Introduction to Lead Free Soldering
Lead free soldering is the process of joining two or more electronic components together using a lead-free solder alloy. Lead-free solders are alloys that do not contain any lead, which is a toxic substance that can cause health and environmental problems. Instead, lead-free solders typically contain tin, silver, copper, and other metals that have similar melting points and wetting properties to lead-based solders.
The switch to lead-free soldering was driven by the European Union’s Restriction of Hazardous Substances (RoHS) directive, which took effect in 2006. The RoHS directive banned the use of lead and other hazardous substances in electronic and electrical equipment sold in the EU. Since then, many other countries have followed suit and implemented similar regulations, making lead-free soldering the standard for the electronics industry worldwide.
Benefits of Lead Free Soldering
There are several benefits to using lead-free solders in electronics manufacturing:
-
Environmental and health benefits: Lead is a toxic substance that can cause a range of health problems, including neurological damage, kidney failure, and reproductive issues. By eliminating lead from solder alloys, lead-free soldering helps to reduce the environmental and health impacts of electronics manufacturing.
-
Improved reliability: Lead-free solders have been shown to have better mechanical strength, thermal fatigue resistance, and creep resistance compared to lead-based solders. This can lead to improved reliability and longer lifetimes for electronic devices.
-
Compliance with regulations: As mentioned above, many countries have implemented regulations that restrict or ban the use of lead in electronics. By using lead-free solders, electronics manufacturers can ensure compliance with these regulations and avoid penalties or fines.
Challenges of Lead Free Soldering
While lead-free soldering offers many benefits, it also presents some challenges compared to traditional lead-based soldering:
-
Higher melting points: Lead-free solders typically have higher melting points than lead-based solders, which means that higher temperatures are required for soldering. This can lead to increased thermal stress on components and PCBs, which can cause reliability issues if not managed properly.
-
Wetting and spreading: Lead-free solders may have different wetting and spreading properties compared to lead-based solders, which can affect the quality and reliability of solder joints. This can be especially challenging for fine-pitch components and high-density PCBs.
-
Tin whiskers: Some lead-free solder alloys, particularly those with high tin content, can be prone to the formation of tin whiskers. Tin whiskers are thin, hair-like growths of tin that can cause short circuits and other reliability issues in electronic devices.
Despite these challenges, lead-free soldering has become the standard for the electronics industry, and manufacturers have developed a range of techniques and best practices to overcome these challenges and ensure high-quality, reliable solder joints.
Lead Free Solder Alloys
There are several lead-free solder alloys that are commonly used in electronics manufacturing. The choice of alloy depends on factors such as the melting point, wetting properties, mechanical strength, and cost. Here are some of the most common lead-free solder alloys:
Tin-Silver-Copper (SAC) Alloys
Tin-silver-copper (SAC) alloys are the most widely used lead-free solder alloys in the electronics industry. They typically contain 95-96% tin, 3-4% silver, and 0.5-1% copper. SAC alloys have good mechanical strength, thermal fatigue resistance, and wetting properties, making them suitable for a wide range of applications.
Some common SAC alloy compositions include:
- SAC305 (96.5% Sn, 3.0% Ag, 0.5% Cu)
- SAC387 (95.5% Sn, 3.8% Ag, 0.7% Cu)
- SAC405 (95.5% Sn, 4.0% Ag, 0.5% Cu)
SAC alloys have a melting point range of 217-220°C, which is higher than traditional lead-based solders (183°C for Sn63Pb37). This means that higher reflow temperatures are required for SAC alloys, which can increase thermal stress on components and PCBs.
Tin-Copper (SnCu) Alloys
Tin-copper (SnCu) alloys are another common lead-free solder alloy, particularly for wave soldering applications. They typically contain 99.3% tin and 0.7% copper. SnCu alloys have good mechanical strength and thermal fatigue resistance, but may have lower wetting properties compared to SAC alloys.
SnCu alloys have a melting point of 227°C, which is higher than SAC alloys. This means that even higher reflow temperatures may be required for SnCu alloys, which can further increase thermal stress on components and PCBs.
