Introduction to PCB Electrical Testing
Printed Circuit Boards (PCBs) are the backbone of modern electronics, found in everything from smartphones to medical devices. To ensure that these PCBs function as intended, they must undergo rigorous testing, including electrical testing. In this article, we will explore the world of PCB electrical testing, its importance, and the various methods used in the industry.
What is PCB Electrical Testing?
PCB electrical testing is a crucial step in the manufacturing process that verifies the electrical performance and functionality of a printed circuit board. It involves subjecting the PCB to various tests to ensure that it meets the specified requirements and is free from defects that could lead to malfunctions or failures.
Why is PCB Electrical Testing Important?
Electrical testing is essential for several reasons:
-
Quality Assurance: Testing ensures that the PCB meets the required specifications and performs as intended, reducing the risk of defective products reaching the end-users.
-
Reliability: Thorough testing helps identify and eliminate potential issues that could lead to premature failure or malfunction of the PCB, enhancing its reliability.
-
Cost Savings: Detecting and addressing defects early in the manufacturing process saves costs associated with rework, repairs, or product recalls.
-
Compliance: Electrical testing helps ensure that the PCB complies with industry standards and regulations, such as IPC (Institute of Printed Circuits) and RoHS (Restriction of Hazardous Substances).
Types of PCB Electrical Tests
There are various types of electrical tests performed on PCBs, each designed to assess specific aspects of the board’s performance. Some of the most common tests include:
Continuity Test
The continuity test verifies that there are no open circuits or broken connections on the PCB. It checks the electrical continuity between two points on the board, ensuring that current can flow uninterrupted through the intended paths.
Short Circuit Test
The short circuit test checks for unintended connections between circuit paths that should be isolated from each other. A short circuit can cause the PCB to malfunction or even damage connected components.
Insulation Resistance Test
The insulation resistance test measures the resistance between isolated conductors on the PCB, such as between adjacent traces or between a trace and the ground plane. This test ensures that there is sufficient insulation to prevent current leakage and cross-talk between signals.
Dielectric Withstanding Voltage (DWV) Test
The DWV test, also known as the hipot (high potential) test, checks the PCB’s ability to withstand high voltages without breaking down the insulation. This test is crucial for ensuring the safety and reliability of the PCB in high-voltage applications.
Flying Probe Test
The flying probe test is an automated test method that uses movable test probes to contact specific points on the PCB. This test is highly flexible and can be used for both prototyping and low-volume production. It is capable of performing continuity, short circuit, and component tests.
In-Circuit Test (ICT)
The in-circuit test is an automated test method that uses a bed-of-nails fixture to make contact with specific points on the PCB. ICT can test for continuity, short circuits, component values, and functionality. It is well-suited for high-volume production and can quickly identify defects.
Functional Test
The functional test verifies that the PCB performs its intended functions as designed. This test typically involves powering up the board and running a series of test routines to check the operation of various subsystems, such as memory, input/output ports, and communication interfaces.
PCB Electrical Testing Equipment
To perform electrical tests on PCBs, manufacturers use a variety of specialized equipment. Some of the most common types of equipment include:
Multimeters
Multimeters are versatile instruments that can measure voltage, current, resistance, and continuity. They are often used for manual testing and troubleshooting of PCBs.
Oscilloscopes
Oscilloscopes are used to visualize and analyze electrical signals on a PCB. They display the voltage of a signal over time, allowing engineers to detect and diagnose issues related to signal integrity, timing, and noise.
Automated Test Equipment (ATE)
ATE systems are computer-controlled test platforms that can perform a wide range of electrical tests on PCBs. They typically consist of a test fixture, a set of programmable instruments, and software for test development and execution. ATE systems are used for both in-circuit and functional testing.
Boundary Scan Test Equipment
Boundary scan test equipment is used to test PCBs designed with boundary scan technology (IEEE 1149.1 standard). This equipment can test for continuity, short circuits, and functionality of digital components on the board without the need for physical access to individual pins.
