Introduction to PCB Grounding
Proper grounding is essential for the optimal performance and reliability of printed circuit boards (PCBs). PCB grounding involves strategically connecting certain points of the circuit to a common ground plane to provide a low-impedance return path for currents, minimize noise and electromagnetic interference (EMI), and ensure the safety of the electronic system. In this comprehensive article, we will delve into the principles, techniques, and best practices for effective PCB grounding.
Understanding the Importance of PCB Grounding
Minimizing Noise and EMI
One of the primary reasons for implementing proper PCB grounding is to minimize noise and EMI. When high-frequency signals travel through the PCB traces, they can generate electromagnetic fields that interfere with other components or circuits. By providing a low-impedance return path through a well-designed ground plane, the noise and EMI can be effectively mitigated, ensuring the integrity of the signals and reducing crosstalk between different parts of the circuit.
Ensuring Signal Integrity
Effective PCB grounding is crucial for maintaining signal integrity. When signals travel through the PCB traces, they require a reference plane to maintain their voltage levels and prevent distortion. The ground plane acts as this reference, providing a stable and consistent voltage reference throughout the circuit. By minimizing the impedance of the ground plane and keeping it as close to the signal traces as possible, signal integrity can be preserved, resulting in cleaner and more reliable signal transmission.
Enhancing Safety and Reliability
Proper PCB grounding also plays a vital role in ensuring the safety and reliability of electronic systems. In the event of a fault or surge, a well-designed ground plane can provide a safe path for the excess current to flow, preventing damage to sensitive components and reducing the risk of electrical shock to users. Additionally, effective grounding helps to dissipate heat generated by components, improving the overall thermal management of the PCB and enhancing its long-term reliability.
Grounding Techniques for PCBs
Single-Point Grounding
Single-point grounding is a technique where all ground connections are made to a single point on the PCB, typically referred to as the “star ground.” This approach minimizes ground loops and ensures that all ground currents flow through a single, low-impedance path. Single-point grounding is particularly effective for low-frequency circuits and systems with a limited number of ground connections. However, it may not be suitable for high-frequency designs or complex circuits with multiple ground planes.
Multi-Point Grounding
Multi-point grounding involves connecting the ground points of different components or sections of the PCB to multiple points on the ground plane. This technique is commonly used in high-frequency designs and circuits with multiple ground planes. By providing multiple return paths for ground currents, multi-point grounding helps to minimize the impedance of the ground plane and reduce the risk of ground loops. However, careful design considerations are required to ensure that the multiple ground connections do not introduce unwanted noise or create potential differences between different ground points.
Hybrid Grounding
Hybrid grounding is a combination of single-point and multi-point grounding techniques. It involves using a single-point ground for low-frequency signals and a multi-point ground for high-frequency signals. This approach takes advantage of the benefits of both techniques, providing a low-impedance return path for high-frequency currents while minimizing ground loops for low-frequency signals. Hybrid grounding requires careful segregation of the ground planes and strategic placement of ground connections to ensure optimal performance.
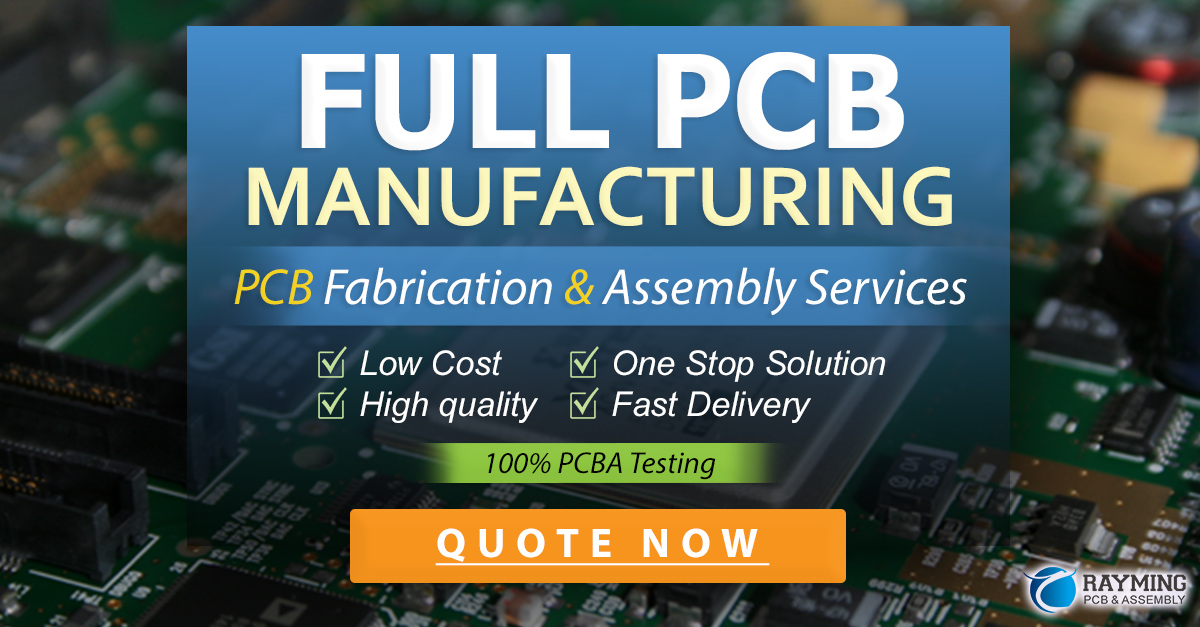
Best Practices for PCB Grounding
Proper Ground Plane Design
Designing an effective ground plane is crucial for successful PCB grounding. The ground plane should be a solid, continuous layer of copper that covers as much of the PCB surface as possible. It should be positioned as close to the signal traces as the manufacturing process allows to minimize the loop area and reduce impedance. In multi-layer PCBs, dedicated ground planes should be used, with vias strategically placed to provide low-impedance connections between layers.
