the pads.
Dispensing
Dispensing is a slower, more precise method of applying solder paste, typically used for low-volume production or prototypes. A dispensing machine applies small dots of solder paste directly onto the PCB pads.
Step 2: Component Placement
Once the solder paste is applied, the next step is to place the electronic components onto the PCB. Modern PCB assembly relies heavily on automated pick-and-place machines to achieve high accuracy and speed.
Pick-and-Place Machines
Pick-and-place machines use computer-controlled nozzles to pick up components from feeders and place them onto the PCB pads with high precision. These machines can place thousands of components per hour, making them essential for high-volume production.
The component placement process typically involves two stages:
- High-speed placement for small, simple components
- Fine-pitch placement for larger, more complex components
Step 3: Reflow Soldering
After the components are placed, the PCB undergoes reflow soldering to permanently bond the components to the board. Reflow soldering involves heating the PCB and components in a controlled manner to melt the solder paste and create a strong electrical and mechanical connection.
Reflow Soldering Process
- Preheat: The PCB is gradually heated to activate the flux and remove any moisture.
- Soak: The temperature is maintained to allow the components and PCB to reach a uniform temperature.
- Reflow: The temperature is increased to melt the solder particles and create a bond between the components and PCB pads.
- Cooling: The PCB is cooled to solidify the solder joints.
Step 4: Inspection
After reflow soldering, the PCB undergoes various inspection processes to ensure the quality of the solder joints and the overall assembly.
Automated Optical Inspection (AOI)
AOI systems use high-resolution cameras and advanced image processing algorithms to detect surface-level defects such as missing components, misaligned components, and solder bridging.
X-ray Inspection
X-ray inspection is used to detect hidden defects, such as voids in solder joints or problems with ball grid array (BGA) components.
Step 5: Testing and Rework
The final step in the PCB assembly process is testing and rework. Functional testing is performed to verify that the assembled PCB operates as intended. If any issues are identified during testing, the PCB may undergo rework to correct the problem.
Types of Functional Testing
- In-Circuit Testing (ICT): Checks individual components and their connections.
- Functional Circuit Testing (FCT): Verifies the overall functionality of the PCB.
- Boundary Scan Testing: Tests complex digital circuits using built-in test access ports (TAPs).
Rework Techniques
- Manual soldering: Used for simple repairs or component replacements.
- Hot air rework: Employs a focused hot air stream to remove and replace components.
- BGA rework: Specialized equipment is used to remove and replace BGA components.
Best Practices for High-Quality PCB Assembly
To ensure a high-quality PCB assembly, consider the following best practices:
- Design for Manufacturing (DFM): Optimize your PCB design to facilitate efficient assembly and minimize potential issues.
- Use high-quality components: Ensure that all components meet the required specifications and are sourced from reputable suppliers.
- Implement strict process controls: Monitor and control critical process parameters, such as solder paste application, component placement accuracy, and reflow temperature profiles.
- Conduct thorough inspections: Utilize AOI, X-ray, and other inspection methods to catch defects early in the process.
- Provide comprehensive documentation: Maintain detailed work instructions, bill of materials (BOM), and other necessary documents to ensure consistency and traceability.
