Understanding Polygon Pour Breaks in Altium
Polygon pour is a crucial feature in Altium Designer that allows users to create copper fills on PCB Layers. However, when working with rigid-flex designs, users may encounter a problem where the polygon pour breaks along the split lines between the rigid and flexible sections. This issue can lead to connectivity problems and manufacturing difficulties.
What Causes Polygon Pour Breaks on Rigid-Flex Split Lines?
The primary reason for polygon pour breaks on rigid-flex split lines is the way Altium handles the transition between rigid and flexible sections. By default, Altium treats the split lines as a boundary, causing the polygon pour to stop at these lines. This behavior is intended to prevent the copper pour from extending onto the flexible section, which may cause issues during the manufacturing process.
How to Prevent Polygon Pour Breaks on Rigid-Flex Split Lines
To prevent polygon pour breaks on rigid-flex split lines, users can employ several techniques:
- Using the “Allow Polygons to Cross Split Lines” Option: Altium provides an option to allow polygons to cross split lines. To enable this option, follow these steps:
- Open the PCB Designer in Altium.
- Navigate to the “Design” menu and select “Board Options.”
- In the “Board Options” window, go to the “Rigid-Flex” tab.
- Check the box next to “Allow Polygons to Cross Split Lines.”
-
Click “OK” to apply the changes.
-
Manually Connecting Polygon Pours: In some cases, users may need to manually connect the polygon pours across the split lines. This can be done by creating a small copper trace that bridges the gap between the polygon pours on either side of the split line. However, this method should be used with caution, as it may affect the flexibility of the design.
-
Using the “Union” Function: Altium’s “Union” function can be used to merge multiple polygon pours into a single entity. This can help maintain connectivity across split lines. To use the “Union” function:
- Select the polygon pours that need to be merged.
- Right-click on one of the selected polygons and choose “Union Selected Objects.”
- The polygon pours will be combined into a single object, maintaining connectivity across the split lines.
Best Practices for Designing Rigid-Flex PCBs in Altium
When designing rigid-flex PCBs in Altium, users should follow these best practices to minimize issues with polygon pour breaks and ensure optimal performance:
-
Plan the Rigid-Flex Layout Carefully: Before starting the design process, carefully plan the layout of the rigid and flexible sections. Consider the placement of components, the routing of traces, and the location of split lines to minimize potential issues.
-
Use Appropriate Layer Stackup: Ensure that the layer stackup is suitable for the rigid-flex design. This may involve using different materials for the rigid and flexible sections and adjusting the thickness of the layers to accommodate the desired flexibility.
-
Follow Manufacturer’s Guidelines: Consult with the PCB manufacturer to understand their specific guidelines for designing rigid-flex PCBs. Different manufacturers may have varying requirements for minimum bend radii, material selection, and other design parameters.
-
Test and Prototype: Before finalizing the design, create prototypes and test them thoroughly to identify any issues with polygon pour breaks or other aspects of the rigid-flex design. This allows for iterative improvements and refinements before moving to full-scale production.
Troubleshooting Polygon Pour Breaks in Altium
If polygon pour breaks persist despite following the prevention methods and best practices, users can try these troubleshooting steps:
-
Check the Split Line Placement: Ensure that the split lines are placed correctly and do not intersect with any components or other design elements. Incorrect split line placement can cause polygon pour breaks.
-
Verify the Layer Stackup: Double-check the layer stackup to ensure that it is configured correctly for the rigid-flex design. Inconsistencies in the layer stackup can lead to polygon pour breaks and other issues.
-
Review the Polygon Pour Settings: Examine the settings for the polygon pour, such as the clearance, thermal relief, and other parameters. Adjust these settings as needed to optimize the polygon pour behavior.
-
Consult with Altium Support: If the issue persists, reach out to Altium’s technical support team for further assistance. They can provide guidance on resolving polygon pour breaks and other design challenges.
