Introduction to PCB Manufacturing
Printed Circuit Board (PCB) manufacturing is a complex process that involves several steps to create the final product. PCBs are essential components in almost all electronic devices, from smartphones and laptops to medical equipment and aerospace systems. The demand for high-quality, reliable PCBs has increased significantly in recent years due to the rapid growth of the electronics industry.
The PCB Manufacturing Process
The PCB manufacturing process typically involves the following steps:
-
Design: The first step is to design the PCB using specialized software such as Altium Designer, Eagle, or KiCad. The design includes the layout of the components, traces, and vias.
-
Fabrication: Once the design is finalized, the PCB is fabricated using a variety of methods, including etching, drilling, and plating. The most common method is photolithography, which uses light to transfer the design onto a copper-clad board.
-
Assembly: After fabrication, the components are assembled onto the PCB using surface mount technology (SMT) or through-hole technology (THT). SMT is more common in modern PCBs due to its smaller size and higher density.
-
Testing: Finally, the assembled PCB is tested to ensure that it functions as intended. This includes electrical testing, visual inspection, and functional testing.
Types of PCBs
There are several types of PCBs, each with its own unique characteristics and applications:
Type | Layers | Applications |
---|---|---|
Single-sided | 1 | Simple, low-cost devices |
Double-sided | 2 | More complex devices, higher density |
Multi-layer | 3+ | High-density, high-speed devices |
Flex | Varies | Wearable devices, tight spaces |
Rigid-flex | Varies | Combines rigid and flex sections |
Carbon Ink PCB Manufacturing
Carbon ink PCB manufacturing is a relatively new technology that offers several advantages over traditional methods. Carbon ink is a conductive material that can be printed onto a variety of substrates, including paper, plastic, and fabric. This allows for the creation of flexible, lightweight, and low-cost PCBs.
Advantages of Carbon Ink PCBs
Carbon ink PCBs offer several advantages over traditional PCBs:
-
Flexibility: Carbon ink PCBs can be printed on flexible substrates, allowing for the creation of wearable devices and other applications where flexibility is important.
-
Low cost: Carbon ink is less expensive than traditional PCB materials, making it an attractive option for low-cost devices.
-
Environmentally friendly: Carbon ink is a non-toxic, biodegradable material that can be easily disposed of without harming the environment.
-
Rapid prototyping: Carbon ink PCBs can be quickly and easily prototyped using standard printing methods, allowing for faster iteration and development.
Applications of Carbon Ink PCBs
Carbon ink PCBs have a wide range of applications, including:
-
Wearable devices: Carbon ink PCBs can be printed on flexible substrates, making them ideal for wearable devices such as smartwatches, fitness trackers, and medical sensors.
-
Internet of Things (IoT): Carbon ink PCBs can be used to create low-cost, disposable sensors for IoT applications such as smart homes, smart cities, and industrial monitoring.
-
RFID tags: Carbon ink can be used to create low-cost, printable RFID tags for inventory management, asset tracking, and access control.
-
Flexible displays: Carbon ink can be used to create flexible displays for smartphones, tablets, and other devices.
PCB Assembly at One-Stop
One-stop PCB assembly is a service that combines PCB manufacturing and assembly into a single, streamlined process. This can save time and money for customers who need both services, as they only need to deal with a single vendor.
Advantages of One-Stop PCB Assembly
One-stop PCB assembly offers several advantages over using separate vendors for manufacturing and assembly:
-
Faster turnaround: By combining manufacturing and assembly into a single process, one-stop PCB assembly can reduce the overall turnaround time for a project.
-
Lower costs: One-stop PCB assembly can be more cost-effective than using separate vendors, as there are fewer transaction costs and opportunities for errors.
-
Improved communication: Having a single point of contact for both manufacturing and assembly can improve communication and reduce the risk of misunderstandings or errors.
-
Higher quality: One-stop PCB assembly providers can ensure that the manufacturing and assembly processes are optimized for each other, resulting in higher quality PCBs.
Choosing a One-Stop PCB Assembly Provider
When choosing a one-stop PCB assembly provider, there are several factors to consider:
-
Experience: Look for a provider with experience in your specific industry or application, as they will be better equipped to handle your unique requirements.
-
Capabilities: Make sure that the provider has the necessary equipment and expertise to handle your project, including any specialized requirements such as high-density interconnect (HDI) or flex PCBs.
-
Quality control: Look for a provider with robust quality control processes in place, including ISO certification and automated inspection equipment.
-
Customer service: Choose a provider with responsive, knowledgeable customer service that can answer your questions and address any issues that arise.
