What are PCBs?
PCBs are flat boards composed of alternating layers of conductive and insulating materials. These layers allow electrical signals to travel between components without interference. PCBs come in various types, including:
- Single-sided PCBs
- Double-sided PCBs
- Multi-layer PCBs
- Flexible PCBs
- Rigid-flex PCBs
Each type serves different purposes based on the complexity and requirements of the electronic device.
The Core Materials of PCBs
While PCBs may incorporate plastic components, the core materials are typically:
Substrate Material
The substrate is the foundation of the PCB, providing a stable base for the conductive layers and components. The most common substrate materials are:
-
FR-4 (Flame Retardant 4): A composite material made of woven fiberglass cloth with an epoxy resin binder. FR-4 is the most widely used substrate due to its excellent mechanical, electrical, and thermal properties.
-
CEM-1 (Composite Epoxy Material 1): A composite of woven fiberglass cloth and cellulose paper impregnated with epoxy resin. CEM-1 is a lower-cost alternative to FR-4 but has inferior performance.
-
Polyimide: A high-performance polymer known for its excellent thermal stability, chemical resistance, and flexibility. Polyimide is often used in flexible PCBs.
-
PTFE (Polytetrafluoroethylene): Also known as Teflon, PTFE is a high-performance plastic with excellent dielectric properties and thermal stability. It is used in high-frequency and microwave applications.
Substrate Material | Composition | Key Properties |
---|---|---|
FR-4 | Fiberglass and epoxy resin | Excellent mechanical and electrical properties |
CEM-1 | Fiberglass, paper, and epoxy | Lower cost, inferior to FR-4 |
Polyimide | High-performance polymer | Thermally stable, chemically resistant, flexible |
PTFE (Teflon) | Fluoropolymer | Excellent dielectric and thermal properties |
Copper Foil
Copper foil is laminated onto the substrate to create the conductive layers of the PCB. The thickness of the copper foil is measured in ounces per square foot (oz/ft²), with common thicknesses ranging from 0.5 oz/ft² to 2 oz/ft². The copper foil is etched to create the desired circuit pattern.
Solder Mask
A solder mask is a thin layer of polymer applied over the copper traces, leaving only the exposed pads for soldering. The solder mask serves several purposes:
- Protects the copper traces from oxidation and corrosion
- Prevents solder bridges between closely spaced pads
- Provides electrical insulation
- Improves the aesthetics of the PCB
Solder masks are typically green but can be found in other colors like red, blue, and black.
Silkscreen
The silkscreen is a layer of ink applied on top of the solder mask to add text, logos, and component identifiers. This helps with assembly and troubleshooting. White ink is the most common, but other colors are available.
The Role of Plastic in PCBs
While plastic is not the primary material in PCBs, it does play a role in several aspects:
Substrate Material
As mentioned earlier, some substrate materials like Polyimide and PTFE are plastics. These high-performance plastics offer unique properties that make them suitable for specific applications.
Solder Mask
The solder mask is a thin layer of polymer, which is a type of plastic. The most common solder mask material is Liquid Photoimageable (LPI) solder mask, which is a photopolymer that can be patterned using photolithography.
Component Packaging
Many electronic components mounted on PCBs are packaged in plastic. Common package types include:
- Dual Inline Package (DIP)
- Small Outline Integrated Circuit (SOIC)
- Quad Flat Package (QFP)
- Ball Grid Array (BGA)
These plastic packages protect the delicate components and provide a standardized form factor for automated assembly.
Connectors and Housings
PCBs often interface with other devices through connectors, many of which have plastic housings. These housings provide insulation, mechanical support, and protection for the electrical contacts.
