Understanding the Different Types of PCB materials
Before delving into the factors that influence PCB material selection, let’s take a closer look at the various types of materials commonly used in PCB fabrication.
FR-4
FR-4 is the most widely used PCB material, consisting of a composite of woven fiberglass cloth impregnated with an epoxy resin. It offers excellent mechanical strength, good electrical insulation properties, and is suitable for a wide range of applications. FR-4 is an affordable option and is compatible with most standard PCB manufacturing processes.
High-Frequency Laminates
For applications that require high-frequency performance, such as RF and microwave circuits, specialized high-frequency laminates are used. These materials, such as Rogers, Taconic, and Isola, offer low dielectric loss, controlled Dielectric constant, and excellent thermal stability. They are designed to minimize signal loss and maintain signal integrity at high frequencies.
Flexible PCB Materials
Flexible PCBs require materials that can withstand repeated bending and flexing without compromising their electrical and mechanical properties. Common flexible PCB materials include polyimide (PI) and polyethylene terephthalate (PET). These materials are thin, lightweight, and offer good flexibility and durability.
Metal-Core PCBs
Metal-core PCBs (MCPCBs) are used in applications that require efficient heat dissipation, such as high-power LED lighting and power electronics. These PCBs feature a metal substrate, typically aluminum, which acts as a heat sink to effectively transfer heat away from components. The metal core is coated with a thin layer of dielectric material, followed by a copper layer for circuit traces.
Ceramic PCBs
Ceramic PCBs are used in high-temperature and high-reliability applications, such as aerospace, automotive, and military electronics. These PCBs are made from ceramic substrates, such as alumina (Al2O3) or aluminum nitride (AlN), which offer excellent thermal conductivity, high dielectric strength, and low thermal expansion. Ceramic PCBs can withstand extreme temperatures and harsh environments.
Factors to Consider When Choosing PCB Material
Now that we have an understanding of the different types of PCB materials available, let’s explore the key factors to consider when selecting the right material for your project.
Electrical Properties
The electrical properties of the PCB material play a crucial role in determining the performance and functionality of the final product. Consider the following electrical properties when choosing a PCB material:
-
Dielectric Constant (Dk): The dielectric constant represents the material’s ability to store electrical energy. A lower Dk value indicates better signal propagation and reduced signal delay. For high-frequency applications, materials with a low and stable Dk are preferred.
-
Dissipation Factor (Df): The dissipation factor, also known as loss tangent, measures the amount of energy lost as heat when an alternating current passes through the material. A lower Df value means less signal loss and better signal integrity. Low-loss materials are essential for high-frequency and high-speed applications.
-
Dielectric Strength: Dielectric strength refers to the maximum electric field strength that the material can withstand before breakdown occurs. Higher dielectric strength provides better insulation and prevents electrical breakdown between conductive layers.
-
Volume Resistivity: Volume resistivity indicates the material’s ability to resist the flow of electrical current through its volume. Higher volume resistivity is desirable for better insulation and reduced leakage currents.
Thermal Properties
Thermal management is a critical aspect of PCB design, especially for high-power and high-density applications. Consider the following thermal properties when selecting a PCB material:
-
Thermal Conductivity: Thermal conductivity measures the material’s ability to conduct heat. Higher thermal conductivity allows for better heat dissipation, reducing the risk of thermal hotspots and improving overall system reliability.
-
Coefficient of Thermal Expansion (CTE): CTE represents the material’s expansion or contraction in response to temperature changes. A mismatch in CTE between the PCB material and components can lead to mechanical stress and potential failures. It’s important to choose a material with a CTE that closely matches the components used.
-
Glass Transition Temperature (Tg): Tg is the temperature at which the material transitions from a rigid, glassy state to a softer, rubbery state. A higher Tg indicates better thermal stability and resistance to deformation at elevated temperatures.
Mechanical Properties
The mechanical properties of the PCB material influence its durability, reliability, and manufacturability. Consider the following mechanical properties:
-
Tensile Strength: Tensile strength represents the material’s ability to withstand pulling forces without breaking. Higher tensile strength provides better mechanical stability and reduces the risk of cracks and fractures.
-
Flexural Strength: Flexural strength measures the material’s ability to resist bending forces. It is particularly important for applications that involve mechanical stresses, such as vibration or impact.
