Introduction to PCB materials
Printed Circuit Boards (PCBs) are the backbone of modern electronics. They provide a platform for mounting and connecting electronic components, enabling the creation of complex circuits. The choice of PCB material is crucial to the performance, reliability, and cost of the final product. In this article, we will explore the various factors to consider when selecting a PCB material and provide guidance on how to make the best choice for your specific application.
Factors to Consider When Choosing PCB Material
Electrical Properties
Dielectric Constant (Dk)
The dielectric constant, also known as relative permittivity, is a measure of a material’s ability to store electrical energy. It is the ratio of the permittivity of the material to the permittivity of free space. A higher Dk value indicates that the material can store more electrical energy, which can be beneficial for certain applications such as capacitors. However, a high Dk value can also lead to signal integrity issues, particularly at high frequencies.
Dissipation Factor (Df)
The dissipation factor, also known as loss tangent, is a measure of a material’s ability to dissipate electrical energy as heat. It is the ratio of the imaginary part of the permittivity to the real part. A lower Df value indicates that the material has lower energy loss, which is desirable for high-frequency applications where signal integrity is critical.
Electrical Strength
Electrical strength, also known as dielectric strength, is the maximum electric field that a material can withstand before breakdown occurs. It is measured in volts per mil (V/mil) or kilovolts per millimeter (kV/mm). A higher electrical strength is desirable for applications with high voltage requirements.
Thermal Properties
Glass Transition Temperature (Tg)
The glass transition temperature is the temperature at which a material transitions from a rigid, glassy state to a soft, rubbery state. It is an important consideration for PCB materials, as it determines the maximum operating temperature of the board. A higher Tg value indicates that the material can maintain its mechanical and electrical properties at higher temperatures.
Coefficient of Thermal Expansion (CTE)
The coefficient of thermal expansion is a measure of how much a material expands or contracts with changes in temperature. It is typically expressed in parts per million per degree Celsius (ppm/°C). A lower CTE value is desirable, as it minimizes the stress on the PCB and its components during temperature cycling.
Thermal Conductivity
Thermal conductivity is a measure of a material’s ability to conduct heat. It is expressed in watts per meter-kelvin (W/mK). A higher thermal conductivity is desirable for applications that generate significant heat, as it helps to dissipate the heat more efficiently, preventing damage to the PCB and its components.
Mechanical Properties
Flexural Strength
Flexural strength is a measure of a material’s ability to resist bending. It is expressed in megapascals (MPa) or pounds per square inch (psi). A higher flexural strength is desirable for applications that require a rigid PCB, such as those subjected to mechanical stress or vibration.
Tensile Strength
Tensile strength is a measure of a material’s ability to resist pulling forces. It is expressed in megapascals (MPa) or pounds per square inch (psi). A higher tensile strength is desirable for applications that require a strong and durable PCB.
Dimensional Stability
Dimensional stability refers to a material’s ability to maintain its original dimensions when subjected to changes in temperature, humidity, or mechanical stress. It is an important consideration for applications that require precise component placement and alignment.
Manufacturing Considerations
Ease of Fabrication
The ease of fabrication refers to how easily a PCB material can be processed using standard PCB manufacturing techniques, such as drilling, routing, and plating. Some materials may require specialized equipment or processing conditions, which can increase manufacturing costs and lead times.
Cost
The cost of PCB materials can vary widely depending on factors such as the type of material, the volume of production, and the required specifications. It is essential to consider the cost implications of material choice in the context of the overall project budget and production scale.
Availability
The availability of PCB materials can impact the lead time and cost of production. Some specialized materials may have limited suppliers or longer lead times, which can affect project timelines and budgets.
Common PCB Materials
FR-4
FR-4 is the most widely used PCB material. It is a composite material made of woven fiberglass fabric impregnated with an epoxy resin. FR-4 offers a good balance of electrical, thermal, and mechanical properties at a relatively low cost. It is suitable for a wide range of applications, from low-frequency digital circuits to moderate-frequency analog circuits.
Property | Value |
---|---|
Dielectric Constant (Dk) | 4.3 – 4.7 |
Dissipation Factor (Df) | 0.02 |
Electrical Strength (kV/mm) | 20 – 30 |
Glass Transition Temperature (Tg) | 130°C – 140°C |
Coefficient of Thermal Expansion (CTE) (ppm/°C) | 12 – 16 (x,y), 50 – 70 (z) |
Thermal Conductivity (W/mK) | 0.3 – 0.4 |
Flexural Strength (MPa) | 400 – 500 |
Tensile Strength (MPa) | 300 – 400 |
High Tg FR-4
High Tg FR-4 is a variant of standard FR-4 with a higher glass transition temperature. It is designed for applications that require higher thermal stability, such as automotive and aerospace electronics. High Tg FR-4 offers improved mechanical and electrical properties at elevated temperatures compared to standard FR-4.
