Introduction to Electrostatic Copper Spraying
Electrostatic copper spraying is a revolutionary technology used in the manufacturing of thick-copper printed circuit boards (PCBs). This innovative process involves the application of a thin layer of copper onto the surface of a PCB substrate using an electrostatic charge. The electrostatic charge attracts the copper particles to the substrate, creating a uniform and adherent coating.
Benefits of Electrostatic Copper Spraying
The benefits of electrostatic copper spraying include:
- Improved adhesion of the copper layer to the substrate
- Uniform thickness of the copper layer
- Reduced waste and overspray compared to traditional spraying methods
- Increased efficiency and productivity in the manufacturing process
- Enhanced electrical and thermal conductivity of the PCB
Applications of Thick-Copper PCBs
Thick-copper PCBs are used in various applications that require high current carrying capacity, thermal management, and mechanical stability. Some of the common applications include:
- Power electronics
- Automotive electronics
- Aerospace and defense systems
- Industrial control systems
- High-performance computing
Power Electronics
In power electronics, thick-copper PCBs are used to handle high currents and voltages. The increased thickness of the copper layer allows for better heat dissipation and reduces the risk of thermal damage to the components. Examples of power electronics applications include:
- Power converters
- Inverters
- Motor drives
- Charging stations for electric vehicles
Automotive Electronics
Thick-copper PCBs are widely used in automotive electronics due to their ability to withstand harsh environmental conditions and vibrations. They are used in various automotive systems, such as:
- Engine control units (ECUs)
- Transmission control modules
- Battery management systems
- Infotainment systems
- Advanced driver assistance systems (ADAS)
Aerospace and Defense Systems
In aerospace and defense applications, thick-copper PCBs are used to ensure reliable performance under extreme conditions. They are used in:
- Radar systems
- Satellite communication systems
- Avionics
- Military vehicles and equipment
Electrostatic Copper Spraying Process
The electrostatic copper spraying process involves several steps to ensure a high-quality and uniform copper coating on the PCB substrate.
Substrate Preparation
Before the copper spraying process begins, the PCB substrate must be properly prepared. This involves cleaning the surface to remove any contaminants or debris that may affect the adhesion of the copper layer. The substrate is then treated with a surface modifier to improve the bonding between the substrate and the copper particles.
Copper Powder Preparation
The copper powder used in the electrostatic spraying process is specially formulated to have the desired particle size and shape. The powder is mixed with a carrier gas, typically nitrogen or air, to create a uniform suspension.
Electrostatic Charging
The copper powder is then charged using an electrostatic generator. The generator applies a high voltage to the powder, causing the particles to become positively charged. The charged particles are attracted to the grounded PCB substrate, which is negatively charged.
Spraying and Deposition
The charged copper powder is sprayed onto the PCB substrate using a specialized nozzle. The electrostatic attraction between the charged particles and the substrate ensures a uniform and adherent coating. The thickness of the copper layer can be controlled by adjusting the spraying parameters, such as the powder flow rate, nozzle distance, and substrate speed.
Curing and Sintering
After the copper layer is deposited, the PCB undergoes a curing and sintering process to improve the electrical and mechanical properties of the coating. The curing process involves exposing the PCB to elevated temperatures, typically between 150°C and 200°C, for a specified duration. This helps to evaporate any remaining solvents and enhances the bonding between the copper particles and the substrate.
The sintering process involves heating the PCB to temperatures near the melting point of copper, typically between 800°C and 900°C, in a controlled atmosphere. This process causes the copper particles to fuse together, creating a dense and highly conductive layer.