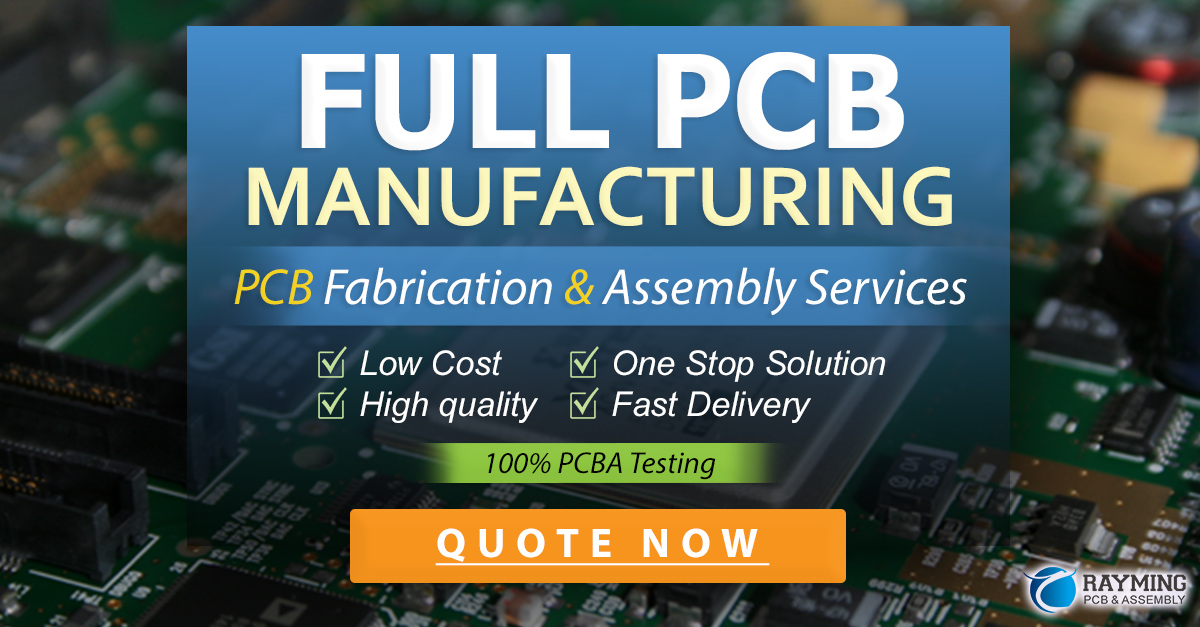
FAQs
-
Q: What is a polygon pour in Altium?
A: A polygon pour is a feature in Altium Designer that allows users to create copper fills on PCB Layers. It is used to provide a continuous copper connection between components and to improve EMI shielding and heat dissipation. -
Q: Why do polygon pours break on rigid-flex split lines?
A: Polygon pours break on rigid-flex split lines because Altium treats the split lines as a boundary by default. This behavior is intended to prevent the copper pour from extending onto the flexible section, which may cause issues during the manufacturing process. -
Q: How can I prevent polygon pour breaks on rigid-flex split lines in Altium?
A: To prevent polygon pour breaks on rigid-flex split lines in Altium, you can use the “Allow Polygons to Cross Split Lines” option in the Board Options dialog, manually connect polygon pours using copper traces, or use the “Union” function to merge multiple polygon pours into a single entity. -
Q: What are some best practices for designing rigid-flex PCBs in Altium?
A: Some best practices for designing rigid-flex PCBs in Altium include careful planning of the layout, using appropriate layer stackups, following manufacturer’s guidelines, and thoroughly testing and prototyping the design before production. -
Q: What should I do if polygon pour breaks persist despite following prevention methods and best practices?
A: If polygon pour breaks persist, you can troubleshoot by checking the split line placement, verifying the layer stackup, reviewing the polygon pour settings, and consulting with Altium’s technical support team for further assistance.
Technique | Description |
---|---|
Allow Polygons to Cross Split Lines | Enable the option in Altium’s Board Options to allow polygons to cross split lines. |
Manually Connect Polygon Pours | Create small copper traces to bridge the gap between polygon pours across split lines. |
Use the “Union” Function | Merge multiple polygon pours into a single entity using Altium’s “Union” function. |
By understanding the causes of polygon pour breaks on rigid-flex split lines, employing prevention techniques, following best practices, and troubleshooting issues as they arise, Altium users can successfully design and manufacture rigid-flex PCBs with optimal performance and reliability.
No responses yet