Introduction to PCB Manufacturing
Printed Circuit Board (PCB) manufacturing is a complex process that involves multiple steps and advanced technologies. In today’s rapidly evolving electronics industry, PCB manufacturing has become increasingly sophisticated to meet the demands for high-performance, miniaturized, and reliable electronic devices. This article will delve into the intricacies of advanced PCB manufacturing, exploring the latest techniques, materials, and quality control measures employed in the industry.
The PCB Manufacturing Process
Design and Layout
The PCB manufacturing process begins with the design and layout of the circuit board. This crucial step involves using specialized software to create a digital representation of the PCB, including the placement of components, routing of traces, and definition of layers. Advanced PCB design software allows for 3D modeling, signal integrity analysis, and thermal management simulations to optimize the board’s performance and reliability.
Material Selection
Selecting the appropriate materials for PCB manufacturing is essential for ensuring the board’s functionality and durability. The most common base material for PCBs is FR-4, a glass-reinforced epoxy laminate. However, advanced applications may require the use of high-frequency materials, such as Rogers or Isola, which offer superior electrical properties and thermal stability. The choice of Copper Foil thickness and type (electrodeposited or rolled) also plays a significant role in the PCB’s performance.
Photolithography and Etching
Once the design is finalized and materials are selected, the next step is to transfer the circuit pattern onto the Copper-Clad Laminate. This is achieved through photolithography, a process that involves coating the laminate with a light-sensitive photoresist, exposing it to UV light through a photomask, and developing the resist to reveal the desired pattern. The exposed copper is then etched away using a chemical solution, leaving only the desired traces and pads.
Lamination and Drilling
For multi-layer PCBs, the individual layers are laminated together under high pressure and temperature to form a single board. The lamination process ensures proper alignment and bonding of the layers. After lamination, holes are drilled through the board to accommodate through-hole components and provide electrical connections between layers. Advanced drilling techniques, such as laser drilling, enable the creation of smaller, more precise holes for high-density designs.
Plating and Surface Finishing
To establish reliable electrical connections and protect the copper traces from oxidation, the PCB undergoes plating and surface finishing processes. Through-hole plating involves depositing a thin layer of copper on the walls of the drilled holes, ensuring continuity between layers. Surface finishing options include Hot Air Solder Leveling (HASL), Electroless Nickel Immersion Gold (ENIG), and Immersion Silver, each with its own advantages in terms of solderability, durability, and cost.
Solder Mask and Silkscreen
A solder mask, typically green in color, is applied to the PCB to protect the copper traces from accidental solder bridging and provide electrical insulation. Openings in the solder mask allow for component soldering and electrical testing. A silkscreen layer is then added to the board, which includes text, logos, and component identifiers for easy assembly and troubleshooting.
Electrical Testing and Inspection
Before the PCB is shipped to the customer, it undergoes rigorous electrical testing and inspection to ensure its functionality and conformance to specifications. Automated Optical Inspection (AOI) systems scan the board for any manufacturing defects, such as short circuits, open circuits, or incorrect component placement. In-circuit testing (ICT) and functional testing are also performed to verify the board’s electrical performance and overall functionality.
Advanced PCB Manufacturing Techniques
High-Density Interconnect (HDI)
HDI PCBs feature smaller vias, finer pitch components, and thinner traces, enabling higher component density and improved signal integrity. Advanced manufacturing techniques, such as microvias, blind and buried vias, and sequential lamination, are employed to achieve HDI designs. These techniques allow for more complex routing and better utilization of board space, making HDI PCBs ideal for compact, high-performance applications.
Embedded Components
Embedded component technology involves placing passive components, such as resistors and capacitors, within the layers of the PCB rather than on the surface. This approach saves board space, reduces parasitic effects, and improves signal integrity. Embedded components are fabricated using specialized materials and processes, such as resistive foils and ceramic capacitor laminates, and require precise control over the manufacturing process.
Flex and Rigid-Flex PCBs
Flexible PCBs, made from thin, flexible substrates like polyimide, offer unique advantages in terms of space savings, weight reduction, and mechanical flexibility. Rigid-flex PCBs combine the benefits of both rigid and flexible substrates, allowing for three-dimensional packaging and improved reliability in applications subject to vibration or mechanical stress. Manufacturing flex and rigid-flex PCBs requires specialized equipment and expertise in material handling, lamination, and coverlay application.
