Introduction to Glass PCBs
Glass Printed Circuit Boards (PCBs) are an emerging technology that offers a range of benefits over traditional PCB materials like FR-4. Glass PCBs are made using a thin layer of glass as the substrate material, which provides superior electrical insulation, dimensional stability, and thermal performance compared to conventional PCB substrates.
Glass PCBs are gaining popularity among PCB designers due to their unique properties and potential applications in various industries, including telecommunications, aerospace, automotive, and medical devices. This article will explore the advantages, manufacturing process, applications, and future prospects of Glass PCBs.
Advantages of Glass PCBs
1. Excellent Electrical Insulation
Glass is an excellent electrical insulator, with a dielectric constant of around 5.3 and a loss tangent of 0.006 at 1 MHz. This makes Glass PCBs ideal for high-frequency applications, as they minimize signal loss and crosstalk between adjacent traces.
2. High Dimensional Stability
Glass has a low coefficient of thermal expansion (CTE), which means it maintains its dimensions even under extreme temperature changes. This dimensional stability is crucial for applications that require precise alignment and registration, such as optoelectronic devices and sensors.
3. Superior Thermal Performance
Glass has a thermal conductivity of around 1 W/mK, which is higher than that of FR-4 (0.3 W/mK). This allows Glass PCBs to dissipate heat more efficiently, reducing the risk of thermal damage to components and improving the overall reliability of the circuit.
4. Transparency and Aesthetic Appeal
Glass PCBs are transparent, which makes them visually appealing and allows for unique design possibilities. The transparency also enables the use of optical inspection techniques for quality control and fault detection.
5. Environmentally Friendly
Glass is a recyclable and eco-friendly material, making Glass PCBs a more sustainable choice compared to traditional PCB materials. The manufacturing process for Glass PCBs also generates less waste and requires fewer harsh chemicals, further reducing the environmental impact.
Manufacturing Process of Glass PCBs
The manufacturing process for Glass PCBs is similar to that of traditional PCBs, with a few key differences. The main steps involved are:
-
Substrate Preparation: The glass substrate is cleaned and prepared for the subsequent steps. This may involve polishing the surface to achieve the desired smoothness and applying an adhesion promoter to enhance the bonding of the conductive layers.
-
Metallization: A thin layer of metal, typically copper, is deposited onto the glass substrate using techniques like sputtering, electroless plating, or lamination. This layer serves as the conductive traces and pads for the circuit.
-
Patterning: The desired circuit pattern is transferred onto the metallized glass substrate using photolithography. A photoresist layer is applied, exposed to UV light through a mask, and developed to create the desired pattern.
-
Etching: The exposed metal areas are etched away using a chemical solution, leaving behind the desired circuit pattern.
-
Insulation and Protection: A dielectric layer, such as solder mask, is applied over the circuit pattern to provide insulation and protection against environmental factors.
-
Drilling and Cutting: Holes are drilled through the Glass PCB for component mounting and interconnections. The board is then cut to the desired shape and size.
-
Assembly: Components are mounted onto the Glass PCB using techniques like surface-mount technology (SMT) or through-hole mounting. The board is then tested and inspected for quality control.
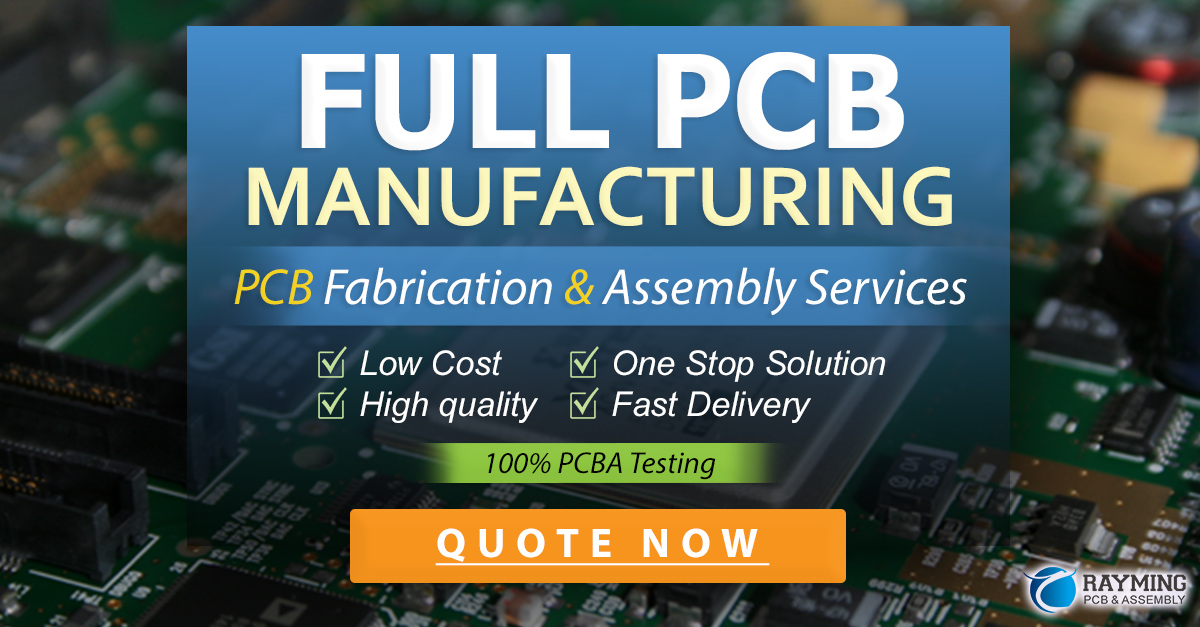
Applications of Glass PCBs
Glass PCBs find applications in various industries due to their unique properties and benefits. Some of the key application areas include:
1. High-Frequency Electronics
Glass PCBs are well-suited for high-frequency applications, such as 5G telecommunications, radar systems, and satellite communication. The low dielectric constant and loss tangent of glass minimize signal attenuation and distortion, enabling high-speed data transmission and improved signal integrity.
