What is PCB Design?
PCB design is the process of creating printed circuit boards that electrically connect and mechanically support electronic components using conductive pathways, tracks or signal traces etched from copper sheets laminated onto a non-conductive substrate. PCB design involves the creation of electronic schematics, component placement, and routing of traces. The aim is to design a reliable, manufacturable PCB that performs its intended function.
Key aspects of PCB design include:
- Schematic capture – creating the electronic schematic diagram showing component connections
- Board layout – arranging components and routing traces on the board
- Design rule checks (DRC) – verifying the design meets manufacturing specifications and will function as intended
- Documentation – generating manufacturing files, assembly notes, board views, etc.
Why is PCB Design Important?
Proper PCB design is critical for several reasons:
-
Functionality – A well-designed PCB will reliably perform its intended function. Poor design can lead to issues like signal integrity problems, electromagnetic interference, thermal problems, etc.
-
Manufacturability – The PCB design must adhere to manufacturing capabilities and design rules. Violations may require redesign or make the board impossible to produce.
-
Cost – Effective PCB layout and stackup can minimize board size and layer count, reducing cost. Errors caught late or that require redesign drastically increase cost.
-
Reliability – Proper component placement, trace routing, and protection against environmental factors improve PCB reliability in the field.
-
Time-to-Market – An efficient design process helps bring products to market faster. Starting with the end in mind and avoiding redesigns accelerates development.
PCB Design Flow
The PCB design process typically follows these steps:
-
Schematic Capture
- Create electronic schematic in EDA tool
- Add components, part numbers, values
- Make electrical connections between components
-
Board Layout
- Define board shape and dimensions
- Place components on board
- Fan out component connections
- Route traces to make point-to-point connections
- Define keepout areas, mounting holes, etc.
-
Design Rule Checks (DRC)
- Verify design meets manufacturing constraints
- Check for errors like open connections, short circuits, trace spacing violations, etc.
- Ensure all connections are routed
-
Documentation
- Generate bill of materials (BOM), Gerber files, drill files, assembly drawings, etc.
- Create PCB assembly and test notes
- Release design package to manufacturing
-
Prototyping and Testing
- Source PCB and components
- Assemble prototype boards
- Perform functional testing and debug
- Incorporate any fixes and improvements
-
Production
- Release final design package
- Mass production run
- Quality control and ongoing reliability testing
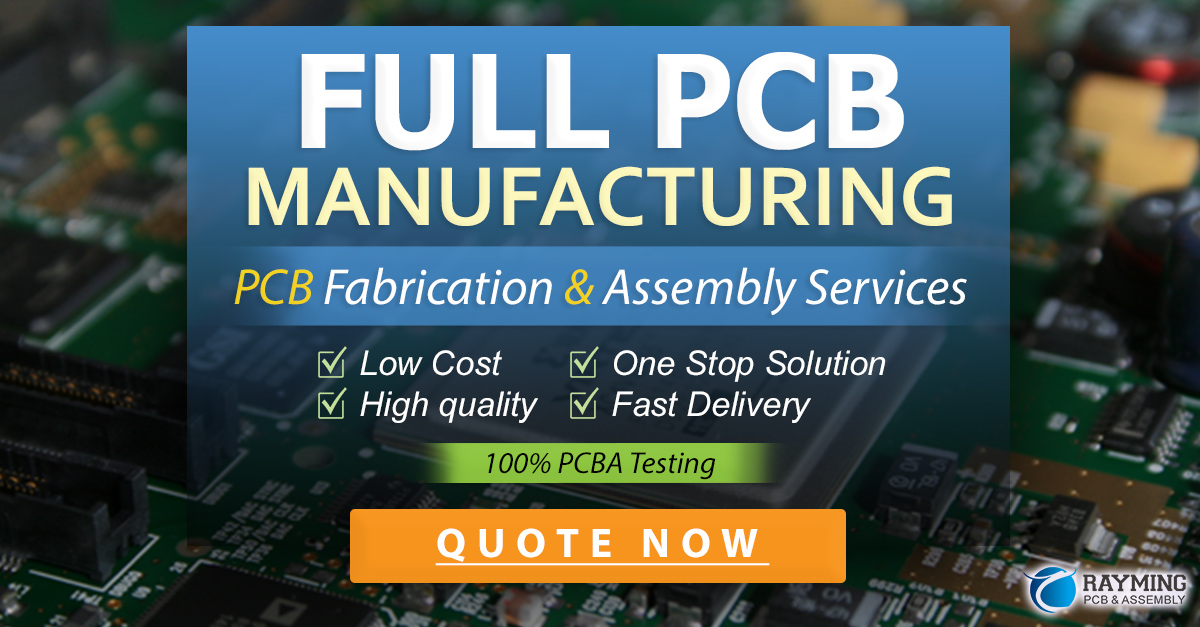
PCB Design Guidelines
Following some basic guidelines helps ensure a manufacturable, functional, and robust PCB design:
Board Stackup
- Use appropriate number of layers for circuit complexity and routing density
- Select dielectric materials based on cost, frequency, and environmental requirements
- Specify copper weights that allow sufficient current carrying capacity
- Define controlled impedance requirements
Component Placement
- Group components by function and circuit block
- Minimize distance between connected components
- Provide adequate clearance for assembly and manufacturing
- Consider component heights, especially for tight packaging
- Orient components for easy soldering and rework
- Use thermal reliefs and vias for heat dissipation
Trace Routing
- Make traces as short and direct as possible
- Use appropriate trace widths for current carried
- Avoid 90 degree corners – use 45s or arcs
- Provide ground planes for shielding and current return
- Route high speed signals carefully to maintain signal integrity
- Avoid crossing split (ground) planes with signals
- Minimize crosstalk by separating parallel traces
- Use solid copper pours to improve EMI/EMC
Power Integrity
- Use appropriate decoupling/bypass capacitors
- Place capacitors close to ICs
- Use power and ground planes
- Define power regions if needed
- Connect analog and digital grounds at one point
- Ensure adequate power trace widths
Manufacturability
- Adhere to minimum trace width and spacing for copper weights used
- Provide sufficient annular rings for vias
- Avoid acute angles or jagged copper features
