Understanding Rogers PCB Materials
Before diving into the specifics of Rogers PCB thickness, it’s essential to understand the different types of Rogers PCB materials available. Some of the most popular Rogers PCB laminates include:
- Rogers RO3000 Series: A ceramic-filled PTFE composite offering excellent electrical properties and low loss at high frequencies.
- Rogers RO4000 Series: A hydrocarbon ceramic laminate with low dielectric constant and loss, ideal for high-frequency applications.
- Rogers RT/duroid Series: A PTFE-based laminate with low dielectric constant and loss, suitable for microwave and millimeter-wave applications.
Each Rogers PCB material has unique properties that make it suitable for specific applications and frequency ranges.
Standard Rogers PCB Thicknesses
Rogers Corporation offers a wide range of standard thicknesses for their PCB laminates to cater to various design requirements. The following table lists the standard thicknesses available for some popular Rogers PCB materials:
Material | Standard Thicknesses (mm) |
---|---|
RO3003, RO3006 | 0.13, 0.25, 0.50, 0.75, 1.00, 1.50 |
RO3010, RO3035 | 0.13, 0.25, 0.50, 0.75, 1.00 |
RO4003C, RO4350B | 0.20, 0.25, 0.50, 0.75, 1.00, 1.50 |
RT/duroid 5870 | 0.13, 0.25, 0.50, 0.75, 1.00 |
RT/duroid 5880 | 0.13, 0.25, 0.50, 0.75, 1.00, 1.50, 2.00 |
It’s important to note that not all thicknesses may be available for every copper weight or panel size. Always consult the manufacturer’s datasheet or contact a Rogers representative for the most up-to-date information on available thicknesses.
Factors Influencing Rogers PCB Thickness Selection
When selecting the appropriate thickness for your Rogers PCB, several factors need to be considered:
Electrical Performance
The thickness of the Rogers PCB laminate can significantly impact its electrical properties, such as impedance, signal integrity, and loss tangent. Thinner laminates generally offer better high-frequency performance due to reduced dielectric loss and improved impedance control. However, thinner laminates may also be more susceptible to signal integrity issues, such as crosstalk and electromagnetic interference (EMI).
Mechanical Strength
The mechanical strength of the Rogers PCB is directly related to its thickness. Thicker laminates provide greater rigidity and resistance to bending, vibration, and impact. This is particularly important for applications that require high reliability or are subject to harsh environmental conditions. However, thicker laminates may also increase the overall weight and size of the PCB Assembly.
Thermal Management
The thickness of the Rogers PCB can also affect its thermal management properties. Thicker laminates have a higher thermal mass and can dissipate heat more effectively, which is crucial for high-power applications. On the other hand, thinner laminates may offer better thermal transfer to an external heatsink or cooling system.
Manufacturing Considerations
The choice of Rogers PCB thickness can impact the manufacturability and cost of the final product. Thinner laminates may require more precise handling and processing, leading to higher manufacturing costs. Additionally, certain PCB fabrication processes, such as drilling and plating, may have limitations on the minimum or maximum thickness that can be accommodated.
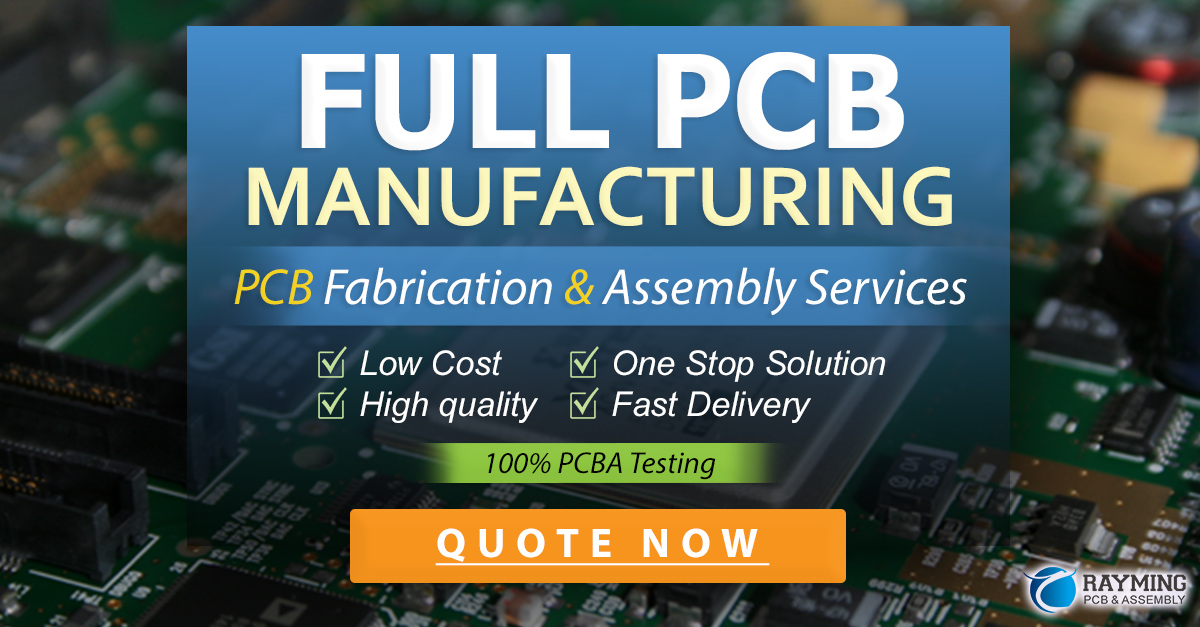
Custom Rogers PCB Thicknesses
In some cases, the standard thicknesses offered by Rogers Corporation may not meet the specific requirements of a design. In such situations, custom thicknesses can be requested. However, custom thicknesses may be subject to minimum order quantities, longer lead times, and higher costs compared to standard thicknesses.
