Factors Influencing PCB pricing
Several key factors contribute to the overall cost of a PCB. These include:
- Board Size and Complexity
- Layer Count
- Material Selection
- Surface Finish
- Quantity and Lead Time
- Additional Features and Services
Let’s explore each of these factors in detail.
Board Size and Complexity
The size and complexity of a PCB have a significant impact on its pricing. Larger boards require more material and may be more challenging to manufacture, resulting in higher costs. Additionally, complex designs with intricate traces, tight tolerances, and high component density can increase the manufacturing complexity and, consequently, the price.
PCB sizes are typically categorized as follows:
Size Category | Dimensions (mm) |
---|---|
Small | < 100 x 100 |
Medium | 100 x 100 – 200 x 200 |
Large | > 200 x 200 |
As a general rule, larger PCBs tend to cost more than smaller ones due to increased material usage and manufacturing complexity.
Layer Count
The number of layers in a PCB directly affects its price. Each additional layer requires more material, processing, and labor, resulting in higher costs. Here’s a breakdown of common layer counts and their relative costs:
Layer Count | Relative Cost |
---|---|
1-2 Layers | Low |
4 Layers | Medium |
6-8 Layers | High |
10+ Layers | Very High |
Single and double-layer PCBs are the most cost-effective options, while multi-layer boards (4 layers or more) are used for more complex designs that require higher circuit density and better signal integrity.
Material Selection
The choice of PCB material directly impacts its performance, reliability, and cost. The most common PCB materials are:
-
FR-4: A glass-reinforced epoxy laminate, FR-4 is the most widely used PCB material due to its good electrical insulation properties, mechanical strength, and cost-effectiveness.
-
High-Frequency Materials: For applications requiring high-frequency operation or low dielectric loss, materials like Rogers, Teflon, or ceramic-based laminates are used. These materials are more expensive than FR-4.
-
Flexible Materials: Flexible PCBs use materials like polyimide or polyester to allow for bending and flexing. These materials are generally more expensive than rigid PCB materials.
The cost of the PCB material is determined by its type, thickness, and the quantity required for your project.
Surface Finish
The surface finish of a PCB is essential for protecting the copper traces and pads from oxidation and ensuring good solderability. Different surface finishes have varying costs and performance characteristics. Common surface finishes include:
- Hot Air Solder Leveling (HASL)
- Organic Solderability Preservative (OSP)
- Immersion Silver
- Immersion Tin
- Electroless Nickel Immersion Gold (ENIG)
HASL and OSP are the most cost-effective options, while ENIG is more expensive but offers superior durability and shelf life.
Quantity and Lead Time
The quantity of PCBs you order and the lead time you require can significantly influence the pricing. Manufacturers often offer volume discounts for larger orders, as the fixed costs associated with setting up the production line can be spread across more units. Here’s an example of how quantity can affect the unit price:
Quantity | Unit Price |
---|---|
1-10 | $50 |
11-50 | $40 |
51-100 | $35 |
101-500 | $30 |
500+ | $25 |
Shorter lead times may also incur additional charges, as manufacturers may need to prioritize your order and adjust their production schedule.
Additional Features and Services
PCB manufacturers offer various additional features and services that can impact the final cost of your PCB. These include:
-
Solder Mask: A protective layer applied over the copper traces to prevent short circuits and improve the PCB’s appearance. Different colors are available, with green being the most common and cost-effective option.
-
Silkscreen: A text or graphic printed on the PCB for component labeling and branding purposes. White is the standard color, while other colors may incur additional costs.
-
Impedance Control: For high-speed or high-frequency applications, precise control of the PCB’s impedance is necessary. This requires specialized manufacturing techniques and can increase the cost.
-
Controlled Impedance: Ensures consistent impedance across the PCB for high-speed signal integrity. This service typically adds 20-30% to the base PCB Cost.
-
Via Filling: Filling vias with conductive material to improve thermal conductivity and signal integrity. This service can add 10-20% to the base PCB cost.
-
Design Review and Optimization: Many PCB manufacturers offer design review services to help optimize your design for manufacturability and cost-effectiveness.
Calculating PCB Price
To calculate the approximate price of your PCB, follow these steps:
- Determine the size and complexity of your PCB design.
- Identify the required number of layers.
- Select the appropriate material based on your application’s requirements.
- Choose the desired surface finish.
- Specify the quantity and lead time for your order.
- Consider any additional features or services you may need.
Once you have this information, you can request quotes from various PCB manufacturers or use online PCB cost calculators to estimate the price of your project.
For example, let’s calculate the price for a medium-sized, 4-layer PCB with HASL surface finish, green solder mask, and white silkscreen. We’ll assume an order quantity of 100 units and a standard lead time.
Factor | Specification | Price Contribution |
---|---|---|
Size | Medium | $10 |
Layer Count | 4 Layers | $30 |
Material | FR-4 | $5 |
Surface Finish | HASL | $5 |
Quantity | 100 units | $35 per unit |
Additional Features | Solder Mask (Green), Silkscreen (White) | $5 |
The estimated price for this PCB would be: $35 (unit price) + $5 (additional features) = $40 per unit. The total cost for 100 units would be approximately $4,000.
