Introduction to Double-Sided PCBs
Double-sided printed circuit boards (PCBs) are a common choice for electronic devices that require a higher component density and more complex circuitry than single-sided PCBs can offer. These PCBs have conductive layers on both sides of the insulating substrate, allowing for the placement of components and the routing of traces on both sides of the board. This article will explore the various types of double-sided PCBs and the manufacturing process involved in their production.
Types of Double-Sided PCBs
1. Conventional Double-Sided PCBs
Conventional double-sided PCBs are the most basic type of double-sided board. They consist of two conductive layers, one on each side of the insulating substrate. The two layers are connected using through-hole technology, which involves drilling holes through the board and plating them with a conductive material to create electrical connections between the layers.
2. Double-Sided PCBs with Plated Through-Holes (PTH)
Double-sided PCBs with plated through-holes (PTH) are an advanced version of conventional double-sided PCBs. In this type of board, the through-holes are plated with a conductive material, typically copper, to create reliable electrical connections between the two layers. This plating process ensures a strong and stable connection, making PTH double-sided PCBs suitable for applications that require high reliability and durability.
3. Double-Sided PCBs with Surface Mount Technology (SMT)
Double-sided PCBs with surface mount technology (SMT) incorporate SMT components on one or both sides of the board. SMT components are smaller and have a lower profile than through-hole components, allowing for higher component density and improved performance. SMT double-sided PCBs can have a mix of both SMT and through-hole components, depending on the specific requirements of the application.
4. Flexible Double-Sided PCBs
Flexible double-sided PCBs are designed to bend and flex without damaging the electrical connections or components. These PCBs are made using flexible insulating materials, such as polyimide or polyester, and thin conductive layers that can withstand repeated bending. Flexible double-sided PCBs are commonly used in applications that require the PCB to fit into tight spaces or to move with the device, such as in wearable electronics or automotive systems.
Double-Sided PCB Manufacturing Process
The manufacturing process for double-sided PCBs involves several steps, each of which is critical to ensuring the quality and reliability of the final product.
1. PCB Design and Layout
The first step in the double-sided PCB manufacturing process is the design and layout of the board. This involves creating a schematic diagram of the circuit and a physical layout of the components and traces on the board. The layout must take into account factors such as component placement, trace width and spacing, and the location of through-holes and vias.
2. Substrate Preparation
Once the design is finalized, the next step is to prepare the insulating substrate. The substrate material, typically FR-4, is cut to the required size and shape. For double-sided PCBs, the substrate is then coated with a thin layer of copper on both sides using a process called electroless copper deposition.
3. Drilling and Plating
After the copper layers are applied, the next step is to drill the necessary holes for through-hole components and vias. These holes are then plated with a conductive material, usually copper, to create electrical connections between the two layers. The plating process involves several sub-steps, including:
- Desmearing: Removing any debris or smeared material from the drilled holes
- Activation: Preparing the hole walls for plating by applying a catalyst
- Electroless copper deposition: Applying a thin layer of copper to the hole walls
- Electrolytic copper plating: Building up the copper thickness to the desired level
4. Patterning and Etching
Once the holes are plated, the next step is to create the desired circuit pattern on the copper layers. This is done using a photolithography process, which involves:
- Applying a photosensitive resist to the copper layers
- Exposing the resist to UV light through a photomask that contains the circuit pattern
- Developing the resist to remove the exposed areas
- Etching away the unwanted copper using a chemical etchant
- Removing the remaining resist, leaving only the desired copper pattern
5. Solder Mask Application
After the etching process, a solder mask is applied to the PCB. The solder mask is a protective layer that covers the copper traces, leaving only the areas where components will be soldered exposed. This helps to prevent short circuits and improves the reliability of the board.
6. Silkscreen Printing
The final step in the manufacturing process is silkscreen printing. This involves printing text, logos, and other markings onto the PCB using a durable ink. The silkscreen layer helps to identify components, provide assembly instructions, and improve the overall aesthetics of the board.
