What is FR4?
FR4 is a composite material made up of woven fiberglass cloth with an epoxy resin binder. The “FR” in FR4 stands for “Flame Retardant,” indicating that the material has been treated to resist the spread of flames in case of a fire. The “4” in FR4 refers to the woven glass reinforcement used in the material, which is a type of electrical-grade fiberglass.
FR4 is known for its excellent mechanical, thermal, and electrical properties, making it an ideal choice for PCB substrates. Some of the key properties of FR4 include:
- High dielectric strength
- Low moisture absorption
- Good thermal stability
- Excellent mechanical strength
- Flame retardancy
Composition of FR4
FR4 is composed of two main components: woven fiberglass cloth and epoxy resin. The fiberglass cloth provides the mechanical strength and dimensional stability to the laminate, while the epoxy resin acts as a binder and provides the necessary electrical insulation.
The typical composition of FR4 is as follows:
Component | Percentage |
---|---|
Woven fiberglass cloth | 40-60% |
Epoxy resin | 40-60% |
The exact composition of FR4 can vary depending on the manufacturer and the specific application requirements.
Manufacturing Process of FR4 PCBs
The manufacturing process of FR4 PCBs involves several steps, including:
-
Preparing the substrate: The FR4 substrate is cut to the desired size and shape, and any necessary holes are drilled.
-
Applying the copper foil: A thin layer of copper foil is laminated onto the FR4 substrate using heat and pressure.
-
Patterning the copper: The desired circuit pattern is transferred onto the copper layer using a photoresist and etching process.
-
Applying the solder mask: A layer of solder mask is applied over the copper traces to protect them from oxidation and short circuits.
-
Applying the silkscreen: A silkscreen layer is applied to the PCB to provide labeling and identification of components.
-
Surface finishing: The exposed copper areas are coated with a surface finish, such as HASL (Hot Air Solder Leveling) or ENIG (Electroless Nickel Immersion Gold), to protect them from oxidation and improve solderability.
Advantages of using FR4 in PCBs
FR4 offers several advantages when used as a PCB substrate material:
-
Excellent electrical insulation: FR4 has a high dielectric strength, which helps to prevent electrical leakage and short circuits.
-
Good mechanical strength: The woven fiberglass reinforcement in FR4 provides excellent mechanical strength and dimensional stability, making it resistant to warping and twisting.
-
Flame retardancy: FR4 is treated with flame retardants, which help to prevent the spread of flames in case of a fire.
-
Wide operating temperature range: FR4 has a glass transition temperature (Tg) of around 130°C to 140°C, allowing it to maintain its properties over a wide temperature range.
-
Cost-effective: FR4 is a relatively inexpensive material compared to other high-performance PCB substrates, making it a cost-effective choice for many applications.
FR4 Grades and Variations
FR4 is available in various grades and variations, each with slightly different properties to suit specific application requirements. Some common variations of FR4 include:
-
High Tg FR4: This variation of FR4 has a higher glass transition temperature (Tg) of around 170°C to 180°C, making it suitable for high-temperature applications.
-
Halogen-free FR4: This variation of FR4 uses halogen-free flame retardants, making it more environmentally friendly and compliant with RoHS (Restriction of Hazardous Substances) regulations.
-
Low-loss FR4: This variation of FR4 has a lower dielectric constant and dissipation factor, making it suitable for high-frequency applications.
-
Controlled impedance FR4: This variation of FR4 is designed to have a specific dielectric constant and thickness, allowing for the precise control of impedance in high-speed digital circuits.
Comparison of FR4 with other PCB materials
While FR4 is the most common PCB substrate material, there are other materials available for specific applications. Some of these materials include:
-
Polyimide: Polyimide is a high-performance polymer with excellent thermal stability and chemical resistance, making it suitable for harsh environments and high-temperature applications.
-
PTFE (Teflon): PTFE is a low-loss dielectric material with excellent high-frequency performance, making it suitable for RF and microwave applications.
-
Aluminum: Aluminum PCBs are used in applications that require high thermal conductivity, such as LED lighting and power electronics.