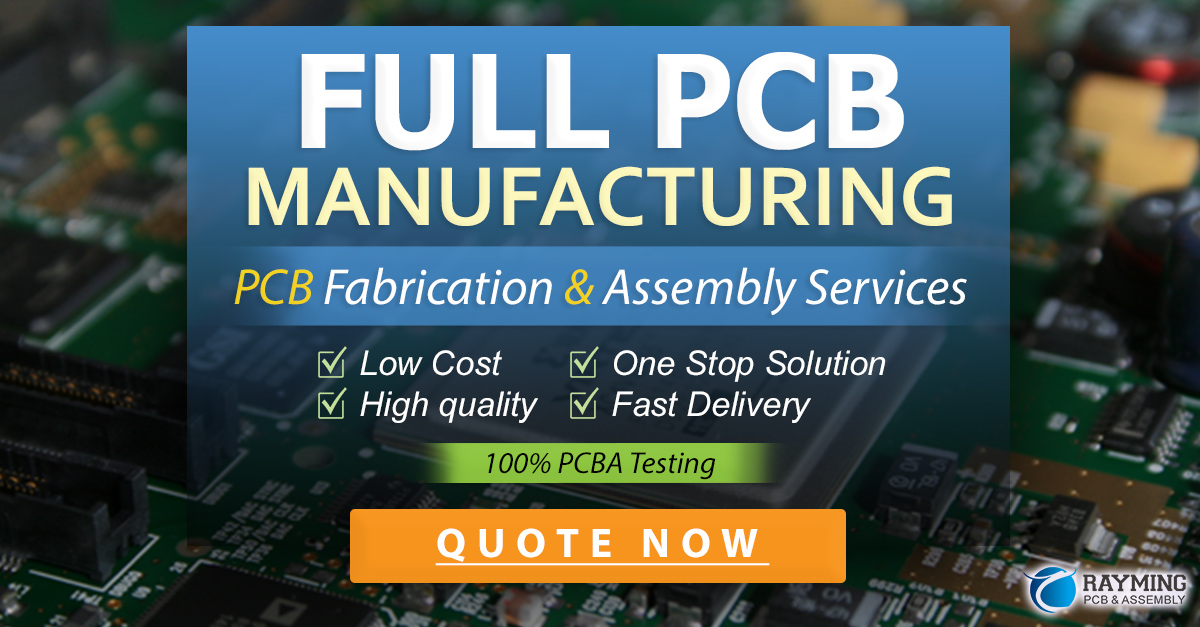
FAQ
Q1: Are PCBs biodegradable?
A1: Traditional PCBs are not biodegradable due to the use of non-biodegradable materials like fiberglass, epoxy, and metal. However, research is ongoing to develop biodegradable PCBs using materials like cellulose and protein-based polymers.
Q2: Can PCBs be recycled?
A2: Yes, PCBs can be recycled to recover valuable materials like copper, gold, and silver. However, the process is complex and requires specialized facilities to handle the toxic chemicals and byproducts.
Q3: Are PCBs environmentally friendly?
A3: Traditional PCBs have a significant environmental impact due to the use of toxic chemicals in manufacturing and the difficulty of recycling. However, the industry is making efforts to develop more eco-friendly materials and processes, such as halogen-free flame retardants and lead-free solders.
Q4: Can PCBs be made at home?
A4: While it is possible to make simple PCBs at home using methods like etching or milling, the process requires specialized equipment, chemicals, and knowledge. Home-made PCBs are typically limited in complexity and quality compared to professionally manufactured ones.
Q5: How long do PCBs last?
A5: The lifespan of a PCB depends on various factors, including the quality of materials, manufacturing process, and operating environment. A well-designed and manufactured PCB can last for decades under proper conditions. However, exposure to extreme temperatures, humidity, vibration, or chemical contamination can significantly reduce the lifespan.
Conclusion
In conclusion, while plastic plays a role in certain aspects of PCBs, such as substrate materials, solder masks, component packaging, and connectors, it is not the primary material. The core of a PCB consists of a substrate material, typically FR-4, with copper foil laminated onto it to create the conductive layers. The plastic components serve to protect, insulate, and provide mechanical support to the PCB and its components.
As the electronics industry continues to evolve, there is a growing focus on developing more environmentally friendly materials and processes for PCBs. This includes the use of biodegradable and recyclable plastics, as well as the elimination of toxic chemicals in manufacturing. By understanding the composition of PCBs and the role of plastic in their construction, we can work towards creating more sustainable and eco-friendly electronic devices.
No responses yet