Introduction to Flex-Rigid PCB
Flex-Rigid PCB, also known as Rigid-Flex PCB, is a unique type of printed Circuit board that combines the benefits of both flexible and rigid PCBs. This innovative technology has revolutionized the electronics industry by providing a solution for applications that require both flexibility and rigidity in a single board. Flex-Rigid PCBs are widely used in various industries, including aerospace, medical, automotive, and consumer electronics.
RAYPCB, a leading manufacturer of high-quality PCBs, has been at the forefront of Flex-Rigid PCB technology. With state-of-the-art facilities and a team of experienced engineers, RAYPCB has the capability to design and manufacture complex Flex-Rigid PCBs that meet the most demanding requirements of their clients.
Advantages of Flex-Rigid PCB
Flex-Rigid PCBs offer several advantages over traditional rigid PCBs, including:
- Space savings: Flex-Rigid PCBs can be folded and shaped to fit into tight spaces, reducing the overall size of the device.
- Weight reduction: By eliminating the need for connectors and cables, Flex-Rigid PCBs can significantly reduce the weight of the device.
- Improved reliability: Flex-Rigid PCBs have fewer interconnects, which reduces the risk of signal loss and improves overall reliability.
- Enhanced design flexibility: Flex-Rigid PCBs allow for more creative and efficient designs, as they can be folded and shaped to fit the device’s form factor.
RAYPCB’s Flex-Rigid PCB Capabilities
RAYPCB has invested heavily in the latest technology and equipment to ensure they can provide their clients with the highest quality Flex-Rigid PCBs. Some of their key capabilities include:
-
Multi-layer Flex-Rigid PCBs: RAYPCB can manufacture Flex-Rigid PCBs with up to 20 layers, allowing for more complex designs and higher component density.
-
High-Density Interconnect (HDI): RAYPCB’s HDI technology enables them to produce Flex-Rigid PCBs with fine pitch traces and micro vias, allowing for even greater design flexibility and miniaturization.
-
Impedance Control: RAYPCB can precisely control the impedance of the Flex-Rigid PCB to ensure optimal signal integrity and performance.
-
Rigorous Testing: Every Flex-Rigid PCB manufactured by RAYPCB undergoes rigorous testing to ensure it meets the highest quality standards. This includes electrical testing, mechanical testing, and environmental testing.
Flex-Rigid PCB Capability | Description |
---|---|
Multi-layer | Up to 20 layers |
HDI | Fine pitch traces and micro vias |
Impedance Control | Precise control for optimal signal integrity |
Rigorous Testing | Electrical, mechanical, and environmental testing |
Flex-Rigid PCB Design Considerations
Designing a Flex-Rigid PCB requires careful consideration of several factors to ensure optimal performance and reliability. Some of the key design considerations include:
1. Bend Radius
The bend radius is a critical factor in Flex-Rigid PCB design, as it determines the minimum distance the board can be bent without causing damage. RAYPCB’s engineers work closely with clients to determine the appropriate bend radius for their specific application.
2. Material Selection
Choosing the right materials is crucial for the performance and reliability of Flex-Rigid PCBs. RAYPCB offers a wide range of materials, including polyimide, polyester, and Teflon, to meet the specific requirements of each application.
3. Stiffener Placement
Stiffeners are used to provide additional support and rigidity to the flexible portions of the Flex-Rigid PCB. RAYPCB’s engineers use advanced software to optimize the placement of stiffeners to ensure the best possible performance.
4. Coverlay Design
The coverlay is a protective layer that covers the flexible portions of the Flex-Rigid PCB. RAYPCB’s engineers carefully design the coverlay to ensure it provides adequate protection without compromising flexibility.
RAYPCB’s Flex-Rigid PCB Manufacturing Process
RAYPCB’s state-of-the-art manufacturing process ensures the highest quality Flex-Rigid PCBs. The process involves several key steps, including:
-
Material Preparation: The flexible and rigid materials are cut to size and cleaned to ensure optimal bonding.
-
Lamination: The flexible and rigid layers are laminated together using advanced equipment and techniques to ensure a strong and reliable bond.