Property | FR4 | Polyimide | PTFE | Aluminum |
---|---|---|---|---|
Dielectric Constant | 4.5 | 3.5 | 2.1 | – |
Dissipation Factor | 0.02 | 0.003 | 0.0004 | – |
Thermal Conductivity (W/mK) | 0.3 | 0.2 | 0.2 | 150 |
Max. Operating Temperature (°C) | 130-140 | 260 | 260 | 150 |
Relative Cost | Low | High | High | Medium |
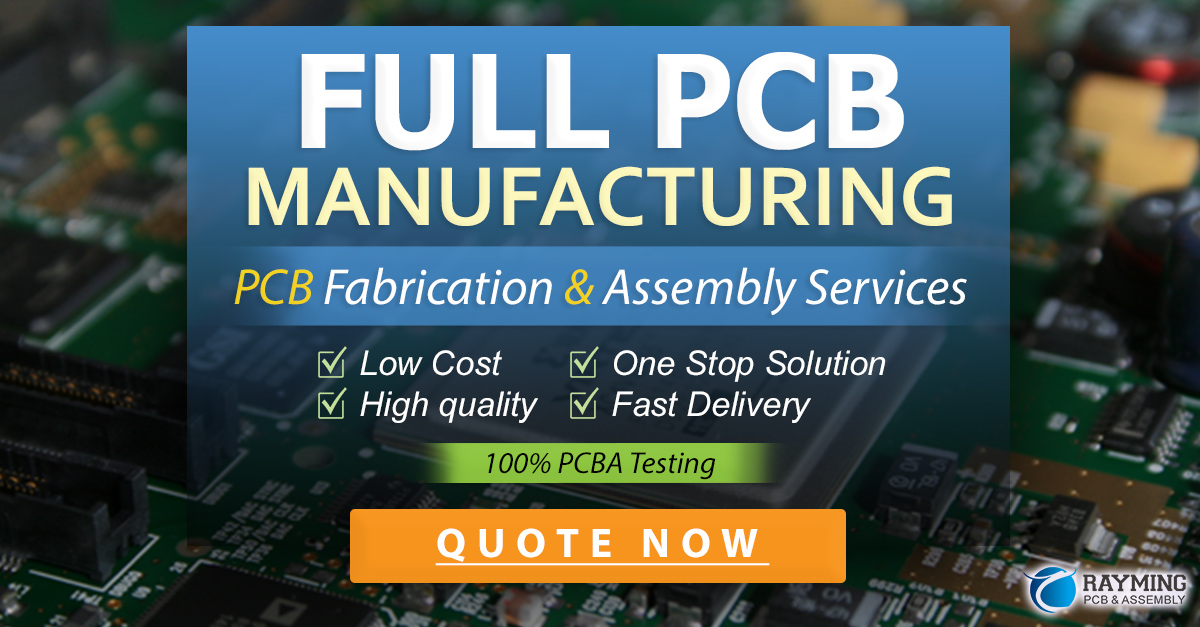
Applications of FR4 PCBs
FR4 PCBs are used in a wide range of applications across various industries, including:
-
Consumer electronics: FR4 is used in the production of PCBs for smartphones, laptops, televisions, and other consumer electronic devices.
-
Automotive electronics: FR4 PCBs are used in various automotive electronic systems, such as engine control units, infotainment systems, and advanced driver assistance systems (ADAS).
-
Industrial electronics: FR4 is used in the production of PCBs for industrial control systems, automation equipment, and power electronics.
-
Medical devices: FR4 PCBs are used in the production of medical electronic devices, such as patient monitors, diagnostic equipment, and implantable devices.
-
Aerospace and defense: FR4 is used in the production of PCBs for aerospace and defense applications, such as avionics, radar systems, and communication equipment.
FAQs
-
Q: Is FR4 the only material used for PCBs?
A: No, while FR4 is the most common material used for PCBs, other materials such as polyimide, PTFE, and aluminum are also used for specific applications. -
Q: Can FR4 PCBs be used in high-temperature applications?
A: Standard FR4 has a glass transition temperature (Tg) of around 130°C to 140°C. For higher temperature applications, high Tg FR4 with a Tg of 170°C to 180°C can be used. -
Q: Are FR4 PCBs environmentally friendly?
A: Standard FR4 uses halogenated flame retardants, which can be harmful to the environment. However, halogen-free FR4 variations are available that use environmentally friendly flame retardants and comply with RoHS regulations. -
Q: Can FR4 PCBs be used for high-frequency applications?
A: While FR4 is suitable for most general-purpose applications, it may not be the best choice for high-frequency applications due to its relatively high dielectric constant and dissipation factor. For high-frequency applications, low-loss materials like PTFE are often preferred. -
Q: How does the cost of FR4 compare to other PCB materials?
A: FR4 is relatively inexpensive compared to other high-performance PCB materials like polyimide and PTFE, making it a cost-effective choice for many applications.
Conclusion
FR4 is the most common material used in the production of PCBs, thanks to its excellent mechanical, thermal, and electrical properties. Its low cost, good performance, and wide availability make it the go-to choice for a wide range of applications, from consumer electronics to aerospace and defense.
While FR4 may not be the best choice for every application, its versatility and reliability have made it an essential material in the world of electronic manufacturing. As PCB technology continues to evolve, it is likely that FR4 will remain a key player in the industry, alongside new and innovative materials that push the boundaries of performance and functionality.
No responses yet