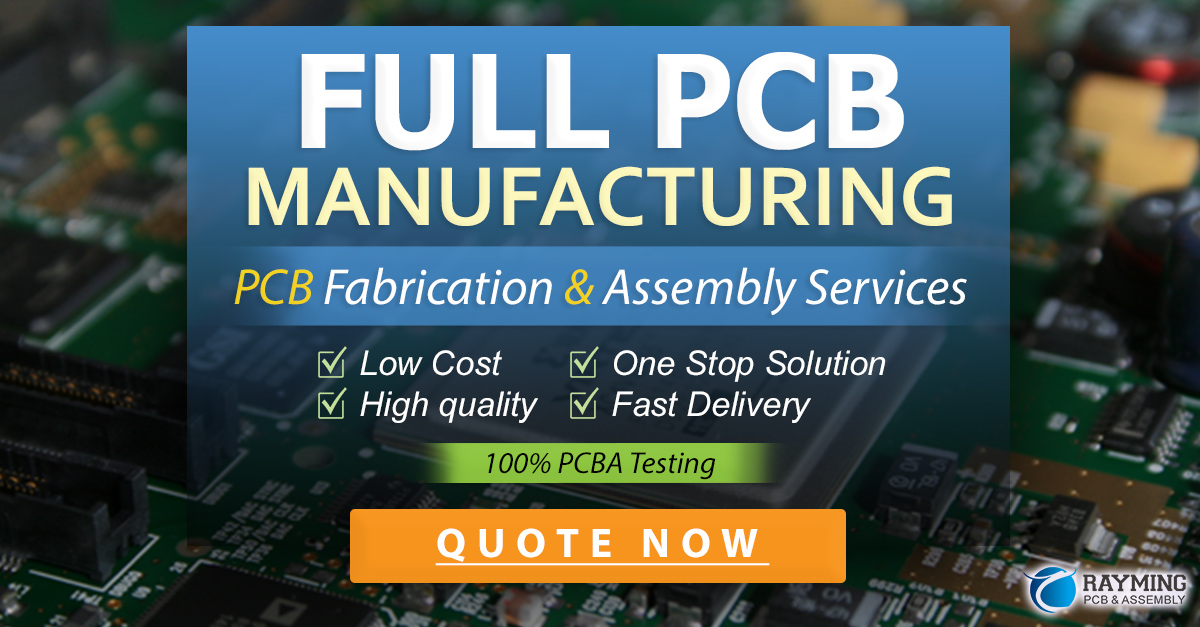
Advantages of Double-Sided PCBs
Double-sided PCBs offer several advantages over single-sided boards, including:
-
Higher component density: With two conductive layers, double-sided PCBs can accommodate more components in a smaller space, allowing for more compact and efficient designs.
-
Improved signal integrity: The use of plated through-holes and vias in double-sided PCBs helps to minimize signal interference and crosstalk, resulting in better signal integrity and overall performance.
-
Enhanced thermal management: Double-sided PCBs can dissipate heat more effectively than single-sided boards, as the additional copper layer helps to spread the heat more evenly across the board.
-
Greater design flexibility: With two conductive layers, designers have more options for routing traces and placing components, enabling more complex and innovative circuit designs.
Challenges in Double-Sided PCB Manufacturing
While double-sided PCBs offer numerous benefits, there are also some challenges associated with their manufacturing, including:
-
Increased complexity: The additional conductive layer and the need for plated through-holes make double-sided PCBs more complex to manufacture than single-sided boards, requiring more advanced equipment and expertise.
-
Higher cost: Due to the increased complexity and the additional materials and processes involved, double-sided PCBs are generally more expensive to manufacture than single-sided boards.
-
Potential for warping: The use of different materials and the application of heat during the manufacturing process can sometimes cause double-sided PCBs to warp or twist, which can affect their performance and reliability.
-
Difficulty in troubleshooting: With components and traces on both sides of the board, troubleshooting and repairs can be more challenging for double-sided PCBs compared to single-sided boards.
