Introduction to PCBA Cleaning
Printed Circuit Board Assembly (PCBA) is a crucial component in modern electronics. It is essential to keep PCBAs clean to ensure optimal performance, reliability, and longevity of the electronic devices. Contaminants such as dust, dirt, flux residues, and other debris can lead to malfunctions, short circuits, and even permanent damage to the PCBA. Therefore, it is crucial to employ safe and effective cleaning methods to maintain the integrity of the PCBA.
In this article, we will discuss various PCBA cleaning techniques, their advantages and disadvantages, and best practices for maintaining clean PCBAs.
Why is PCBA Cleaning Important?
PCBA cleaning is essential for several reasons:
-
Ensures proper functioning: Contaminants on the PCBA can interfere with the electrical signals, leading to malfunctions or complete failure of the electronic device.
-
Prevents corrosion: Flux residues, if left uncleaned, can cause corrosion on the PCBA, leading to permanent damage.
-
Improves reliability: A clean PCBA is more reliable and has a longer lifespan compared to a contaminated one.
-
Maintains aesthetic appeal: A clean PCBA looks more professional and aesthetically pleasing.
-
Complies with industry standards: Many industries have specific cleanliness requirements for PCBAs, and proper cleaning ensures compliance with these standards.
Common Contaminants on PCBAs
Before discussing the cleaning methods, let’s take a look at some common contaminants found on PCBAs:
-
Flux residues: Flux is used during soldering to prevent oxidation and improve solder joint quality. However, flux residues can be corrosive and conductive, leading to issues if not properly cleaned.
-
Dust and dirt: PCBAs can accumulate dust and dirt during the manufacturing process or in the operating environment.
-
Oils and greases: Fingerprints, lubricants, and other oils can contaminate the PCBA during handling or operation.
-
Solder balls and splashes: During the soldering process, small solder balls or splashes can land on the PCBA, causing short circuits if not removed.
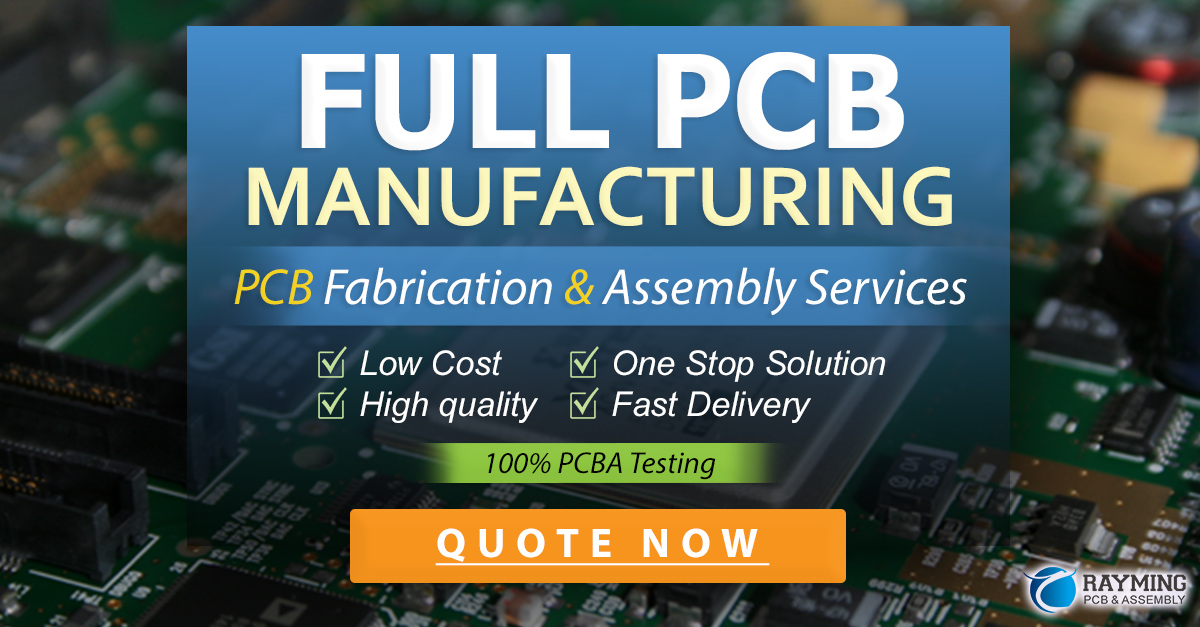
PCBA Cleaning Methods
There are several methods for cleaning PCBAs, each with its own advantages and disadvantages. The choice of the cleaning method depends on factors such as the type of contaminants, the size and complexity of the PCBA, and the available resources.
1. Manual Cleaning
Manual cleaning involves using hand tools, such as brushes, swabs, or wipes, to remove contaminants from the PCBA. This method is suitable for small-scale cleaning or hard-to-reach areas.
Advantages:
– Low cost
– Suitable for small-scale cleaning
– Can target specific areas
Disadvantages:
– Time-consuming
– Labor-intensive
– Risk of damage to components
– Inconsistent results
2. Ultrasonic Cleaning
Ultrasonic cleaning uses high-frequency sound waves to agitate a cleaning solution, creating tiny bubbles that implode and release energy, dislodging contaminants from the PCBA.
