What is a Rigid-Flex PCB?
A Rigid-Flex PCB, also known as a flexible printed circuit board, is a unique type of circuit board that combines the features of both rigid and flexible PCBs. It consists of multiple layers of flexible PCB substrates, such as polyimide or polyester, interconnected by plated through-holes (PTHs) and integrated with rigid PCB sections. This hybrid design enables the board to be bent, folded, or twisted to fit into compact spaces or conform to specific shapes, making it ideal for applications that require flexibility, reliability, and space efficiency.
Key features of Rigid-Flex PCBs
- Combination of rigid and flexible sections
- Multiple layers of flexible substrates
- Interconnected by plated through-holes
- Ability to bend, fold, or twist
- High reliability and space efficiency
Structure of a Rigid-Flex PCB
A Rigid-Flex PCB consists of several layers of different materials, each serving a specific purpose. The main components of a Rigid-Flex PCB include:
1. Flexible Substrate
The flexible substrate is the foundation of the Rigid-Flex PCB. It is typically made of polyimide or polyester, which are known for their excellent flexibility, thermal stability, and dielectric properties. The substrate is usually thin, ranging from 0.051 mm to 0.127 mm (2 to 5 mils), allowing for easy bending and folding.
2. Copper Layers
Copper layers are laminated onto the flexible substrate to create the conductive pathways for electrical signals. The number of copper layers can vary depending on the complexity of the design, but it is common to have two to six layers in a Rigid-Flex PCB. The copper thickness typically ranges from 17.5 μm to 70 μm (0.5 oz to 2 oz).
3. Adhesive Layers
Adhesive layers are used to bond the copper layers to the flexible substrate. These layers are typically made of acrylic or epoxy-based materials and provide a strong, reliable bond between the layers.
4. Coverlay
The coverlay is a protective layer that covers the outer copper layers of the flexible sections. It is usually made of polyimide or polyester and serves to insulate and protect the copper traces from damage and environmental factors.
5. Rigid Sections
The rigid sections of a Rigid-Flex PCB are made of standard FR-4 material, similar to traditional rigid PCBs. These sections provide mechanical support and stability to the flexible sections and house components that require a stable base, such as connectors, switches, and large ICs.
6. Plated Through-Holes (PTHs)
PTHs are used to interconnect the layers of the Rigid-Flex PCB and provide electrical continuity between the rigid and flexible sections. They are drilled through the entire stack-up of the board and plated with copper to create a conductive path.
Layer | Material | Thickness Range |
---|---|---|
Flexible Substrate | Polyimide or Polyester | 0.051 mm – 0.127 mm |
Copper Layers | Copper | 17.5 μm – 70 μm |
Adhesive Layers | Acrylic or Epoxy-based | 0.025 mm – 0.051 mm |
Coverlay | Polyimide or Polyester | 0.025 mm – 0.051 mm |
Rigid Sections | FR-4 | 0.2 mm – 1.6 mm |
Benefits of Rigid-Flex PCBs
Rigid-Flex PCBs offer several advantages over traditional rigid PCBs, making them an attractive option for many applications:
1. Space Savings
By combining rigid and flexible sections, Rigid-Flex PCBs can be designed to fit into compact spaces and conform to specific shapes, reducing the overall size and weight of the device. This is particularly beneficial for portable electronic devices, such as smartphones, tablets, and wearables.
2. Increased Reliability
The flexible sections of a Rigid-Flex PCB can absorb stress and vibrations, reducing the risk of mechanical failures caused by repeated bending or twisting. Additionally, the elimination of connectors and wires between rigid sections improves signal integrity and reduces the potential for connection-related failures.
3. Improved Signal Integrity
Rigid-Flex PCBs offer better signal integrity compared to traditional rigid PCBs with separate flexible interconnects. By eliminating connectors and wires, the signal path is shorter and more direct, reducing noise, crosstalk, and electromagnetic interference (EMI).
4. Simplified Assembly
With Rigid-Flex PCBs, the number of interconnects and connectors is reduced, simplifying the assembly process and minimizing the risk of human error. This can lead to faster production times, lower assembly costs, and improved overall reliability.
5. Design Flexibility
Rigid-Flex PCBs allow for greater design flexibility, as the flexible sections can be bent, folded, or twisted to accommodate unique form factors and space constraints. This enables designers to create more innovative and compact devices without sacrificing functionality or reliability.
