Introduction to PCB Enclosures
A printed circuit board assembly (PCBA) is the heart of any electronic device, containing all the components and circuitry necessary for its operation. To protect the delicate PCBA from damage, dust, moisture, and electromagnetic interference (EMI), it is essential to house it within a well-designed enclosure. This article will guide you through the process of designing an optimal PCB enclosure that meets your specific requirements.
Key Considerations for PCB Enclosure Design
When designing a PCB enclosure, there are several critical factors to consider:
-
Size and shape: The enclosure must accommodate the dimensions of the PCBA, including any protruding components, connectors, or mounting points.
-
Material selection: Choose a material that offers the necessary strength, durability, and thermal properties for your application, such as plastic, metal, or composites.
-
Environmental protection: Consider the environment in which the device will operate and select an enclosure that provides adequate protection against dust, moisture, and other contaminants.
-
Thermal management: Ensure that the enclosure allows for proper heat dissipation to prevent overheating of the PCBA components.
-
EMI shielding: If the device is sensitive to electromagnetic interference or generates EMI itself, incorporate shielding features into the enclosure design.
-
Manufacturability: Design the enclosure with ease of manufacturing and assembly in mind to minimize costs and production time.
Step-by-Step PCB Enclosure Design Process
Step 1: Gather PCBA Specifications
Before starting the enclosure design, collect all relevant information about the PCBA, including:
- Dimensions (length, width, height)
- Component locations and heights
- Connector types and positions
- Mounting hole locations
- Power requirements and heat generation
Step 2: Select Enclosure Material
Based on the PCBA specifications and the intended application, choose an appropriate material for the enclosure. Common options include:
Material | Advantages | Disadvantages |
---|---|---|
Plastic (ABS, polycarbonate) | Lightweight, cost-effective, easy to mold | Limited strength and Thermal conductivity |
Aluminum | Strong, lightweight, good thermal conductivity | More expensive than plastic, requires additional processing |
Steel | Very strong and durable | Heavy, prone to corrosion |
Composites (e.g., carbon fiber) | High strength-to-weight ratio, good thermal properties | Expensive, complex manufacturing process |
Step 3: Determine Enclosure Size and Shape
Using the PCBA dimensions and component locations, design the internal layout of the enclosure. Allow for sufficient clearance around components and connectors, and consider the placement of any batteries, displays, or user interface elements. Decide on the overall shape of the enclosure based on ergonomics, aesthetics, and manufacturing constraints.
Step 4: Incorporate Thermal Management Features
To ensure proper heat dissipation, include features such as heat sinks, cooling fins, or vents in the enclosure design. Use thermal simulation software to analyze the heat flow within the enclosure and optimize the placement of thermal management features.
Step 5: Address Environmental Protection Needs
Depending on the intended operating environment, incorporate features that protect the PCBA from dust, moisture, and other contaminants. This may include:
- Gaskets or seals around enclosure seams and openings
- IP (Ingress Protection) rated enclosures for harsh environments
- Conformal coatings or potting compounds for additional moisture protection
Step 6: Implement EMI Shielding
If EMI shielding is required, design the enclosure to include features such as:
- Conductive coatings or paints on the interior surfaces
- Conductive gaskets around seams and openings
- Shielded connectors or cable assemblies
Step 7: Design for Manufacturing and Assembly
To minimize production costs and time, design the enclosure with manufacturability in mind:
- Use standard sizes and shapes whenever possible
- Minimize the number of parts and assembly steps
- Incorporate features that facilitate easy assembly, such as snap-fits or threaded inserts
- Allow for adequate tolerances and draft angles for molded parts
Step 8: Prototype and Test
Before finalizing the enclosure design, create prototypes and perform thorough testing to validate the design’s performance, including:
- Fit and function tests with the PCBA
- Thermal testing to ensure adequate heat dissipation
- Environmental testing (e.g., dust, moisture, vibration)
- EMI testing to verify shielding effectiveness
Step 9: Iterate and Refine
Based on the results of prototyping and testing, make any necessary adjustments to the enclosure design. Repeat the prototyping and testing process until the design meets all requirements and performance criteria.
