The Importance of Fast and Quality PCB fabrication
The electronics industry is constantly evolving, with new devices and applications being developed at a rapid pace. To keep up with this demand, PCB fabrication must be both fast and of high quality. Here are some reasons why fast and quality PCB fabrication is essential:
- Shorter time-to-market: With faster PCB fabrication, companies can bring their products to market more quickly, gaining a competitive edge.
- Cost-effectiveness: Quality PCBs reduce the risk of failures and rework, ultimately saving time and money.
- Improved reliability: Well-manufactured PCBs ensure the proper functioning and longevity of electronic devices.
- Enhanced customer satisfaction: Delivering high-quality products on time helps build trust and loyalty among customers.
The PCB Fabrication Process
To understand how fast and quality PCB fabrication is achieved, it’s essential to grasp the various steps involved in the process. The typical PCB fabrication process consists of the following stages:
1. Design and Layout
The first step in PCB fabrication is designing the circuit and creating the PCB layout. This involves using specialized software to plan the placement of components, traces, and vias on the board. A well-designed layout is crucial for ensuring the proper functioning and manufacturability of the PCB.
2. Material Selection
Choosing the right materials is essential for creating high-quality PCBs. The most common base material for PCBs is FR-4, a glass-reinforced epoxy laminate. However, other materials, such as polyimide or PTFE, may be used for specific applications that require higher temperature resistance or better dielectric properties.
3. Copper Deposition
Once the base material is selected, a thin layer of copper is deposited onto the board. This is typically done using a process called electroplating, where an electric current is used to deposit copper ions onto the surface of the board.
4. Photoresist Application and Exposure
A photoresist, a light-sensitive material, is applied to the copper-clad board. The PCB layout is then printed onto a transparent film, known as a photomask. The photomask is placed on top of the photoresist-coated board and exposed to UV light. The areas of the photoresist exposed to UV light become soluble, while the unexposed areas remain intact.
5. Etching
After exposure, the board is placed in an etching solution, which removes the copper from the areas where the photoresist has been exposed and dissolved. This leaves behind the desired copper traces and pads as defined by the PCB layout.
6. Drill and Plating
Holes are drilled into the board to accommodate through-hole components and vias. These holes are then plated with copper to ensure proper electrical connectivity between layers.
7. Solder Mask and Silkscreen
A solder mask, typically green in color, is applied to the board to protect the copper traces and prevent solder bridging. A silkscreen layer is then added to provide labels, logos, and other markings on the PCB.
8. Surface Finish
Finally, a surface finish is applied to the exposed copper areas to prevent oxidation and enhance solderability. Common surface finishes include Hot Air Solder Leveling (HASL), Immersion Silver, and Electroless Nickel Immersion Gold (ENIG).
Factors Affecting PCB Fabrication Speed and Quality
Several factors can influence the speed and quality of PCB fabrication. Understanding these factors can help in optimizing the fabrication process and ensuring the best possible results.
1. PCB Complexity
The complexity of the PCB design directly impacts the fabrication speed and quality. More complex designs with high component density, fine pitch sizes, and multiple layers require more time and precision to manufacture. Simplifying the design, when possible, can help improve fabrication speed and reduce the risk of errors.
2. Material Availability
The availability of the required materials can also affect the speed of PCB fabrication. Common materials, such as FR-4, are readily available and can be sourced quickly. However, specialized materials for high-performance applications may have longer lead times, impacting the overall fabrication speed.
3. Manufacturing Capabilities
The manufacturing capabilities of the PCB fabrication facility play a significant role in determining the speed and quality of the final product. Advanced equipment, skilled technicians, and well-maintained facilities are essential for producing high-quality PCBs quickly. Choosing a reputable PCB manufacturer with a proven track record can help ensure fast and reliable fabrication.
4. Quality Control Processes
Robust quality control processes are crucial for maintaining the quality of PCBs during fabrication. This includes regular inspections, testing, and adherence to industry standards such as IPC. Implementing strict quality control measures may slightly increase fabrication time but ultimately leads to higher-quality PCBs and fewer defects.
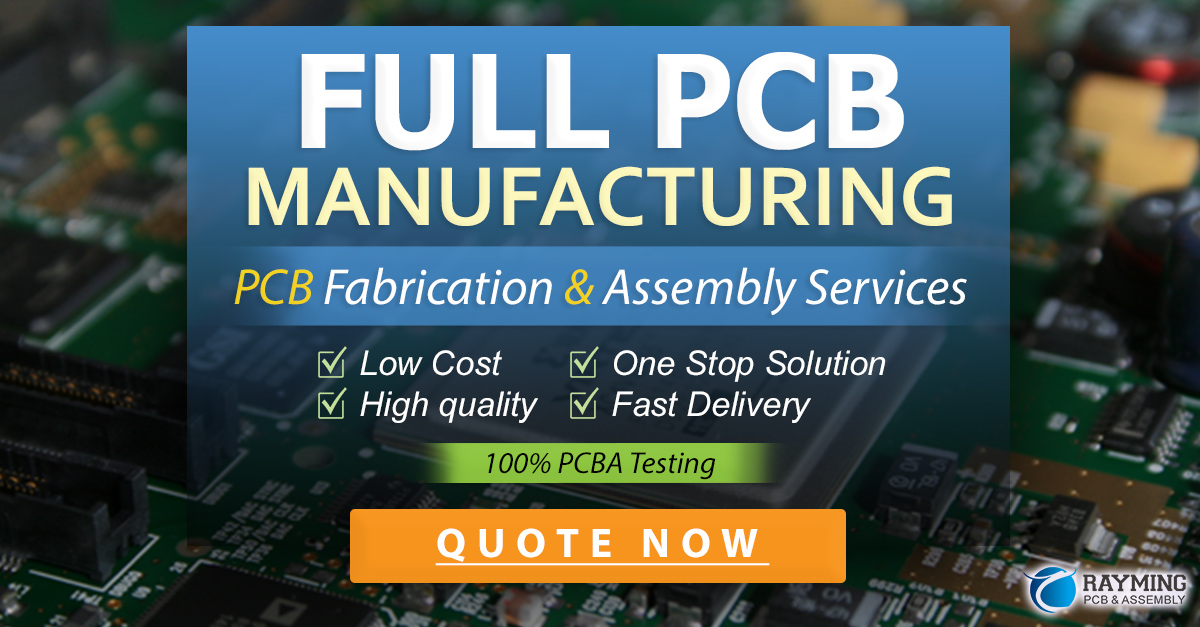
Advanced Technologies in PCB Fabrication
As the demand for faster and higher-quality PCBs grows, new technologies are emerging to meet these requirements. Some of the advanced technologies being employed in PCB fabrication include:
1. High-Density Interconnect (HDI)
HDI technology allows for the creation of PCBs with finer traces, smaller vias, and higher component density. This enables the fabrication of more compact and powerful electronic devices. HDI PCBs are produced using advanced techniques such as micro-vias, blind and buried vias, and sequential lamination.