Ground Plane Partitioning
In complex PCB designs with multiple subsystems or signal types, it may be necessary to partition the ground plane to isolate different sections of the circuit. This technique involves dividing the ground plane into separate regions, each dedicated to a specific subsystem or signal type. Ground plane partitioning helps to prevent noise coupling between different sections of the PCB and ensures that each subsystem has its own low-impedance return path. However, careful consideration must be given to the placement of partitioning slots or gaps to avoid creating unintended resonances or impedance discontinuities.
Minimizing Ground Loops
Ground loops occur when there are multiple paths for ground currents to flow, creating potential differences and inducing noise in the circuit. To minimize ground loops, it is important to ensure that all ground connections are made to a common point or plane, and that the ground plane has a low impedance. Avoiding long ground traces and using multiple vias to connect ground points to the plane can help reduce the risk of ground loops. In some cases, isolating sensitive circuits or using galvanic isolation techniques may be necessary to break ground loops and prevent noise coupling.
Component Placement and Routing
Proper component placement and routing play a significant role in effective PCB grounding. Components should be placed as close to their respective ground connections as possible to minimize the length of ground traces and reduce impedance. High-frequency components and signals should be positioned near the center of the ground plane to minimize the loop area and reduce EMI. Routing of signal traces should be done in a manner that minimizes the crossing of ground planes and avoids creating unnecessary ground loops.
Grounding of Shielded Cables and Connectors
When using shielded cables and connectors in a PCB design, proper grounding of the shields is essential to ensure effective shielding and prevent noise coupling. The shields should be connected to the ground plane at both ends of the cable, using low-impedance connections such as dedicated ground pins or conductive gaskets. In some cases, it may be necessary to use 360-degree shielding or EMI filters to further reduce noise and interference.
Table: Common PCB Grounding Issues and Solutions
Issue | Cause | Solution |
---|---|---|
Excessive noise and EMI | Poor ground plane design or inadequate grounding connections | Improve ground plane continuity and minimize impedance |
Signal integrity degradation | Insufficient ground reference or long ground traces | Optimize ground plane placement and use multiple vias |
Ground loops | Multiple ground paths or improper ground connections | Ensure single-point grounding and isolate sensitive circuits |
Thermal management issues | Inadequate grounding of heat-generating components | Provide sufficient grounding and use thermal vias |
Shielding effectiveness | Improper grounding of shielded cables or connectors | Implement 360-degree shielding and use conductive gaskets |
Frequently Asked Questions (FAQ)
1. What is the purpose of grounding in PCB design?
Answer: The purpose of grounding in PCB design is to provide a low-impedance return path for currents, minimize noise and electromagnetic interference (EMI), ensure signal integrity, and enhance the safety and reliability of the electronic system.
2. What is the difference between single-point and multi-point grounding?
Answer: Single-point grounding involves connecting all ground points to a single location on the PCB, known as the star ground. It is effective for low-frequency circuits and minimizes ground loops. Multi-point grounding, on the other hand, connects ground points to multiple locations on the ground plane, providing multiple return paths for ground currents. It is commonly used in high-frequency designs and circuits with multiple ground planes.
3. How can ground loops be minimized in PCB design?
Answer: Ground loops can be minimized by ensuring that all ground connections are made to a common point or plane, using a low-impedance ground plane, avoiding long ground traces, and using multiple vias to connect ground points to the plane. In some cases, isolating sensitive circuits or using galvanic isolation techniques may be necessary to break ground loops and prevent noise coupling.
4. What is the importance of ground plane partitioning in PCB grounding?
Answer: Ground plane partitioning involves dividing the ground plane into separate regions, each dedicated to a specific subsystem or signal type. It helps to prevent noise coupling between different sections of the PCB and ensures that each subsystem has its own low-impedance return path. However, careful consideration must be given to the placement of partitioning slots or gaps to avoid creating unintended resonances or impedance discontinuities.
5. How should shielded cables and connectors be grounded in a PCB design?
Answer: Shielded cables and connectors should be grounded by connecting the shields to the ground plane at both ends of the cable, using low-impedance connections such as dedicated ground pins or conductive gaskets. This ensures effective shielding and prevents noise coupling. In some cases, 360-degree shielding or EMI filters may be necessary to further reduce noise and interference.
Conclusion
Effective grounding is a critical aspect of PCB design that ensures optimal performance, signal integrity, and reliability of electronic systems. By understanding the principles of PCB grounding, applying appropriate grounding techniques, and following best practices, designers can minimize noise, reduce EMI, and create robust and reliable PCB layouts. Whether using single-point, multi-point, or hybrid grounding approaches, careful consideration of ground plane design, component placement, routing, and shielding is essential for achieving successful PCB grounding. By addressing common grounding issues and implementing suitable solutions, designers can optimize their PCB designs for enhanced functionality and longevity.
No responses yet