What is an HDI PCB?
An HDI PCB is a type of printed circuit board that features a higher wiring density than traditional PCBs. This is achieved through the use of smaller vias, finer trace widths, and advanced manufacturing techniques. HDI PCBs allow for the integration of more components and connections within a smaller area, enabling the creation of compact and high-performance electronic devices.
The main characteristics of HDI PCBs include:
– Higher wiring density compared to conventional PCBs
– Smaller vias (microvias) with diameters less than 150 microns
– Finer trace widths and spacing
– Increased number of layers
– Advanced manufacturing processes, such as sequential build-up (SBU) and any-layer HDI
Benefits of HDI PCBs
HDI PCBs offer several advantages over traditional PCBs, making them an attractive choice for many applications. Some of the key benefits include:
-
Miniaturization: The higher wiring density and smaller components used in HDI PCBs allow for the creation of more compact devices. This is particularly important in industries such as consumer electronics, where smaller and lighter products are in high demand.
-
Improved performance: With shorter signal paths and reduced parasitic capacitance and inductance, HDI PCBs offer better signal integrity and faster signal propagation. This leads to improved overall performance of the electronic device.
-
Increased functionality: The ability to integrate more components and connections within a smaller area enables the incorporation of more features and functions into the device. This is crucial for applications that require complex functionality in a limited space.
-
Cost-effectiveness: Although HDI PCBs may have a higher initial cost compared to traditional PCBs, they often lead to cost savings in the long run. The miniaturization and increased functionality offered by HDI PCBs can reduce the overall size and weight of the device, resulting in lower material and shipping costs.
HDI PCB Manufacturing Process
The manufacturing process for HDI PCBs is more complex than that of traditional PCBs due to the higher density and smaller features involved. The two main methods used for HDI PCB fabrication are sequential build-up (SBU) and any-layer HDI.
Sequential Build-Up (SBU)
In the SBU process, the HDI PCB is constructed layer by layer, with each layer being added sequentially. The process involves the following steps:
-
Core layer fabrication: A standard double-sided PCB is used as the core layer, which serves as the foundation for the HDI PCB.
-
Laser drilling: Microvias are drilled into the core layer using a laser, creating small, precise holes for interconnections.
-
Plating: The microvias are filled with copper to establish electrical connections between layers.
-
Lamination: Additional layers of prepreg (pre-impregnated) material and copper foil are laminated onto the core layer.
-
Repetition: Steps 2-4 are repeated for each subsequent layer until the desired number of layers is achieved.
-
Final finishing: The outer layers are processed, and the final finishing, such as solder mask application and surface finish, is performed.
Any-Layer HDI
Any-layer HDI, also known as built-up or stacked microvia HDI, involves the fabrication of HDI PCBs with microvias that span multiple layers. This method allows for even greater wiring density and flexibility in design. The process is similar to the SBU method but with the added capability of creating microvias that connect non-adjacent layers.
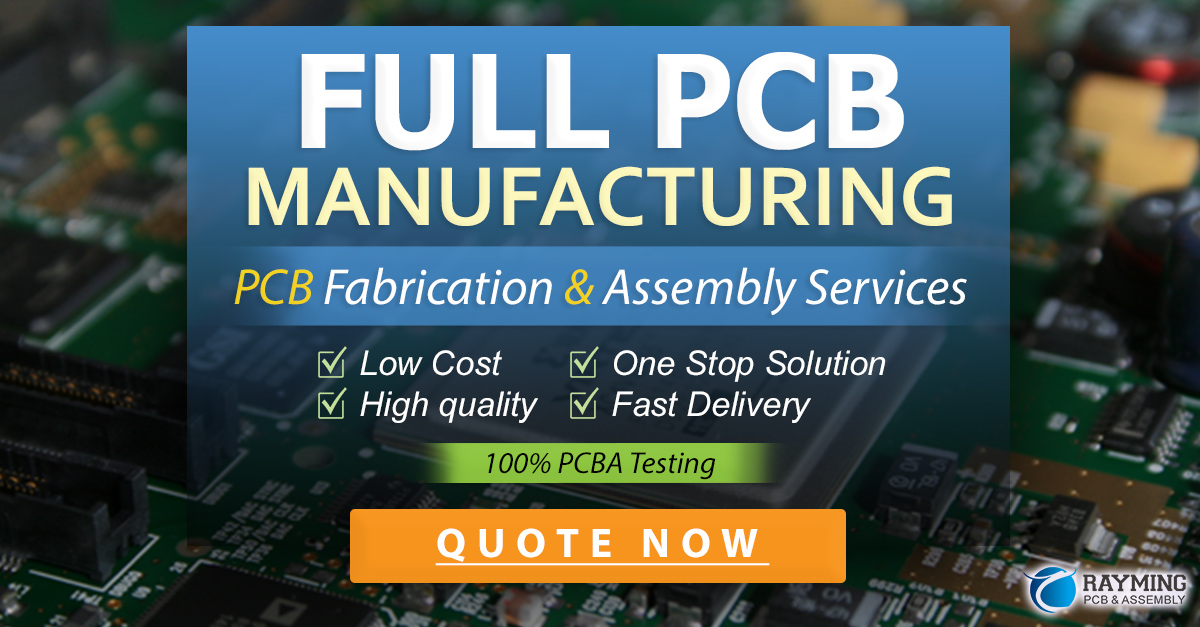
HDI PCB Design Considerations
Designing an HDI PCB requires careful consideration of various factors to ensure optimal performance and manufacturability. Some key design considerations include:
-