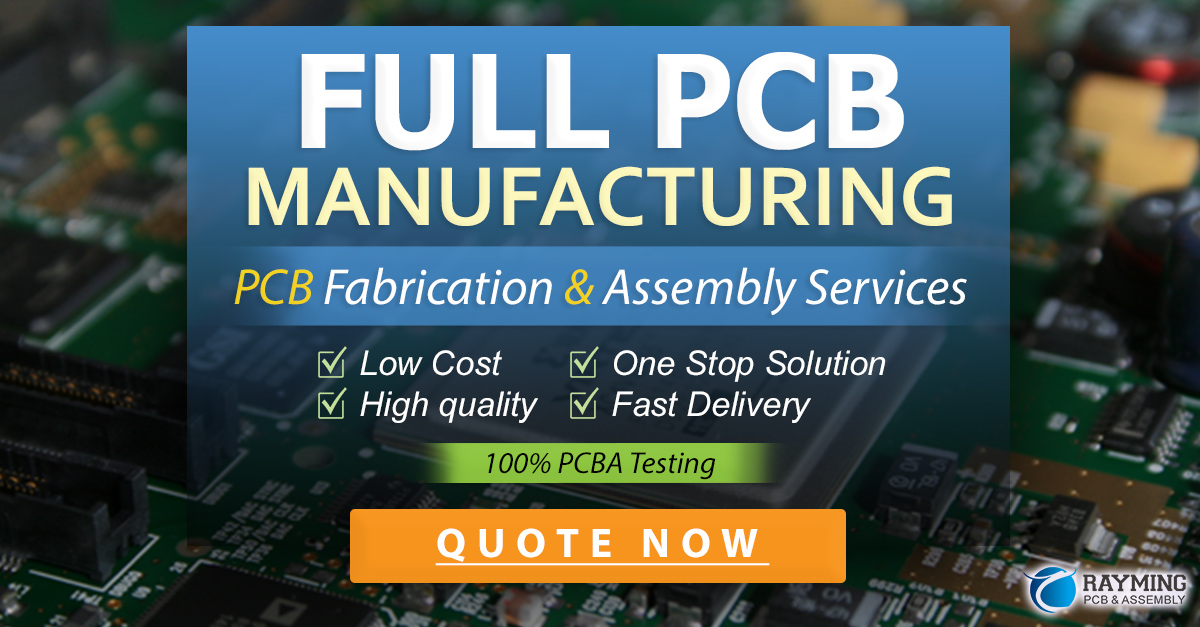
Applications of Rigid-Flex PCBs
Rigid-Flex PCBs are used in a wide range of industries and applications, including:
1. Consumer Electronics
Smartphones, tablets, laptops, wearables, and other portable devices often employ Rigid-Flex PCBs to achieve compact designs and improve reliability.
2. Aerospace and Defense
Rigid-Flex PCBs are used in aerospace and defense applications, such as satellites, aircraft, and military equipment, where space savings, reliability, and environmental resistance are critical.
3. Medical Devices
Medical devices, such as implantable sensors, wearable monitors, and surgical instruments, benefit from the compact size and reliability of Rigid-Flex PCBs.
4. Automotive Electronics
Rigid-Flex PCBs are used in automotive electronics, such as infotainment systems, driver assistance systems, and vehicle controls, where space constraints and reliability are important factors.
5. Industrial Equipment
Industrial equipment, such as robotics, automation systems, and process control devices, can utilize Rigid-Flex PCBs to reduce size, improve reliability, and simplify assembly.
Costs of Rigid-Flex PCBs
The cost of Rigid-Flex PCBs is generally higher compared to traditional rigid PCBs due to the more complex manufacturing process and the use of specialized materials. Several factors contribute to the overall cost of a Rigid-Flex PCB:
1. Material Costs
The flexible substrates, adhesives, and coverlays used in Rigid-Flex PCBs are more expensive than the materials used in traditional rigid PCBs. Additionally, the use of high-performance materials, such as polyimide, can further increase the material costs.
2. Manufacturing Complexity
The manufacturing process for Rigid-Flex PCBs is more complex and time-consuming compared to rigid PCBs. It involves additional steps, such as laminating flexible layers, creating the rigid-to-flex transition areas, and applying coverlays. This increased complexity contributes to higher manufacturing costs.
3. Design Complexity
The design of Rigid-Flex PCBs is more challenging than traditional rigid PCBs due to the need to account for the flexible sections and the transition areas between rigid and flexible sections. This often requires specialized design software and expertise, which can add to the overall cost.