Property | Value |
---|---|
Dielectric Constant (Dk) | 4.3 – 4.7 |
Dissipation Factor (Df) | 0.02 |
Electrical Strength (kV/mm) | 20 – 30 |
Glass Transition Temperature (Tg) | 170°C – 180°C |
Coefficient of Thermal Expansion (CTE) (ppm/°C) | 12 – 16 (x,y), 50 – 70 (z) |
Thermal Conductivity (W/mK) | 0.3 – 0.4 |
Flexural Strength (MPa) | 400 – 500 |
Tensile Strength (MPa) | 300 – 400 |
Rogers laminate
Rogers laminates are a family of high-performance PCB materials designed for demanding RF and microwave applications. They offer excellent electrical properties, including low dielectric constant and dissipation factor, as well as good thermal and mechanical stability. Some popular Rogers laminates include:
- RO4000 series: A hydrocarbon ceramic laminate with low Dk and Df, suitable for high-frequency applications up to 40 GHz.
- RO3000 series: A ceramic-filled PTFE laminate with low Dk and Df, suitable for applications up to 77 GHz.
- RT/duroid series: A PTFE-based laminate with low Dk and Df, suitable for applications up to 100 GHz.
Property | RO4350B | RO3003 | RT/duroid 5880 |
---|---|---|---|
Dielectric Constant (Dk) | 3.48 | 3.00 | 2.20 |
Dissipation Factor (Df) | 0.0037 | 0.0010 | 0.0009 |
Electrical Strength (kV/mm) | 39 | 40 | 48 |
Glass Transition Temperature (Tg) | >280°C | >280°C | >300°C |
Coefficient of Thermal Expansion (CTE) (ppm/°C) | 11-14 (x,y), 46 (z) | 17 (x,y), 24 (z) | 31 (x,y), 237 (z) |
Thermal Conductivity (W/mK) | 0.62 | 0.50 | 0.20 |
Polyimide
Polyimide is a high-temperature, high-performance PCB material known for its excellent thermal stability, mechanical strength, and chemical resistance. It is often used in aerospace, military, and medical applications that require operation in harsh environments. Polyimide has a higher cost compared to FR-4 but offers superior performance in demanding conditions.
Property | Value |
---|---|
Dielectric Constant (Dk) | 3.4 – 3.5 |
Dissipation Factor (Df) | 0.002 – 0.008 |
Electrical Strength (kV/mm) | 100 – 150 |
Glass Transition Temperature (Tg) | >260°C |
Coefficient of Thermal Expansion (CTE) (ppm/°C) | 12 – 16 (x,y), 40 – 60 (z) |
Thermal Conductivity (W/mK) | 0.2 – 0.3 |
Flexural Strength (MPa) | 400 – 600 |
Tensile Strength (MPa) | 300 – 500 |
Isola laminate
Isola laminates are a range of high-performance PCB materials designed for various applications, including high-speed digital, RF, and automotive electronics. Some popular Isola laminates include:
- FR408HR: A high-performance, high-Tg FR-4 laminate suitable for high-speed digital and RF applications.
- IS410: A low-loss, high-speed laminate designed for high-frequency applications up to 100 GHz.
- I-Speed: A low-Dk, low-Df laminate designed for high-speed digital applications.