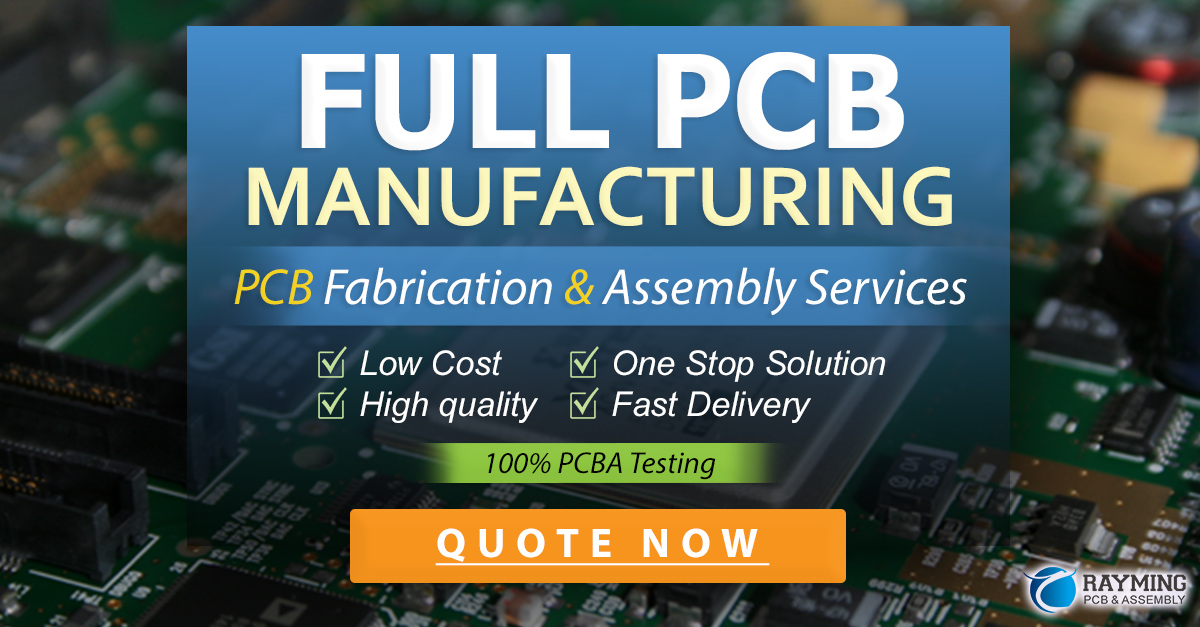
Advantages of Electrostatic Copper Spraying
Electrostatic copper spraying offers several advantages over traditional copper deposition methods, such as electroplating and foil lamination.
Uniform Thickness and Adhesion
One of the main advantages of electrostatic copper spraying is the ability to achieve a uniform thickness of the copper layer across the entire PCB surface. The electrostatic attraction ensures that the copper particles are evenly distributed, resulting in a consistent coating thickness. This uniformity is critical for maintaining the electrical and thermal performance of the PCB.
Additionally, the electrostatic spraying process promotes excellent adhesion between the copper layer and the substrate. The charged particles are strongly attracted to the substrate, creating a tight bond that resists delamination and improves the overall reliability of the PCB.
Reduced Waste and Environmental Impact
Electrostatic copper spraying is a more environmentally friendly process compared to traditional copper deposition methods. The process generates less waste, as the overspray is minimized due to the electrostatic attraction. This reduces the amount of copper that needs to be recovered or disposed of, leading to cost savings and a lower environmental impact.
Moreover, electrostatic spraying eliminates the need for hazardous chemicals, such as acids and plating solutions, that are commonly used in electroplating processes. This reduces the risk of environmental contamination and improves the safety of the manufacturing process.
Increased Efficiency and Productivity
Electrostatic copper spraying is a highly efficient process that can significantly increase the productivity of PCB manufacturing. The process is faster than traditional methods, as the copper layer can be deposited in a single step without the need for multiple plating cycles. This reduces the overall manufacturing time and allows for higher throughput.
Furthermore, the electrostatic spraying process is highly automated, which reduces the need for manual labor and minimizes the risk of human error. This automation leads to consistent quality and improved process control, resulting in higher yields and lower production costs.
Challenges and Limitations
Despite the numerous advantages of electrostatic copper spraying, there are some challenges and limitations associated with the technology.
Equipment and Process Optimization
Electrostatic copper spraying requires specialized equipment and process parameters that must be carefully optimized to achieve the desired results. The equipment, such as the electrostatic generator and spraying nozzle, must be properly maintained and calibrated to ensure consistent performance.
Additionally, the process parameters, such as the powder flow rate, nozzle distance, and substrate speed, must be fine-tuned for each specific PCB design and substrate material. This optimization process can be time-consuming and may require extensive testing and validation.