When considering a custom thickness, it’s essential to engage with a Rogers representative or an experienced PCB fabricator to discuss the feasibility, timeline, and cost implications of the custom solution.
Multilayer Rogers PCB Thickness Considerations
Multilayer Rogers PCBs introduce additional complexity when it comes to thickness selection. The overall thickness of a multilayer PCB depends on the number of layers, the thickness of each individual layer, and the thickness of the prepreg used to bond the layers together.
When designing a multilayer Rogers PCB, it’s crucial to consider the following factors:
Layer Count and Stacking
The number of layers in a multilayer Rogers PCB directly affects its overall thickness. As the layer count increases, so does the total thickness of the PCB. The stacking order of the layers, including signal, ground, and power planes, also impacts the electrical performance and mechanical integrity of the PCB.
Prepreg Thickness
Prepreg is a partially cured resin-impregnated fabric used to bond the layers of a multilayer PCB together. The thickness of the prepreg can vary and contributes to the overall thickness of the PCB. Thicker prepregs provide better inter-layer adhesion and mechanical strength, while thinner prepregs allow for tighter layer spacing and improved electrical performance.
Impedance Control
In high-speed digital and RF applications, controlling the impedance of the signal traces is critical for maintaining signal integrity. The thickness of the dielectric material between the signal trace and the reference plane (ground or power) directly affects the characteristic impedance of the trace. Careful selection of layer thicknesses and dielectric materials is necessary to achieve the desired impedance and minimize signal distortion.
FAQ
-
Q: What is the thinnest Rogers PCB laminate available?
A: The thinnest standard thickness for Rogers PCB laminates is typically 0.13 mm (5 mils). However, not all Rogers materials may be available in this thickness. Always consult the manufacturer’s datasheet for the specific material you are interested in. -
Q: Can I use a thicker Rogers PCB laminate for high-frequency applications?
A: While thinner laminates generally offer better high-frequency performance, thicker laminates can still be used in high-frequency applications. The choice of thickness depends on the specific requirements of your design, such as mechanical strength, thermal management, and manufacturability. -
Q: How does the thickness of Rogers PCB affect its cost?
A: The thickness of Rogers PCB can impact its cost in several ways. Thinner laminates may require more precise handling and processing, leading to higher manufacturing costs. Thicker laminates may be more expensive due to the increased material usage. Additionally, custom thicknesses may be subject to minimum order quantities and higher prices compared to standard thicknesses. -
Q: Can I mix different thicknesses of Rogers PCB laminates in a multilayer PCB?
A: Yes, it is possible to use different thicknesses of Rogers PCB laminates in a multilayer PCB. This is often done to optimize the electrical performance, mechanical strength, and thermal management of the PCB. However, mixing different thicknesses can increase the complexity of the design and manufacturing process, so it’s essential to work closely with an experienced PCB fabricator. -
Q: How do I select the appropriate thickness for my Rogers PCB design?
A: Selecting the appropriate thickness for your Rogers PCB design involves considering multiple factors, such as electrical performance, mechanical strength, thermal management, and manufacturing constraints. It’s recommended to consult with a Rogers representative or an experienced PCB design engineer to discuss your specific requirements and determine the optimal thickness for your application.
Conclusion
The thickness of Rogers PCB is a critical parameter that impacts its electrical performance, mechanical strength, thermal management, and manufacturability. Rogers Corporation offers a wide range of standard thicknesses for their high-performance PCB laminates, catering to various design requirements. When selecting the appropriate thickness for your Rogers PCB, it’s essential to consider factors such as electrical properties, mechanical stability, thermal dissipation, and manufacturing constraints.
For multilayer Rogers PCBs, additional considerations come into play, such as layer count, stacking order, prepreg thickness, and impedance control. Engaging with a Rogers representative or an experienced PCB design engineer can help you navigate these complexities and make informed decisions about the optimal thickness for your application.
By understanding the available options and key considerations for Rogers PCB thickness, you can design and manufacture high-performance PCBs that meet your specific requirements and excel in demanding RF and microwave applications.
No responses yet