Introduction to Aluminum PCBs and Their Manufacturing Process
Aluminum PCBs, also known as metal core PCBs (MCPCBs), are a type of printed circuit board that utilizes an aluminum substrate instead of the traditional FR-4 material. These PCBs are designed to provide excellent thermal management and heat dissipation properties, making them ideal for applications that generate significant amounts of heat, such as high-power LED lighting, automotive electronics, and power converters.
In this article, we will delve into the manufacturing process of aluminum PCBs in a PCB factory, discussing the various steps involved, the equipment used, and the quality control measures implemented to ensure the production of high-quality boards.
Advantages of Aluminum PCBs
Before we explore the manufacturing process, let’s briefly discuss the advantages of aluminum PCBs:
- Enhanced thermal conductivity: Aluminum substrates have a much higher thermal conductivity compared to FR-4, allowing for efficient heat dissipation.
- Improved reliability: By effectively managing heat, aluminum PCBs minimize the risk of component failure due to thermal stress, thereby increasing the overall reliability of the electronic device.
- Reduced weight and thickness: Aluminum PCBs can be made thinner and lighter than traditional PCBs, making them suitable for space-constrained applications.
- Cost-effective: For high-volume production, aluminum PCBs can be more cost-effective than other thermal management solutions, such as heat sinks or fans.
The Aluminum PCB Manufacturing Process
The manufacturing process of aluminum PCBs involves several critical steps, each of which contributes to the quality and performance of the final product. Let’s examine these steps in detail.
Step 1: Material Selection and Preparation
The first step in the manufacturing process is to select the appropriate materials for the aluminum PCB. The main components include:
- Aluminum substrate: The thickness and grade of the aluminum substrate are chosen based on the specific application requirements, such as the desired thermal conductivity and mechanical strength.
- Dielectric layer: A dielectric layer, typically made of a thermally conductive material like aluminum oxide or boron nitride, is applied to the aluminum substrate to provide electrical insulation.
- Copper foil: A thin layer of copper foil is laminated onto the dielectric layer to create the conductive layer for the PCB.
Once the materials are selected, they are cleaned and prepared for the subsequent manufacturing steps.
Step 2: Circuit Design and Artwork Generation
The circuit design for the aluminum PCB is created using specialized PCB design software, such as Altium Designer or KiCad. The design takes into account the specific requirements of the application, including the component placement, routing, and thermal management considerations.
After the circuit design is finalized, the artwork files are generated, which include the copper layer patterns, solder mask, and silkscreen layers. These files are used to create the photomasks or stencils required for the subsequent fabrication steps.
Step 3: Photoresist Application and Exposure
A photoresist, a light-sensitive polymer, is applied to the copper-clad aluminum substrate. The photoresist can be applied using various methods, such as:
- Dry film lamination: A pre-cut sheet of photoresist is laminated onto the copper surface using heat and pressure.
- Liquid photoresist coating: The board is coated with a liquid photoresist using a spin coater or a dip-and-dwell process.
After the photoresist application, the board is exposed to ultraviolet (UV) light through the photomask, which contains the desired circuit pattern. The UV light hardens the exposed areas of the photoresist, while the unexposed areas remain soluble.
Step 4: Developing and Etching
After exposure, the board is developed using a chemical developer solution, which removes the soluble, unexposed areas of the photoresist. This process reveals the underlying copper layer in the desired circuit pattern.
Next, the board undergoes an etching process, where the exposed copper is removed using a chemical etchant, typically an acidic solution like ferric chloride or ammonium persulfate. The hardened photoresist acts as a protective mask, ensuring that only the unwanted copper is etched away.
Step 5: Photoresist Stripping and Cleaning
Once the etching process is complete, the remaining photoresist is stripped away using a chemical stripper or an alkaline solution. The board is then thoroughly cleaned to remove any residues or contaminants.
Step 6: Solder Mask Application and Legend Printing
A solder mask, a protective layer that covers the copper traces, is applied to the board. The solder mask is typically a green or black polymer that is applied using a screen printing or photoimaging process. Openings in the solder mask are left for the component pads and other features that require soldering.
After the solder mask application, the legend or silkscreen layer is printed onto the board. This layer contains text and symbols that provide information about the components, part numbers, and other relevant details.
Step 7: Surface Finish Application
A surface finish is applied to the exposed copper pads to protect them from oxidation and to enhance the solderability of the board. Common surface finishes for aluminum PCBs include:
- HASL (Hot Air Solder Leveling): A layer of tin-lead alloy is applied to the pads using a hot air leveling process.