Via size and placement: Microvias in HDI PCBs are typically smaller than those in traditional PCBs, with diameters ranging from 50 to 150 microns. The placement of these vias is critical to ensure proper connectivity and signal integrity.
-
Trace width and spacing: HDI PCBs feature finer trace widths and spacing compared to traditional PCBs. Designers must adhere to the minimum trace width and spacing guidelines specified by the manufacturer to ensure manufacturability and reliability.
-
Layer stack-up: The arrangement of layers in an HDI PCB is crucial for signal integrity and manufacturability. Designers must carefully plan the layer stack-up, considering factors such as signal routing, power distribution, and impedance control.
-
Signal integrity: With the increased wiring density and smaller features in HDI PCBs, signal integrity becomes a critical concern. Designers must employ techniques such as impedance matching, proper grounding, and shielding to minimize signal interference and ensure reliable performance.
-
Thermal management: The higher component density in HDI PCBs can lead to increased heat generation. Designers must incorporate appropriate thermal management strategies, such as the use of thermal vias, heat sinks, and proper component placement, to ensure adequate heat dissipation.
Applications of HDI PCBs
HDI PCBs find applications in a wide range of industries and products where miniaturization, high performance, and increased functionality are essential. Some common applications include:
-
Consumer electronics: Smartphones, tablets, wearables, and other portable devices heavily rely on HDI PCBs to achieve compact sizes and advanced features.
-
Aerospace and defense: HDI PCBs are used in avionics, satellite systems, and military equipment, where reliability, performance, and space constraints are critical.
-
Medical devices: Implantable devices, diagnostic equipment, and other medical electronics benefit from the miniaturization and reliability offered by HDI PCBs.
-
Automotive electronics: As vehicles become more technologically advanced, HDI PCBs are used in various automotive applications, such as infotainment systems, driver assistance systems, and engine control units.
-
Industrial automation: HDI PCBs are employed in industrial control systems, sensors, and communication devices to enable compact and reliable automation solutions.
HDI PCB Testing and Quality Control
Ensuring the quality and reliability of HDI PCBs is crucial for the proper functioning and longevity of the electronic devices they are used in. Rigorous testing and quality control measures are employed throughout the manufacturing process to identify and address any defects or issues.
Some common testing methods for HDI PCBs include:
-
Automated optical inspection (AOI): AOI systems use high-resolution cameras and advanced image processing algorithms to inspect the PCB for defects such as missing components, incorrect component placement, and Solder Bridging.
-
X-ray Inspection: X-ray imaging is used to inspect the internal structure of the HDI PCB, particularly the microvias and interconnections, for any defects or anomalies.
-
Electrical testing: Various electrical tests, such as continuity testing, insulation resistance testing, and high-potential (hipot) testing, are performed to ensure proper electrical functionality and isolation between circuits.
-
Microsectioning: In some cases, destructive testing methods like microsectioning may be employed to examine the cross-section of the HDI PCB and assess the quality of the plating, lamination, and via formation.
In addition to these testing methods, manufacturers often implement strict quality control measures, such as statistical process control (SPC) and continuous improvement programs, to maintain consistent quality and identify areas for optimization.