Cost Optimization Strategies
To optimize the cost of your PCB project, consider the following strategies:
- Minimize the board size and complexity where possible.
- Reduce the number of layers if your design allows for it.
- Choose cost-effective materials that meet your application’s requirements.
- Select a budget-friendly surface finish, such as HASL or OSP, if suitable for your project.
- Order in larger quantities to benefit from volume discounts.
- Plan ahead to allow for standard lead times and avoid rush charges.
- Optimize your design for manufacturability to reduce the likelihood of production issues and delays.
By carefully considering these factors and working closely with your PCB manufacturer, you can effectively manage the cost of your PCB project while ensuring the desired performance and reliability.
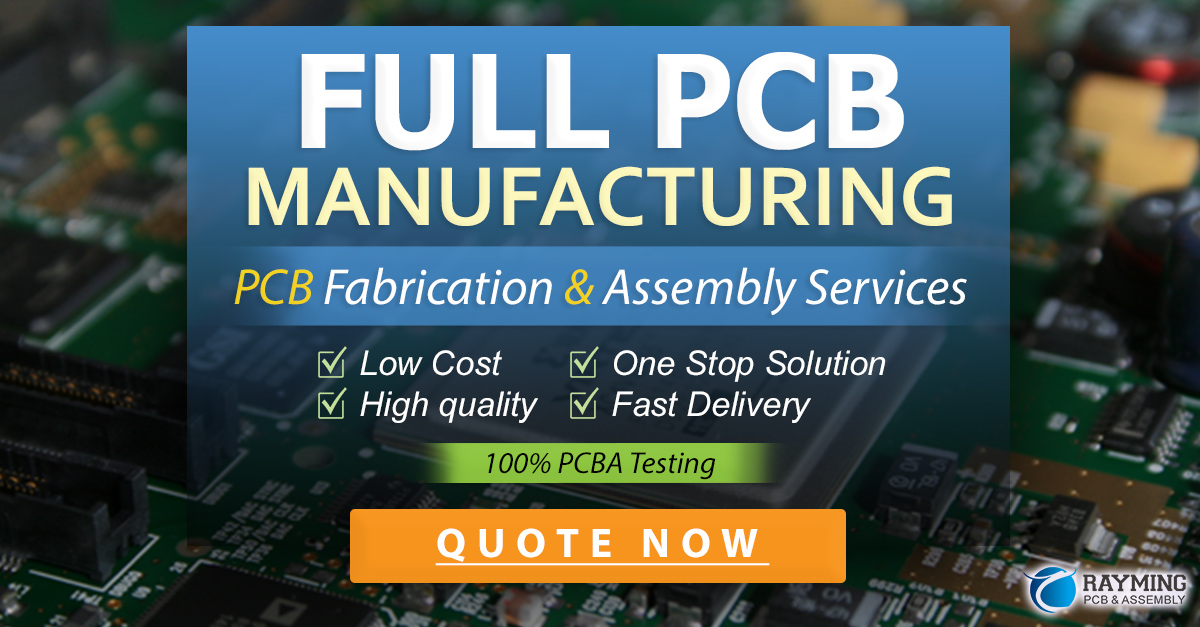
Frequently Asked Questions (FAQ)
-
What is the most cost-effective PCB material?
FR-4 is the most cost-effective and widely used PCB material. It offers good electrical insulation properties, mechanical strength, and thermal stability at a relatively low cost compared to other materials. -
How does the number of layers affect PCB pricing?
The number of layers in a PCB directly impacts its price. Each additional layer requires more material, processing, and labor, resulting in higher costs. Single and double-layer PCBs are the most cost-effective options, while multi-layer boards (4 layers or more) are used for more complex designs but come at a higher price point. -
Can I reduce the cost of my PCB by ordering a larger quantity?
Yes, ordering a larger quantity of PCBs can often result in a lower unit price. Manufacturers offer volume discounts for larger orders, as the fixed costs associated with setting up the production line can be spread across more units. However, it’s essential to balance the potential cost savings with your actual needs and storage capabilities. -
What is the most economical surface finish for PCBs?
Hot Air Solder Leveling (HASL) and Organic Solderability Preservative (OSP) are the most cost-effective surface finish options for PCBs. They provide good solderability and protection against oxidation at a lower cost compared to other surface finishes like Immersion Silver or Electroless Nickel Immersion Gold (ENIG). -
How can I optimize my PCB design to reduce costs?
To optimize your PCB design for cost reduction, consider the following strategies: - Minimize the board size and complexity where possible.
- Reduce the number of layers if your design allows for it.
- Choose cost-effective materials that meet your application’s requirements.
- Select a budget-friendly surface finish, such as HASL or OSP, if suitable for your project.
- Optimize your component placement and routing to improve manufacturability and reduce the likelihood of production issues.
- Work closely with your PCB manufacturer to identify potential cost-saving opportunities in your design.
By understanding the factors that influence PCB pricing and implementing cost optimization strategies, you can effectively manage the budget for your PCB project while ensuring the desired performance and reliability.
No responses yet