- ENIG (Electroless Nickel Immersion Gold): A layer of nickel is deposited onto the pads, followed by a thin layer of gold.
- OSP (Organic Solderability Preservative): A thin, organic coating is applied to the pads to protect them from oxidation.
Step 8: Drilling and Routing
Holes are drilled into the board to accommodate through-hole components and vias. The drilling process is typically performed using computer-controlled drilling machines, which ensure precise hole placement and size.
After drilling, the board outline is routed using a CNC (Computer Numerical Control) router or a laser cutter. This process cuts the board into its final shape and size.
Step 9: Inspection and Quality Control
Throughout the manufacturing process, various inspection and quality control measures are implemented to ensure the consistency and reliability of the aluminum PCBs. Some of these measures include:
- Visual inspection: Boards are visually inspected for defects such as scratches, dents, or discoloration.
- Automated Optical Inspection (AOI): An automated system scans the board for defects in the copper patterns, solder mask, and legend layers.
- Electrical testing: Boards are tested for continuity, insulation resistance, and other electrical properties to ensure proper functionality.
- Thermal conductivity testing: The thermal performance of the aluminum PCBs is evaluated to ensure they meet the specified requirements.
Boards that pass the inspection and quality control tests are packaged and shipped to the customer, while those that fail are either reworked or scrapped, depending on the nature and severity of the defects.
Equipment Used in Aluminum PCB Manufacturing
The manufacturing of aluminum PCBs requires specialized equipment to ensure the precision and quality of the final product. Some of the key pieces of equipment used in a PCB factory include:
- CNC drilling and routing machines: These computer-controlled machines are used for precise drilling and routing of the aluminum PCBs.
- Photoimaging equipment: UV exposure units and developers are used to transfer the circuit pattern onto the photoresist-coated boards.
- Etching equipment: Conveyorized or spray etching machines are used to remove the unwanted copper from the boards.
- Solder mask and legend printing machines: Screen printing or inkjet printing machines are used to apply the solder mask and legend layers to the boards.
- Surface finish application equipment: Depending on the chosen surface finish, equipment such as HASL machines, ENIG plating lines, or OSP coating systems are used.
- Automated Optical Inspection (AOI) systems: These computerized systems scan the boards for defects and ensure the quality of the final product.
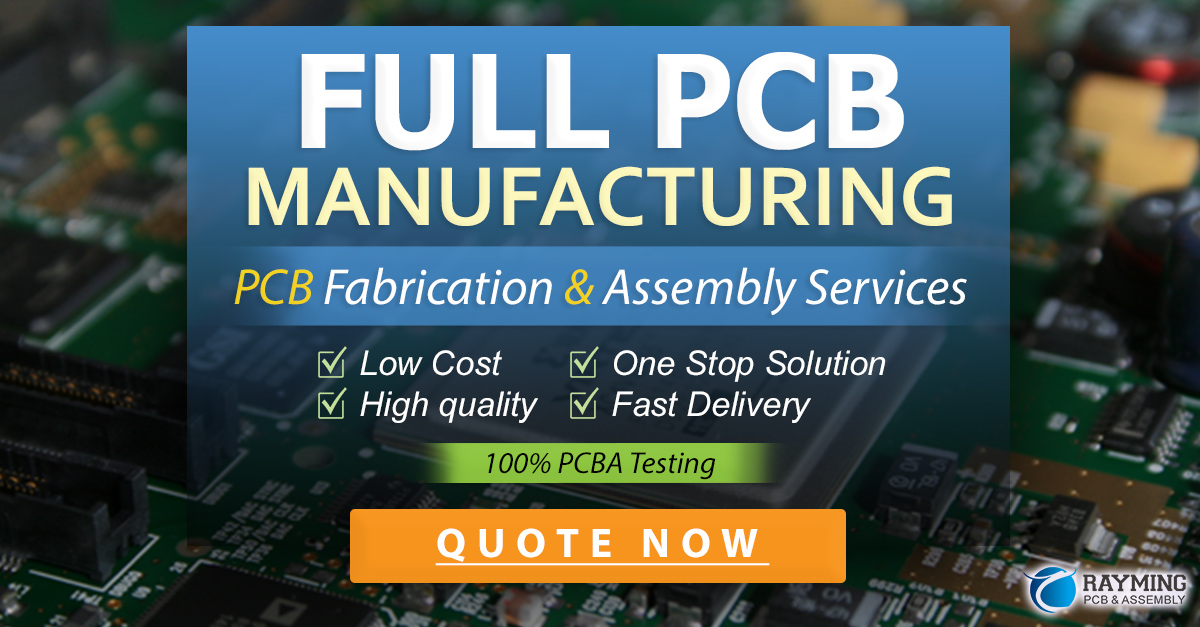
Challenges in Aluminum PCB Manufacturing
While aluminum PCBs offer numerous advantages, their manufacturing process does present some unique challenges compared to traditional FR-4 PCBs:
- Material handling: Aluminum substrates are more prone to scratches and dents during handling, requiring extra care throughout the manufacturing process.
