What is PCB Solder Mask?
PCB solder mask, also known as solder resist or solder stop mask, is a thin layer of polymer applied to the copper traces of a printed circuit board (PCB). Its primary purpose is to protect the copper traces from oxidation, prevent solder bridges from forming between closely spaced pads, and provide electrical insulation. Solder mask also serves as a barrier against environmental contaminants and improves the PCB’s overall durability.
Composition of Solder Mask
Solder mask is typically composed of epoxy or acrylic-based materials that are mixed with fillers, pigments, and other additives to achieve the desired properties. The most common solder mask colors are green, red, blue, and black, although other colors are available for specific applications or aesthetic purposes.
Property | Description |
---|---|
Electrical Insulation | High dielectric strength to prevent short circuits |
Chemical Resistance | Resistant to acids, alkalis, and solvents used in PCB Manufacturing and assembly |
Thermal Stability | Able to withstand high temperatures during soldering processes |
Adhesion | Strong adhesion to the PCB surface to prevent delamination |
UV Resistance | Resistant to UV light exposure to prevent degradation over time |
PCB Solder Mask Application Methods
There are several methods for applying solder mask to a PCB, each with its advantages and limitations. The choice of application method depends on factors such as the PCB’s complexity, the required precision, and the production volume.
1. Screen Printing
Screen printing is the most common method for applying solder mask to PCBs. It involves using a fine mesh screen with a stencil of the desired solder mask pattern. The solder mask ink is forced through the screen onto the PCB surface using a squeegee. The PCB is then cured in an oven to harden the solder mask.
Advantages of Screen Printing
- Cost-effective for high-volume production
- Suitable for simple PCB Designs
- Relatively fast process
Limitations of Screen Printing
- Limited precision compared to other methods
- Not suitable for complex PCB designs with fine features
- Requires frequent screen cleaning and maintenance
2. Liquid Photo Imageable (LPI) Solder Mask
LPI solder mask is a photosensitive polymer that is applied to the PCB surface as a liquid. The PCB is then exposed to UV light through a photomask, which hardens the exposed areas of the solder mask. The unexposed areas are then removed using a developer solution, leaving the desired solder mask pattern on the PCB.
Advantages of LPI Solder Mask
- High precision and resolution
- Suitable for complex PCB designs with fine features
- Excellent electrical insulation properties
Limitations of LPI Solder Mask
- More expensive than screen printing
- Slower process compared to screen printing
- Requires specialized equipment and materials
3. Dry Film Solder Mask
Dry film solder mask is a solid photosensitive film that is laminated onto the PCB surface using heat and pressure. The PCB is then exposed to UV light through a photomask, which crosslinks the exposed areas of the film. The unexposed areas are removed using a developer solution, leaving the desired solder mask pattern on the PCB.
Advantages of Dry Film Solder Mask
- High precision and resolution
- Suitable for complex PCB designs with fine features
- Faster than LPI solder mask application
Limitations of Dry Film Solder Mask
- More expensive than screen printing
- Requires specialized equipment for lamination and exposure
- May not conform well to irregular PCB surfaces
4. Inkjet Printing
Inkjet printing is an emerging technology for applying solder mask to PCBs. It involves using a high-resolution inkjet printer to deposit the solder mask ink directly onto the PCB surface. The PCB is then cured in an oven to harden the solder mask.
Advantages of Inkjet Printing
- High precision and resolution
- Suitable for complex PCB designs with fine features
- Minimal waste and low setup costs
Limitations of Inkjet Printing
- Slower than other methods
- Limited availability of compatible solder mask inks
- May require multiple passes to achieve the desired thickness
Solder Mask Application Process
Regardless of the chosen application method, the solder mask application process generally follows these steps:
-
PCB Cleaning: The PCB surface is thoroughly cleaned to remove any contaminants that may affect solder mask adhesion.
-
Solder Mask Application: The solder mask is applied to the PCB surface using one of the methods described above.
-
Curing: The PCB is heated in an oven to cure the solder mask, making it hard and durable.
-
Inspection: The PCB is inspected for defects such as pinholes, bubbles, or incomplete coverage. Any defects are repaired or the PCB is reworked if necessary.
-
Final Finish: The exposed copper pads are coated with a final finish, such as HASL, RAYPCB/”>ENIG, or OSP, to protect them from oxidation and enhance solderability.