Future Trends in HDI PCB Technology
As the demand for smaller, more powerful electronic devices continues to grow, HDI PCB technology is expected to evolve to meet these challenges. Some of the future trends in HDI PCB technology include:
-
Increased layer count: HDI PCBs with higher layer counts, such as 8, 10, or even 12 layers, are becoming more common to accommodate the growing complexity and functionality of electronic devices.
-
Embedding components: The integration of passive components, such as resistors and capacitors, directly into the PCB Substrate is gaining traction. This technique, known as embedded component technology (ECT), further reduces the size and improves the performance of HDI PCBs.
-
Advanced materials: The development of new, high-performance materials, such as low-loss dielectrics and ultra-thin laminates, will enable the fabrication of HDI PCBs with even finer features and improved signal integrity.
-
3D printing: Additive manufacturing techniques, such as 3D printing, are being explored for the fabrication of HDI PCBs. This approach has the potential to enable more complex geometries, faster prototyping, and customization of PCBs.
-
Artificial intelligence (AI) in design and manufacturing: AI and machine learning algorithms are being employed to optimize HDI PCB design and manufacturing processes. These technologies can help identify potential issues, suggest design improvements, and streamline production, leading to higher quality and efficiency.
Frequently Asked Questions (FAQ)
-
Q: What is the difference between HDI PCBs and traditional PCBs?
A: HDI PCBs have a higher wiring density compared to traditional PCBs, featuring smaller vias (microvias), finer trace widths, and advanced manufacturing techniques. This allows for the integration of more components and connections within a smaller area, enabling the creation of compact and high-performance electronic devices. -
Q: What are the benefits of using HDI PCBs?
A: The main benefits of using HDI PCBs include miniaturization, improved performance, increased functionality, and cost-effectiveness. HDI PCBs allow for the creation of smaller, lighter devices with enhanced signal integrity, faster signal propagation, and more features and functions. -
Q: What are the common manufacturing processes for HDI PCBs?
A: The two main manufacturing processes for HDI PCBs are sequential build-up (SBU) and any-layer HDI. In the SBU process, the HDI PCB is constructed layer by layer, with each layer being added sequentially. Any-layer HDI involves the fabrication of HDI PCBs with microvias that span multiple layers, allowing for even greater wiring density and flexibility in design. -
Q: What are the key design considerations for HDI PCBs?
A: When designing HDI PCBs, key considerations include via size and placement, trace width and spacing, layer stack-up, signal integrity, and thermal management. Designers must carefully plan these aspects to ensure optimal performance, manufacturability, and reliability of the HDI PCB. -
Q: What are some common applications of HDI PCBs?
A: HDI PCBs are widely used in various industries and applications where miniaturization, high performance, and increased functionality are essential. Common applications include consumer electronics, aerospace and defense, medical devices, automotive electronics, and industrial automation.
Conclusion
HDI PCBs have revolutionized the electronic manufacturing industry by enabling the creation of smaller, more powerful, and feature-rich devices. With their higher wiring density, improved performance, and increased functionality, HDI PCBs have become an essential technology for meeting the demands of modern electronic products.
As the trend towards miniaturization and advanced functionality continues, HDI PCB technology is expected to evolve further, incorporating new materials, manufacturing processes, and design techniques. By staying at the forefront of these developments, manufacturers and designers can leverage the benefits of HDI PCBs to create innovative and competitive electronic devices that meet the ever-changing needs of the market.
Comparison | HDI PCBs | Traditional PCBs |
---|---|---|
Wiring Density | Higher, with smaller vias and trace widths | Lower, with larger vias and trace widths |
Component Density | Higher, allowing for more miniaturization | Lower, limited by larger feature sizes |
Signal Integrity | Improved, due to shorter signal paths | Relatively lower, with longer signal paths |
Manufacturing Process | More complex, involving SBU or any-layer HDI | Simpler, using standard PCB fabrication techniques |
Cost | Higher initial cost, but potential for long-term savings | Lower initial cost, but less potential for miniaturization and added functionality |
In summary, HDI PCBs offer a powerful solution for the challenges of miniaturization, performance, and functionality in electronic devices. By understanding the capabilities, design considerations, and manufacturing processes involved in HDI PCBs, engineers and manufacturers can harness this technology to create innovative and competitive products that push the boundaries of what is possible in the world of electronics.
No responses yet