-
Drilling: Holes are drilled through the Flex-Rigid PCB to accommodate components and vias.
-
Plating: The drilled holes are plated with copper to create electrical connections between layers.
-
Etching: Unwanted copper is removed from the surface of the Flex-Rigid PCB using advanced etching techniques.
-
Solder Mask Application: A solder mask is applied to the Flex-Rigid PCB to protect the copper traces and prevent short circuits.
-
Surface Finish: A surface finish, such as ENIG or HASL, is applied to the Flex-Rigid PCB to improve solderability and protect against oxidation.
-
Cutting and Forming: The Flex-Rigid PCB is cut to its final shape and size, and any necessary forming is performed.
-
Testing and Inspection: Every Flex-Rigid PCB undergoes rigorous testing and inspection to ensure it meets the highest quality standards.
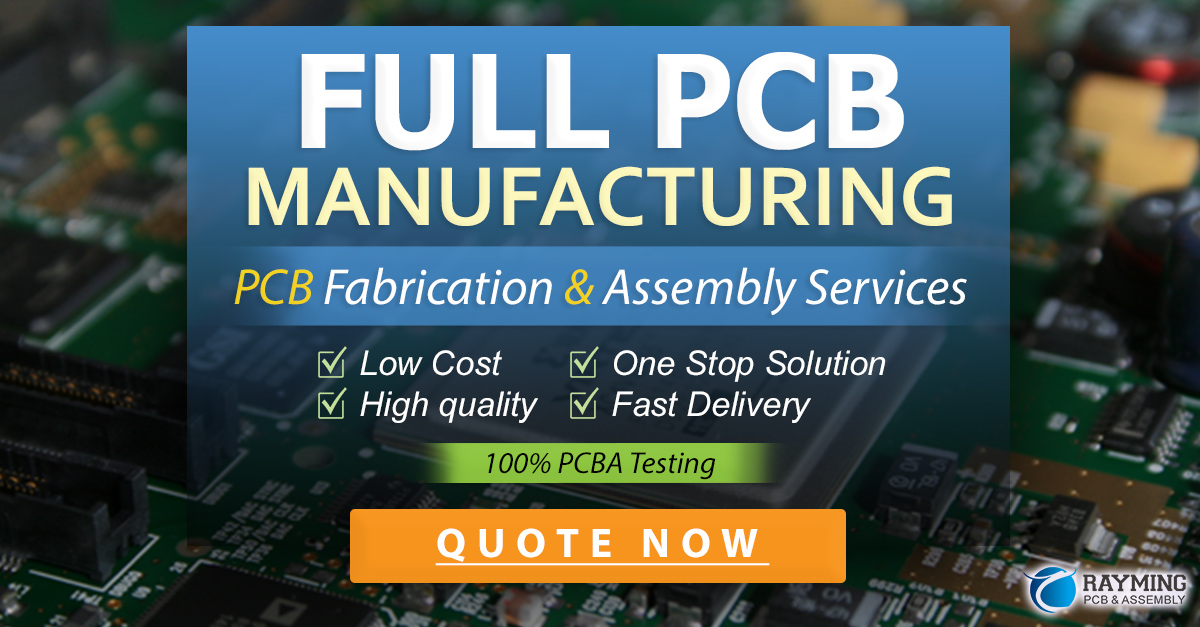
Applications of Flex-Rigid PCB
Flex-Rigid PCBs are used in a wide range of applications across various industries. Some of the most common applications include:
1. Aerospace
Flex-Rigid PCBs are widely used in aerospace applications, such as satellites, aircraft, and missiles. They offer significant weight and space savings, as well as improved reliability in harsh environments.
2. Medical Devices
Flex-Rigid PCBs are ideal for medical devices, such as wearable monitors and implantable devices. They allow for smaller, more comfortable devices that can conform to the human body.
3. Automotive
Flex-Rigid PCBs are increasingly used in automotive applications, such as dashboard displays, control modules, and sensors. They offer improved reliability and design flexibility in the harsh automotive environment.
4. Consumer Electronics
Flex-Rigid PCBs are used in a wide range of consumer electronics, such as smartphones, tablets, and smartwatches. They enable smaller, more lightweight devices with improved functionality.