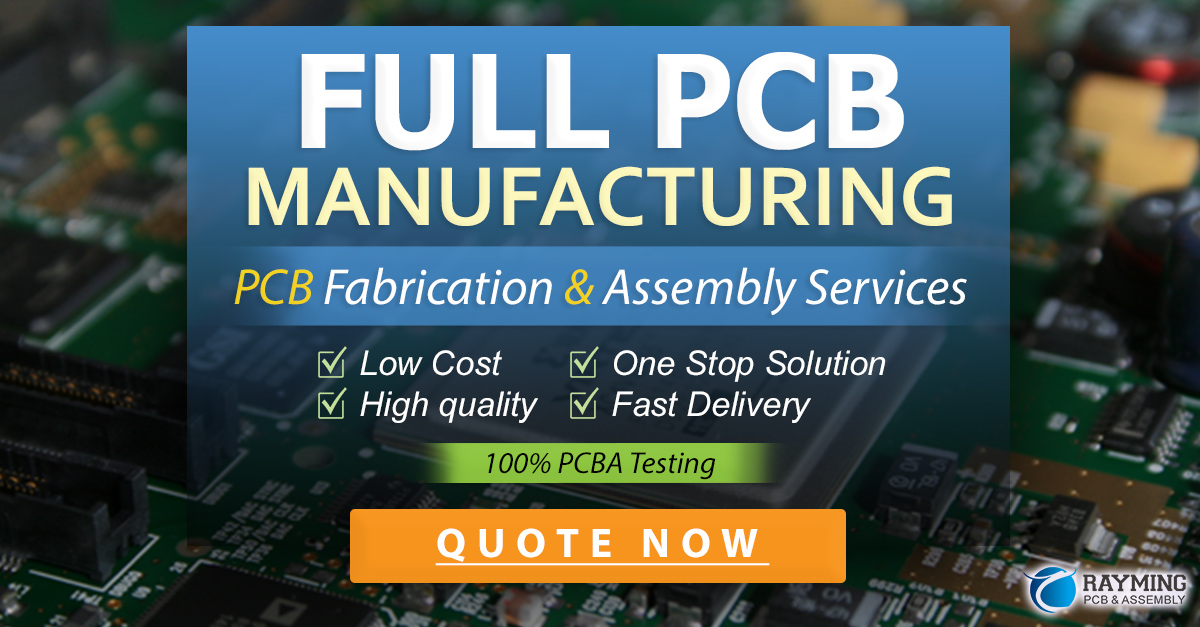
Frequently Asked Questions (FAQ)
-
What is the difference between carbon ink PCBs and traditional PCBs?
Carbon ink PCBs are printed using conductive carbon ink on flexible substrates, while traditional PCBs are fabricated using copper traces on rigid substrates. Carbon ink PCBs are more flexible, lightweight, and low-cost than traditional PCBs. -
What are the advantages of using one-stop PCB assembly?
One-stop PCB assembly can save time and money by combining manufacturing and assembly into a single process. It can also improve communication, quality, and turnaround time by having a single point of contact for the entire project. -
What industries use carbon ink PCBs?
Carbon ink PCBs are used in a variety of industries, including wearable devices, IoT, RFID, and flexible displays. They are particularly well-suited for applications that require flexibility, low cost, and rapid prototyping. -
How do I choose a one-stop PCB assembly provider?
When choosing a one-stop PCB assembly provider, look for experience, capabilities, quality control, and customer service. Make sure that the provider has the necessary expertise and equipment to handle your specific project requirements. -
What is the typical turnaround time for one-stop PCB assembly?
The turnaround time for one-stop PCB assembly varies depending on the complexity of the project and the provider’s capabilities. However, one-stop assembly can generally reduce the overall turnaround time compared to using separate vendors for manufacturing and assembly.
Conclusion
Carbon ink PCB manufacturing and one-stop PCB assembly are two innovative technologies that are changing the way PCBs are designed, manufactured, and assembled. Carbon ink PCBs offer several advantages over traditional PCBs, including flexibility, low cost, and environmental friendliness. One-stop PCB assembly can save time and money by combining manufacturing and assembly into a single, streamlined process.
As the electronics industry continues to evolve, it is likely that we will see more adoption of these technologies in a variety of applications. From wearable devices to IoT sensors, carbon ink PCBs and one-stop assembly have the potential to revolutionize the way we design and manufacture electronic devices.
If you are considering using carbon ink PCBs or one-stop assembly for your next project, be sure to choose a provider with the necessary experience, capabilities, and quality control processes in place. With the right partner, you can take advantage of these innovative technologies to create high-quality, reliable PCBs faster and more cost-effectively than ever before.
No responses yet