Factors Affecting PCB cost
1. Board Size and Complexity
The size and complexity of your PCB design play a crucial role in determining the overall cost. Larger boards require more material and may take longer to manufacture, resulting in higher costs. Additionally, complex designs with intricate traces, multiple layers, and high component density will also increase the price.
Board Size | Complexity | Cost Impact |
---|---|---|
Small | Simple | Low |
Small | Complex | Medium |
Large | Simple | Medium |
Large | Complex | High |
2. Number of Layers
PCBs can be manufactured with varying numbers of layers, ranging from single-layer to multi-layer boards. The more layers a PCB has, the higher the cost will be. This is because additional layers require more material, processing time, and precision during the manufacturing process.
Number of Layers | Cost Impact |
---|---|
1-2 | Low |
4 | Medium |
6-8 | High |
10+ | Very High |
3. Material Selection
The choice of materials used in the PCB fabrication process can also affect the overall cost. The most common PCB material is FR-4, which is a glass-reinforced epoxy laminate. However, there are other specialized materials available for specific applications, such as high-frequency or high-temperature environments. These specialized materials often come with a higher price tag.
Material | Cost Impact |
---|---|
FR-4 | Standard |
Rogers | High |
Polyimide | High |
Aluminum | Medium |
4. Surface Finish
The surface finish of a PCB refers to the coating applied to the exposed copper traces and pads to protect them from oxidation and enhance solderability. Different surface finishes have varying costs associated with them. Some common surface finishes include:
- HASL (Hot Air Solder Leveling)
- ENIG (Electroless Nickel Immersion Gold)
- OSP (Organic Solderability Preservative)
- Immersion Silver
- Immersion Tin
Surface Finish | Cost Impact |
---|---|
HASL | Low |
OSP | Low |
Immersion Tin | Medium |
Immersion Silver | Medium |
ENIG | High |
5. Quantity and Lead Time
The quantity of PCBs you order and the lead time you require can significantly influence the cost per board. Ordering larger quantities often results in a lower cost per unit due to economies of scale. However, if you need a quick turnaround time, you may incur additional charges for expedited manufacturing and shipping.
Quantity | Lead Time | Cost Impact |
---|---|---|
Low | Standard | High |
Low | Expedited | Very High |
High | Standard | Low |
High | Expedited | Medium |
PCB Cost Estimation
To get a rough idea of how much your PCB might cost, you can use online PCB cost calculators provided by various manufacturers. These calculators take into account the factors mentioned above and provide you with an estimated price based on your specific requirements.
However, for a more accurate quote, it is always best to directly contact the PCB manufacturer with your design files and specifications. They will be able to provide you with a detailed breakdown of the costs involved and help you optimize your design for cost-effectiveness, if necessary.
Cost-Saving Strategies
If you’re looking to reduce the cost of your PCBs, consider the following strategies:
-
Optimize your design for manufacturability: Work with your PCB manufacturer to ensure that your design is optimized for their manufacturing processes. This can help reduce the complexity and cost of your boards.
-
Choose standard specifications: Whenever possible, opt for standard PCB specifications, such as board thickness, copper weight, and surface finish. Custom specifications may increase the cost and lead time.
-
Order in bulk: If you require a large number of PCBs, consider placing a bulk order to take advantage of volume discounts.
-
Plan ahead: Rushing a PCB order can significantly increase the cost. By planning ahead and allowing for longer lead times, you can save money on your PCB production.
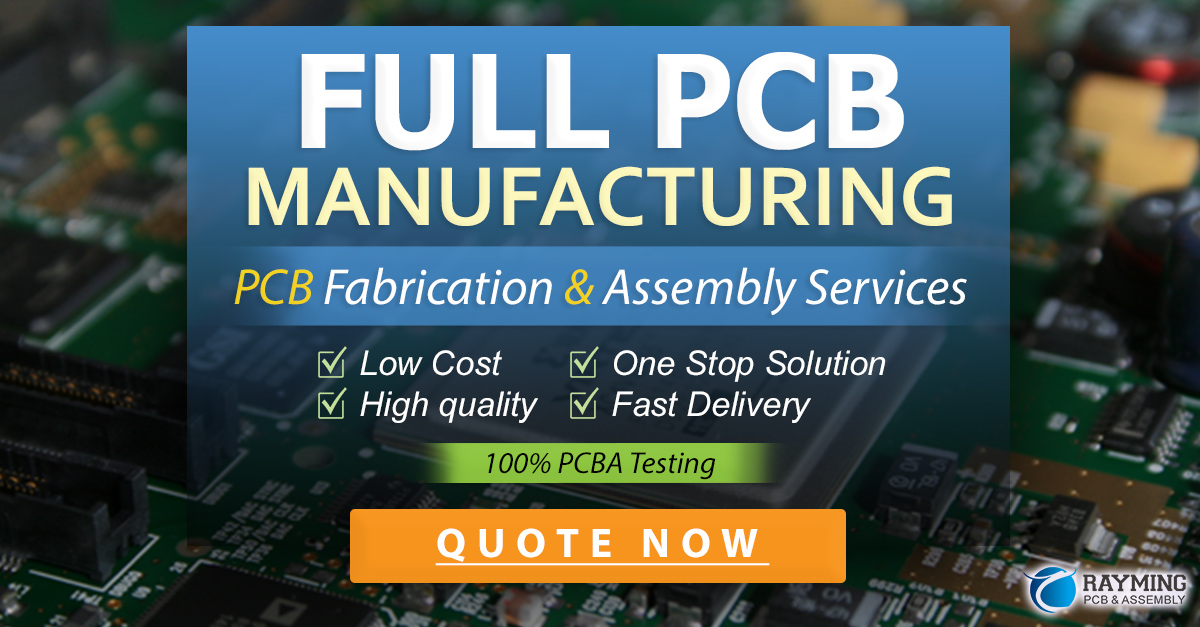
FAQ
1. What is the minimum cost for a single PCB?
The minimum cost for a single PCB can vary depending on the manufacturer, but it typically ranges from $10 to $50, depending on the size, complexity, and specifications of the board.
2. How much does a 4-layer PCB cost compared to a 2-layer PCB?
A 4-layer PCB usually costs about 30-50% more than a 2-layer PCB with the same specifications. This is due to the additional materials and processing required for the extra layers.
3. Can I get a discount for ordering a large quantity of PCBs?
Yes, most PCB manufacturers offer volume discounts for larger orders. The more PCBs you order, the lower the cost per unit will be.
4. How long does it typically take to manufacture a PCB?
The lead time for PCB manufacturing can range from a few days to several weeks, depending on the complexity of the design, the manufacturer’s workload, and the shipping method chosen. Standard lead times are usually between 1-2 weeks.
5. Are there any additional costs I should be aware of when ordering PCBs?
Yes, there may be additional costs for services such as design review, file preparation, tooling, and shipping. Be sure to discuss any potential extra costs with your PCB manufacturer before placing your order.
In conclusion, the cost of a PCB board depends on various factors, including the size, complexity, number of layers, material selection, surface finish, quantity, and lead time. By understanding these factors and working closely with your PCB manufacturer, you can make informed decisions and optimize your design to achieve the best balance between cost and performance for your project.
No responses yet