What is PCB Lamination?
PCB lamination is a critical step in the Printed Circuit Board manufacturing process where multiple layers of the PCB are bonded together under high temperature and pressure to form a single, solid board. The lamination process creates a strong, stable, and electrically insulated foundation for the subsequent etching, drilling, and component assembly stages.
RAYPCB, a leading PCB Manufacturer, employs state-of-the-art lamination techniques to ensure the highest quality and reliability of their circuit boards. In this article, we will delve into the details of the PCB lamination process, its importance, and the key factors that contribute to a successful lamination outcome.
The Importance of PCB Lamination
PCB lamination plays a crucial role in the overall performance and longevity of a printed circuit board. A well-executed lamination process offers several benefits:
-
Mechanical Strength: Lamination bonds the layers together, creating a sturdy and durable board that can withstand physical stress and vibrations.
-
Electrical Insulation: The lamination process ensures proper insulation between the conductive layers, preventing short circuits and signal interference.
-
Dimensional Stability: Lamination helps maintain the board’s flatness and prevents warping, which is essential for accurate component placement and soldering.
-
Thermal conductivity: A well-laminated board allows for efficient heat dissipation, preventing overheating and ensuring the long-term reliability of the components.
The PCB Lamination Process at RAYPCB
RAYPCB follows a meticulous lamination process to guarantee the best possible results. The process involves several key steps:
1. Material Preparation
The first step in the lamination process is to prepare the materials. This includes:
- Copper Foil: Thin sheets of copper are cleaned and treated to ensure optimal adhesion to the prepreg material.
- Prepreg: Prepreg (pre-impregnated) is a fiberglass cloth pre-coated with a partially cured epoxy resin. It serves as the insulating layer between the copper foils.
- Core Layers: For multi-layer boards, previously laminated and etched core layers are used.
2. Layup
The layup process involves stacking the prepared materials in the proper sequence. The stack typically consists of alternating layers of copper foil, prepreg, and core layers (if applicable). The arrangement of these layers determines the final thickness and functionality of the PCB.
Layer Type | Function |
---|---|
Copper Foil | Conductive layer for electrical connections |
Prepreg | Insulating layer between copper foils |
Core Layer | Previously laminated and etched layers for multi-layer boards |
3. Lamination Press
Once the layers are stacked, they are placed in a lamination press. The press applies heat and pressure to the stack, causing the epoxy resin in the prepreg to flow and bond the layers together. The lamination process typically involves the following parameters:
- Temperature: The press heats the stack to a specific temperature, usually between 180°C and 200°C, depending on the type of prepreg used.
- Pressure: A uniform pressure, ranging from 200 to 400 psi, is applied to ensure proper bonding and to remove any air pockets between the layers.
- Time: The lamination time varies based on the board thickness and the prepreg type, but it generally ranges from 1 to 2 hours.
Parameter | Typical Range |
---|---|
Temperature | 180°C – 200°C |
Pressure | 200 – 400 psi |
Time | 1 – 2 hours |
4. Cooling
After the lamination cycle is complete, the press slowly cools down the laminated board to room temperature. The cooling process must be gradual to prevent thermal shock and to allow the epoxy resin to fully cure and solidify.
5. Inspection
Once the laminated board has cooled, it undergoes a thorough inspection to ensure its quality. This includes checking for:
- Delamination: Any separation between the layers is a critical defect that can lead to electrical and mechanical failures.
- Warpage: Excessive warping can cause difficulties in subsequent manufacturing processes and affect the board’s functionality.
- Thickness: The board’s thickness is measured to verify that it meets the specified tolerances.
