What is FR4 Material?
FR4 (or Flame Retardant 4) is a composite material composed of woven fiberglass cloth with an epoxy resin binder that is flame resistant. FR4 glass epoxy is a popular and versatile high-pressure thermoset plastic laminate grade with good strength to weight ratios.
FR4 glass epoxy is an excellent electrical insulator with considerable mechanical strength. These attributes, along with the flame retardant properties, make FR4 the primary insulating substrate material used for most rigid printed circuit boards (PCBs).
Properties of FR4 That Make it Ideal for PCBs
FR4 has a number of favorable mechanical, electrical, and thermal properties that make it well-suited as a base material for PCBs, including:
1. High Dielectric Strength
FR4 has a dielectric strength of about 500 to 800 volts/mil (20-31 KV/mm), which is very good for an insulating material. This allows FR4 PCBs to be used in higher voltage applications.
2. Low Moisture Absorption
FR4 absorbs very little moisture compared to other plastics. Moisture absorption is detrimental to PCBs as it can degrade insulation resistance and dielectric properties. Typical moisture absorption for FR4 is 0.10-0.15%.
3. Good Thermal Performance
The glass transition temperature (Tg) of FR4 is typically between 115-125°C. This is the temperature range where the resin transitions from a glassy to a softened state. The relatively high Tg allows FR4 PCBs to maintain integrity at higher operating temperatures.
The thermal expansion of FR4 is also relatively low and closely matches that of copper, which minimizes mechanical stress between the copper traces and FR4 substrate as temperature fluctuates. Typical thermal expansion coefficients are:
Axis | Thermal Expansion Coefficient |
---|---|
X-Y | 14-16 ppm/°C |
Z | 50-70 ppm/°C |
The thermal conductivity of FR4 is about 0.25 W/m•K. While low compared to metals, it is sufficient to allow moderate heat dissipation into the PCB from components.
4. Mechanical Strength and Stiffness
The woven glass and cross-linked epoxy resin give FR4 good mechanical properties:
Property | Typical Value |
---|---|
Tensile Strength | 310-380 MPa |
Compressive Strength | 415-495 MPa |
Flexural Strength | 415-580 MPa |
Young’s Modulus | 16-22 GPa |
This strength and rigidity allow FR4 PCBs to structurally support attached components and withstand moderate impacts, bending, and other mechanical stresses. The material is hard and abrasion resistant.
5. Good Machining Properties
FR4 cuts, drills and routes cleanly without splintering. Well-defined holes and edges are essential for the precision drilling and machining required to manufacture PCBs.
6. Flame Resistant
The epoxy resin used in FR4 is designed to be self-extinguishing. FR4 will burn in the presence of a direct flame but should extinguish once the flame is removed. This is an important safety feature for electronics.
Grades and Variations of FR4
There are a number of different types and grades of FR4 that are used for PCBs, each with slightly different properties optimized for certain applications:
Standard FR4
The most common type of FR4 with standard Tg of 130-140°C. Used for most PCB applications.
High Tg FR4
FR4 with higher glass transition temperatures, typically 170-180°C. Used for higher temperature applications like automotive and aerospace electronics.
Halogen-Free FR4
Standard FR4 uses brominated fire retardants. Some halogen-free versions are available that use metallic hydroxides instead. These are used where halogen outgassing is a concern.
High-Speed/Low-Loss FR4
Specialty FR4 grades engineered to have lower dielectric loss and allow higher frequency operation for high speed digital and RF applications. Examples include Isola’s FR408 and Neltec’s N4000-13.
