What are PCB traces?
PCB traces are the conductive paths that electrically connect different components on a printed circuit board. These traces are typically made of copper and are etched or printed onto the insulating substrate of the PCB. They carry signals and power between components, enabling the device to function as intended.
Types of PCB Traces
There are several types of PCB traces, each with its own characteristics and applications:
-
Signal Traces: These traces carry low-current signals between components, such as data or control signals. They are usually narrow and have specific design requirements to maintain signal integrity.
-
Power Traces: Power traces are wider and thicker than signal traces, as they need to carry higher currents to supply power to components. They often have specific design rules to minimize voltage drop and ensure adequate current-carrying capacity.
-
Ground Traces: Ground traces provide a common reference point for the circuit and help to minimize noise and interference. They are typically connected to a ground plane, which is a large area of copper on the PCB.
-
Differential Pairs: Differential pairs are two traces that carry a differential signal, where the signal is the difference between the voltages on the two traces. They are commonly used in high-speed digital interfaces to minimize noise and crosstalk.
PCB Trace Manufacturing Process
The manufacturing process for PCB traces involves several steps, each of which contributes to the final quality and reliability of the traces.
Step 1: PCB Design and Layout
The first step in creating PCB traces is designing the circuit and laying out the components on the board. This is typically done using specialized PCB design software, such as Altium Designer or KiCad. The designer must consider factors such as component placement, signal integrity, power distribution, and manufacturing constraints when creating the layout.
Step 2: Substrate Preparation
Once the design is finalized, the next step is to prepare the substrate for the traces. The most common substrate material for PCBs is FR-4, a glass-reinforced epoxy laminate. The substrate is cleaned and inspected to ensure it is free of contaminants and defects.
Step 3: Copper Cladding
After substrate preparation, a thin layer of copper is applied to the surface of the substrate. This is typically done using a process called electroless copper plating, where the substrate is immersed in a chemical bath that deposits a uniform layer of copper onto the surface.
Step 4: Photoresist Application
Next, a photosensitive material called photoresist is applied to the copper-clad substrate. This is typically done using a process called screen printing or photolithography. The photoresist is exposed to light through a mask that contains the desired trace pattern, causing the exposed areas to harden.
Step 5: Developing and Etching
After exposure, the photoresist is developed, removing the unexposed areas and leaving behind the hardened trace pattern. The board is then placed in an etching solution, which removes the exposed copper, leaving only the traces protected by the hardened photoresist.
Step 6: Photoresist Removal and Cleaning
Once the etching process is complete, the remaining photoresist is removed using a chemical stripper. The board is then cleaned and inspected to ensure the traces are properly formed and free of defects.
Step 7: Finishing and Protection
The final step in the PCB trace manufacturing process is to apply a finishing layer to protect the traces from oxidation and corrosion. This can be done using various methods, such as solder mask application, plating, or conformal coating. These finishing layers also serve to insulate the traces from each other and prevent short circuits.
PCB Trace Design Considerations
Designing PCB traces requires careful consideration of several factors to ensure optimal performance and reliability. Some of the key considerations include:
Trace Width and Thickness
The width and thickness of a trace determine its electrical characteristics, such as resistance, inductance, and current-carrying capacity. Trace width is typically determined by the current requirements of the circuit, with wider traces used for higher currents. Trace thickness is usually dictated by the copper weight of the PCB, which is expressed in ounces per square foot (oz/ft²).
Common PCB Copper Weights
Copper Weight (oz/ft²) | Typical Thickness (mm) |
---|---|
0.5 | 0.017 |
1 | 0.034 |
2 | 0.068 |
3 | 0.102 |
Trace Spacing and Clearance
The spacing between traces and the clearance between traces and other features, such as vias or component pads, are critical for maintaining signal integrity and preventing short circuits. The minimum spacing and clearance requirements are determined by the manufacturing capabilities of the PCB fabricator and the electrical requirements of the circuit.
Signal Integrity
Signal integrity refers to the ability of a trace to carry a signal without distortion or interference. This is particularly important for high-speed digital signals, where factors such as impedance matching, crosstalk, and reflections can degrade signal quality. Designers must consider factors such as trace geometry, dielectric properties, and termination strategies to maintain signal integrity.
Thermal Management
PCB traces can generate heat due to electrical resistance, which can lead to performance issues and reliability problems. Designers must consider the thermal properties of the traces and the PCB substrate, as well as the power dissipation of the components, to ensure adequate thermal management. Techniques such as using wider traces, adding thermal vias, or incorporating heatsinks can help to mitigate thermal issues.