Choosing RAYPCB for Your Flex-Rigid PCB Needs
RAYPCB is the ideal choice for your Flex-Rigid PCB needs. With their state-of-the-art facilities, experienced engineers, and commitment to quality, RAYPCB can provide you with the highest quality Flex-Rigid PCBs for your specific application.
Some of the key reasons to choose RAYPCB include:
-
Experience: RAYPCB has years of experience in designing and manufacturing Flex-Rigid PCBs for a wide range of industries and applications.
-
Quality: RAYPCB is committed to providing the highest quality Flex-Rigid PCBs. Every board undergoes rigorous testing and inspection to ensure it meets the highest standards.
-
Advanced Technology: RAYPCB invests in the latest technology and equipment to ensure they can provide their clients with the most advanced Flex-Rigid PCB solutions.
-
Customer Support: RAYPCB offers exceptional customer support, with a team of experienced engineers available to answer any questions and provide guidance throughout the design and manufacturing process.
Future of Flex-Rigid PCB Technology
The future of Flex-Rigid PCB technology is bright, with continued advancements in materials, manufacturing processes, and design tools. Some of the key trends and developments to watch include:
-
Increased Adoption: As more industries recognize the benefits of Flex-Rigid PCBs, adoption is expected to continue to grow rapidly.
-
Advanced Materials: New materials, such as high-temperature polyimides and low-loss dielectrics, are being developed to improve the performance and reliability of Flex-Rigid PCBs.
-
3D Printing: 3D printing technology is being explored as a potential method for manufacturing Flex-Rigid PCBs, which could enable even greater design flexibility and customization.
-
Artificial Intelligence: AI-powered design tools are being developed to optimize Flex-Rigid PCB layouts and improve manufacturing efficiency.
Frequently Asked Questions (FAQ)
-
What is a Flex-Rigid PCB?
A Flex-Rigid PCB is a type of printed circuit board that combines flexible and rigid materials to create a board that can be folded, bent, or shaped to fit into tight spaces or conform to unique form factors. -
What are the advantages of using a Flex-Rigid PCB?
Flex-Rigid PCBs offer several advantages, including space and weight savings, improved reliability, and enhanced design flexibility. They also reduce the need for connectors and cables, which can improve signal integrity and reduce manufacturing costs. -
What industries commonly use Flex-Rigid PCBs?
Flex-Rigid PCBs are commonly used in aerospace, medical devices, automotive, and consumer electronics industries, among others. -
How many layers can a Flex-Rigid PCB have?
RAYPCB can manufacture Flex-Rigid PCBs with up to 20 layers, allowing for complex designs and high component density. -
Why should I choose RAYPCB for my Flex-Rigid PCB needs?
RAYPCB offers state-of-the-art facilities, experienced engineers, advanced technology, and exceptional customer support, making them the ideal choice for your Flex-Rigid PCB needs.
Conclusion
Flex-Rigid PCBs are a game-changing technology that offers numerous benefits over traditional rigid PCBs. With their ability to save space, reduce weight, improve reliability, and enhance design flexibility, Flex-Rigid PCBs are becoming increasingly popular across a wide range of industries.
RAYPCB is at the forefront of Flex-Rigid PCB technology, with state-of-the-art facilities, experienced engineers, and a commitment to quality. Whether you’re working on an aerospace project, a medical device, an automotive component, or a consumer electronics product, RAYPCB has the capability and expertise to provide you with the highest quality Flex-Rigid PCBs for your specific application.
As the demand for smaller, lighter, and more reliable electronics continues to grow, the future of Flex-Rigid PCB technology looks bright. With continued advancements in materials, manufacturing processes, and design tools, Flex-Rigid PCBs are poised to play an increasingly important role in shaping the future of the electronics industry.
If you’re looking for a trusted partner for your Flex-Rigid PCB needs, look no further than RAYPCB. With their proven track record of success and commitment to customer satisfaction, RAYPCB is the ideal choice for your next project. Contact them today to learn more about how they can help you bring your vision to life with Flex-Rigid PCB technology.
No responses yet