Introduction to Flex PCBs
Flexible printed circuit boards, or flex PCBs, have revolutionized the electronics industry with their versatility, durability, and compact design. These innovative circuit boards are made from flexible materials, allowing them to bend, twist, and fold without compromising their electrical functionality. Flex PCBs have become increasingly popular in various applications, from consumer electronics to medical devices, aerospace, and automotive industries.
What are Flex PCBs?
Flex PCBs are a type of printed circuit board that uses flexible base materials, such as polyimide or polyester, instead of the traditional rigid FR4 substrate. The conductive traces are printed on these flexible substrates using advanced manufacturing techniques, resulting in a circuit board that can bend and flex without breaking or losing its electrical properties.
Advantages of Flex PCBs
Flex PCBs offer several advantages over traditional rigid PCBs:
- Flexibility: The most obvious advantage of flex PCBs is their ability to bend and flex, allowing for more creative and space-saving designs.
- Durability: Flex PCBs are more resistant to vibration, shock, and extreme temperatures compared to rigid PCBs.
- Lightweight: The flexible materials used in flex PCBs are generally lighter than the rigid FR4 substrate, making them ideal for weight-sensitive applications.
- Compact design: Flex PCBs can be folded and shaped to fit into tight spaces, reducing the overall size of electronic devices.
- Reduced assembly costs: By replacing multiple rigid PCBs with a single flex PCB, assembly costs can be significantly reduced.
Types of Flex PCBs
There are several types of flex PCBs, each with its own unique characteristics and applications.
Single-Sided Flex PCBs
Single-sided flex PCBs have conductive traces printed on only one side of the flexible substrate. They are the simplest and most cost-effective type of flex PCB, suitable for applications with low complexity and minimal electrical requirements.
Double-Sided Flex PCBs
Double-sided flex PCBs have conductive traces printed on both sides of the flexible substrate, allowing for more complex circuits and higher component density. The two sides are connected using through-hole vias, similar to rigid PCBs.
Multi-Layer Flex PCBs
Multi-layer flex PCBs consist of three or more layers of flexible substrate with conductive traces printed on each layer. These layers are laminated together using adhesive materials, with vias connecting the different layers. Multi-layer flex PCBs offer the highest level of complexity and density, suitable for advanced applications that require high-speed signal transmission and dense component placement.
Rigid-Flex PCBs
Rigid-flex PCBs combine the benefits of both rigid and flexible PCBs by incorporating rigid sections and flexible sections in a single circuit board. The rigid sections provide structural support and can accommodate larger components, while the flexible sections allow for bending and folding. Rigid-flex PCBs are commonly used in applications that require a mix of stability and flexibility, such as aerospace and medical devices.
Flex PCB Manufacturing Process
The manufacturing process for flex PCBs is similar to that of rigid PCBs, with a few key differences to accommodate the flexible materials.
Material Selection
The first step in manufacturing flex PCBs is selecting the appropriate flexible substrate material. The most common materials used are polyimide (PI) and polyester (PET). PI is known for its high heat resistance and durability, while PET is a more cost-effective option for less demanding applications.
Circuit Design and Artwork Creation
The circuit design for flex PCBs must take into account the unique mechanical and electrical properties of the flexible substrate. The artwork, which includes the conductive traces and component placement, is created using specialized CAD software.
Printing and Etching
The artwork is then printed onto the flexible substrate using advanced printing techniques, such as screen printing or photolithography. The unwanted copper is etched away, leaving only the desired conductive traces.
Lamination and Drilling
For multi-layer flex PCBs, the individual layers are laminated together using adhesive materials and heat and pressure. Through-holes and vias are then drilled to connect the different layers.
Component Assembly and Testing
Finally, the components are assembled onto the flex PCB using Surface Mount Technology (SMT) or through-hole mounting. The assembLED PCB undergoes rigorous testing to ensure its functionality and reliability.