4. Volume and Quantity
As with most PCBs, the cost per unit of Rigid-Flex PCBs decreases as the order quantity increases. However, due to the higher material and manufacturing costs, the cost reduction may not be as significant as with traditional rigid PCBs.
Despite the higher costs, the benefits of Rigid-Flex PCBs, such as space savings, improved reliability, and design flexibility, often justify the investment for many applications. As the demand for compact and reliable electronic devices continues to grow, the use of Rigid-Flex PCBs is expected to increase, which may lead to more competitive pricing in the future.
Choosing a Rigid-Flex PCB Manufacturer
When selecting a Rigid-Flex PCB manufacturer, it is essential to consider several factors to ensure that you receive high-quality boards that meet your specific requirements:
1. Experience and Expertise
Look for a manufacturer with extensive experience in producing Rigid-Flex PCBs. They should have a deep understanding of the unique challenges associated with designing and manufacturing these boards and be able to provide guidance and support throughout the process.
2. Manufacturing Capabilities
Ensure that the manufacturer has the necessary equipment and facilities to produce Rigid-Flex PCBs that meet your specifications. This includes the ability to handle the required layer counts, material types, and feature sizes.
3. Quality Control
A reliable Rigid-Flex PCB manufacturer should have robust quality control processes in place to ensure that the boards meet the highest standards of quality and reliability. This may include inspections at various stages of the manufacturing process, as well as electrical and mechanical testing.
4. Certifications and Standards
Look for a manufacturer that holds relevant industry certifications, such as ISO 9001, IATF 16949, or AS9100, which demonstrate their commitment to quality and adherence to established standards.
5. Customer Support and Communication
Choose a manufacturer that provides excellent customer support and maintains clear communication throughout the design and manufacturing process. They should be responsive to your inquiries, provide regular updates on your project status, and be willing to work with you to address any issues that may arise.
6. Pricing and Lead Times
While cost is an important consideration, it should not be the sole deciding factor when choosing a Rigid-Flex PCB manufacturer. Strike a balance between competitive pricing and the assurance of high-quality boards delivered within acceptable lead times.
By carefully evaluating potential Rigid-Flex PCB manufacturers based on these criteria, you can select a partner that will help you bring your designs to life with the highest quality and reliability.
Frequently Asked Questions (FAQ)
1. What is the minimum bend radius for a Rigid-Flex PCB?
The minimum bend radius for a Rigid-Flex PCB depends on several factors, including the thickness of the flexible substrate, the number of copper layers, and the type of materials used. As a general rule, the minimum bend radius is typically 6 to 10 times the total thickness of the flexible section.
2. Can Rigid-Flex PCBs be used in high-temperature environments?
Yes, Rigid-Flex PCBs can be designed to withstand high-temperature environments. This is achieved by using high-temperature materials, such as polyimide, which can maintain its mechanical and electrical properties at elevated temperatures.
3. How does the layer count affect the cost of a Rigid-Flex PCB?
The layer count is one of the main factors that influence the cost of a Rigid-Flex PCB. As the number of layers increases, the complexity of the manufacturing process also increases, leading to higher costs. Additionally, higher layer counts may require more expensive materials and more advanced manufacturing equipment.
4. Are Rigid-Flex PCBs suitable for high-frequency applications?
Yes, Rigid-Flex PCBs can be designed for high-frequency applications. By careful selection of materials, optimizing the layer stack-up, and implementing proper signal integrity techniques, Rigid-Flex PCBs can provide excellent high-frequency performance.
5. How long does it typically take to manufacture a Rigid-Flex PCB?
The lead time for manufacturing a Rigid-Flex PCB can vary depending on the complexity of the design, the selected materials, and the manufacturer’s workload. On average, lead times can range from 2 to 6 weeks, but it is best to consult with your chosen manufacturer for a more accurate estimate based on your specific project requirements.
Conclusion
Rigid-Flex PCBs offer a unique combination of flexibility, reliability, and space efficiency, making them an attractive option for a wide range of industries and applications. By understanding the structure, benefits, and costs associated with Rigid-Flex PCBs, designers and engineers can make informed decisions when considering this technology for their projects.
When selecting a Rigid-Flex PCB manufacturer, it is crucial to choose a partner with the experience, capabilities, and commitment to quality that will help bring your designs to fruition. By working closely with your manufacturer and leveraging the advantages of Rigid-Flex PCBs, you can create innovative, compact, and reliable electronic devices that meet the demands of today’s competitive market.
No responses yet