Tin-Bismuth (SnBi) Alloys
Tin-bismuth (SnBi) alloys are sometimes used as a low-temperature lead-free solder alloy. They typically contain 42% tin and 58% bismuth. SnBi alloys have a melting point of 138°C, which is lower than both lead-based and SAC alloys. This makes them suitable for soldering temperature-sensitive components or substrates.
However, SnBi alloys have lower mechanical strength and thermal fatigue resistance compared to SAC alloys, which can limit their use in some applications. They also have a tendency to form large, plate-like grains, which can affect the reliability of solder joints.
Other Lead Free Alloys
There are several other lead-free solder alloys that are used in specific applications or for specialized requirements. These include:
- Tin-silver (SnAg) alloys: Used for high-temperature applications or for soldering to silver-plated surfaces.
- Tin-zinc (SnZn) alloys: Used for soldering to aluminum or for low-temperature applications.
- Tin-antimony (SnSb) alloys: Used for high-temperature applications or for soldering to gold-plated surfaces.
The choice of lead-free solder alloy depends on the specific requirements of the application, including the operating temperature, mechanical stress, and substrate materials. Manufacturers may also consider factors such as cost, availability, and compatibility with existing soldering processes and equipment when selecting a lead-free solder alloy.
Reflow Soldering Process
Reflow soldering is a process used to attach surface mount components to a printed circuit board (PCB) using a lead-free solder alloy. The reflow soldering process involves applying solder paste to the PCB pads, placing the components onto the solder paste, and then heating the assembly in a reflow oven to melt the solder and form a permanent connection between the components and the PCB.
The reflow soldering process typically involves the following steps:
-
Solder paste printing: Solder paste, which is a mixture of solder alloy powder and flux, is applied to the PCB pads using a stencil or screen printing process. The solder paste is typically applied in a thin, uniform layer that matches the pattern of the pads on the PCB.
-
Component placement: The surface mount components are placed onto the solder paste using an automated pick-and-place machine or by hand. The components are positioned accurately on the pads and held in place by the tackiness of the solder paste.
-
Reflow: The PCB assembly is then placed in a reflow oven, which heats the assembly to a specific temperature profile that melts the solder alloy and forms a metallurgical bond between the components and the PCB pads. The reflow profile typically involves a preheat stage, a soak stage, a reflow stage, and a cooling stage.
-
Inspection: After the reflow process is complete, the PCB assembly is inspected for defects such as bridging, tombstoning, or insufficient solder joints. Automated optical inspection (AOI) systems are often used to detect defects quickly and accurately.
-
Rework and repair: If defects are found during the inspection process, the PCB assembly may need to be reworked or repaired. This may involve removing and replacing components, adding additional solder, or using specialized repair techniques.
The reflow soldering process is a critical step in the manufacturing of electronic devices, as it directly affects the quality and reliability of the solder joints and the overall performance of the device. Proper control of the reflow profile, solder paste printing, and component placement are essential for achieving high-quality solder joints and minimizing defects.