-
Youngs Modulus: Youngs modulus, or elastic modulus, indicates the material’s stiffness and resistance to elastic deformation. A higher Youngs modulus provides better dimensional stability and reduces warping or bowing of the PCB.
Environmental Factors
The environment in which the PCB will operate can significantly impact the choice of material. Consider the following environmental factors:
-
Operating Temperature Range: Determine the expected operating temperature range for your application. Choose a material that can withstand the anticipated temperature extremes without degradation or failure.
-
Humidity Resistance: If the PCB will be exposed to high humidity environments, select a material with good moisture resistance to prevent moisture absorption and potential reliability issues.
-
Chemical Resistance: Consider the exposure to chemicals, solvents, or other corrosive substances in the operating environment. Choose a material that offers adequate chemical resistance to ensure long-term reliability.
Cost and Availability
Cost and availability are practical considerations when selecting a PCB material. Some specialized materials, such as high-frequency laminates or ceramic substrates, can be more expensive and may have longer lead times compared to standard materials like FR-4. Evaluate the cost implications and availability of the desired material to ensure it aligns with your project budget and timeline.
Manufacturability
The manufacturability of the PCB material is an important factor to consider, especially for high-volume production. Some materials may require specialized processing techniques or have limitations in terms of minimum feature sizes or layer counts. Discuss your material choice with your PCB manufacturer to ensure compatibility with their manufacturing capabilities and to identify any potential challenges or limitations.
PCB Material Selection Guidelines
To help you navigate the material selection process, here are some general guidelines to follow:
-
Start with the electrical requirements: Prioritize the electrical properties that are critical for your application, such as dielectric constant, dissipation factor, and dielectric strength. These properties will heavily influence the signal integrity and performance of your PCB.
-
Consider the operating environment: Evaluate the expected operating temperature range, humidity levels, and exposure to chemicals or other environmental factors. Choose a material that can withstand the anticipated environmental conditions without compromising reliability.
-
Assess thermal management needs: Determine the power dissipation requirements and thermal management strategies for your PCB. If efficient heat dissipation is crucial, consider materials with high thermal conductivity, such as metal-core PCBs or ceramic substrates.
-
Evaluate mechanical requirements: Consider the mechanical stresses and strains that the PCB will be subjected to, such as vibration, impact, or flexing. Select a material with appropriate mechanical properties to ensure durability and reliability.
-
Balance cost and performance: Strike a balance between the desired performance characteristics and the cost of the material. Higher-performance materials may come at a premium, so evaluate the cost-benefit trade-offs and align them with your project budget and requirements.
-
Consult with your PCB manufacturer: Engage with your PCB manufacturer early in the design process to discuss your material selection. They can provide valuable insights into the manufacturability, availability, and cost implications of different materials, helping you make an informed decision.