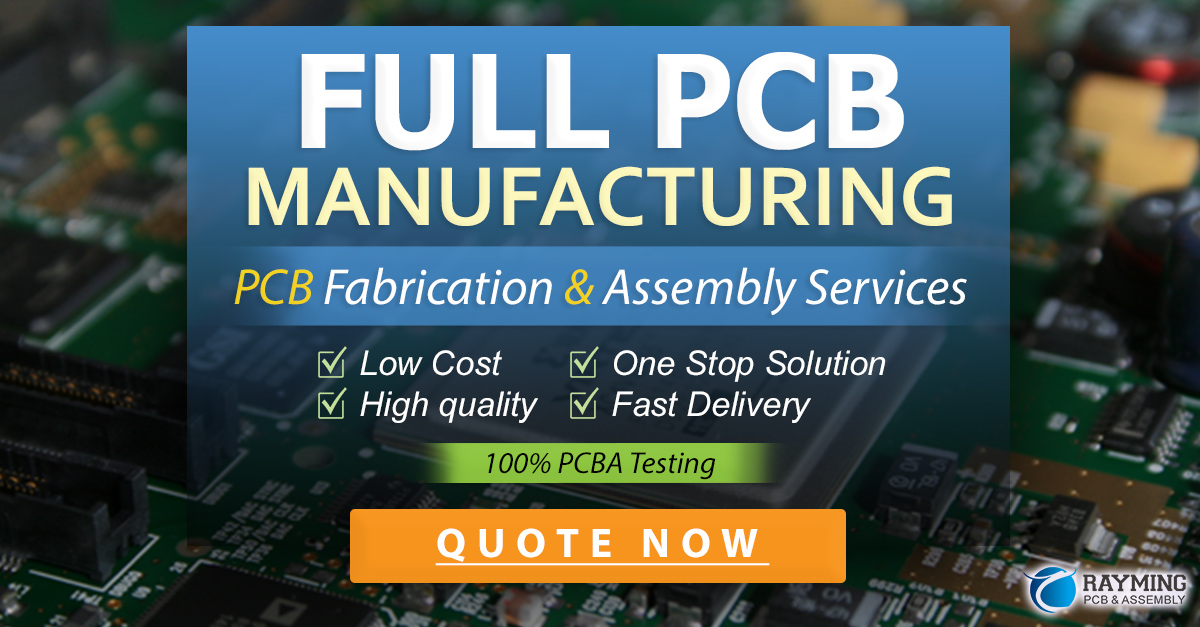
Factors Affecting PCB Lamination Quality
Several factors can influence the quality of the lamination process and the resulting PCB. RAYPCB carefully controls these factors to maintain the highest standards:
1. Material Selection
Choosing the right materials is essential for a successful lamination. Factors to consider include:
- Prepreg Type: Different prepregs have varying flow characteristics, curing temperatures, and dielectric properties. Selecting the appropriate prepreg ensures proper bonding and electrical insulation.
- Copper Foil Thickness: The copper foil thickness affects the board’s electrical properties and the lamination process. Thinner foils require less pressure and heat to achieve adequate bonding.
- Core Layer Quality: For multi-layer boards, the quality of the core layers directly impacts the final laminated board’s performance.
2. Layup Accuracy
Precise layup is critical for achieving the desired board thickness and functionality. Any misalignment or incorrect stacking can lead to defects and performance issues.
3. Press Parameters
The lamination press parameters, such as temperature, pressure, and time, must be carefully controlled to ensure optimal bonding and to prevent defects like delamination or excessive resin flow.
4. Cleanliness
Maintaining a clean environment during the lamination process is crucial. Any contaminants, such as dust or oils, can interfere with the bonding process and lead to defects.
Frequently Asked Questions (FAQ)
-
Q: What is the difference between prepreg and core layers in PCB lamination?
A: Prepreg is a fiberglass cloth pre-coated with partially cured epoxy resin, which serves as the insulating layer between copper foils. Core layers are previously laminated and etched layers used in multi-layer boards. -
Q: How does the lamination process affect the electrical properties of a PCB?
A: Lamination ensures proper insulation between the conductive layers, preventing short circuits and signal interference. A well-laminated board also allows for efficient heat dissipation, which is essential for the long-term reliability of the components. -
Q: What is the typical temperature range for PCB lamination?
A: The typical temperature range for PCB lamination is between 180°C and 200°C, depending on the type of prepreg used. -
Q: How long does the PCB lamination process take?
A: The lamination time varies based on the board thickness and the prepreg type, but it generally ranges from 1 to 2 hours. -
Q: What are some common defects that can occur during PCB lamination?
A: Some common defects that can occur during PCB lamination include delamination (separation between layers), warpage (excessive board curvature), and thickness variations.
Conclusion
PCB lamination is a vital step in the printed Circuit board manufacturing process, ensuring the mechanical strength, electrical insulation, and dimensional stability of the final product. RAYPCB’s commitment to using the best materials, state-of-the-art equipment, and strict process controls guarantees the highest quality lamination for their customers.
By understanding the importance of lamination, the key steps involved, and the factors that influence the process, designers and engineers can work closely with RAYPCB to create reliable, high-performance printed circuit boards for a wide range of applications.
No responses yet