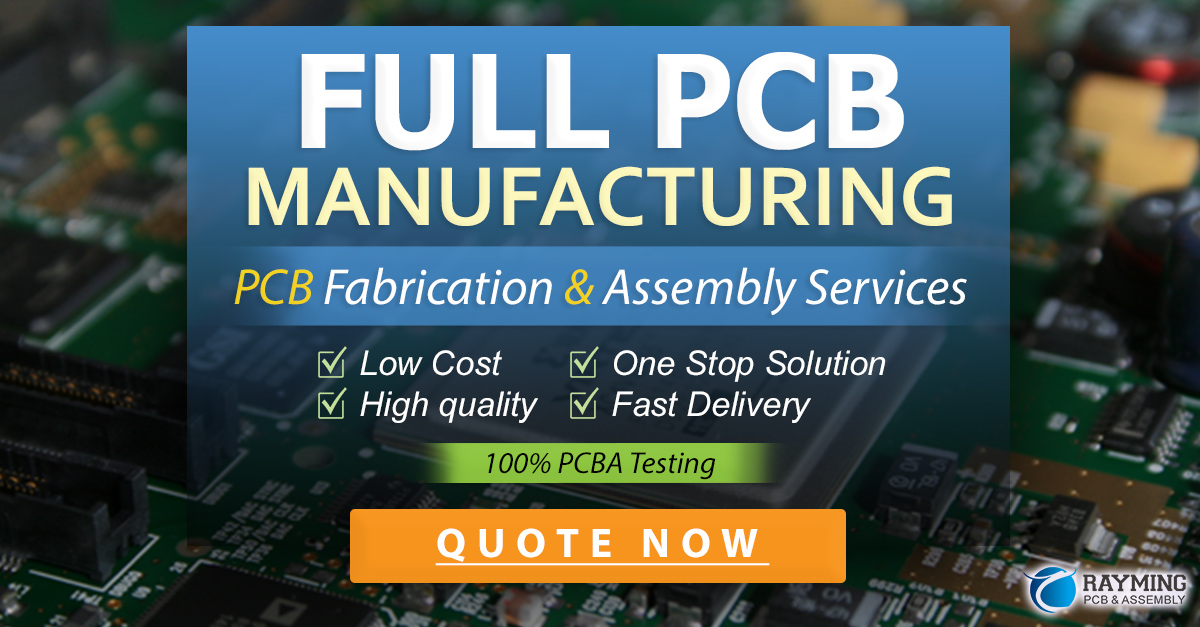
PCB Assembly Challenges and Solutions
Challenge | Solution |
---|---|
Miniaturization | Use high-precision pick-and-place machines and fine-pitch stencils for solder paste application. |
High-mix, low-volume production | Implement flexible manufacturing systems and rapid changeover processes. |
Electrostatic discharge (ESD) | Establish an ESD-safe environment and train personnel on proper ESD handling procedures. |
Thermal management | Consider thermal requirements during the design phase and use appropriate heat dissipation techniques. |
Frequently Asked Questions (FAQ)
1. What is the difference between through-hole and surface-mount PCB assembly?
Through-hole PCB assembly involves inserting component leads through holes drilled in the PCB and soldering them on the opposite side. Surface-mount PCB assembly places components directly onto pads on the PCB surface and uses reflow soldering to create the connections. Surface-mount technology allows for smaller components and higher-density PCB designs.
2. How long does the PCB assembly process typically take?
The duration of the PCB assembly process depends on factors such as the complexity of the PCB design, the number of components, and the production volume. Simple PCBs with a low component count can be assembled in a matter of hours, while complex, high-volume projects may take several days or weeks.
3. What is the role of flux in the soldering process?
Flux is a chemical agent that helps to remove oxidation from metal surfaces and promotes the formation of a strong solder joint. It is a key component of solder paste and is also used in manual soldering processes. Flux improves the wetting properties of the solder, allowing it to flow more easily and create a reliable connection between the component and the PCB pad.
4. How can I ensure the quality of my PCB assembly?
To ensure the quality of your PCB assembly, follow best practices such as designing for manufacturability, using high-quality components, implementing strict process controls, conducting thorough inspections, and providing comprehensive documentation. Additionally, work with experienced PCB assembly providers who have a proven track record of delivering high-quality products.
5. What are some common PCB assembly defects, and how can they be prevented?
Common PCB assembly defects include solder bridges, cold solder joints, tombstoning, and component misalignment. These defects can be prevented by optimizing the PCB design, using appropriate solder paste and stencil thickness, maintaining proper reflow temperature profiles, and conducting regular maintenance on assembly equipment. Thorough inspection processes, such as AOI and X-ray, can help identify defects early in the production process.
Conclusion
PCB assembly is a complex process that requires careful planning, attention to detail, and adherence to best practices. By understanding the key steps involved in PCB assembly, from solder paste application to testing and rework, you can ensure that your PCBs are assembled to the highest quality standards. Implementing strict process controls, conducting thorough inspections, and working with experienced PCB assembly providers can help you overcome common challenges and achieve reliable, high-performing PCBs for your applications.
No responses yet