Introduction to High Current PCB Design
High current PCB design is a specialized area of printed circuit board design that focuses on handling high levels of electrical current. These PCBs are crucial in various applications where high power delivery is required, such as power electronics, automotive systems, and industrial equipment. Designing high current PCBs involves careful consideration of several factors to ensure reliable and efficient operation while minimizing potential issues like excessive heat generation and electromagnetic interference (EMI).
Key Challenges in High Current PCB Design
- Thermal management
- Current carrying capacity
- Voltage drop
- EMI and signal integrity
Thermal Management in High Current PCBs
One of the primary challenges in high current PCB design is managing the heat generated by the high levels of current flowing through the traces. Excessive heat can lead to component failure, reduced reliability, and even PCB damage. To mitigate these risks, several thermal management techniques are employed:
Copper Trace Width and Thickness
Increasing the width and thickness of copper traces helps to reduce resistance and improve current carrying capacity. Wider traces also dissipate heat more effectively, reducing the risk of thermal issues. The IPC-2152 standard provides guidelines for determining the appropriate trace width and thickness based on the required current carrying capacity and temperature rise.
Current (A) | Trace Width (mm) | Trace Thickness (oz) |
---|---|---|
5 | 1.5 | 1 |
10 | 3.0 | 2 |
20 | 6.0 | 3 |
Thermal Vias and Heat Sinks
Thermal vias are small, plated through-holes that transfer heat from the top layer of the PCB to the bottom layer or internal layers. By strategically placing thermal vias near high-power components, designers can effectively dissipate heat and prevent localized hot spots. Heat sinks can also be attached to the PCB to further enhance heat dissipation, especially for components with high power dissipation.
Current Carrying Capacity and Voltage Drop
Calculating Current Carrying Capacity
To ensure that the PCB traces can handle the required current without excessive heating or voltage drop, designers must calculate the current carrying capacity of the traces. The current carrying capacity depends on several factors, including:
- Trace width and thickness
- Ambient temperature
- Temperature rise
- Copper weight
The IPC-2152 standard provides equations and tables to help designers determine the appropriate trace dimensions for a given current requirement.
Minimizing Voltage Drop
Voltage drop occurs when current flows through a conductor with finite resistance, leading to a decrease in voltage along the length of the conductor. In high current PCBs, voltage drop can be a significant issue, as it can affect the performance of connected components. To minimize voltage drop, designers can:
- Use wider and thicker traces to reduce resistance
- Minimize trace length
- Use higher copper weights
- Utilize power and ground planes
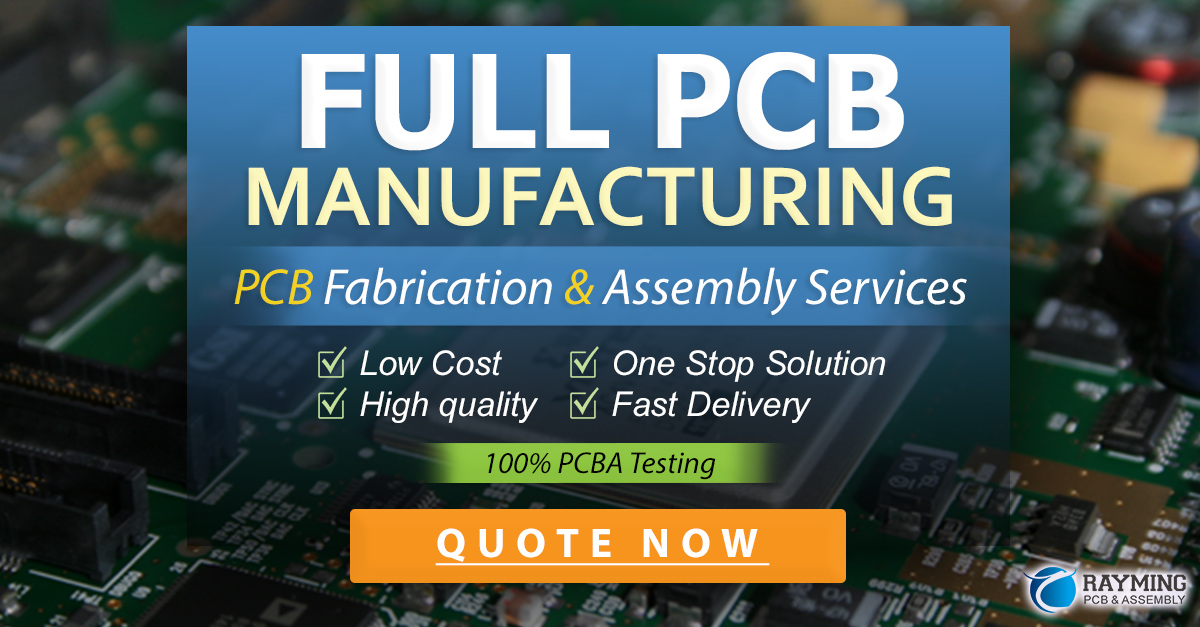
EMI and Signal Integrity
High current PCBs can generate significant electromagnetic interference (EMI) due to the large currents flowing through the traces. This EMI can interfere with nearby electronic devices and cause signal integrity issues within the PCB itself. To mitigate EMI and maintain signal integrity, designers can employ several techniques:
Proper Grounding and Shielding
Implementing a solid grounding strategy is crucial for minimizing EMI and ensuring signal integrity. This includes using ground planes, properly connecting components to ground, and using shielding techniques like grounded copper pours or conductive enclosures.
