What is a Flex PCB?
A Flex PCB, also known as a flexible circuit board, is a type of printed circuit board that can bend, fold, and twist without damaging the electrical components or connections. Unlike traditional rigid PCBs, Flex PCBs are made using flexible substrate materials, such as polyimide or polyester, which allow for greater design freedom and improved reliability in applications that require flexibility.
Flex PCBs can be categorized based on the number of layers they contain, ranging from single-layer to multi-layer designs with up to 10 layers. The number of layers in a Flex PCB directly impacts its complexity, functionality, and cost.
Advantages of Flex PCBs
Flex PCBs offer several advantages over traditional rigid PCBs, making them an attractive choice for a wide range of applications. Some of the key benefits of Flex PCBs include:
-
Flexibility and Durability: Flex PCBs can withstand repeated bending and flexing without compromising the integrity of the electrical connections, making them ideal for applications that require movement or are subject to vibrations and shock.
-
Lightweight and Compact: By eliminating the need for bulky connectors and wiring, Flex PCBs enable the design of lightweight and compact electronic devices, which is particularly important for portable and wearable applications.
-
Improved Signal Integrity: Flex PCBs offer better signal integrity compared to traditional wire harnesses, as they minimize electromagnetic interference (EMI) and reduce signal loss.
-
Reduced Assembly Costs: Flex PCBs can simplify the assembly process by reducing the number of connectors and wiring required, leading to lower assembly costs and shorter production times.
-
Design Flexibility: Flex PCBs allow for greater design freedom, enabling engineers to create complex, three-dimensional layouts that would be impossible with rigid PCBs.
Flex PCB Manufacturing Process
The manufacturing process for Flex PCBs shares many similarities with that of rigid PCBs, but with some key differences to accommodate the flexible substrate materials. The main steps in the Flex PCB manufacturing process are as follows:
-
Designing the Flex PCB: The first step in the manufacturing process is to design the Flex PCB using specialized CAD software. The design must take into account the specific requirements of the application, such as the number of layers, the level of flexibility required, and the placement of components.
-
Creating the Artwork: Once the design is complete, the artwork for each layer of the Flex PCB is created. The artwork is used to generate the photomasks that will be used in the subsequent steps of the manufacturing process.
-
Laminating the Flexible Substrate: The flexible substrate material, typically polyimide or polyester, is laminated with a thin layer of copper on one or both sides, depending on the design requirements.
-
Applying the Photoresist: A photoresist layer is applied to the copper-clad substrate and then exposed to UV light through the photomasks created in step 2. This process transfers the artwork onto the photoresist layer.
-
Developing and Etching: The exposed photoresist is developed, and the unwanted copper is etched away, leaving behind the desired circuit pattern.
-
Applying the Coverlay: A coverlay, which is a protective layer of insulating material, is applied to the surface of the Flex PCB to protect the circuitry and provide additional insulation.
-
Cutting and Drilling: The Flex PCB is cut to its final shape, and any necessary holes or vias are drilled.
-
Surface Finishing: The exposed copper areas of the Flex PCB are coated with a surface finish, such as ENIG (Electroless Nickel Immersion Gold) or OSP (Organic Solderability Preservative), to protect the copper from oxidation and improve solderability.
