Understanding Differential Signaling and Trace Impedance
Differential signaling is a widely used technique in high-speed digital systems to transmit data over paired conductors. Unlike single-ended signaling, which uses a single conductor and a common ground reference, differential signaling uses two complementary signals carried on two separate conductors. The differential signal is the voltage difference between these two conductors.
The main advantages of differential signaling include:
1. Improved noise immunity
2. Reduced electromagnetic interference (EMI)
3. Better signal integrity at high frequencies
To achieve these benefits, it is crucial to maintain a consistent differential impedance along the length of the traces. Impedance Matching is essential to minimize signal reflections, ensure proper termination, and optimize signal quality.
What is Trace Impedance?
Trace impedance refers to the opposition to the flow of alternating current (AC) in a PCB trace. It is determined by the trace geometry, dielectric properties of the PCB substrate, and the presence of nearby reference planes. The characteristic impedance of a trace is the ratio of the voltage to the current in a traveling wave on the trace.
In a typical PCB Stackup, traces are routed between two reference planes, such as ground or power planes. These reference planes provide a low-impedance return path for the signal current and help maintain a constant impedance along the trace.
However, in some cases, it may not be possible or desirable to have a continuous reference plane beneath the differential traces. This can occur due to routing constraints, layer limitations, or other design requirements. In such scenarios, it becomes challenging to control the differential impedance without a reference plane.
Factors Affecting Differential Trace Impedance
Several factors influence the differential impedance of traces in the absence of a reference plane:
-
Trace geometry: The width, thickness, and spacing of the differential traces play a significant role in determining their impedance. Wider traces have lower impedance, while thinner traces have higher impedance. The spacing between the traces affects the coupling and the differential impedance.
-
Dielectric constant (Dk): The dielectric constant of the PCB substrate material impacts the impedance of the traces. A higher Dk value results in lower impedance, while a lower Dk value leads to higher impedance.
-
Height above ground: The distance between the differential traces and the nearest reference plane (if present) affects the impedance. As the height increases, the impedance also increases.
-
Proximity to other traces: The presence of other traces or conductors near the differential pair can influence the impedance through electromagnetic coupling.
Techniques for Controlling Differential Impedance
Controlling differential impedance without a reference plane requires careful design considerations and techniques. Here are some approaches to achieve consistent impedance:
1. Adjust Trace Geometry
One of the primary methods to control differential impedance is by adjusting the trace geometry. This involves modifying the width, thickness, and spacing of the differential traces.
- Increasing the trace width lowers the impedance, while decreasing the width increases the impedance.
- Increasing the trace thickness lowers the impedance, while decreasing the thickness increases the impedance.
- Increasing the spacing between the traces decreases the coupling and increases the differential impedance, while decreasing the spacing has the opposite effect.
By carefully selecting the appropriate trace geometry, designers can achieve the desired differential impedance without relying on a reference plane.
Trace Width (mil) | Trace Thickness (mil) | Trace Spacing (mil) | Differential Impedance (Ω) |
---|---|---|---|
5 | 1.4 | 5 | 100 |
6 | 1.4 | 5 | 90 |
7 | 1.4 | 5 | 83 |
8 | 1.4 | 5 | 77 |
Table 1: Example of how trace geometry affects differential impedance.
2. Utilize Dielectric Materials
The choice of dielectric material for the PCB substrate significantly influences the differential impedance. By selecting materials with appropriate dielectric constants (Dk), designers can achieve the desired impedance.
- High-Dk materials, such as FR-4, lower the impedance and require wider trace spacing to maintain the same impedance compared to low-Dk materials.
- Low-Dk materials, such as Rogers or Isola, exhibit higher impedance and allow for narrower trace spacing while maintaining the same impedance.
Designers should consider the dielectric properties of the available materials and choose the one that best suits their impedance requirements.
Dielectric Material | Dielectric Constant (Dk) | Dissipation Factor (Df) | Differential Impedance (Ω) |
---|---|---|---|
FR-4 | 4.3 | 0.02 | 100 |
Rogers RO4003C | 3.38 | 0.0027 | 100 |
Isola IS410 | 3.96 | 0.0165 | 100 |
Table 2: Comparison of dielectric materials and their impact on differential impedance.
3. Employ Shielding Techniques
In the absence of a continuous reference plane, shielding techniques can be employed to control the differential impedance and minimize crosstalk.
-
Coplanar shielding: This technique involves placing ground traces or pours alongside the differential traces on the same layer. The ground traces act as a local reference plane and help maintain a consistent impedance.
-
Microstrip shielding: If a reference plane is available on an adjacent layer, designers can use microstrip shielding. This involves placing the differential traces on one layer and a ground plane on the adjacent layer, with the traces positioned over the ground plane.