2. Embedded Components
Embedded component technology involves placing components inside the PCB substrate rather than on the surface. This saves space, reduces the overall size of the PCB, and improves signal integrity. Embedded components are particularly useful in applications where miniaturization is crucial, such as wearable devices and medical implants.
3. 3D Printing
3D printing technology is increasingly being used in PCB fabrication to create complex structures and shapes that are difficult to achieve with traditional manufacturing methods. This includes the creation of 3D printed circuit boards, where conductive traces are printed directly onto a 3D-printed substrate. While still in its early stages, 3D printing has the potential to revolutionize PCB fabrication, enabling faster prototyping and more flexible designs.
Choosing a PCB Fabrication Partner
Selecting the right PCB fabrication partner is essential for ensuring fast and quality PCB production. When choosing a PCB manufacturer, consider the following factors:
- Experience and expertise: Look for a manufacturer with a proven track record in producing PCBs similar to your requirements.
- Manufacturing capabilities: Ensure that the manufacturer has the necessary equipment and technologies to meet your specific needs.
- Quality control processes: Choose a manufacturer that adheres to strict quality control standards and has a robust testing and inspection process.
- Turnaround time: Consider the manufacturer’s average turnaround time and their ability to meet your deadlines.
- Customer support: Select a manufacturer that offers responsive and knowledgeable customer support to assist you throughout the fabrication process.
Frequently Asked Questions (FAQs)
1. What is the typical turnaround time for PCB fabrication?
The typical turnaround time for PCB fabrication varies depending on the complexity of the design, the materials used, and the manufacturer’s capabilities. Simple PCBs can be fabricated in as little as 24 hours, while more complex designs may take several days or weeks.
2. How can I ensure the quality of my PCBs during fabrication?
To ensure the quality of your PCBs during fabrication, choose a reputable manufacturer with strict quality control processes, provide clear and detailed design files, and communicate your requirements effectively. Additionally, consider requesting a sample or prototype before proceeding with a full production run.
3. What are the most common materials used in PCB fabrication?
The most common base material used in PCB fabrication is FR-4, a glass-reinforced epoxy laminate. Other materials, such as polyimide, PTFE, and Rogers materials, are used for specific applications that require higher temperature resistance or better dielectric properties.
4. Can I expedite the PCB fabrication process?
Yes, many PCB manufacturers offer expedited services for an additional fee. This can include faster turnaround times, priority processing, and express shipping. However, it’s essential to ensure that the faster fabrication process does not compromise the quality of the final product.
5. What should I look for when selecting a PCB fabrication partner?
When selecting a PCB fabrication partner, consider factors such as their experience and expertise, manufacturing capabilities, quality control processes, turnaround time, and customer support. Choose a manufacturer that can meet your specific requirements and has a proven track record of producing high-quality PCBs.
Conclusion
Fast and quality PCB fabrication is essential for meeting the demands of the rapidly evolving electronics industry. By understanding the fabrication process, factors affecting speed and quality, and the advanced technologies available, businesses can make informed decisions when selecting a PCB fabrication partner. Choosing a reputable manufacturer with the necessary expertise, capabilities, and commitment to quality control can help ensure the successful production of high-quality PCBs in a timely manner.
PCB Fabrication Process | Description |
---|---|
Design and Layout | Creating the PCB layout using specialized software |
Material Selection | Choosing the appropriate base material for the PCB |
Copper Deposition | Depositing a thin layer of copper onto the board |
Photoresist Application and Exposure | Applying photoresist and exposing it to UV light through a photomask |
Etching | Removing copper from exposed areas to create traces and pads |
Drill and Plating | Drilling holes and plating them with copper for electrical connectivity |
Solder Mask and Silkscreen | Applying a protective solder mask and adding labels and markings |
Surface Finish | Applying a surface finish to prevent oxidation and enhance solderability |
As the electronics industry continues to advance, the demand for fast and quality PCB fabrication will only increase. By staying informed about the latest technologies, processes, and best practices, businesses can ensure that they are well-positioned to meet this demand and deliver high-quality electronic products to their customers.
No responses yet