- Thermal expansion: Aluminum has a higher coefficient of thermal expansion (CTE) compared to FR-4, which can lead to stress and warping of the board during thermal cycling. Proper design and material selection are crucial to mitigate these issues.
- Adhesion: Ensuring proper adhesion between the dielectric layer and the aluminum substrate can be challenging, as the surface of the aluminum must be properly prepared and treated to promote bonding.
- Drilling and routing: Due to the harder nature of aluminum compared to FR-4, drilling and routing of aluminum PCBs require specialized tools and optimized machining parameters to minimize tool wear and ensure clean, precise cuts.
Despite these challenges, advances in materials science, manufacturing technologies, and process optimization have enabled PCB factories to produce high-quality aluminum PCBs consistently and cost-effectively.
Quality Control and Testing of Aluminum PCBs
To ensure the reliability and performance of aluminum PCBs, stringent quality control measures and testing procedures are implemented throughout the manufacturing process. Some of the key quality control and testing activities include:
- Incoming material inspection: All raw materials, including aluminum substrates, dielectric layers, and copper foils, are inspected for quality and conformance to specifications before being used in production.
- In-process inspections: Visual and automated inspections are performed at various stages of the manufacturing process to identify and correct any defects or deviations from the specified requirements.
- Electrical testing: Finished boards undergo electrical tests to verify continuity, insulation resistance, and other critical electrical properties. These tests may include flying probe testing, fixture-based testing, or boundary scan testing, depending on the complexity of the board and the test coverage required.
- Thermal performance testing: The thermal conductivity and heat dissipation properties of the aluminum PCBs are tested to ensure they meet the specified requirements. This may involve the use of thermal imaging cameras, thermocouples, or other specialized testing equipment.
- Mechanical testing: Boards may be subjected to mechanical tests, such as bend testing or impact testing, to evaluate their structural integrity and durability under various stress conditions.
- Reliability testing: Accelerated life testing, thermal cycling, and humidity testing may be performed to assess the long-term reliability of the aluminum PCBs under simulated operating conditions.
By implementing these quality control measures and testing procedures, PCB factories can deliver high-quality, reliable aluminum PCBs that meet the demanding requirements of various applications.
Aluminum PCB Applications and Market Trends
Aluminum PCBs find application in a wide range of industries and products, where thermal management and heat dissipation are critical factors. Some of the key application areas include:
- LED lighting: Aluminum PCBs are extensively used in high-power LED lighting systems, such as street lights, stadium lights, and industrial lighting, where they help to efficiently dissipate the heat generated by the LEDs, thereby improving their performance and lifespan.
- Automotive electronics: In the automotive industry, aluminum PCBs are used in power converters, engine control units (ECUs), and other electronic systems that are subjected to high temperatures and harsh environmental conditions.
- Power electronics: Aluminum PCBs are used in power supply modules, motor drives, and other power electronic devices, where they help to manage the heat generated by high-current components such as MOSFETs and IGBTs.
- Telecommunications: In the telecommunications industry, aluminum PCBs are used in base station equipment, RF power amplifiers, and other high-performance electronic systems that require efficient thermal management.
- Aerospace and defense: Aluminum PCBs are used in various aerospace and defense applications, such as radar systems, avionics, and satellite communications equipment, where reliability and performance under extreme conditions are paramount.
The market for aluminum PCBs is expected to grow steadily in the coming years, driven by the increasing demand for high-performance electronic systems across various industries. Factors such as the growing adoption of LEDs, the proliferation of electric and hybrid vehicles, and the expansion of 5G networks are expected to fuel the growth of the aluminum PCB market.