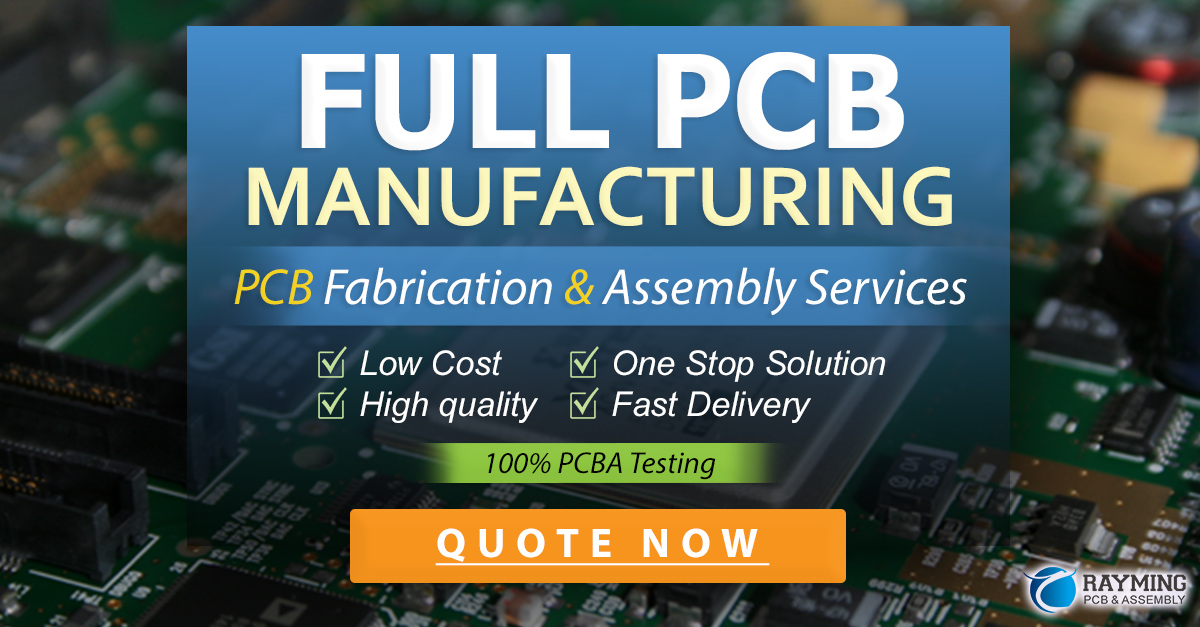
FR4 PCB Applications
Thanks to its excellent all-around properties and low cost, FR4 is used for the vast majority (>90%) of rigid PCBs, making it by far the most common base material. FR4 PCBs are used in virtually every type of electronic device, including:
- Consumer electronics
- Computers and peripherals
- Telecommunications equipment
- Industrial controls
- Medical devices
- Automotive electronics
- Aerospace systems
- LED lighting
FR4’s combination of electrical insulation, mechanical strength, thermal stability, and flame resistance make it an excellent substrate for mounting and interconnecting electronic components in a wide range of operating environments and conditions.
Alternatives to FR4 PCBs
While FR4 is used for the vast majority of PCBs, there are some alternative base materials used for specialized applications, including:
Metal Core PCBs
For high power applications that generate significant heat, the FR4 can be bonded to a metal baseplate, usually aluminum. The metal helps dissipate heat away from the components.
High Frequency Laminates
For microwave frequencies and other high frequency RF applications, special low-loss laminates like Rogers 4000 series or Teflon materials may be used instead of FR4.
Flexible PCBs
For flexible circuits, plastics like polyimide are used instead of rigid FR4. The copper traces can be bonded between two layers of polyimide or to one side.
Ceramic PCBs
In some high reliability or high temperature applications, ceramic substrates like alumina may be used instead of FR4. Ceramic PCBs are very expensive.
However, for most standard PCB applications across consumer, commercial, industrial and other sectors, FR4 provides the best all-around performance and value. That’s why FR4 continues to be used for the vast majority of rigid PCBs.
FAQ
1. What does FR4 stand for?
FR4 stands for “Flame Retardant 4”, indicating a woven glass epoxy laminate with self-extinguishing flammability characteristics.
2. Is FR4 waterproof?
FR4 has low moisture absorption but is not fully waterproof. Exposing FR4 PCBs to liquid water for extended periods is not recommended. Conformal coatings can be applied to PCBs to improve moisture resistance if needed.
3. What is the difference between G10 and FR4?
G10 is a woven glass epoxy laminate very similar to FR4 but without the flame retardant additives. FR4 is essentially the flame resistant version of G10. The two materials have very similar mechanical and electrical properties but G10 will burn more readily.
4. Can I cut or drill FR4 myself?
FR4 is a relatively hard material and requires carbide tools to machine effectively. It can be cut, drilled and routed but proper tools and precautions are necessary, especially to avoid inhaling the dust. PCB fabrication houses use specialized high-speed equipment to machine FR4.
5. How much does FR4 PCB cost?
The cost of FR4 PCBs depends on many factors including size, number of layers, complexity, quantity, and additional manufacturing options. In general, simple 2-layer FR4 PCBs can cost under $10 each in small quantities, while large, complex multilayer boards can cost hundreds of dollars each. Large volumes drastically reduce the per-unit cost.
No responses yet