Introduction to PCB Testing
Printed Circuit Boards (PCBs) and Printed Circuit Board Assemblies (PCBAs) are essential components in modern electronics. To ensure the reliability and functionality of these boards, various testing techniques are employed throughout the manufacturing process. In this article, we will explore the common PCB/PCBA Testing techniques used in the industry to guarantee the quality and performance of these critical components.
Why is PCB Testing Important?
PCB testing is crucial for several reasons:
-
Quality Assurance: Testing helps identify defects and issues early in the manufacturing process, ensuring that only high-quality boards are delivered to customers.
-
Cost Savings: Detecting faults early reduces the cost of repairs and rework, as fixing issues becomes more expensive in later stages of production or after the product is shipped.
-
Reliability: Thorough testing ensures that the PCBs and PCBAs will function as intended, increasing the reliability of the final product.
-
Safety: Proper testing helps prevent potential safety hazards caused by faulty components or improper assembly.
Types of PCB/PCBA Testing Techniques
There are various testing techniques used to evaluate the quality and functionality of PCBs and PCBAs. These techniques can be categorized into two main groups: visual inspection and electrical testing.
Visual Inspection Techniques
Visual inspection is the first step in the testing process and involves examining the PCB or PCBA for any visible defects or anomalies. Some common visual inspection techniques include:
Manual Visual Inspection
In this method, a skilled operator visually inspects the board using magnifying lenses or microscopes to identify any defects, such as:
- Solder bridges
- Insufficient solder
- Component misalignment
- Damaged components
While manual visual inspection is time-consuming, it is still an essential step in the testing process.
Automated Optical Inspection (AOI)
AOI uses high-resolution cameras and computer vision algorithms to automatically inspect PCBs and PCBAs for defects. This technique is faster and more consistent than manual inspection, and it can detect a wide range of defects, including:
- Missing components
- Incorrect component placement
- Solder defects
- Trace and pad issues
AOI systems can be programmed with specific rules and tolerances to identify defects based on the PCB design and manufacturing standards.
Electrical Testing Techniques
Electrical testing involves verifying the electrical characteristics and functionality of the PCB or PCBA. Some common electrical testing techniques include:
In-Circuit Testing (ICT)
ICT is a bed-of-nails testing method that uses a custom-designed fixture with spring-loaded probes to make contact with specific test points on the PCB. This technique allows for the testing of individual components and circuits, checking for:
- Short circuits
- Open circuits
- Resistance values
- Capacitance values
- Diode and transistor functionality
ICT is an efficient way to identify defects in the PCB and ensure that the components are functioning correctly.
Flying Probe Testing
Flying probe testing is an alternative to ICT that uses movable probes to make contact with test points on the PCB. This technique is more flexible than ICT, as it does not require a custom fixture. Flying probe testing is ideal for:
- Low-volume production
- Prototype testing
- Boards with limited test points
However, flying probe testing is generally slower than ICT due to the movement of the probes.
Functional Testing
Functional testing involves verifying the overall functionality of the PCBA by simulating real-world operating conditions. This type of testing ensures that the PCBA performs as intended and meets the specified requirements. Functional testing may include:
- Power-on testing
- Boundary scan testing
- Programming and firmware verification
- Environmental testing (temperature, humidity, vibration)
Functional testing is typically performed after the PCB has passed visual inspection and electrical testing.
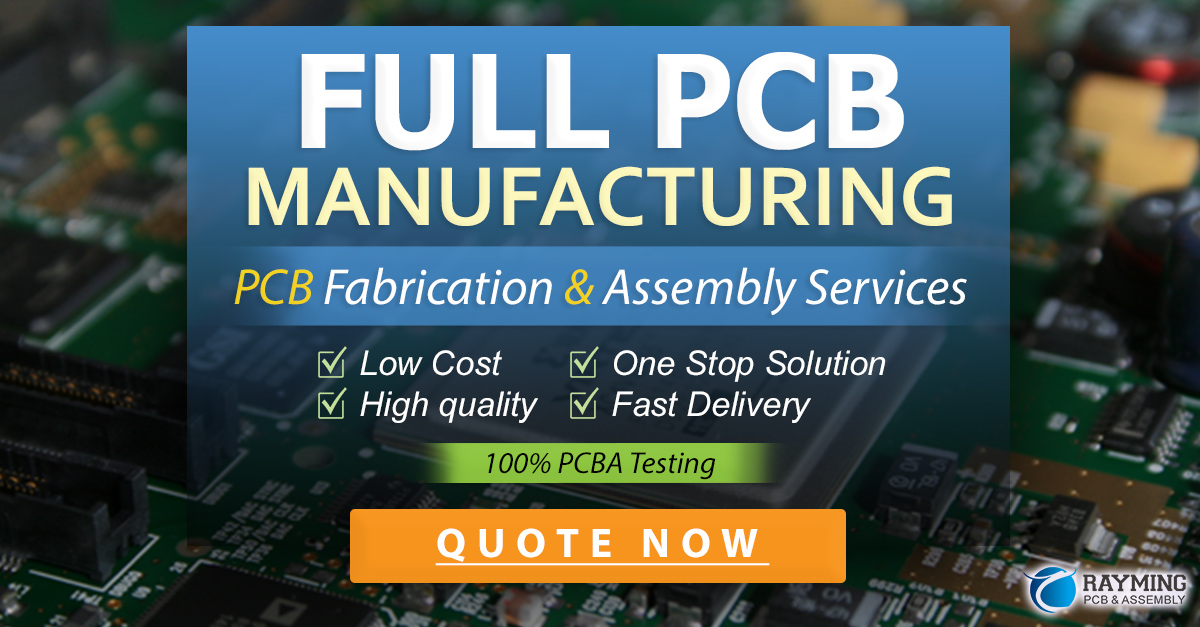
Comparison of PCB/PCBA Testing Techniques
Testing Technique | Advantages | Disadvantages |
---|---|---|
Manual Visual Inspection | – Identifies visible defects – Useful for prototype and low-volume production |
– Time-consuming – Subject to human error – Limited to visible defects |
