Introduction to FR4-TG PCB material
FR4-TG is a type of flame-retardant (FR) printed circuit board (PCB) material that has a high glass transition temperature (Tg). It is widely used in the electronics industry for manufacturing high-quality, reliable PCBs that can withstand harsh operating conditions.
What is FR4?
FR4 is a common type of PCB material that is made from a composite of woven fiberglass cloth and an epoxy resin binder. The “FR” in FR4 stands for “Flame Retardant,” indicating that the material has been treated with chemicals to reduce its flammability and improve its resistance to burning.
What is Glass Transition Temperature (Tg)?
Glass transition temperature (Tg) is a critical property of PCB Materials that refers to the temperature at which the material transitions from a hard, glassy state to a soft, rubbery state. At temperatures above the Tg, the material becomes more flexible and less rigid, which can lead to warping, delamination, and other defects in the PCB.
Advantages of High Tg in FR4-TG
FR4-TG has a higher glass transition temperature compared to standard FR4 material. This means that FR4-TG can maintain its structural integrity and electrical properties at higher operating temperatures, making it ideal for use in applications that generate a lot of heat or are exposed to high ambient temperatures.
Properties of FR4-TG PCB Material
FR4-TG has several key properties that make it an excellent choice for high-performance PCB applications. These properties include:
1. High Glass Transition Temperature
As mentioned earlier, FR4-TG has a high glass transition temperature, typically in the range of 170°C to 180°C. This is significantly higher than the Tg of standard FR4 material, which is around 130°C to 140°C.
PCB Material | Typical Tg Range |
---|---|
Standard FR4 | 130°C to 140°C |
FR4-TG | 170°C to 180°C |
2. Excellent Thermal Stability
Due to its high Tg, FR4-TG exhibits excellent thermal stability over a wide temperature range. This means that the material can maintain its dimensions and electrical properties even when subjected to high temperatures for extended periods.
3. Good Mechanical Strength
FR4-TG has good mechanical strength and stiffness, which helps to prevent warping and other defects in the PCB. This is particularly important for applications that require high reliability and long-term stability.
4. Low Thermal Expansion
FR4-TG has a low coefficient of thermal expansion (CTE), which means that it expands and contracts very little with changes in temperature. This helps to reduce stress on the PCB and its components, improving overall reliability.
PCB Material | Typical CTE (ppm/°C) |
---|---|
Standard FR4 | 14 to 16 |
FR4-TG | 12 to 14 |
5. Excellent Electrical Properties
FR4-TG has excellent electrical properties, including high insulation resistance, low Dielectric Constant, and low loss tangent. These properties make FR4-TG well-suited for high-frequency and high-speed applications.
Electrical Property | Typical Value |
---|---|
Dielectric Constant | 4.5 to 4.7 |
Loss Tangent | 0.02 to 0.03 |
Insulation Resistance | > 10^12 ohms |
Applications of FR4-TG PCB Material
FR4-TG is widely used in a variety of high-performance PCB applications, including:
1. Automotive Electronics
Automotive electronics are subjected to harsh operating conditions, including high temperatures, vibrations, and moisture. FR4-TG’s high Tg and excellent thermal stability make it an ideal choice for automotive PCBs, such as engine control units (ECUs), infotainment systems, and advanced driver assistance systems (ADAS).
2. Industrial Electronics
Industrial electronics, such as factory automation systems, power electronics, and process control equipment, often operate in challenging environments with high temperatures and heavy loads. FR4-TG’s robustness and reliability make it well-suited for these applications.
3. Aerospace and Defense
Aerospace and defense applications demand the highest levels of performance and reliability from their electronic components. FR4-TG’s high Tg, low CTE, and excellent electrical properties make it a popular choice for avionics, radar systems, and other mission-critical applications.
4. Medical Devices
Medical devices, such as imaging equipment, patient monitors, and surgical instruments, require PCBs that can withstand repeated sterilization cycles and operate reliably over long periods. FR4-TG’s thermal stability and mechanical strength make it an excellent choice for these applications.
5. High-Frequency and High-Speed Applications
FR4-TG’s low dielectric constant and low loss tangent make it well-suited for high-frequency and high-speed applications, such as 5G wireless communication systems, radar, and high-speed digital interfaces.