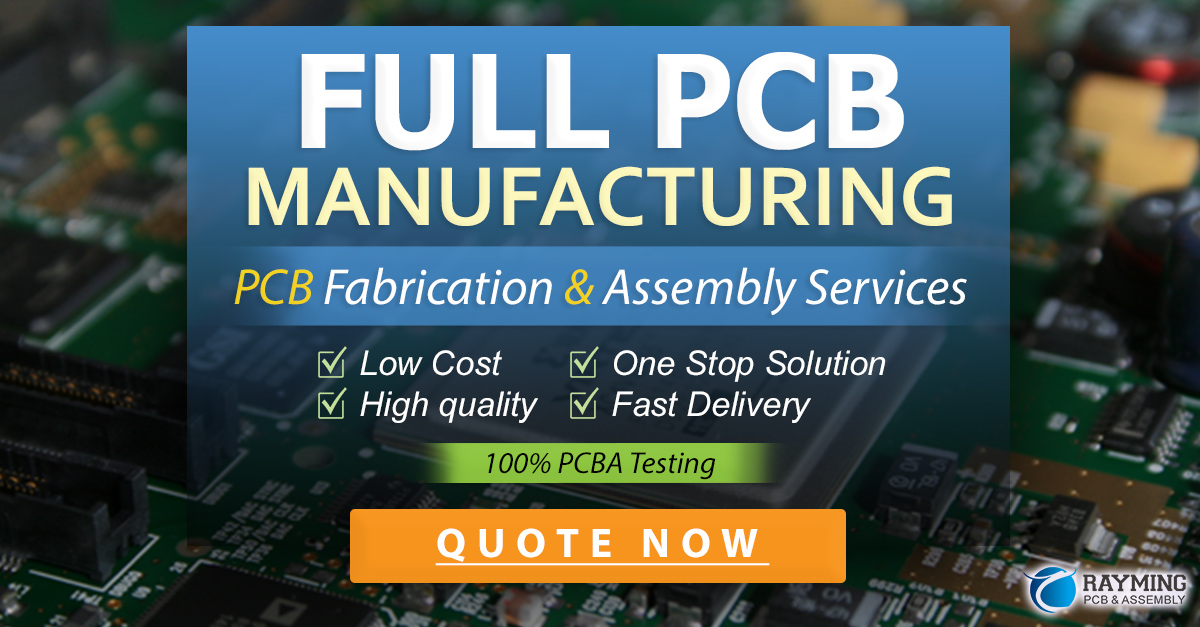
PCB Electrical Testing Procedures
The electrical testing process typically involves the following steps:
-
Test Planning: Develop a comprehensive test plan that outlines the specific tests to be performed, the test conditions, and the acceptance criteria.
-
Test Fixture Design: Create a custom test fixture that provides electrical access to the PCB for testing. The fixture should be designed to minimize the risk of damage to the board and ensure reliable contact with the test points.
-
Test Program Development: Develop test programs or scripts that automate the execution of the planned tests. These programs should control the test equipment, apply the necessary stimuli, and capture the test results.
-
Test Execution: Run the test programs and monitor the results. If any failures are detected, investigate the root cause and take appropriate corrective actions.
-
Test Reporting: Generate test reports that document the test results, including any failures and the actions taken to resolve them. These reports serve as evidence of the PCB’s electrical performance and compliance with requirements.
Benefits of Automated PCB Electrical Testing
Automated electrical testing offers several advantages over manual testing methods:
-
Speed: Automated tests can be executed much faster than manual tests, reducing the overall test time and increasing throughput.
-
Consistency: Automated tests ensure that the same test conditions are applied consistently to every PCB, reducing the risk of human error and variability in test results.
-
Repeatability: Automated tests can be easily repeated, allowing for quick retesting of boards that have undergone rework or repair.
-
Scalability: Automated test systems can be scaled up to handle higher production volumes without significantly increasing the test time or resources required.
Challenges in PCB Electrical Testing
Despite the many benefits of electrical testing, there are some challenges that manufacturers must address:
-
Test Coverage: Ensuring that all critical aspects of the PCB’s electrical performance are adequately tested can be challenging, especially for complex designs with high component densities.