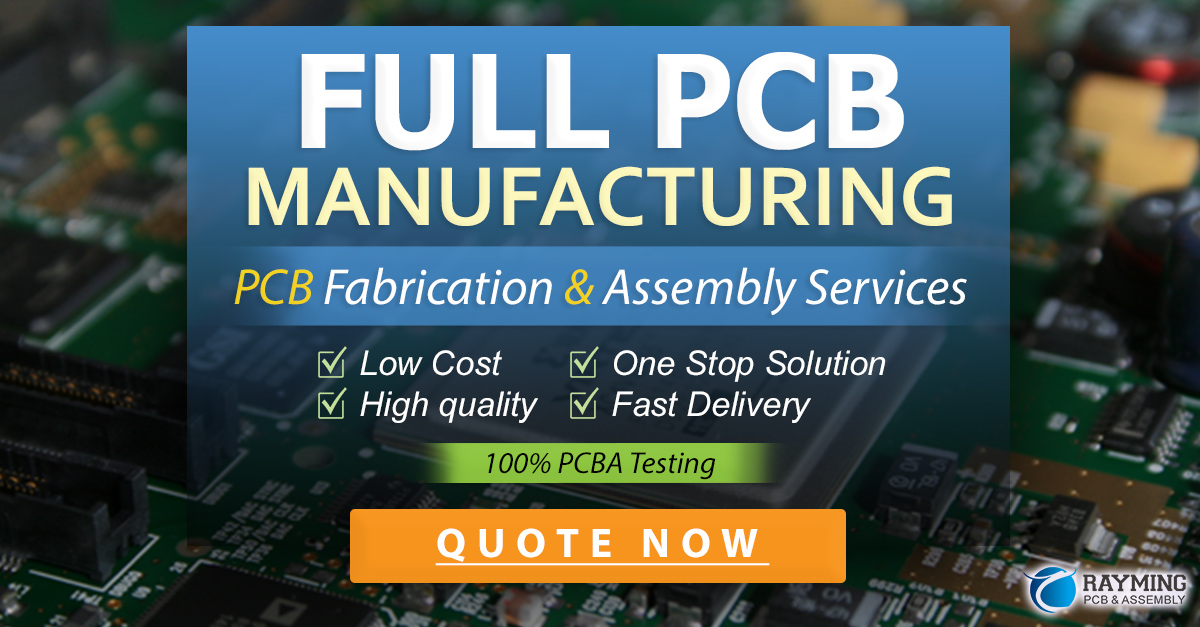
Reflow Profile for Lead Free Soldering
The reflow profile is a critical aspect of the lead-free soldering process, as it determines the time and temperature profile that the PCB assembly is subjected to during the reflow process. The reflow profile must be carefully designed and controlled to ensure that the solder alloy melts and forms a reliable bond between the components and the PCB pads, while minimizing thermal stress on the components and the PCB.
A typical reflow profile for lead-free soldering consists of four stages:
-
Preheat: The PCB assembly is heated to a temperature below the melting point of the solder alloy, typically around 150-180°C. The purpose of the preheat stage is to evaporate the solvents in the solder paste and activate the flux, which helps to remove oxidation and improve wetting of the solder. The preheat stage also helps to minimize thermal shock to the components and the PCB.
-
Soak: The PCB assembly is held at a constant temperature, typically around 180-200°C, for a period of time to allow the components and the PCB to reach a uniform temperature. The soak stage helps to further activate the flux and prepare the solder alloy for melting.
-
Reflow: The PCB assembly is heated to a peak temperature above the melting point of the solder alloy, typically around 235-250°C for SAC alloys. The peak temperature is held for a short period of time, typically 30-90 seconds, to allow the solder to melt and form a metallurgical bond with the component leads and the PCB pads. The reflow stage is the most critical stage of the reflow profile, as it directly affects the quality and reliability of the solder joints.
-
Cooling: The PCB assembly is cooled at a controlled rate to room temperature. The cooling rate must be carefully controlled to minimize thermal stress on the components and the PCB, and to allow the solder joints to solidify and form a strong, reliable bond.
The specific parameters of the reflow profile, such as the ramp rates, soak times, and peak temperatures, depend on the specific lead-free solder alloy being used, as well as the size and thermal mass of the components and the PCB. Manufacturers typically use a combination of theoretical calculations, experimental testing, and process monitoring to develop and optimize the reflow profile for their specific application.
Here is an example of a typical reflow profile for a SAC305 lead-free solder alloy:
Stage | Temperature Range (°C) | Time (seconds) |
---|---|---|
Preheat | 25-150 | 60-90 |
Soak | 150-180 | 60-120 |
Reflow | 235-245 | 30-60 |
Cooling | 245-25 | 30-60 |
It is important to note that the reflow profile is just one aspect of the lead-free soldering process, and that other factors such as the solder paste printing, component placement, and PCB design also play a critical role in achieving high-quality solder joints and reliable electronic devices.
Defects in Lead Free Soldering
Despite the many advantages of lead-free soldering, there are several types of defects that can occur during the soldering process. These defects can affect the quality and reliability of the solder joints and the overall performance of the electronic device. Here are some of the most common types of defects in lead-free soldering:
Bridging
Bridging is a defect that occurs when solder inadvertently connects two or more adjacent pads or component leads that should not be connected. Bridging can be caused by excessive solder paste, incorrect component placement, or insufficient solder mask between pads. Bridging can cause short circuits and other electrical failures in the device.