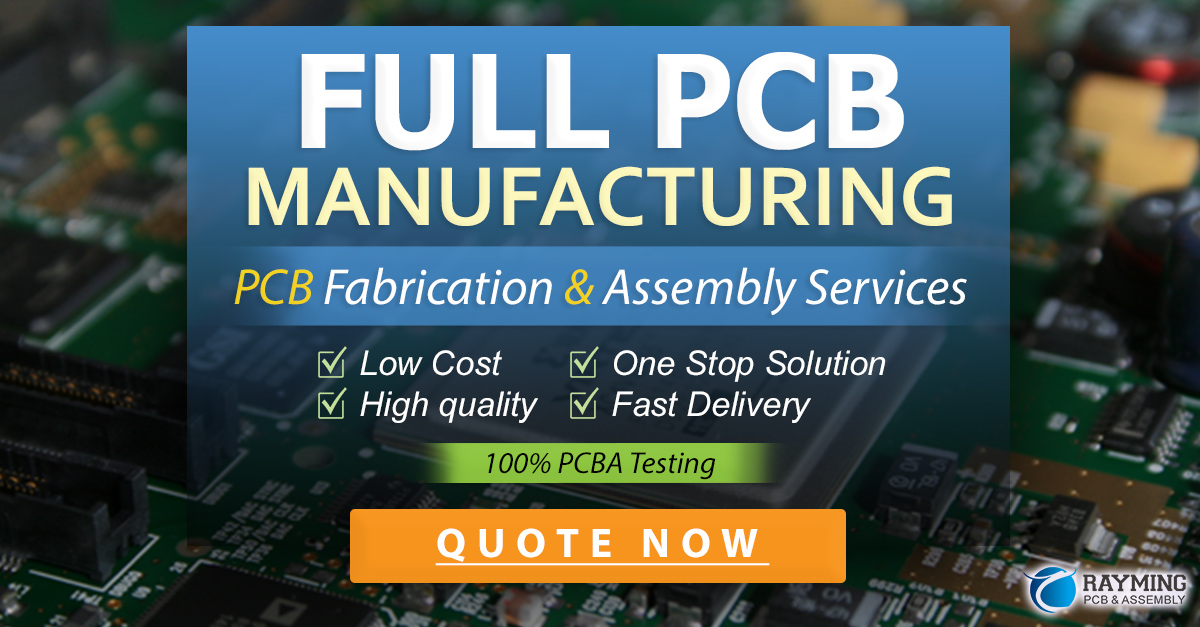
Manufacturing Considerations for FR4-TG PCBs
When designing and manufacturing PCBs using FR4-TG material, there are several key considerations to keep in mind:
1. Lamination Process
The lamination process for FR4-TG PCBs typically requires higher temperatures and pressures compared to standard FR4 material. This is necessary to ensure proper bonding between the layers and to achieve the desired mechanical and electrical properties.
2. Drill Parameters
Due to its higher Tg and increased hardness, FR4-TG may require different drill parameters compared to standard FR4. This can include adjusted feed rates, speeds, and drill bit geometries to ensure clean, accurate holes and minimize tool wear.
3. Resin Content
The resin content in FR4-TG material can affect its performance and processing characteristics. Higher resin content can improve the material’s thermal stability and mechanical strength, but may also increase its brittleness and make it more difficult to drill and route.
Resin Content | Typical Range |
---|---|
Standard FR4 | 35% to 45% |
FR4-TG | 45% to 55% |
4. Controlled Impedance
When designing FR4-TG PCBs for high-frequency or high-speed applications, it is important to consider controlled impedance requirements. This involves carefully selecting the dielectric thickness, trace widths, and spacing to achieve the desired impedance values and minimize signal integrity issues.
5. Thermal Management
Although FR4-TG has excellent thermal stability, it is still important to consider thermal management strategies when designing PCBs for high-temperature applications. This can include using thermal vias, heatsinks, or other cooling techniques to dissipate heat and prevent overheating of components.
FAQ
1. What does the “TG” in FR4-TG stand for?
“TG” stands for “glass transition temperature” (Tg), which refers to the temperature at which the PCB material transitions from a hard, glassy state to a soft, rubbery state.
2. How does FR4-TG differ from standard FR4 material?
FR4-TG has a higher glass transition temperature (Tg) compared to standard FR4, typically in the range of 170°C to 180°C versus 130°C to 140°C for standard FR4. This higher Tg provides improved thermal stability and mechanical strength.
3. What are some common applications for FR4-TG PCBs?
FR4-TG PCBs are commonly used in automotive electronics, industrial electronics, aerospace and defense systems, medical devices, and high-frequency or high-speed applications that require high reliability and performance.
4. Are there any special manufacturing considerations for FR4-TG PCBs?
Yes, FR4-TG PCBs may require higher lamination temperatures and pressures, adjusted drill parameters, and careful control of resin content compared to standard FR4 material. Designers should also consider controlled impedance and thermal management strategies when working with FR4-TG.
5. Can FR4-TG be used for all PCB applications?
While FR4-TG offers superior performance in many demanding applications, it may not be necessary or cost-effective for all PCB designs. Standard FR4 material is still widely used and suitable for many general-purpose applications. The choice between FR4-TG and standard FR4 depends on the specific requirements and operating conditions of the application.
Conclusion
FR4-TG is a high-performance PCB material that offers several key advantages over standard FR4, including a higher glass transition temperature, improved thermal stability, and excellent mechanical and electrical properties. These characteristics make FR4-TG an ideal choice for demanding applications in industries such as automotive, industrial, aerospace, medical, and high-frequency electronics.
When designing and manufacturing PCBs using FR4-TG material, it is important to consider factors such as lamination process, drill parameters, resin content, controlled impedance, and thermal management to ensure optimal performance and reliability.
As the electronics industry continues to push the boundaries of performance and functionality, FR4-TG will likely play an increasingly important role in enabling the next generation of high-reliability, high-speed, and high-temperature PCB applications.
No responses yet