Substrate Compatibility
Not all PCB substrates are compatible with the electrostatic copper spraying process. Some substrates, such as those with high surface roughness or poor electrical conductivity, may not provide adequate bonding or performance. In these cases, alternative copper deposition methods may be required.
Cost Considerations
While electrostatic copper spraying offers many cost-saving benefits, such as reduced waste and increased efficiency, the initial investment in equipment and process development can be significant. This may limit the adoption of the technology, particularly for smaller PCB manufacturers with limited resources.
Future Trends and Developments
As the demand for thick-copper PCBs continues to grow, the electrostatic copper spraying technology is expected to evolve and improve.
Advanced Copper Alloys
Researchers are exploring the use of advanced copper alloys in electrostatic spraying to enhance the mechanical and thermal properties of the copper layer. These alloys, such as copper-nickel and copper-molybdenum, offer improved strength, ductility, and thermal conductivity compared to pure copper.
Hybrid Deposition Techniques
Combining electrostatic copper spraying with other deposition techniques, such as electroplating or chemical vapor deposition (CVD), may offer unique advantages. Hybrid deposition techniques can provide additional control over the copper layer thickness, adhesion, and electrical properties.
Additive Manufacturing Integration
Integrating electrostatic copper spraying with additive manufacturing techniques, such as 3D printing, may enable the fabrication of complex PCB structures with embedded copper layers. This integration could lead to the development of novel PCB designs with improved functionality and performance.
FAQ
-
Q: What is the typical thickness of a copper layer deposited using electrostatic spraying?
A: The thickness of the copper layer can vary depending on the specific application and PCB design. Electrostatic spraying can typically deposit copper layers ranging from 50 µm to 500 µm (0.05 mm to 0.5 mm) in thickness. -
Q: Can electrostatic copper spraying be used for multilayer PCBs?
A: Yes, electrostatic copper spraying can be used for multilayer PCBs. The process can be repeated to deposit multiple layers of copper, with insulating layers in between, to create a multilayer structure. -
Q: How does the electrical conductivity of electrostatically sprayed copper compare to that of traditional copper foils?
A: The electrical conductivity of electrostatically sprayed copper is comparable to that of traditional copper foils. However, the conductivity can be affected by factors such as the copper purity, particle size, and sintering conditions. -
Q: Is electrostatic copper spraying suitable for high-volume production?
A: Yes, electrostatic copper spraying is well-suited for high-volume production. The process is highly automated and efficient, allowing for high throughput and consistent quality. -
Q: Are there any safety concerns associated with electrostatic copper spraying?
A: As with any manufacturing process, proper safety precautions must be taken when using electrostatic copper spraying. The process involves high voltage electricity and fine copper powder, which can pose risks if not handled properly. Appropriate personal protective equipment (PPE) and safety protocols should be in place to ensure the safety of the operators.
Conclusion
Electrostatic copper spraying is a cutting-edge technology that offers numerous benefits for the manufacturing of thick-copper PCBs. The process enables the deposition of uniform and adherent copper layers, reducing waste and improving efficiency compared to traditional methods. With its wide range of applications, from power electronics to aerospace systems, electrostatic copper spraying is poised to play a significant role in the future of PCB manufacturing.
As the technology continues to evolve, with advancements in copper alloys, hybrid deposition techniques, and additive manufacturing integration, the potential for electrostatic copper spraying to revolutionize the PCB industry is immense. By embracing this innovative technology, PCB manufacturers can stay ahead of the curve and meet the growing demands for high-performance, reliable, and cost-effective thick-copper PCBs.
Copper Deposition Method | Thickness Range | Advantages | Limitations |
---|---|---|---|
Electrostatic Spraying | 50 µm – 500 µm | – Uniform thickness – Excellent adhesion – Reduced waste – Increased efficiency |
– Equipment and process optimization – Substrate compatibility – Initial investment cost |
Electroplating | 1 µm – 100 µm | – Well-established process – Wide range of thickness – Good electrical conductivity |
– Multiple plating cycles – Hazardous chemicals – Waste generation |
Foil Lamination | 18 µm – 400 µm | – Simple process – Wide availability of foils – Good electrical conductivity |
– Limited adhesion – Potential for air entrapment – Waste generation |
No responses yet