What is a Flexible PCB?
A flexible PCB, also known as a flex circuit or FPC, is a printed circuit board made from flexible materials such as polyimide or polyester. Unlike rigid PCBs, FPCs can bend and flex, allowing them to conform to the shape of the device they are used in. This makes them ideal for applications where space is limited, or where the circuitry needs to move or flex during operation.
FPCs consist of a thin layer of conductive copper traces bonded to a flexible substrate material. They can be single-sided, double-sided, or multi-layered, depending on the complexity of the circuit design. FPCs also often incorporate additional features such as stiffeners, shields, and connectors to enhance their functionality.
Advantages of Flexible PCBs
Flexible PCBs offer several advantages over traditional rigid PCBs:
-
Flexibility: FPCs can bend and flex, allowing them to conform to the shape of the device and fit into tight spaces.
-
Lightweight: FPCs are much lighter than rigid PCBs, making them ideal for portable and wearable devices.
-
Durability: FPCs are more resistant to vibration and shock than rigid PCBs, making them more reliable in harsh environments.
-
Space-saving: FPCs can be folded or rolled up, allowing for more compact device designs.
-
Cost-effective: FPCs can reduce assembly costs by eliminating the need for connectors and wires between boards.
Flexible PCB Manufacturing Process
The manufacturing process for Fabricating FPCs involves several steps, each of which requires specialized equipment and expertise. The main steps in the FPC manufacturing process are:
- Circuit design
- Material selection
- Substrate preparation
- Copper foil lamination
- Circuit patterning
- Etching
- Coverlay application
- Surface finishing
- Cutting and forming
- Inspection and testing
Let’s take a closer look at each step in the process.
Circuit Design
The first step in fabricating an FPC is to design the circuit. This involves creating a schematic diagram of the circuit and then laying out the physical design using CAD software. The circuit design must take into account the specific requirements of the application, such as the number of layers, the required flexibility, and the anticipated environmental conditions.
Material Selection
The next step is to select the appropriate materials for the FPC. The most common substrate materials used in FPCs are polyimide and polyester. Polyimide is more expensive but offers better thermal stability and mechanical properties than polyester. The choice of substrate material depends on the specific requirements of the application.
The conductive traces in FPCs are typically made from copper foil. The thickness of the copper foil can vary depending on the current-carrying requirements of the circuit. Thicker copper foil is used for high-current applications, while thinner foil is used for lower-current applications.
Substrate Preparation
Once the materials have been selected, the substrate must be prepared for lamination. This involves cleaning the substrate to remove any contaminants and then applying an adhesive layer to bond the copper foil to the substrate.
Copper Foil Lamination
The next step is to laminate the copper foil onto the prepared substrate. This is typically done using a hot press, which applies heat and pressure to bond the copper foil to the substrate. The lamination process must be carefully controlled to ensure good adhesion and to prevent air bubbles or voids from forming between the layers.
Circuit Patterning
After lamination, the circuit pattern is transferred onto the copper foil using a photolithography process. This involves coating the copper foil with a light-sensitive photoresist material and then exposing it to UV light through a photomask containing the circuit pattern. The exposed areas of the photoresist are then developed, leaving the circuit pattern exposed on the copper foil.
Etching
The next step is to etch away the unwanted copper foil, leaving only the circuit pattern on the substrate. This is typically done using a chemical etching process, where the FPC is immersed in an etchant solution that dissolves the exposed copper. The etching process must be carefully controlled to ensure that the circuit pattern is not over-etched or under-etched.
Coverlay Application
After etching, a coverlay material is applied over the circuit pattern to protect it from damage and provide electrical insulation. The coverlay is typically a thin layer of polyimide or polyester material that is laminated onto the FPC using a hot press.
Surface Finishing
The exposed copper traces on the FPC are then finished to protect them from oxidation and improve their solderability. Common surface finishes used in FPCs include:
- ENIG (Electroless Nickel Immersion Gold)
- OSP (Organic Solderability Preservative)
- Immersion Tin
- Immersion Silver
The choice of surface finish depends on the specific requirements of the application, such as the expected environmental conditions and the soldering process used.
Cutting and Forming
Once the FPC has been fabricated, it must be cut and formed into its final shape. This is typically done using a CNC cutting machine or a laser cutting system. The FPC may also be formed into a specific shape using a forming die or a thermoforming process.
Inspection and Testing
The final step in the FPC manufacturing process is inspection and testing. This involves visually inspecting the FPC for defects such as shorts, opens, or misalignments, and then testing it for electrical functionality using automated test equipment (ATE). The FPC must pass all quality control checks before it can be shipped to the customer.