-
Test Access: As PCBs become more compact and densely populated, accessing test points for probing can be difficult. Designers must consider testability during the PCB layout process to ensure adequate test access.
-
Test Fixture Maintenance: Test fixtures are subject to wear and tear over time, which can affect the reliability of the test results. Regular maintenance and calibration of test fixtures are essential to ensure accurate and consistent testing.
-
Keeping Up with Technology: As new technologies and components are introduced, test equipment and methods must be updated to accommodate them. This requires ongoing investment in equipment and training for test engineers.
Conclusion
PCB electrical testing is a critical aspect of the manufacturing process that ensures the quality, reliability, and functionality of printed circuit boards. By employing a combination of manual and automated test methods, manufacturers can identify and address defects early, reducing costs and improving customer satisfaction. As PCB designs continue to evolve and become more complex, the importance of robust electrical testing will only continue to grow.
Frequently Asked Questions (FAQ)
1. What is the difference between in-circuit testing (ICT) and functional testing?
In-circuit testing focuses on verifying the presence, orientation, and value of individual components on the PCB, as well as checking for continuity and short circuits. Functional testing, on the other hand, tests the overall performance of the PCB as a complete system, ensuring that it functions as intended in its final application.
2. Can all PCBs be tested using automated test equipment (ATE)?
While ATE systems are highly versatile and can test a wide range of PCBs, some boards may require manual testing or specialized test equipment due to their unique design or requirements. For example, high-frequency or RF PCBs may require specialized test equipment to accurately measure their performance.
3. How often should test fixtures be maintained and calibrated?
The frequency of test fixture maintenance and calibration depends on factors such as the usage intensity, the type of tests performed, and the environment in which the fixtures are used. As a general rule, test fixtures should be inspected and cleaned regularly, and calibration should be performed at least annually or whenever there are signs of degraded performance.
4. What is the role of test coverage analysis in PCB electrical testing?
Test coverage analysis is the process of evaluating the extent to which a test plan or test suite covers the various aspects of a PCB’s electrical performance. It helps identify areas that may be insufficiently tested, allowing test engineers to refine their test plans and ensure comprehensive coverage of the board’s functionality.
5. How can PCB designers improve the testability of their designs?
PCB designers can improve testability by considering test access early in the design process. This includes providing adequate test points, using boundary scan technology where appropriate, and adhering to design for testability (DFT) principles. By collaborating with test engineers and incorporating testability features into the PCB layout, designers can help streamline the testing process and improve overall product quality.
Test Type | Purpose | Advantages | Disadvantages |
---|---|---|---|
Continuity Test | Checks for open circuits and broken connections | Simple and quick to perform | Limited to detecting open circuits |
Short Circuit Test | Checks for unintended connections between circuit paths | Identifies potential short circuits that can cause malfunctions | May not detect all types of shorts, such as resistive shorts |
Insulation Resistance Test | Measures resistance between isolated conductors | Ensures sufficient insulation to prevent current leakage and cross-talk | Can be time-consuming for large or complex PCBs |
Dielectric Withstanding Voltage (DWV) Test | Checks the PCB’s ability to withstand high voltages | Crucial for ensuring safety and reliability in high-voltage applications | Requires specialized high-voltage test equipment |
Flying Probe Test | Automated test using movable test probes | Highly flexible and suitable for prototyping and low-volume production | Slower than other automated test methods |
In-Circuit Test (ICT) | Automated test using a bed-of-nails fixture | Well-suited for high-volume production and can quickly identify defects | Requires custom test fixtures and may not detect all types of faults |
Functional Test | Verifies that the PCB performs its intended functions | Tests the overall performance of the PCB as a complete system | May require specialized test equipment and can be time-consuming |
In conclusion, PCB electrical testing is a multi-faceted process that involves a range of test methods, equipment, and procedures. By understanding the various types of tests and their applications, manufacturers can develop comprehensive test strategies that ensure the quality, reliability, and functionality of their products. As PCB technology continues to advance, the importance of robust electrical testing will only continue to grow, making it an essential aspect of the electronics manufacturing industry.
No responses yet