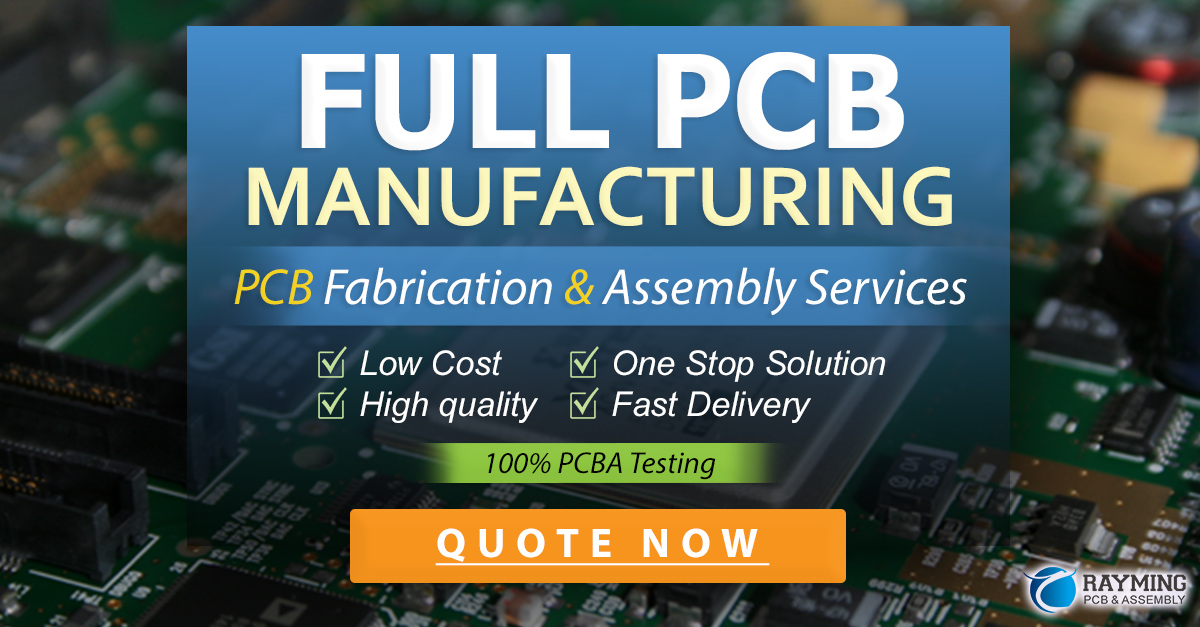
PCB Material Comparison Table
To provide a quick reference for comparing common PCB materials, refer to the table below:
Material | Dielectric Constant (Dk) | Dissipation Factor (Df) | Thermal Conductivity (W/mK) | Coefficient of Thermal Expansion (CTE) (ppm/°C) | Tg (°C) | Typical Applications |
---|---|---|---|---|---|---|
FR-4 | 4.3 – 4.7 | 0.02 | 0.3 – 0.4 | 12 – 16 | 130-140 | General-purpose, digital and analog circuits |
High-Frequency Laminates | 2.2 – 10.2 | 0.0009 – 0.0035 | 0.2 – 0.7 | 12 – 70 | 200-280 | RF, microwave, high-speed digital |
Polyimide (PI) | 3.4 – 3.5 | 0.002 – 0.003 | 0.2 – 0.3 | 20 – 40 | 250-260 | Flexible circuits, high-temperature applications |
Metal-Core PCBs (Aluminum) | 3.5 – 9.0 | 0.002 – 0.03 | 1.5 – 3.0 | 6 – 25 | – | High-power electronics, LED lighting |
Alumina (Al2O3) | 9.0 – 10.0 | 0.0001 – 0.0004 | 20 – 30 | 6.5 – 7.5 | – | High-temperature, high-reliability applications |
Frequently Asked Questions (FAQ)
- What is the most commonly used PCB material?
-
FR-4 is the most widely used PCB material due to its good balance of electrical, mechanical, and thermal properties, as well as its cost-effectiveness and compatibility with standard manufacturing processes.
-
How do I choose the right PCB material for high-frequency applications?
-
For high-frequency applications, select materials with low dielectric constant (Dk) and low dissipation factor (Df) to minimize signal loss and maintain signal integrity. High-frequency laminates, such as Rogers or Taconic materials, are specifically designed for these applications.
-
What are the advantages of using metal-core PCBs?
-
Metal-core PCBs offer excellent thermal conductivity, allowing for efficient heat dissipation from high-power components. They are commonly used in applications such as LED lighting and power electronics to improve thermal management and reliability.
-
Can I use flexible PCB materials for all applications?
-
Flexible PCB materials, such as polyimide (PI) or polyethylene terephthalate (PET), are suitable for applications that require flexibility, lightweight design, or conformity to specific shapes. However, they may not be the best choice for applications that demand high thermal conductivity or rigidity.
-
How does the operating temperature range affect PCB material selection?
- The operating temperature range is a crucial factor in PCB material selection. Choose a material that can withstand the expected temperature extremes without degradation or failure. Materials with higher glass transition temperatures (Tg) offer better thermal stability and are suitable for high-temperature applications.
Conclusion
Selecting the right PCB material is a critical step in ensuring the optimal performance, reliability, and cost-effectiveness of your PCB design. By considering factors such as electrical properties, thermal management, mechanical requirements, environmental conditions, cost, and manufacturability, you can make an informed decision that aligns with your specific application needs.
Remember to prioritize the key characteristics that are essential for your design, and engage with your PCB manufacturer early in the process to discuss material options and manufacturability. With a well-chosen PCB material, you can achieve the desired functionality, durability, and overall success of your electronic product.
No responses yet