3D Printing
3D printing technology is finding its way into PCB manufacturing, offering new possibilities for rapid prototyping and customization. Conductive ink printing allows for the creation of circuit traces and passive components directly onto 3D-printed substrates, enabling the fabrication of complex, three-dimensional circuit structures. While still in its early stages, 3D printing has the potential to revolutionize PCB manufacturing, particularly for low-volume, high-mix applications.
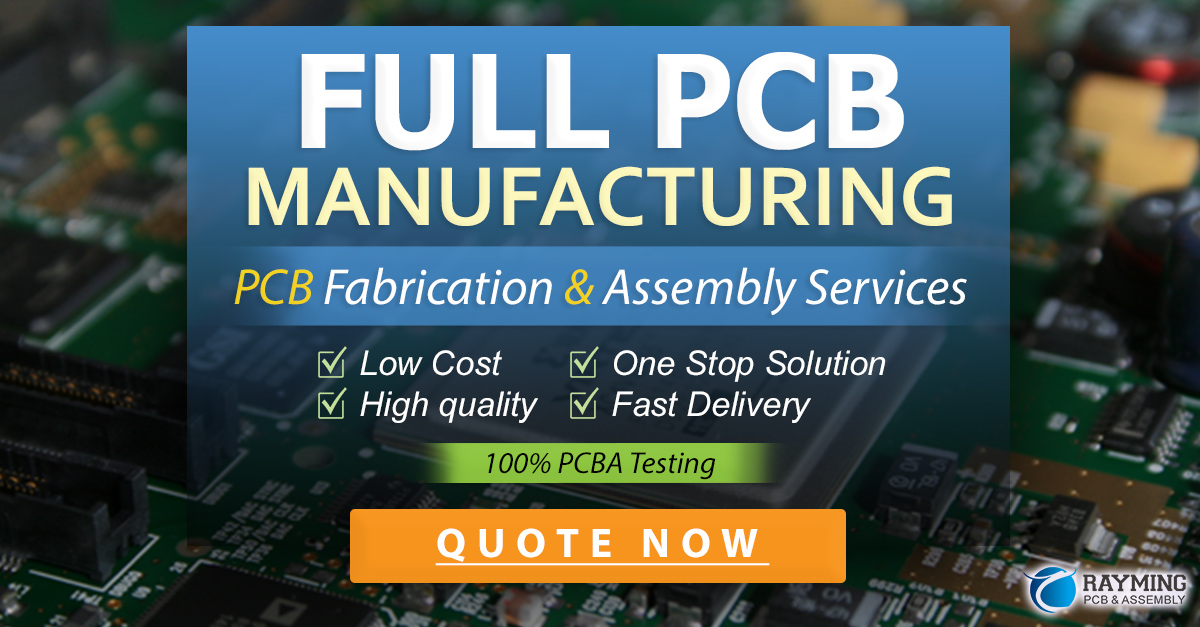
Quality Control and Standards
IPC Standards
The electronics industry relies on a set of internationally recognized standards developed by the IPC (Association Connecting Electronics Industries) to ensure consistency, reliability, and interoperability in PCB manufacturing. Key IPC standards include:
- IPC-A-600: Acceptability of Printed Boards
- IPC-6012: Qualification and Performance Specification for Rigid Printed Boards
- IPC-2221: Generic Standard on Printed Board Design
- IPC-7351: Generic Requirements for Surface Mount Design and Land Pattern Standard
Adherence to these standards helps manufacturers maintain high quality and meet customer expectations.
Quality Management Systems
Implementing robust quality management systems, such as ISO 9001 and AS9100, is essential for PCB manufacturers to consistently deliver high-quality products and services. These systems establish documented processes, continuous improvement practices, and customer satisfaction metrics to drive organizational excellence and minimize defects and errors in the manufacturing process.