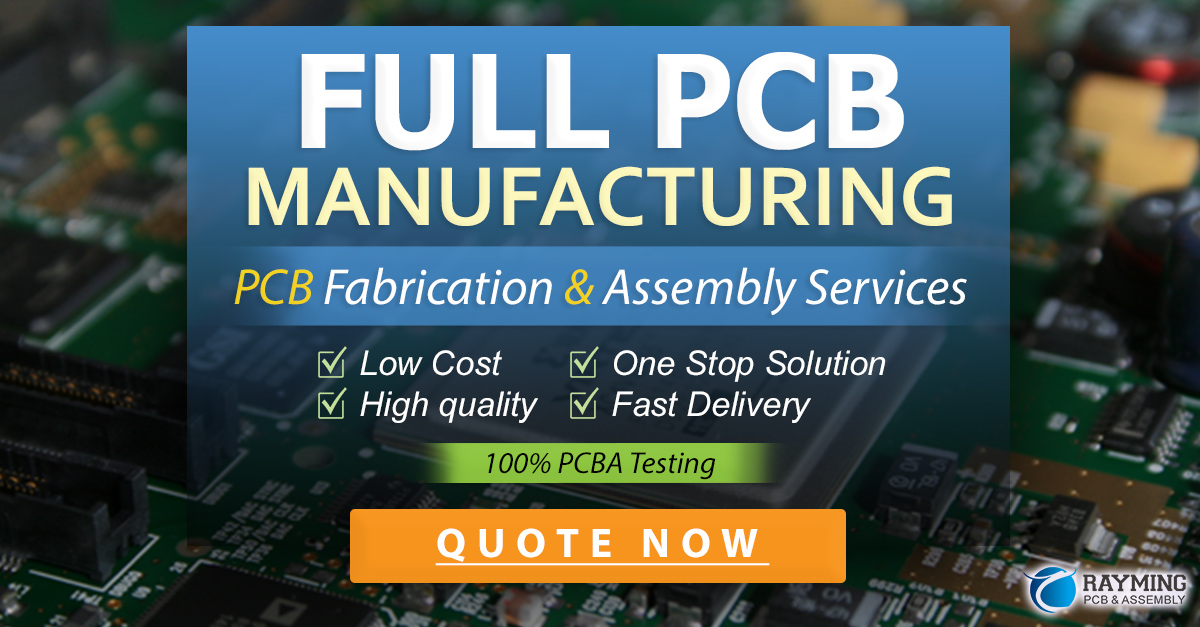
PCB Enclosure Design Best Practices
To ensure a successful PCB enclosure design, follow these best practices:
-
Collaborate closely with the PCBA design team to ensure compatibility and optimal integration between the PCBA and enclosure.
-
Use 3D modeling software to create detailed enclosure designs and perform virtual fit checks with the PCBA model.
-
Consider the end-user experience when designing the enclosure, including ergonomics, aesthetics, and ease of use.
-
Plan for future upgrades or modifications by incorporating features that allow for easy access to the PCBA and components.
-
Work with experienced manufacturers and suppliers to ensure the enclosure can be produced efficiently and cost-effectively.
Frequently Asked Questions (FAQ)
1. What is the most common material used for PCB enclosures?
Plastic (ABS or polycarbonate) is the most common material for PCB enclosures due to its cost-effectiveness, ease of molding, and adequate strength and durability for most applications.
2. How do I determine the necessary level of environmental protection for my PCB enclosure?
Consider the intended operating environment for your device and consult the IP (Ingress Protection) rating system to determine the required level of protection against solid objects and liquids.
3. What is the best way to ensure proper heat dissipation in a PCB enclosure?
Use thermal simulation software to analyze the heat flow within the enclosure and optimize the placement of thermal management features such as heat sinks, cooling fins, or vents. Ensure that there is adequate airflow around the PCBA components.
4. How can I minimize the cost of manufacturing a PCB enclosure?
To minimize manufacturing costs, use standard sizes and shapes whenever possible, minimize the number of parts and assembly steps, and incorporate features that facilitate easy assembly, such as snap-fits or threaded inserts.
5. What are the key steps in the PCB enclosure design process?
The key steps in the PCB enclosure design process are:
- Gather PCBA specifications
- Select enclosure material
- Determine enclosure size and shape
- Incorporate thermal management features
- Address environmental protection needs
- Implement EMI shielding
- Design for manufacturing and assembly
- Prototype and test
- Iterate and refine
Conclusion
Designing an optimal PCB enclosure requires careful consideration of the PCBA specifications, intended application, and operating environment. By following the step-by-step design process and best practices outlined in this article, you can create a PCB enclosure that effectively protects your PCBA while meeting all functional and performance requirements. Remember to collaborate closely with the PCBA design team, use 3D modeling software, and work with experienced manufacturers to ensure a successful end product.
No responses yet