Automated Optical Inspection (AOI) | – Fast and consistent – Detects a wide range of defects – Programmable with specific rules and tolerances |
– Expensive equipment – May require additional testing for hidden defects |
In-Circuit Testing (ICT) | – Tests individual components and circuits – Efficient for high-volume production |
– Requires custom fixtures – Limited to accessible test points – May not detect all functional issues |
Flying Probe Testing | – Flexible, no custom fixtures required – Ideal for low-volume production and prototypes |
– Slower than ICT – Limited number of probes may affect testing speed |
Functional Testing | – Verifies overall functionality – Simulates real-world operating conditions |
– Requires developed firmware and software – May not identify specific component-level faults |
Best Practices for PCB/PCBA Testing
To ensure the effectiveness of PCB/PCBA testing, consider the following best practices:
-
Develop a comprehensive test plan: Define the testing requirements, methods, and acceptance criteria based on the PCB design and end-use application.
-
Start testing early: Implement testing at various stages of the manufacturing process to identify and address issues as early as possible.
-
Use a combination of testing techniques: Employ a mix of visual inspection, electrical testing, and functional testing to ensure comprehensive coverage.
-
Maintain proper documentation: Keep detailed records of test results, defects, and corrective actions for traceability and continuous improvement.
-
Regularly review and update test procedures: As PCB designs and manufacturing processes evolve, review and update testing procedures to ensure they remain effective and relevant.
Conclusion
PCB/PCBA testing is a critical aspect of the electronics manufacturing process, ensuring the quality, reliability, and functionality of these essential components. By employing a combination of visual inspection, electrical testing, and functional testing techniques, manufacturers can identify and address defects early, reduce costs, and deliver high-quality products to their customers. Implementing best practices and continuously improving testing procedures will help maintain the effectiveness of PCB/PCBA testing in an ever-evolving industry.
Frequently Asked Questions (FAQ)
-
Q: What is the difference between PCB and PCBA testing?
A: PCB testing focuses on the bare printed circuit board, checking for defects in the traces, pads, and vias. PCBA testing, on the other hand, involves testing the board with components already soldered on, verifying the functionality and electrical characteristics of the assembled board. -
Q: Is it necessary to perform all the testing techniques mentioned in the article?
A: The choice of testing techniques depends on factors such as the complexity of the PCB, the production volume, and the end-use application. While it is not always necessary to perform all the techniques, using a combination of visual inspection, electrical testing, and functional testing is recommended for comprehensive coverage. -
Q: Can PCB/PCBA testing be outsourced to third-party service providers?
A: Yes, many electronics manufacturers outsource their PCB/PCBA testing to specialized service providers. These providers have the expertise, equipment, and resources to perform various testing techniques efficiently and effectively. -
Q: How can I determine the appropriate testing techniques for my PCB/PCBA?
A: The selection of testing techniques should be based on factors such as the PCB design complexity, component types, manufacturing process, and end-use requirements. Consulting with experienced PCB designers, manufacturing engineers, and testing experts can help determine the most suitable testing techniques for your specific case. -
Q: What are the consequences of inadequate PCB/PCBA testing?
A: Inadequate testing can lead to several issues, such as: - Undetected defects leading to product failures and customer returns
- Increased repair and rework costs
- Delayed time-to-market due to issues discovered late in the manufacturing process
- Potential safety hazards in critical applications
- Damage to the manufacturer’s reputation and brand image
By implementing a robust PCB/PCBA testing process, manufacturers can mitigate these risks and ensure the delivery of high-quality, reliable products to their customers.
No responses yet