Decoupling Capacitors and Ferrite Beads
Decoupling capacitors help to reduce high-frequency noise and stabilize the power supply by providing a local source of charge for fast-switching components. Placing decoupling capacitors close to high-current components can help to minimize EMI and improve signal integrity. Ferrite beads can also be used to suppress high-frequency noise and prevent EMI from propagating along the traces.
PCB Layout Considerations
Component Placement
Proper component placement is essential for optimizing current flow, minimizing trace length, and reducing the risk of thermal issues. High-power components should be placed close to the power input to minimize trace length and voltage drop. Components that dissipate significant amounts of heat should be spaced apart to prevent localized hot spots and allow for effective heat dissipation.
Trace Routing
When routing traces for high current PCBs, designers should follow these guidelines:
- Use wide, short traces to minimize resistance and voltage drop
- Avoid sharp corners and use 45-degree angles instead
- Provide adequate spacing between traces to prevent crosstalk and EMI
- Use power and ground planes to distribute current evenly
Applications of High Current PCBs
High current PCBs are used in a wide range of applications, including:
- Power electronics
- Switching power supplies
- Motor drives
- Inverters
- Automotive systems
- Electric vehicle charging systems
- Battery management systems
- High-power audio amplifiers
- Industrial equipment
- Welding machines
- CNC machines
- Robotics
Frequently Asked Questions (FAQ)
1. What is the difference between high current and regular PCB design?
High current PCB design focuses on handling high levels of electrical current, typically above 5A, while regular PCB design deals with lower current levels. High current PCBs require special consideration for thermal management, current carrying capacity, voltage drop, and EMI, which may not be as critical in regular PCB design.
2. How can I determine the appropriate trace width and thickness for a given current requirement?
The IPC-2152 standard provides guidelines and equations to help designers determine the appropriate trace width and thickness based on the required current carrying capacity, ambient temperature, temperature rise, and copper weight.
3. What is the purpose of thermal vias in high current PCBs?
Thermal vias are small, plated through-holes that transfer heat from the top layer of the PCB to the bottom layer or internal layers. They help to dissipate heat more effectively and prevent localized hot spots, which can cause component failure or PCB damage.
4. How can I minimize voltage drop in high current PCBs?
To minimize voltage drop, designers can use wider and thicker traces to reduce resistance, minimize trace length, use higher copper weights, and utilize power and ground planes to distribute current evenly.
5. What are some techniques for mitigating EMI in high current PCBs?
To mitigate EMI in high current PCBs, designers can implement a solid grounding strategy, use shielding techniques like grounded copper pours or conductive enclosures, place decoupling capacitors close to high-current components, and use ferrite beads to suppress high-frequency noise.
Conclusion
High current PCB design is a critical aspect of many electronic systems, enabling the reliable and efficient delivery of high power to various components. By carefully considering factors such as thermal management, current carrying capacity, voltage drop, and EMI, designers can create robust and high-performing PCBs for a wide range of applications, from power electronics to automotive systems and industrial equipment.
As technology advances and the demand for high-power electronics continues to grow, the importance of skilled high current PCB design will only increase. By staying up-to-date with the latest design techniques, standards, and best practices, PCB designers can meet the evolving challenges of high current applications and contribute to the development of cutting-edge electronic systems.
No responses yet