2. Optoelectronics and Photonics
The transparency of Glass PCBs makes them ideal for optoelectronic and photonic applications, such as LED lighting, displays, and optical sensors. The glass substrate allows for the integration of optical components and waveguides directly onto the PCB, enabling compact and efficient optoelectronic systems.
3. Automotive Electronics
Glass PCBs can withstand the harsh environmental conditions encountered in automotive applications, such as extreme temperatures, vibrations, and moisture. They are used in various automotive systems, including engine control units, infotainment systems, and advanced driver assistance systems (ADAS).
4. Medical Devices
The biocompatibility and chemical resistance of glass make Glass PCBs suitable for medical device applications. They are used in implantable devices, diagnostic equipment, and medical sensors, where reliability and long-term stability are critical.
5. Aerospace and Defense
Glass PCBs offer high reliability and performance in demanding aerospace and defense applications. They are used in avionics systems, satellite communication, and military electronics, where they must withstand extreme environmental conditions and meet stringent reliability requirements.
Future Prospects and Challenges
Glass PCBs are an emerging technology with significant potential for future growth and innovation. Some of the key prospects and challenges include:
1. Advanced Manufacturing Techniques
Researchers are exploring advanced manufacturing techniques to further enhance the capabilities of Glass PCBs. These include 3D printing, laser direct structuring (LDS), and additive manufacturing, which enable the creation of complex 3D structures and embedded components within the glass substrate.
2. Integration with Other Technologies
Glass PCBs can be integrated with other emerging technologies, such as flexible electronics, wearable devices, and Internet of Things (IoT) applications. The combination of glass substrates with flexible materials and sensors opens up new possibilities for smart and connected devices.
3. Cost and Scalability
Currently, the manufacturing cost of Glass PCBs is higher compared to traditional PCBs due to the specialized materials and processes involved. Efforts are being made to optimize the manufacturing process and scale up production to reduce costs and make Glass PCBs more competitive in the market.
4. Standardization and Qualification
As Glass PCBs are a relatively new technology, there is a need for standardization and qualification procedures to ensure consistent quality and reliability. Industry associations and standards bodies are working towards developing guidelines and specifications for Glass PCBs to facilitate their widespread adoption.
Frequently Asked Questions (FAQ)
1. What is the main difference between Glass PCBs and traditional PCBs?
The main difference is the substrate material used. Glass PCBs use a thin layer of glass as the substrate, while traditional PCBs typically use materials like FR-4 (a composite of fiberglass and epoxy resin). Glass offers superior electrical insulation, dimensional stability, and thermal performance compared to FR-4.
2. Are Glass PCBs more expensive than traditional PCBs?
Currently, Glass PCBs are more expensive to manufacture compared to traditional PCBs due to the specialized materials and processes involved. However, as the technology matures and production scales up, the cost is expected to decrease, making Glass PCBs more competitive in the market.
3. Can Glass PCBs be used for flexible electronics applications?
While glass itself is not flexible, Glass PCBs can be integrated with flexible materials to create hybrid structures for flexible electronics applications. Researchers are exploring ways to combine the benefits of glass substrates with the flexibility of other materials to enable new possibilities in wearable devices and flexible sensors.
4. What are the environmental benefits of using Glass PCBs?
Glass is a recyclable and eco-friendly material, making Glass PCBs a more sustainable choice compared to traditional PCB materials. The manufacturing process for Glass PCBs also generates less waste and requires fewer harsh chemicals, reducing the environmental impact compared to conventional PCB production.
5. How do Glass PCBs compare to ceramic PCBs in terms of performance?
Glass PCBs and ceramic PCBs share some similar properties, such as excellent electrical insulation and high thermal stability. However, glass has a lower dielectric constant and loss tangent compared to most ceramics, making it more suitable for high-frequency applications. Glass is also transparent, which enables unique design possibilities and optical inspection capabilities not available with ceramic PCBs.
Comparison Table: Glass PCBs vs. Traditional FR-4 PCBs
Property | Glass PCBs | FR-4 PCBs |
---|---|---|
Dielectric Constant | 5.3 | 4.5 |
Loss Tangent (at 1 MHz) | 0.006 | 0.02 |
Thermal Conductivity | 1 W/mK | 0.3 W/mK |
CTE (ppm/°C) | 3.3 | 14-16 |
Transparency | Yes | No |
Recyclability | High | Low |
Typical Applications | High-frequency, optoelectronics, automotive, medical | General-purpose, low-cost electronics |
Conclusion
Glass PCBs represent a promising new technology that offers several advantages over traditional PCB materials. With their excellent electrical insulation, high dimensional stability, superior thermal performance, and transparency, Glass PCBs are well-suited for a wide range of applications, including high-frequency electronics, optoelectronics, automotive systems, medical devices, and aerospace/defense.
As the technology continues to develop, advanced manufacturing techniques and integration with other emerging technologies will further expand the possibilities of Glass PCBs. While there are still challenges to overcome, such as cost and standardization, the future prospects for Glass PCBs are bright, and they are poised to play an increasingly important role in the electronics industry.
PCB designers should consider Glass PCBs as a viable option for their projects, especially when high performance, reliability, and unique design requirements are critical. As the demand for advanced electronic systems grows, Glass PCBs are set to become a key enabler of innovation and progress in various industries.
No responses yet