Property | FR408HR | IS410 | I-Speed |
---|---|---|---|
Dielectric Constant (Dk) | 3.65 | 3.45 | 3.00 |
Dissipation Factor (Df) | 0.010 | 0.004 | 0.004 |
Electrical Strength (kV/mm) | 45 | 60 | 60 |
Glass Transition Temperature (Tg) | 180°C | 200°C | 200°C |
Coefficient of Thermal Expansion (CTE) (ppm/°C) | 12-16 (x,y), 50-60 (z) | 10-14 (x,y), 28-40 (z) | 10-14 (x,y), 28-40 (z) |
Thermal Conductivity (W/mK) | 0.4 – 0.5 | 0.5 – 0.6 | 0.5 – 0.6 |
Flexural Strength (MPa) | 500 – 600 | 600 – 700 | 600 – 700 |
Tensile Strength (MPa) | 400 – 500 | 500 – 600 | 500 – 600 |
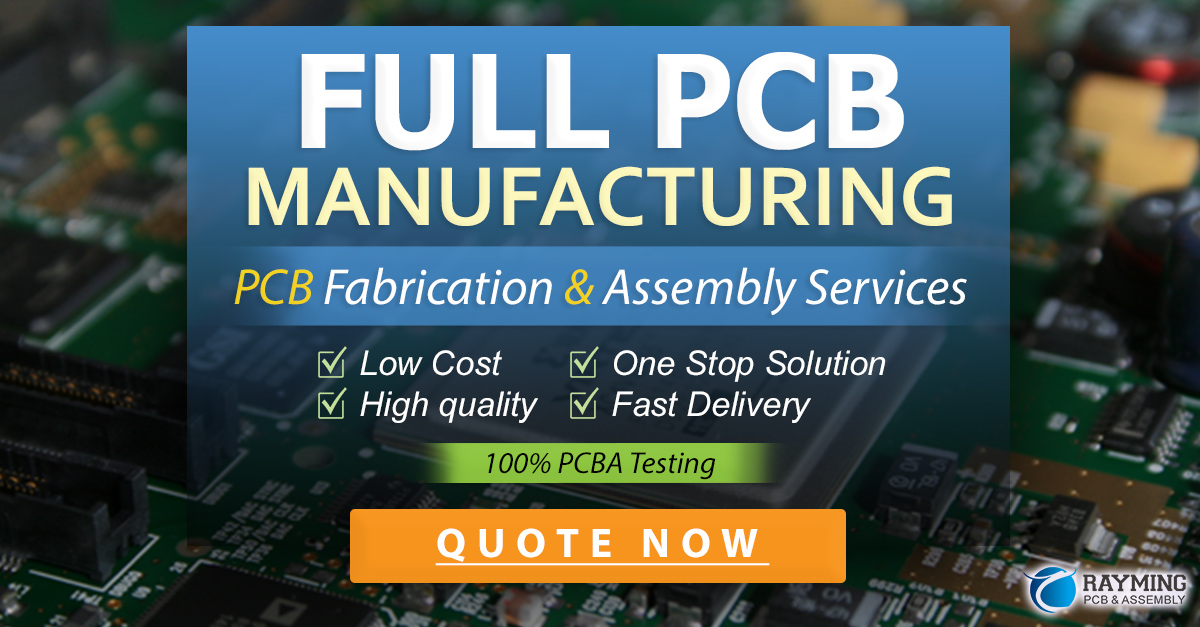
Selecting the Right PCB Material
When selecting a PCB material, consider the following steps:
-
Determine the application requirements: Identify the key performance requirements for your application, such as operating frequency, temperature range, mechanical stress, and environmental conditions.
-
Prioritize material properties: Based on the application requirements, prioritize the material properties that are most critical for your design. For example, high-frequency applications may prioritize low Dk and Df, while high-temperature applications may prioritize high Tg and thermal conductivity.
-
Evaluate material options: Compare the properties of various PCB materials and select the ones that best meet your prioritized requirements. Consider factors such as cost, availability, and manufacturing constraints when making your decision.
-
Consult with PCB manufacturers: Engage with PCB manufacturers to discuss your material choices and gather their input on manufacturability, cost, and lead time. They can provide valuable insights based on their experience and capabilities.
-
Prototype and test: Before finalizing your material choice, consider prototyping and testing your design with the selected material to validate its performance and manufacturability. This can help identify any potential issues early in the development process.
Frequently Asked Questions (FAQ)
- What is the most common PCB material?
-
FR-4 is the most widely used PCB material due to its good balance of properties and relatively low cost.
-
What PCB materials are suitable for high-frequency applications?
-
Rogers laminates, such as RO4000 and RO3000 series, and Isola laminates, such as IS410, are designed for high-frequency applications due to their low dielectric constant and dissipation factor.
-
What PCB materials are suitable for high-temperature applications?
-
Polyimide and high Tg FR-4 are suitable for high-temperature applications due to their higher glass transition temperature and better thermal stability compared to standard FR-4.
-
How does the dielectric constant affect PCB performance?
-
A lower dielectric constant reduces the signal propagation delay and minimizes signal integrity issues, especially at high frequencies. However, a higher dielectric constant can be beneficial for certain applications, such as capacitors, where higher energy storage is desired.
-
What is the difference between Tg and Td?
- Tg (glass transition temperature) is the temperature at which a material transitions from a rigid, glassy state to a soft, rubbery state. Td (decomposition temperature) is the temperature at which a material begins to break down and lose its properties. Tg is more relevant for determining the maximum operating temperature of a PCB, while Td is important for understanding the material’s thermal limits during manufacturing processes, such as soldering.
Conclusion
Choosing the right PCB material is a critical decision that can significantly impact the performance, reliability, and cost of your electronic product. By understanding the key material properties, such as electrical, thermal, and mechanical characteristics, and considering the specific requirements of your application, you can make an informed choice that balances performance and cost.
Remember to prioritize the most critical material properties for your design, evaluate multiple material options, and consult with PCB manufacturers to ensure the best possible outcome. With careful material selection and validation through prototyping and testing, you can create high-quality, reliable PCBs that meet the demands of your application.
No responses yet