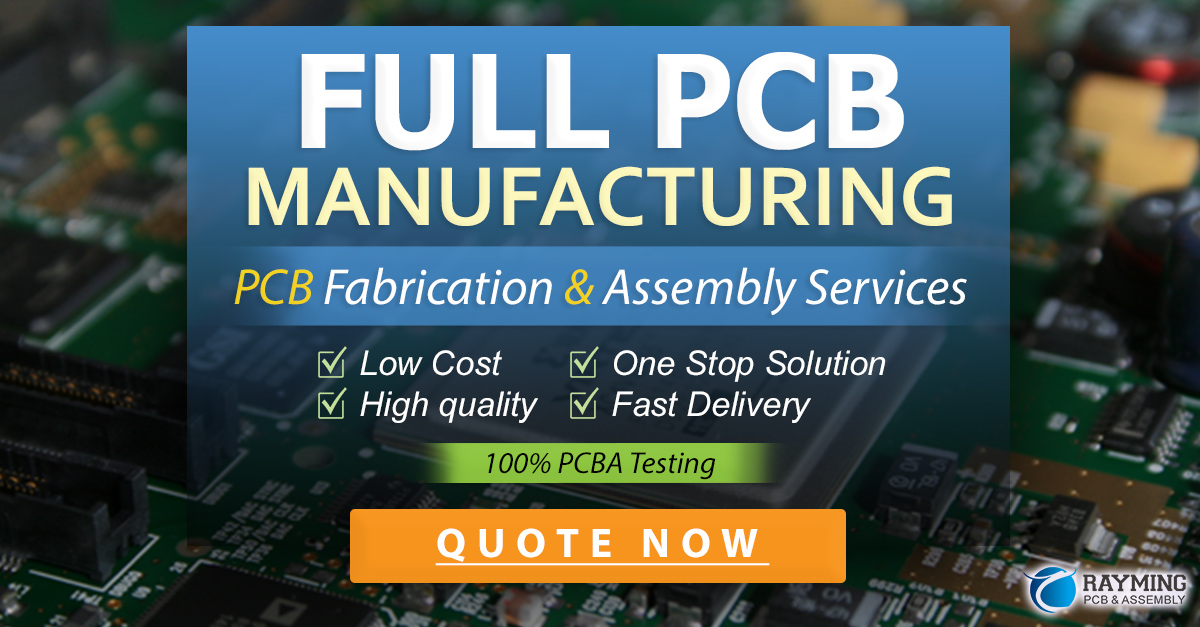
Challenges in Flexible PCB Manufacturing
While FPCs offer many advantages over rigid PCBs, they also present some unique manufacturing challenges. Some of the main challenges in FPC manufacturing include:
-
Material handling: FPCs are made from thin, flexible materials that can be easily damaged during handling. Special care must be taken to avoid stretching, tearing, or creasing the material during the manufacturing process.
-
Dimensional stability: FPCs can be prone to dimensional changes due to temperature and humidity variations. This can cause issues with circuit alignment and registration during the manufacturing process.
-
Adhesion: Ensuring good adhesion between the copper foil and the substrate material can be challenging, especially for multi-layer FPCs. Poor adhesion can lead to delamination and circuit failures.
-
Impedance control: Controlling the impedance of the circuit traces can be more difficult in FPCs than in rigid PCBs, due to the flexible nature of the substrate material.
-
Assembly: Assembling components onto an FPC can be more challenging than with a rigid PCB, due to the flexibility of the substrate and the smaller size of the components used.
Despite these challenges, advances in materials, equipment, and processes have made it possible to manufacture high-quality FPCs for a wide range of applications.
Applications of Flexible PCBs
Flexible PCBs are used in a wide range of applications where flexibility, lightweight, and compact size are important. Some common applications of FPCs include:
-
Consumer electronics: FPCs are commonly used in smartphones, tablets, laptops, and wearable devices, where they enable compact and lightweight designs.
-
Medical devices: FPCs are used in medical devices such as hearing aids, pacemakers, and insulin pumps, where they provide reliable and flexible connectivity.
-
Automotive electronics: FPCs are used in automotive applications such as dashboard displays, camera modules, and sensors, where they offer improved reliability and space savings compared to traditional wiring harnesses.
-
Aerospace and defense: FPCs are used in aerospace and defense applications such as avionics, satellites, and military equipment, where they provide lightweight and reliable connectivity in harsh environments.
-
Industrial automation: FPCs are used in industrial automation applications such as robotics, motion control, and machine vision, where they offer improved flexibility and reliability compared to rigid PCBs.
FAQ
What is the difference between a flexible PCB and a rigid PCB?
A flexible PCB is made from flexible materials such as polyimide or polyester, while a rigid PCB is made from a rigid material such as FR-4. FPCs can bend and flex, while rigid PCBs cannot. FPCs are typically thinner and lighter than rigid PCBs, and can be used in applications where flexibility and compact size are important.
What are the advantages of using a flexible PCB?
The main advantages of using a flexible PCB are:
- Flexibility: FPCs can bend and flex, allowing them to conform to the shape of the device and fit into tight spaces.
- Lightweight: FPCs are much lighter than rigid PCBs, making them ideal for portable and wearable devices.
- Durability: FPCs are more resistant to vibration and shock than rigid PCBs, making them more reliable in harsh environments.
- Space-saving: FPCs can be folded or rolled up, allowing for more compact device designs.
- Cost-effective: FPCs can reduce assembly costs by eliminating the need for connectors and wires between boards.
What materials are used to make flexible PCBs?
The most common substrate materials used in FPCs are polyimide and polyester. Polyimide is more expensive but offers better thermal stability and mechanical properties than polyester. The conductive traces in FPCs are typically made from copper foil, with the thickness of the foil varying depending on the current-carrying requirements of the circuit.
What are the main steps in the flexible PCB manufacturing process?
The main steps in the FPC manufacturing process are:
- Circuit design
- Material selection
- Substrate preparation
- Copper foil lamination
- Circuit patterning
- Etching
- Coverlay application
- Surface finishing
- Cutting and forming
- Inspection and testing
Each step requires specialized equipment and expertise to ensure a high-quality finished product.
What are some common applications of flexible PCBs?
Some common applications of FPCs include:
- Consumer electronics: smartphones, tablets, laptops, and wearable devices
- Medical devices: hearing aids, pacemakers, and insulin pumps
- Automotive electronics: dashboard displays, camera modules, and sensors
- Aerospace and defense: avionics, satellites, and military equipment
- Industrial automation: robotics, motion control, and machine vision
FPCs offer improved flexibility, reliability, and space savings compared to traditional rigid PCBs in these applications.
No responses yet