Tombstoning
Tombstoning, also known as drawbridging, is a defect that occurs when a component stands up on one end during the reflow process, rather than lying flat on the PCB. Tombstoning is typically caused by uneven heating or cooling of the component, or by unbalanced solder joints on the component leads. Tombstoning can cause open circuits or intermittent connections in the device.
Insufficient Solder
Insufficient solder is a defect that occurs when there is not enough solder to form a reliable bond between the component and the PCB pad. Insufficient solder can be caused by poor solder paste printing, incorrect component placement, or insufficient reflow time or temperature. Insufficient solder can cause weak or intermittent connections in the device.
Excess Solder
Excess solder is a defect that occurs when there is too much solder on the component or PCB pad. Excess solder can be caused by excessive solder paste printing, incorrect component placement, or excessive reflow time or temperature. Excess solder can cause bridging or other electrical failures in the device.
Poor Wetting
Poor wetting is a defect that occurs when the solder does not flow or adhere properly to the component or PCB pad. Poor wetting can be caused by contamination, oxidation, or incorrect reflow profile parameters. Poor wetting can cause weak or unreliable solder joints in the device.
Head-in-Pillow
Head-in-pillow (HIP) is a defect that occurs when the solder ball on a BGA component does not collapse and wet the PCB pad during the reflow process. HIP can be caused by oxidation, contamination, or incorrect reflow profile parameters. HIP can cause open circuits or intermittent connections in the device.
To minimize the occurrence of these defects, manufacturers must carefully control the lead-free soldering process, including the solder paste printing, component placement, and reflow profile. They must also use appropriate materials, such as solder pastes and fluxes that are compatible with the lead-free solder alloy and the PCB surface finish. Regular process monitoring and quality control measures, such as visual inspection and electrical testing, can also help to identify and correct defects before they affect the final product.
Frequently Asked Questions (FAQ)
1. What is the difference between lead-based and lead-free soldering?
Lead-based soldering uses a solder alloy that contains lead, typically in a ratio of 63% tin and 37% lead (Sn63Pb37). Lead-free soldering uses a solder alloy that does not contain lead, but instead uses other metals such as tin, silver, and copper (e.g. SAC305). Lead-free soldering has become the standard in the electronics industry due to concerns about the health and environmental impacts of lead.
2. What are the most common lead-free solder alloys?
The most common lead-free solder alloys are tin-silver-copper (SAC) alloys, such as SAC305 and SAC405. These alloys typically contain 95-96% tin, 3-4% silver, and 0.5-1% copper. Other common lead-free alloys include tin-copper (SnCu) and tin-bismuth (SnBi) alloys.
3. What are the challenges of lead-free soldering compared to lead-based soldering?
Lead-free soldering presents several challenges compared to lead-based soldering, including higher melting points, different wetting and spreading properties, and the potential for tin whisker formation. Lead-free solders also require higher reflow temperatures, which can increase thermal stress on components and PCBs.
4. What are the key steps in the reflow soldering process?
The key steps in the reflow soldering process are:
- Solder paste printing: Applying solder paste to the PCB pads using a stencil or screen printing process.
- Component placement: Placing the surface mount components onto the solder paste using an automated pick-and-place machine or by hand.
- Reflow: Heating the PCB assembly in a reflow oven to melt the solder and form a bond between the components and the PCB pads.
- Inspection: Inspecting the PCB assembly for defects such as bridging, tombstoning, or insufficient solder joints.
- Rework and repair: Reworking or repairing any defects found during the inspection process.
5. What are some common defects that can occur in lead-free soldering?
Some common defects that can occur in lead-free soldering include:
- Bridging: Solder inadvertently connecting two or more adjacent pads or component leads.
- Tombstoning: A component standing up on one end during the reflow process.
- Insufficient solder: Not enough solder to form a reliable bond between the component and the PCB pad.
- Excess solder: Too much solder on the component or PCB pad.
- Poor wetting: Solder
No responses yet