-
Stripline shielding: For inner layers, stripline shielding can be used. This technique sandwiches the differential traces between two ground planes, providing shielding from both sides.
Shielding techniques help confine the electromagnetic fields and reduce the impact of nearby traces or conductors on the differential impedance.
4. Optimize Trace Routing
Careful trace routing is crucial to maintain consistent differential impedance throughout the signal path. Designers should consider the following guidelines:
-
Length matching: Ensure that the lengths of the differential traces are closely matched to avoid phase imbalance and impedance mismatch. Length mismatches can lead to signal integrity issues and degrade the differential signal quality.
-
Avoid discontinuities: Minimize abrupt changes in trace geometry, such as sharp bends or width transitions. Discontinuities can cause impedance variations and reflections, impacting signal integrity.
-
Route differentially: Treat the differential pair as a single unit during routing. Avoid splitting the pairs or routing them separately, as this can introduce impedance mismatches and degrade the differential signal.
-
Maintain consistent spacing: Keep the spacing between the differential traces consistent along the entire route. Variations in spacing can affect the coupling and impedance of the differential pair.
By following these routing guidelines, designers can minimize impedance variations and ensure a more consistent differential impedance profile.
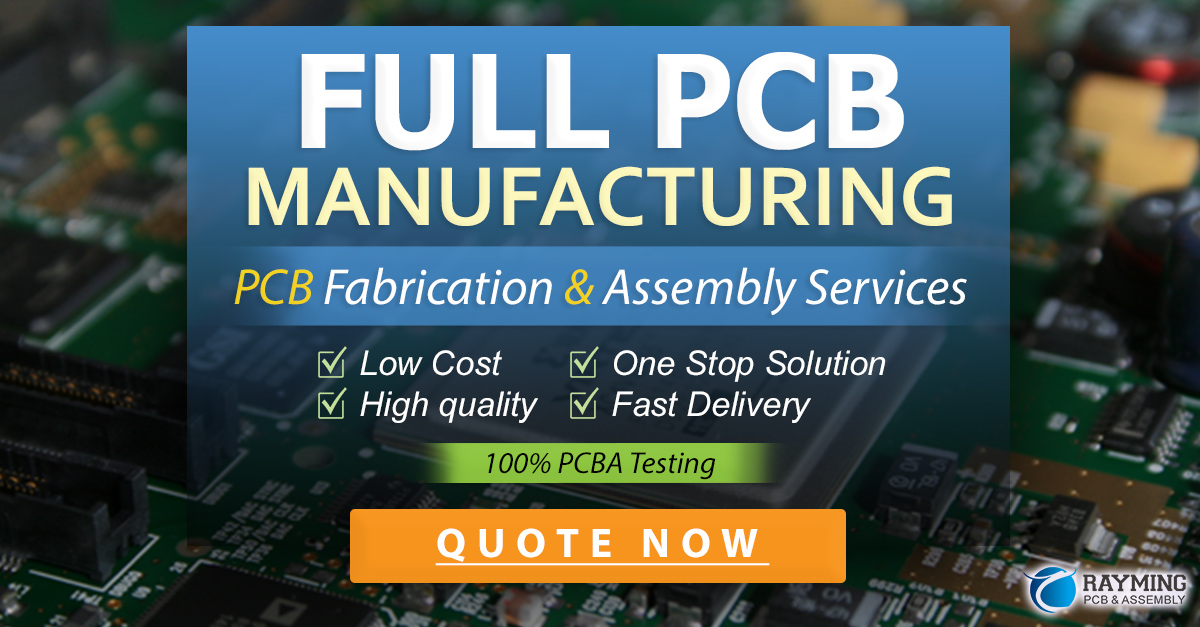
Simulation and Analysis
To accurately predict and optimize the differential impedance without a reference plane, designers can leverage simulation tools and analysis techniques. These tools help in modeling the PCB stackup, trace geometry, and dielectric properties to estimate the impedance and identify potential issues.
2D Field Solvers
2D field solvers, such as Polar SI9000 or Ansys SIwave, can be used to analyze the cross-section of the differential traces and calculate the impedance. These tools solve Maxwell’s equations in two dimensions and provide accurate impedance results based on the trace geometry, dielectric properties, and boundary conditions.
Designers can input the PCB stackup information, including layer thicknesses, dielectric constants, and trace dimensions, into the 2D field solver. The solver then computes the electric and magnetic field distributions and calculates the characteristic impedance of the differential pair.
3D Electromagnetic Simulation
For more complex scenarios, such as traces with non-uniform geometry or in the presence of nearby components, 3D electromagnetic (EM) simulation tools like Ansys HFSS or Cadence Sigrity can be employed. These tools perform full-wave EM simulations to accurately model the electromagnetic behavior of the differential traces and their surrounding environment.