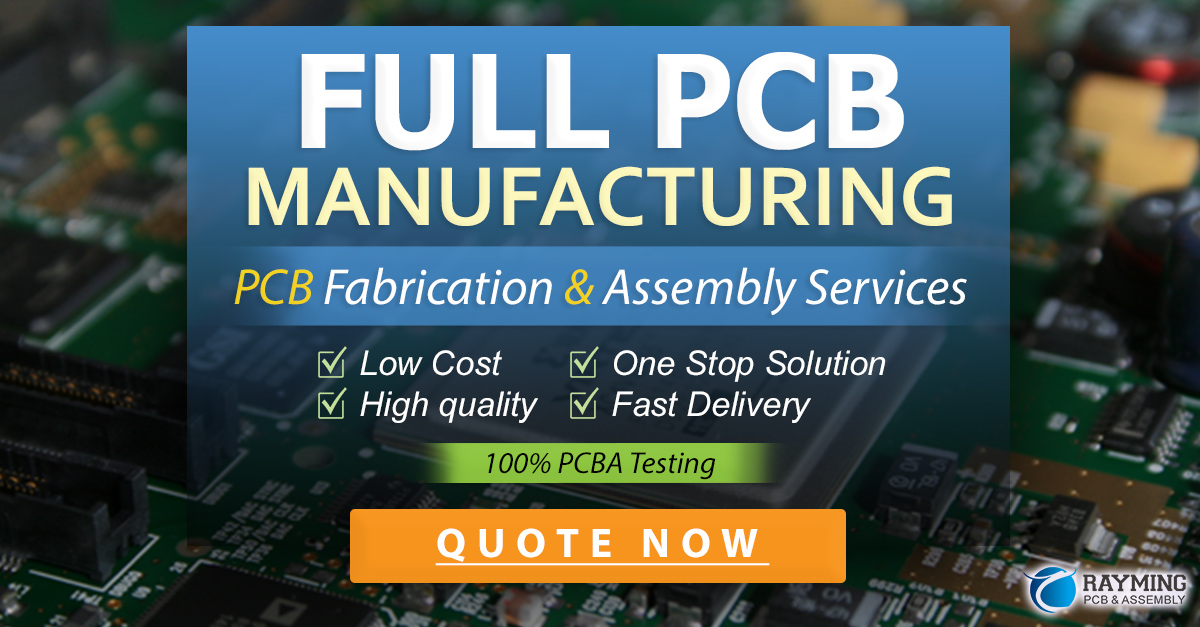
Applications of Flex PCBs
Flex PCBs have found applications in a wide range of industries due to their unique properties and benefits.
Consumer Electronics
Flex PCBs are widely used in consumer electronics, such as smartphones, tablets, and wearables. They allow for compact and lightweight designs, enabling manufacturers to create sleek and portable devices.
Medical Devices
The medical industry has embraced flex PCBs for their reliability, durability, and ability to fit into small, complex devices. Flex PCBs are used in implantable devices, such as pacemakers and hearing aids, as well as in diagnostic equipment and surgical instruments.
Aerospace and Defense
Flex PCBs are essential in the aerospace and defense industries, where weight reduction and space savings are critical. They are used in satellites, aircraft, and military equipment, offering high reliability and resistance to harsh environments.
Automotive
The automotive industry has increasingly adopted flex PCBs for their ability to withstand vibration, extreme temperatures, and harsh conditions. Flex PCBs are used in various automotive applications, such as dashboard electronics, sensor systems, and entertainment systems.
Industrial Equipment
Flex PCBs are used in industrial equipment, such as robotics, automation systems, and control panels. Their flexibility allows for creative designs and improved functionality in complex machinery.
Designing for Flex PCBs
Designing for flex PCBs requires a different approach compared to designing for rigid PCBs. Here are some key considerations:
Bend Radius
The bend radius is the minimum radius at which a flex PCB can be bent without causing damage or affecting its performance. Designers must ensure that the bend radius is within the limits specified by the manufacturer and that the components and traces are placed accordingly.
Strain Relief
Strain relief is essential in flex PCB design to prevent damage caused by repeated bending or flexing. This can be achieved by using stiffeners, such as polyimide or FR4, in areas where the PCB is likely to experience stress.