Advantages:
– Effective for removing stubborn contaminants
– Can clean complex geometries and hard-to-reach areas
– Automated process
Disadvantages:
– Higher initial cost
– Risk of damage to delicate components
– Requires compatible cleaning solutions
3. Spray Cleaning
Spray cleaning involves using a pressurized spray of cleaning solution to remove contaminants from the PCBA. The cleaning solution is typically applied using a spray gun or nozzle.
Advantages:
– Fast and efficient
– Can cover large areas quickly
– Suitable for high-volume cleaning
Disadvantages:
– Risk of over-spraying and damaging components
– Requires proper ventilation and protective equipment
– May not be effective for stubborn contaminants
4. Vapor Degreasing
Vapor degreasing uses a boiling solvent to create a vapor that condenses on the PCBA, dissolving and removing contaminants. The PCBA is then rinsed with pure solvent and dried.
Advantages:
– Highly effective for removing oils, greases, and flux residues
– Leaves no residue on the PCBA
– Automated process
Disadvantages:
– Higher initial cost
– Requires special equipment and facilities
– Some solvents may be hazardous or environmentally harmful
Cleaning Solutions
The choice of cleaning solution depends on the type of contaminants and the cleaning method employed. Some common cleaning solutions include:
-
Deionized (DI) water: DI water is a popular choice for removing water-soluble contaminants, such as flux residues.
-
Isopropyl alcohol (IPA): IPA is effective for removing oils, greases, and some flux residues. It evaporates quickly, leaving no residue.
-
Aqueous cleaners: Aqueous cleaners are water-based solutions containing surfactants and other additives. They are effective for removing a wide range of contaminants and are generally environmentally friendly.
-
Solvents: Various solvents, such as trichloroethylene, perchloroethylene, and n-propyl bromide, can be used for vapor degreasing. However, many of these solvents are being phased out due to environmental and health concerns.
Best Practices for PCBA Cleaning
To ensure safe and effective PCBA cleaning, follow these best practices:
-
Use the appropriate cleaning method and solution: Choose the cleaning method and solution based on the type of contaminants, the size and complexity of the PCBA, and the available resources.
-
Follow manufacturer’s guidelines: Always follow the manufacturer’s guidelines for the cleaning equipment and solutions to ensure optimal results and prevent damage to the PCBA.
-
Protect sensitive components: Use masking materials or remove sensitive components before cleaning to prevent damage.
-
Ensure proper ventilation: Some cleaning solutions may emit harmful fumes. Ensure proper ventilation and use protective equipment, such as gloves and respirators, when necessary.
-
Dry the PCBA thoroughly: After cleaning, ensure that the PCBA is thoroughly dried to prevent corrosion and other issues.
-
Inspect the PCBA: After cleaning and drying, inspect the PCBA for any signs of damage or remaining contaminants. Repeat the cleaning process if necessary.
FAQs
-
Q: How often should I clean my PCBA?
A: The frequency of cleaning depends on the operating environment and the level of contaminants. In general, PCBAs should be cleaned whenever there are visible contaminants or if the device experiences malfunctions due to contamination. -
Q: Can I use household cleaners to clean my PCBA?
A: No, household cleaners may contain harsh chemicals that can damage the PCBA. Always use cleaning solutions specifically designed for electronics. -
Q: Is it necessary to clean a brand new PCBA?
A: Yes, even brand new PCBAs may have contaminants from the manufacturing process. It is recommended to clean the PCBA before use to ensure optimal performance. -
Q: Can I clean a PCBA with just compressed air?
A: Compressed air can be used to remove loose dust and debris, but it is not effective for removing stubborn contaminants like flux residues or oils. A more thorough cleaning method is recommended for these contaminants. -
Q: How can I prevent my PCBA from getting contaminated?
A: To prevent contamination, store PCBAs in clean, dry environments, handle them with clean gloves, and avoid exposing them to dust, dirt, or other contaminants. Regularly inspect and clean the PCBAs to maintain their cleanliness.
Conclusion
Cleaning PCBAs is a critical aspect of maintaining the performance, reliability, and longevity of electronic devices. By understanding the common contaminants, cleaning methods, and best practices, you can ensure that your PCBAs remain clean and functional. Always choose the appropriate cleaning method and solution based on the specific needs of your PCBA, and follow the manufacturer’s guidelines to prevent damage. Regular inspections and cleaning will help you keep your PCBAs in top condition, ensuring the optimal performance of your electronic devices.
Cleaning Method | Advantages | Disadvantages |
---|---|---|
Manual Cleaning | – Low cost – Suitable for small-scale cleaning – Can target specific areas |
– Time-consuming – Labor-intensive – Risk of damage to components – Inconsistent results |
Ultrasonic Cleaning | – Effective for removing stubborn contaminants – Can clean complex geometries and hard-to-reach areas – Automated process |
– Higher initial cost – Risk of damage to delicate components – Requires compatible cleaning solutions |
Spray Cleaning | – Fast and efficient – Can cover large areas quickly – Suitable for high-volume cleaning |
– Risk of over-spraying and damaging components – Requires proper ventilation and protective equipment – May not be effective for stubborn contaminants |
Vapor Degreasing | – Highly effective for removing oils, greases, and flux residues – Leaves no residue on the PCBA – Automated process |
– Higher initial cost – Requires special equipment and facilities – Some solvents may be hazardous or environmentally harmful |
No responses yet