3D EM simulations take into account the complete PCB geometry, including traces, vias, and components. They can help identify impedance discontinuities, coupling effects, and potential signal integrity issues. By analyzing the S-parameters and time-domain reflectometry (TDR) results, designers can fine-tune the trace geometry and optimize the differential impedance.
Impedance Measurement
After fabricating the PCB, it is essential to verify the actual differential impedance through measurements. Impedance measurement techniques, such as TDR or vector network analyzer (VNA) measurements, can be used to characterize the impedance profile of the differential traces.
TDR measurements involve injecting a fast rise-time pulse into the differential pair and measuring the reflected signal. By analyzing the reflection coefficients and propagation delay, designers can determine the impedance variations along the trace length and identify any discontinuities or mismatches.
VNA measurements, on the other hand, involve sweeping a range of frequencies and measuring the S-parameters of the differential pair. The S-parameters provide information about the impedance, insertion loss, and return loss of the traces. By comparing the measured impedance with the target impedance, designers can validate the design and make necessary adjustments.
Best Practices and Guidelines
When designing differential traces without a reference plane, consider the following best practices and guidelines to ensure optimal signal integrity and impedance control:
-
Use balanced differential traces: Ensure that the differential traces are symmetrical and have equal length, width, and spacing. Balanced traces help maintain a consistent differential impedance and minimize common-mode noise.
-
Keep traces close to each other: Place the differential traces as close together as possible while maintaining the required spacing for impedance control. Closer spacing improves coupling and reduces the impact of external noise sources.
-
Avoid crossing reference plane gaps: If possible, route the differential traces to avoid crossing gaps in the reference plane. Crossing plane gaps can cause impedance discontinuities and degrade signal quality.
-
Use differential vias: When transitioning between layers, use differential vias to maintain the balance and coupling of the differential pair. Differential vias should be placed close together and have equal length and diameter.
-
Minimize trace bends: Avoid sharp bends or abrupt changes in trace direction. Use smooth, gradual bends to minimize impedance discontinuities and reflections.
-
Provide sufficient clearance: Ensure adequate clearance between the differential traces and other components, traces, or planes to avoid unintended coupling and impedance variations.
-
Perform thorough simulation and analysis: Utilize simulation tools and analysis techniques to predict and optimize the differential impedance. Verify the design through measurements to ensure compliance with the target impedance.
Frequently Asked Questions (FAQ)
-
What is the impact of not having a reference plane on differential impedance?
Not having a reference plane beneath the differential traces can make it more challenging to control and maintain a consistent differential impedance. Without a reference plane, the impedance becomes more sensitive to trace geometry, dielectric properties, and nearby conductors. -
Can differential impedance be achieved without a reference plane?
Yes, it is possible to achieve differential impedance without a reference plane by carefully designing the trace geometry, selecting appropriate dielectric materials, and employing shielding techniques. However, it requires more effort and attention to detail compared to having a continuous reference plane. -
What is the recommended spacing between differential traces?
The recommended spacing between differential traces depends on factors such as the target impedance, trace width, dielectric constant, and manufacturing capabilities. Generally, a spacing of 2 to 3 times the trace width is a good starting point. However, it is essential to perform simulations and calculations to determine the optimal spacing for a specific design. -
How does the height of the traces above the reference plane affect differential impedance?
The height of the traces above the reference plane, also known as the dielectric thickness, affects the differential impedance. As the height increases, the impedance also increases. Designers need to consider the available layer stackup and choose appropriate dielectric thicknesses to achieve the desired impedance. -
What are the consequences of impedance mismatches in differential traces?
Impedance mismatches in differential traces can lead to signal integrity issues, such as reflections, ringing, and increased crosstalk. These issues can degrade the quality of the differential signal, cause timing errors, and limit the maximum operating frequency of the system. Proper impedance matching is crucial to ensure reliable high-speed data transmission.
Conclusion
Designing differential traces without a reference plane presents unique challenges in controlling and maintaining the desired impedance. By understanding the factors that influence differential impedance and employing appropriate design techniques, it is possible to achieve consistent impedance even in the absence of a continuous reference plane.
Adjusting trace geometry, selecting suitable dielectric materials, utilizing shielding techniques, and optimizing trace routing are key strategies to control differential impedance. Additionally, leveraging simulation tools and performing thorough analysis and measurements are essential to validate and fine-tune the design.
By following best practices and guidelines, designers can successfully implement differential signaling without a reference plane while ensuring signal integrity and reliable high-speed data transmission. However, it is important to recognize the limitations and challenges associated with this approach and carefully consider the specific requirements of each design.
As technology advances and data rates continue to increase, the importance of differential signaling and impedance control becomes even more critical. By staying informed about the latest techniques and tools, designers can effectively tackle the challenges of differential trace impedance in various PCB design scenarios, including those without a reference plane.
No responses yet