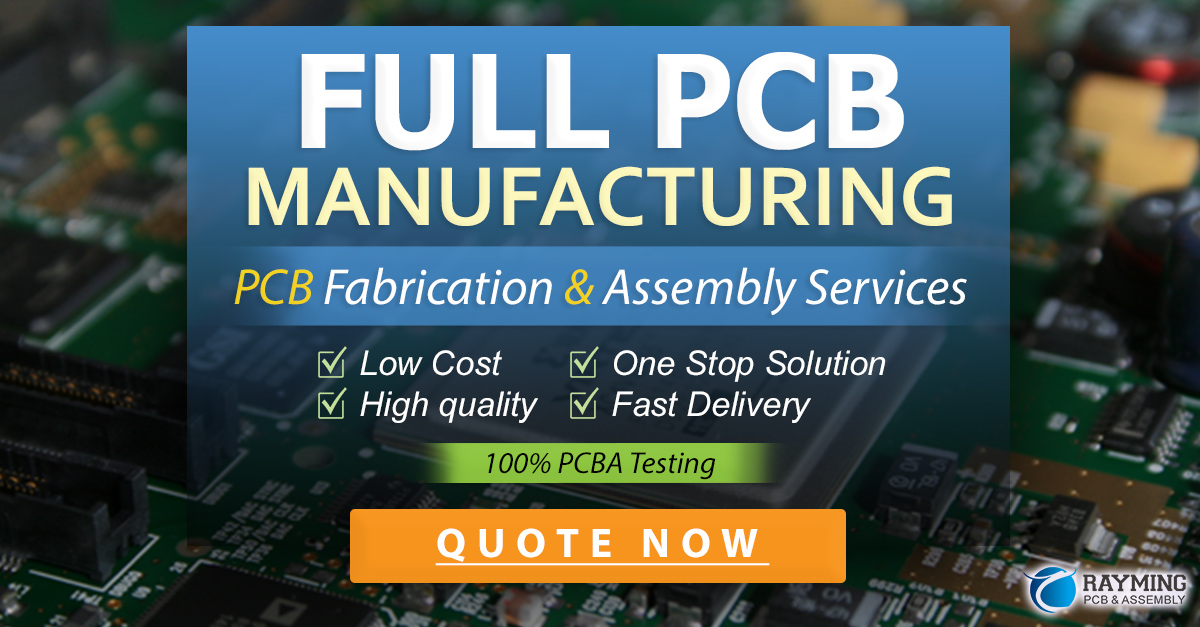
Flex PCB Assembly
Once the Flex PCB has been manufactured, it must be assembled with the required electronic components to create a functional circuit. The assembly process for Flex PCBs is similar to that of rigid PCBs, but with some additional considerations to account for the flexible nature of the substrate.
The main steps in the Flex PCB assembly process are as follows:
-
Solder Paste Application: Solder paste is applied to the pads on the Flex PCB using a stencil or syringe. The solder paste contains a mixture of tiny solder particles and flux, which helps to clean and prepare the surfaces for soldering.
-
Component Placement: The electronic components are placed onto the Flex PCB using a pick-and-place machine or by hand, depending on the complexity of the design and the size of the components.
-
Reflow Soldering: The Flex PCB with the placed components is passed through a reflow oven, which heats the solder paste to its melting point, allowing it to flow and form a strong electrical and mechanical connection between the components and the PCB.
-
Inspection and Testing: After the soldering process, the assembled Flex PCB undergoes a visual inspection and electrical testing to ensure that all connections are properly formed and that the circuit functions as intended.
-
Conformal Coating (Optional): In some cases, a conformal coating may be applied to the assembled Flex PCB to provide additional protection against moisture, dust, and other environmental factors.
Flex PCB Layer Stack-up
Flex PCBs can be manufactured with various layer stack-ups, ranging from single-layer to multi-layer designs with up to 10 layers. The choice of layer stack-up depends on the specific requirements of the application, such as signal integrity, power distribution, and overall complexity.
Here are some common Flex PCB layer stack-ups:
-
Single-Layer Flex PCB: A single-layer Flex PCB consists of a flexible substrate with a single layer of copper on one side. This type of Flex PCB is the simplest and most cost-effective option, suitable for applications with low complexity and minimal power requirements.
-
Double-Layer Flex PCB: A double-layer Flex PCB has two layers of copper, one on each side of the flexible substrate. This configuration allows for more complex circuitry and better power distribution compared to single-layer designs.