- Define solder mask and silkscreen layers
- Panelize boards if applicable for fab process
Testing and Rework
- Provide test points for key signals
- Ensure access to signals for debug
- Avoid blind or buried vias if possible for easier rework
- Consider vias in pads for dense BGA footprints
PCB Layout Software
Many PCB layout and EDA (electronic design automation) software packages are available, ranging from simple to very advanced. Some popular options include:
Tool | Vendor | Level | Operating System |
---|---|---|---|
EAGLE | Autodesk | Entry | Windows, Mac, Linux |
KiCad | Open Source | Entry | Windows, Mac, Linux |
CircuitStudio | Altium | Mid-Range | Windows |
DipTrace | Novarm | Mid-Range | Windows |
OrCAD/Allegro | Cadence | High-End | Windows, Linux |
Altium Designer | Altium | High-End | Windows |
PADS | Mentor | High-End | Windows |
Xpedition | Mentor | High-End | Windows, Linux |
Selection factors may include:
– Ease of use and learning curve
– Schematic capture and layout capabilities
– Design rule checks and error prevention
– Supported board complexity and layer counts
– Automated functions (auto-routing, etc.)
– Library and component availability
– Output file formats
– Extensibility and customization
– Cost and licensing
PCB Design Services
For those without in-house PCB design expertise, many PCB design services are available to assist in schematic development, board layout, manufacturing handoff and more. Engaging an experienced PCB design service can improve design quality, accelerate timelines, and reduce costly mistakes.
Attributes to look for in a PCB design service include:
- Technical capability in your application area
- Experience with your EDA toolset
- Clear design requirements capture process
- Frequent and clear design reviews
- Detailed documentation and design package handoff
- Assistance with manufacturing and vendor management
- Prototyping and testing support
- Good communication and responsiveness
- Positive references and design examples
- Competitive cost and lead times
Frequently Asked Questions
What is the best PCB design software?
There is no single “best” PCB design software, as the ideal choice depends on the user’s needs, budget, and preferences. For entry-level or hobbyist use, EAGLE or KiCad are good options. For more advanced professional use, Altium Designer, OrCAD/Allegro, or Mentor PADS are popular.
How much does custom PCB design cost?
The cost of custom PCB design can vary widely based on the complexity of the board, layer count, designer experience level, turnaround time, and other factors. Simple designs may cost a few hundred dollars while complex, high-speed digital boards could be tens of thousands of dollars. Getting a clear quote up front is advisable.
How long does PCB design take?
PCB design timelines can range from a few days to several months based on the complexity of the design and any iterations required. Simple single-layer boards may be designed in under a week, while complex multi-layer boards with sensitive RF circuits, for example, could take several design spins over multiple months to optimize.
What information is needed to get started with PCB design?
To begin a PCB design, key information required includes:
– The electronic schematic or circuit description
– The components to be used (part numbers, datasheets, footprints)
– The board size and mechanical constraints
– Special requirements (controlled impedance, environmental, agency certifications, etc.)
– The desired quantity and target cost
– Required design outputs (Gerber/ODB++ files, design files, etc.)
What are some common PCB design mistakes to avoid?
Some common pitfalls in PCB design include:
– Failing to consider manufacturing capabilities and constraints up front
– Not properly defining the PCB stackup and layer structure
– Incorrect component footprints and pinouts
– Forgetting to connect power and ground pins
– Violating controlled impedance requirements
– Lack of a clearly defined design rule check (DRC) process
– Not considering testing and rework requirements
– Insufficient communication between schematic and layout designers
– Rushing design reviews and sign-offs
By following the guidelines outlined above, carefully selecting design tools and partners, and proactively communicating requirements, you’ll be well on your way to successful PCB design. Effective PCB design is a critical contributor to electronic product functionality, reliability, cost, and time-to-market.
No responses yet