Environmental Considerations
As environmental regulations become more stringent, PCB manufacturers must adopt eco-friendly practices and materials. The Restriction of Hazardous Substances (RoHS) directive and the Registration, Evaluation, Authorization, and Restriction of Chemicals (REACH) regulation have driven the industry towards the use of lead-free solders and the elimination of harmful substances in PCB manufacturing. Manufacturers are also implementing green initiatives, such as waste reduction, energy efficiency, and water conservation, to minimize their environmental impact.
Frequently Asked Questions (FAQ)
- What is the difference between a single-layer and a multi-layer PCB?
-
A Single-layer PCB has conductive traces on only one side of the substrate, while a multi-layer PCB has multiple layers of conductive traces separated by insulating layers. Multi-layer PCBs offer higher component density, better signal integrity, and improved thermal management compared to single-layer boards.
-
What is the purpose of a solder mask in PCB manufacturing?
-
A solder mask is a protective layer applied to the PCB to prevent accidental solder bridging between closely spaced traces and pads. It also provides electrical insulation and protects the copper traces from oxidation and environmental damage. The solder mask has openings to allow for component soldering and electrical testing.
-
What are the advantages of using HDI technology in PCB manufacturing?
-
HDI (High-Density Interconnect) technology enables the fabrication of PCBs with smaller vias, finer pitch components, and thinner traces. This results in higher component density, improved signal integrity, and better utilization of board space. HDI PCBs are ideal for compact, high-performance applications, such as smartphones, wearables, and advanced medical devices.
-
How do embedded components differ from surface-mounted components?
-
Surface-mounted components are placed on the surface of the PCB and soldered to pads, while embedded components are placed within the layers of the PCB. Embedded components save board space, reduce parasitic effects, and improve signal integrity. However, they require specialized materials and manufacturing processes, making them more challenging and expensive to implement compared to surface-mounted components.
-
What role do IPC standards play in PCB manufacturing?
- IPC standards are internationally recognized guidelines that ensure consistency, reliability, and interoperability in PCB manufacturing. They cover various aspects of PCB design, fabrication, assembly, and testing. Adhering to IPC standards helps manufacturers maintain high quality, meet customer expectations, and facilitate seamless integration of PCBs into electronic systems.
Conclusion
Advanced PCB manufacturing is a constantly evolving field, driven by the ever-increasing demands for high-performance, miniaturized, and reliable electronic devices. From design and material selection to cutting-edge fabrication techniques and rigorous quality control, every aspect of the PCB manufacturing process plays a critical role in determining the final product’s functionality and durability.
As the electronics industry continues to push the boundaries of innovation, PCB manufacturers must stay abreast of the latest technologies, standards, and best practices to remain competitive. By embracing advanced manufacturing techniques, such as HDI, embedded components, and 3D printing, and prioritizing quality, reliability, and environmental sustainability, PCB manufacturers can meet the challenges of the future and contribute to the development of groundbreaking electronic solutions.
PCB Manufacturing Process | Description |
---|---|
Design and Layout | Creating a digital representation of the PCB using specialized software |
Material Selection | Choosing appropriate base materials, copper foil, and laminate for the PCB |
Photolithography and Etching | Transferring the circuit pattern onto the copper-clad laminate and etching away unwanted copper |
Lamination and Drilling | Bonding multiple layers together and drilling holes for through-hole components and inter-layer connections |
Plating and Surface Finishing | Depositing copper in drilled holes and applying a protective surface finish to the PCB |
Solder Mask and Silkscreen | Applying a solder mask for insulation and a silkscreen for component identification |
Electrical Testing and Inspection | Verifying the PCB’s functionality and conformance to specifications using automated systems |
Advanced PCB Manufacturing Techniques | Description |
---|---|
High-Density Interconnect (HDI) | Fabricating PCBs with smaller vias, finer pitch components, and thinner traces for higher density and performance |
Embedded Components | Placing passive components within the layers of the PCB to save space and improve signal integrity |
Flex and Rigid-Flex PCBs | Incorporating flexible substrates for space savings, weight reduction, and mechanical flexibility |
3D Printing | Using conductive ink printing to create circuit traces and components directly onto 3D-printed substrates |
By understanding the intricacies of advanced PCB manufacturing and staying informed about the latest developments in the field, engineers, designers, and managers can make informed decisions, optimize their designs, and collaborate effectively with PCB manufacturers to bring their innovative ideas to life.
No responses yet