Future Developments and Innovations in Aluminum PCB Manufacturing
As the demand for aluminum PCBs continues to grow, PCB factories are investing in research and development to improve the manufacturing process, enhance the performance of the boards, and reduce costs. Some of the key areas of focus for future developments and innovations include:
- Advanced materials: Researchers are exploring new materials and coatings that can improve the thermal conductivity, electrical insulation, and adhesion properties of aluminum PCBs. For example, the use of nanomaterials or ceramic fillers in the dielectric layer could enhance the thermal performance of the boards.
- 3D printing: The application of 3D printing technologies in PCB manufacturing could enable the production of complex, multilayer aluminum PCBs with intricate geometries and embedded features, such as cooling channels or heat spreaders.
- Automation and Industry 4.0: PCB factories are increasingly adopting automation technologies and Industry 4.0 principles to improve the efficiency, flexibility, and quality of aluminum PCB manufacturing. This includes the use of robotics, machine learning, and real-time data analytics to optimize the production process and minimize defects.
- Sustainable manufacturing: As environmental concerns gain prominence, PCB factories are exploring ways to make aluminum PCB manufacturing more sustainable. This may involve the use of eco-friendly materials, the implementation of closed-loop recycling systems, or the adoption of energy-efficient production processes.
By embracing these innovations and developments, PCB factories can stay at the forefront of aluminum PCB manufacturing and deliver high-quality, cost-effective solutions to meet the evolving needs of their customers.
Frequently Asked Questions (FAQ)
-
What are the main differences between aluminum PCBs and traditional FR-4 PCBs?
Aluminum PCBs use an aluminum substrate instead of the FR-4 material used in traditional PCBs. The aluminum substrate provides superior thermal conductivity and heat dissipation properties, making them ideal for applications that generate significant amounts of heat. However, aluminum PCBs are typically more expensive and require specialized manufacturing processes compared to FR-4 PCBs. -
Can aluminum PCBs be used for all types of electronic applications?
While aluminum PCBs offer excellent thermal management properties, they may not be suitable for all electronic applications. Factors such as cost, weight, and the specific requirements of the application must be considered when deciding whether to use an aluminum PCB. In general, aluminum PCBs are best suited for applications that require efficient heat dissipation and can justify the higher cost of the boards. -
How do PCB factories ensure the quality and reliability of aluminum PCBs?
PCB factories implement stringent quality control measures and testing procedures throughout the manufacturing process to ensure the quality and reliability of aluminum PCBs. These measures include incoming material inspection, in-process inspections, electrical testing, thermal performance testing, mechanical testing, and reliability testing. By adhering to these quality control standards, PCB factories can consistently produce high-quality aluminum PCBs that meet the specified requirements. -
What are some of the challenges in manufacturing aluminum PCBs?
Manufacturing aluminum PCBs presents several challenges compared to traditional FR-4 PCBs. These challenges include material handling, as aluminum substrates are more prone to scratches and dents; thermal expansion, which can lead to stress and warping of the board; adhesion issues between the dielectric layer and the aluminum substrate; and the need for specialized tools and optimized machining parameters for drilling and routing. -
What are the future trends in aluminum PCB manufacturing?
The future of aluminum PCB manufacturing is focused on improving the performance, cost-effectiveness, and sustainability of the boards. Key areas of development include the exploration of advanced materials, the application of 3D printing technologies, the adoption of automation and Industry 4.0 principles, and the implementation of sustainable manufacturing practices. By embracing these innovations, PCB factories can stay competitive and meet the evolving needs of their customers.
Conclusion
Aluminum PCBs are a critical component in many high-performance electronic applications, offering superior thermal management and heat dissipation properties compared to traditional FR-4 PCBs. The manufacturing process of aluminum PCBs involves several complex steps, from material selection and preparation to circuit design, photoresist application, etching, solder mask application, surface finish, drilling, routing, and quality control.
PCB factories rely on specialized equipment and skilled personnel to ensure the precision, quality, and reliability of the final product. Despite the challenges involved in manufacturing aluminum PCBs, ongoing research and development efforts are focused on improving the performance, cost-effectiveness, and sustainability of these boards.
As the demand for high-performance electronic systems continues to grow across various industries, the market for aluminum PCBs is expected to expand significantly in the coming years. By staying at the forefront of technological advancements and adopting innovative manufacturing practices, PCB factories can capitalize on this growth opportunity and deliver cutting-edge aluminum PCB solutions to their customers.
No responses yet