Trace Width and Spacing
The trace width and spacing on flex PCBs must be carefully designed to ensure signal integrity and prevent short circuits. Designers must also consider the effect of bending on the traces and adjust the design accordingly.
Component Placement
Component placement on flex PCBs must take into account the flexibility of the substrate and the potential for stress on the components during bending. Designers should place components in areas with minimal flexing and use appropriate mounting techniques, such as adhesives or stiffeners.
Testing and Quality Control
Ensuring the reliability and functionality of flex PCBs requires rigorous testing and quality control measures.
Visual Inspection
Visual inspection is the first step in quality control, where the PCB is examined for any obvious defects, such as scratches, dents, or discoloration.
Continuity and Isolation Testing
Continuity testing ensures that all the connections on the PCB are intact and functional, while isolation testing checks for any short circuits between adjacent traces.
Flexibility Testing
Flex PCBs must undergo flexibility testing to ensure that they can withstand the expected number of bending cycles without losing their electrical or mechanical properties. This is typically done using specialized equipment that repeatedly bends the PCB to simulate real-world conditions.
Environmental Testing
Flex PCBs used in harsh environments, such as aerospace or automotive applications, must undergo environmental testing to ensure their reliability under extreme conditions. This may include temperature cycling, humidity testing, and vibration testing.
Future of Flex PCBs
As technology continues to advance and the demand for smaller, lighter, and more flexible electronics grows, the future of flex PCBs looks promising.
Advanced Materials
Researchers are continually developing new materials with improved flexibility, durability, and electrical properties. These advanced materials, such as graphene and carbon nanotubes, may revolutionize the flex PCB industry in the coming years.
3D Printing
3D printing technology has the potential to transform the manufacturing of flex PCBs by enabling the creation of complex, three-dimensional structures with embedded electronic components. This could lead to even more compact and innovative designs.
Wearable Technology
The growth of wearable technology, such as smartwatches and fitness trackers, is driving the demand for flex PCBs that can conform to the human body and withstand constant movement and flexing.
Internet of Things (IoT)
The proliferation of IoT devices, which often require small, flexible, and low-power electronics, is expected to fuel the growth of the flex PCB Market in the coming years.
Frequently Asked Questions (FAQ)
-
What is the difference between flex PCBs and rigid PCBs?
Flex PCBs are made from flexible materials, such as polyimide or polyester, which allow them to bend and flex without losing their electrical properties. Rigid PCBs, on the other hand, are made from a rigid FR4 substrate and cannot be bent or flexed. -
Can flex PCBs be used in high-temperature applications?
Yes, flex PCBs made from polyimide (PI) can withstand high temperatures, making them suitable for applications such as aerospace and automotive electronics. -
How long do flex PCBs last compared to rigid PCBs?
Flex PCBs can last just as long as, if not longer than, rigid PCBs when designed and manufactured properly. They are more resistant to vibration and shock, which can extend their lifespan in harsh environments. -
Are flex PCBs more expensive than rigid PCBs?
Flex PCBs are generally more expensive than rigid PCBs due to the specialized materials and manufacturing processes required. However, they can often reduce overall system costs by replacing multiple rigid PCBs and reducing assembly time. -
Can flex PCBs be repaired if damaged?
Repairing flex PCBs can be challenging due to their delicate nature and the specialized materials used. In most cases, it is more cost-effective to replace a damaged flex PCB rather than attempting to repair it.
Conclusion
Flexible PCBs have transformed the electronics industry, enabling the creation of compact, lightweight, and durable devices across various sectors. With their unique properties and benefits, flex PCBs have become an essential component in modern electronics, from consumer gadgets to medical devices, aerospace, and automotive applications.
As technology advances and the demand for smaller, more flexible electronics grows, the future of flex PCBs looks promising. Advanced materials, 3D printing, wearable technology, and the Internet of Things are expected to drive the growth and innovation in the flex PCB market.
By understanding the capabilities, manufacturing processes, design considerations, and testing requirements of flex PCBs, engineers and manufacturers can harness the full potential of this versatile technology to create innovative, reliable, and high-performance electronic devices.
No responses yet