Applications of Double-Sided PCBs
Double-sided PCBs are used in a wide range of electronic devices and applications, including:
-
Consumer electronics: Many consumer devices, such as smartphones, tablets, and laptops, use double-sided PCBs to achieve high component density and performance in a compact form factor.
-
Industrial equipment: Double-sided PCBs are commonly used in industrial control systems, power electronics, and automation equipment, where reliability and durability are critical.
-
Medical devices: The enhanced signal integrity and thermal management capabilities of double-sided PCBs make them well-suited for use in medical devices, such as patient monitors and diagnostic equipment.
-
Automotive electronics: Double-sided PCBs are increasingly used in automotive applications, such as engine control units, infotainment systems, and advanced driver assistance systems (ADAS), where space is limited and reliability is paramount.
-
Aerospace and defense: The high-performance and reliability requirements of aerospace and defense applications often necessitate the use of double-sided PCBs, which can withstand harsh environmental conditions and meet strict quality standards.
Frequently Asked Questions (FAQ)
-
Q: What is the difference between a double-sided PCB and a multi-layer PCB?
A: A double-sided PCB has two conductive layers, one on each side of the insulating substrate, while a multi-layer PCB has three or more conductive layers, with insulating layers separating them. Multi-layer PCBs offer even higher component density and more complex routing options than double-sided PCBs. -
Q: Can double-sided PCBs be used for high-frequency applications?
A: Yes, double-sided PCBs can be used for high-frequency applications, but they may require special design considerations to minimize signal integrity issues, such as impedance matching and crosstalk. In some cases, multi-layer PCBs or specialized materials may be necessary to achieve optimal high-frequency performance. -
Q: Are double-sided PCBs more environmentally friendly than single-sided PCBs?
A: While double-sided PCBs require more materials and processing steps than single-sided boards, they can actually be more environmentally friendly in some cases. By allowing for higher component density and more compact designs, double-sided PCBs can reduce the overall size and weight of electronic devices, leading to reduced material consumption and transportation costs. -
Q: How do I choose between a conventional double-sided PCB and one with plated through-holes?
A: The choice between a conventional double-sided PCB and one with plated through-holes depends on the specific requirements of your application. Plated through-hole PCBs offer superior electrical connections and reliability, making them suitable for applications that demand high performance and durability. However, they are also more expensive and complex to manufacture than conventional double-sided PCBs. -
Q: Can double-sided PCBs be manufactured using lead-free materials?
A: Yes, double-sided PCBs can be manufactured using lead-free materials, such as lead-free solder and surface finishes. Many PCB manufacturers now offer lead-free options to comply with environmental regulations and to meet the growing demand for more sustainable electronic products.
Conclusion
Double-sided PCBs are a versatile and widely used type of printed circuit board, offering numerous advantages over single-sided boards, including higher component density, improved signal integrity, and enhanced thermal management. With various types of double-sided PCBs available, including conventional, plated through-hole, surface mount, and flexible variants, designers have a wide range of options to choose from based on their specific application requirements.
The manufacturing process for double-sided PCBs involves several critical steps, from design and layout to substrate preparation, drilling, plating, patterning, etching, and finishing. Each step requires precision, expertise, and specialized equipment to ensure the quality and reliability of the final product.
While double-sided PCBs offer many benefits, they also present some challenges, such as increased complexity, higher cost, and potential manufacturing issues. However, the advantages of double-sided PCBs often outweigh these challenges, making them a preferred choice for a wide range of electronic devices and applications, from consumer electronics and industrial equipment to medical devices, automotive electronics, and aerospace and defense systems.
As technology continues to advance and the demand for more compact, high-performance electronic devices grows, the importance of double-sided PCBs in the electronics industry is likely to increase. By understanding the types, manufacturing processes, advantages, and challenges of double-sided PCBs, designers and manufacturers can make informed decisions and create innovative, reliable, and efficient electronic products.
No responses yet