Step | Description |
---|---|
PCB Cleaning | Remove contaminants from the PCB surface |
Solder Mask Application | Apply solder mask using the chosen method |
Curing | Heat the PCB to cure the solder mask |
Inspection | Check for defects and repair if necessary |
Final Finish | Apply a protective coating to exposed copper pads |
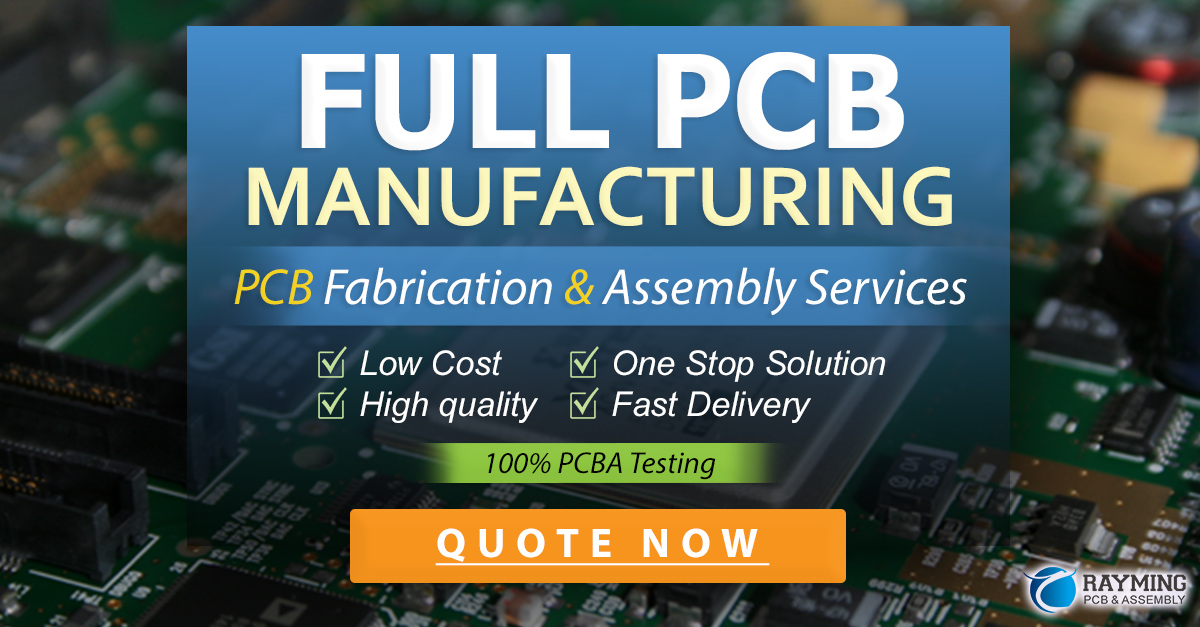
Solder Mask Design Considerations
When designing a PCB with solder mask, there are several factors to consider to ensure optimal performance and manufacturability:
1. Solder Mask Clearance
Solder mask clearance refers to the distance between the edge of a copper pad and the edge of the solder mask opening. Adequate clearance is necessary to ensure proper solder joint formation and prevent solder mask from interfering with the soldering process.
Pad Size | Minimum Solder Mask Clearance |
---|---|
≤ 0.5 mm | 0.05 mm |
0.5 – 1.0 mm | 0.075 mm |
1.0 – 2.0 mm | 0.1 mm |
> 2.0 mm | 0.15 mm |
2. Solder Mask Thickness
Solder mask thickness is critical for providing adequate insulation and protection to the PCB. The typical thickness range for solder mask is between 0.01 mm and 0.03 mm. Thicker solder mask may be required for high-voltage applications or to improve durability.
3. Solder Mask Color
The choice of solder mask color is primarily driven by aesthetic considerations, as it does not significantly affect the PCB’s performance. However, some colors may have slightly different properties, such as thermal absorption or UV resistance.
4. Solder Mask Surface Finish
The surface finish of the solder mask can impact its ability to repel moisture and contaminants. A glossy finish is generally preferred for its better protection and ease of cleaning, while a matte finish may be chosen for its improved ink adhesion and aesthetic appeal.
Frequently Asked Questions (FAQ)
-
What is the purpose of solder mask on a PCB?
Solder mask serves multiple purposes on a PCB, including protecting the copper traces from oxidation, preventing solder bridges between closely spaced pads, providing electrical insulation, and improving the PCB’s overall durability. -
What are the most common solder mask application methods?
The most common solder mask application methods are screen printing, liquid photo imageable (LPI) solder mask, dry film solder mask, and inkjet printing. Each method has its advantages and limitations, and the choice depends on factors such as PCB complexity, required precision, and production volume. -
What is the typical thickness of solder mask on a PCB?
The typical thickness range for solder mask is between 0.01 mm and 0.03 mm. Thicker solder mask may be required for high-voltage applications or to improve durability. -
Does solder mask color affect PCB performance?
Solder mask color is primarily chosen for aesthetic reasons and does not significantly affect PCB performance. However, some colors may have slightly different properties, such as thermal absorption or UV resistance. -
What is solder mask clearance, and why is it important?
Solder mask clearance refers to the distance between the edge of a copper pad and the edge of the solder mask opening. Adequate clearance is necessary to ensure proper solder joint formation and prevent solder mask from interfering with the soldering process. The minimum clearance depends on the pad size and ranges from 0.05 mm to 0.15 mm.
No responses yet