-
Multi-Layer Flex PCB: Multi-layer Flex PCBs can have anywhere from 3 to 10 layers of copper, with insulating layers of flexible substrate material in between. These designs offer the highest level of complexity and functionality, enabling the integration of advanced features such as controlled impedance, shielding, and high-speed signaling.
Here’s an example of a 4-layer Flex PCB stack-up:
Layer | Material | Thickness (mm) |
---|---|---|
Top Coverlay | Polyimide | 0.05 |
Top Copper | Copper | 0.018 |
Core Substrate | Polyimide | 0.05 |
Inner Copper 1 | Copper | 0.018 |
Core Substrate | Polyimide | 0.05 |
Inner Copper 2 | Copper | 0.018 |
Core Substrate | Polyimide | 0.05 |
Bottom Copper | Copper | 0.018 |
Bottom Coverlay | Polyimide | 0.05 |
Applications of Flex PCBs
Flex PCBs find applications in a wide range of industries and products, thanks to their flexibility, durability, and compact size. Some common applications of Flex PCBs include:
-
Consumer Electronics: Flex PCBs are widely used in smartphones, tablets, laptops, and wearable devices, where their flexibility and compact size enable the design of slim and lightweight products.
-
Medical Devices: Flex PCBs are essential components in many medical devices, such as hearing aids, pacemakers, and implantable sensors, where their reliability and flexibility are critical for patient safety and comfort.
-
Automotive Electronics: Flex PCBs are increasingly used in automotive applications, such as dashboard displays, lighting systems, and sensors, where their ability to withstand vibrations and harsh environments is highly valued.
-
Aerospace and Defense: Flex PCBs are used in various aerospace and defense applications, such as avionics systems, satellite communications, and military equipment, where their lightweight and compact size help to reduce overall system weight and size.
-
Industrial Automation: Flex PCBs are used in industrial automation systems, such as robotics, motion control, and data acquisition, where their flexibility and durability enable reliable operation in demanding environments.
Frequently Asked Questions (FAQ)
- What is the maximum number of layers that can be achieved in a Flex PCB?
Flex PCBs can be manufactured with up to 10 layers, although the most common designs have between 1 and 4 layers. The maximum number of layers depends on the specific requirements of the application and the capabilities of the PCB manufacturer.
- Can Flex PCBs be used in high-temperature environments?
Yes, Flex PCBs can be designed to withstand high temperatures by using specialized substrate materials and components rated for high-temperature operation. However, the specific temperature range will depend on the materials used and the design of the Flex PCB.
- How do Flex PCBs compare to rigid PCBs in terms of cost?
Flex PCBs are generally more expensive than rigid PCBs due to the specialized materials and manufacturing processes required. However, the cost difference can be offset by the benefits of Flex PCBs, such as reduced assembly costs, improved reliability, and greater design flexibility.
- Can Flex PCBs be used in applications that require high-speed signaling?
Yes, Flex PCBs can be designed to support high-speed signaling by using controlled impedance techniques and specialized materials. However, the specific design requirements will depend on the signal speeds and frequencies involved.
- What are the main challenges in Flex PCB assembly?
The main challenges in Flex PCB assembly include handling the flexible substrate material, ensuring proper alignment of components, and managing the thermal expansion and contraction of the materials during the soldering process. Specialized equipment and techniques may be required to overcome these challenges and ensure reliable assembly.
Conclusion
Flex PCBs have become an essential component in the design and manufacture of modern electronic devices, offering unparalleled flexibility, durability, and compact size. With the ability to accommodate anywhere from 1 to 10 layers, Flex PCBs can be tailored to meet the specific requirements of a wide range of applications, from consumer electronics to medical devices and aerospace systems.
As the demand for smaller, lighter, and more reliable electronic devices continues to grow, the importance of Flex PCBs in the electronics industry is set to increase. By understanding the manufacturing and assembly processes, as well as the key considerations for designing Flex PCBs, engineers and product designers can unlock the full potential of this versatile technology and create innovative solutions for the challenges of today and tomorrow.
No responses yet