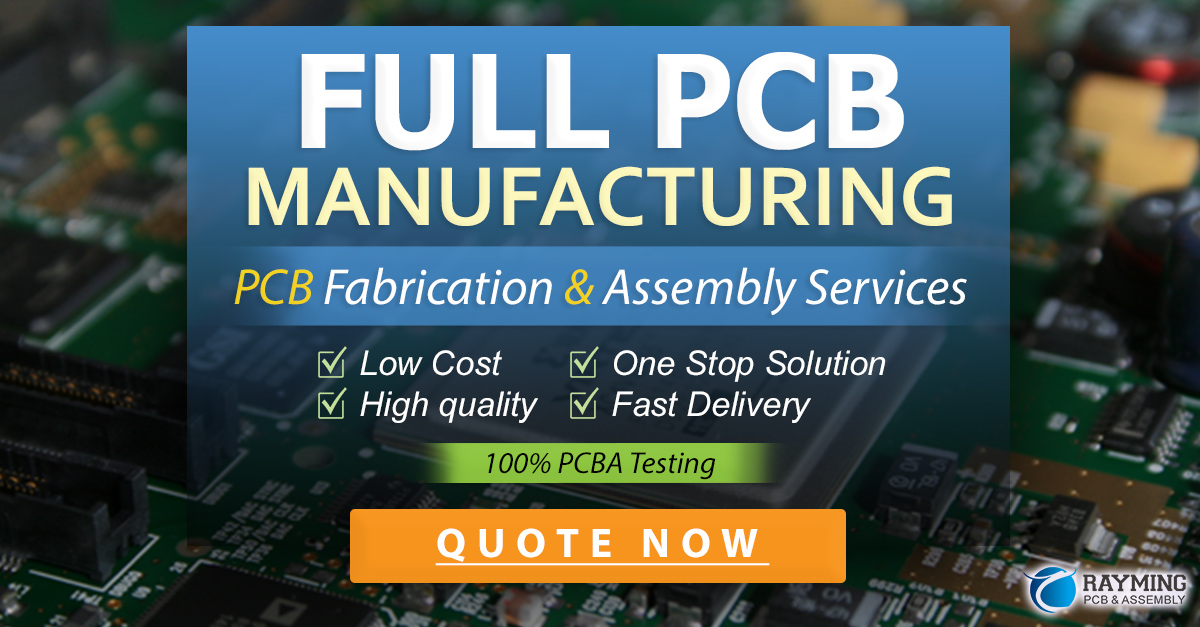
Frequently Asked Questions (FAQ)
-
What is the most common material used for PCB traces?
Copper is the most common material used for PCB traces due to its excellent electrical conductivity, thermal conductivity, and ease of manufacturing. -
How do I determine the appropriate trace width for my design?
The appropriate trace width depends on several factors, including the current requirements of the circuit, the copper weight of the PCB, and the maximum allowable temperature rise. There are various online calculators and design guides available to help determine the optimal trace width for a given application. -
What is the difference between a solder mask and a conformal coating?
A solder mask is a thin layer of polymer applied to the surface of a PCB to protect the traces from oxidation and prevent solder bridges during assembly. A conformal coating is a protective layer applied to the entire PCB assembly to protect it from moisture, dust, and other environmental factors. -
Can PCB traces be repaired if damaged?
In some cases, damaged PCB traces can be repaired using techniques such as soldering, conductive epoxy, or wire jumpers. However, the feasibility of repair depends on the extent of the damage and the accessibility of the affected traces. In many cases, it may be more cost-effective to replace the entire PCB. -
What is the difference between a microstrip and a stripline trace?
A microstrip trace is a trace that runs on the surface of a PCB, with a ground plane on one side. A stripline trace is a trace that is sandwiched between two ground planes inside the PCB. Microstrip traces are easier to manufacture but more susceptible to interference, while stripline traces offer better signal integrity but are more complex to fabricate.
Conclusion
PCB traces are the lifeblood of modern electronics, enabling the interconnection of components and the transmission of signals and power. The manufacturing process for PCB traces involves a combination of chemical, mechanical, and photolithographic techniques, each of which contributes to the final quality and reliability of the traces.
Designing PCB traces requires careful consideration of factors such as trace geometry, spacing, signal integrity, and thermal management. By understanding these considerations and working closely with experienced PCB fabricators, designers can create PCBs that meet the demanding requirements of today’s electronic devices.
As technology continues to advance, the importance of PCB traces will only continue to grow. By staying up-to-date with the latest manufacturing techniques and design best practices, engineers and designers can ensure that their PCBs are ready to meet the challenges of the future.
No responses yet