Introduction to DFM in PCB Design
Design for Manufacturability (DFM) is a crucial aspect of PCB design that focuses on optimizing the design to ensure efficient and cost-effective manufacturing. By considering DFM principles during the design phase, engineers can minimize potential issues, reduce manufacturing costs, and improve the overall quality of the PCB. In this article, we will discuss some important matters that require attention when implementing DFM in PCB design.
Key Aspects of DFM in PCB Design
- Component selection and placement
- Trace routing and spacing
- Vias and holes
- Soldermask and silkscreen
- Panelization and breakaway tabs
Component Selection and Placement
Choosing the Right Components
When selecting components for your PCB design, consider the following factors to ensure compatibility with DFM principles:
- Package type and size
- Pitch and lead spacing
- Availability and cost
- Thermal requirements
Optimal Component Placement
Proper component placement is essential for efficient manufacturing and reliable performance. Keep these guidelines in mind:
- Group similar components together
- Maintain adequate spacing between components
- Avoid placing components too close to the board edges
- Consider the orientation of polarized components
Component Package | Minimum Spacing |
---|---|
SOT-23 | 0.5 mm |
SOIC-8 | 0.8 mm |
QFP-64 | 1.0 mm |
BGA-256 | 1.5 mm |
Trace Routing and Spacing
Trace Width and Thickness
When designing traces, consider the following factors:
- Current carrying capacity
- Impedance requirements
- Manufacturing capabilities
Trace Width | Current Capacity (1 oz. copper) |
---|---|
0.2 mm | 0.5 A |
0.4 mm | 1.0 A |
0.8 mm | 2.0 A |
1.6 mm | 4.0 A |
Trace Spacing and Clearance
Maintain appropriate spacing between traces and components to prevent short circuits and signal integrity issues. Follow these guidelines:
- Minimum trace-to-trace spacing: 0.15 mm
- Minimum trace-to-pad spacing: 0.2 mm
- Minimum trace-to-via spacing: 0.25 mm
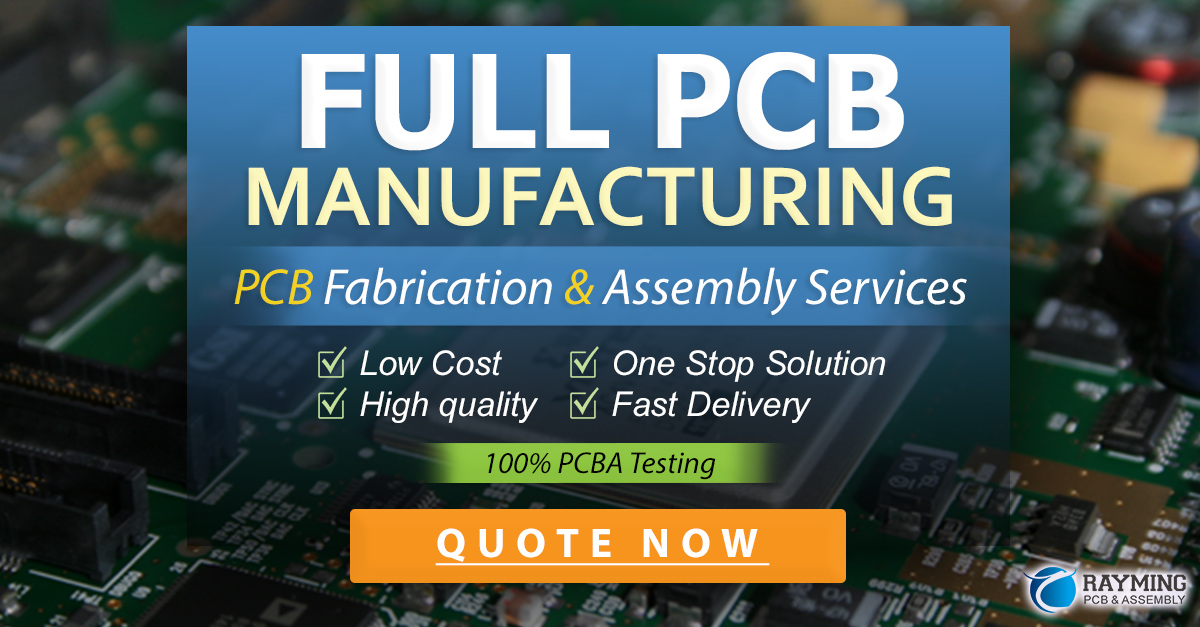
Vias and Holes
Via Types and Sizes
Choose the appropriate via type and size based on your design requirements:
- Through-hole vias
- Blind vias
- Buried vias
- Microvias
Via Type | Minimum Diameter | Minimum Drill Size |
---|---|---|
Through-hole | 0.6 mm | 0.3 mm |
Blind | 0.4 mm | 0.2 mm |
Buried | 0.4 mm | 0.2 mm |
Microvia | 0.2 mm | 0.1 mm |
Via Placement and Spacing
When placing vias, follow these guidelines to ensure manufacturability:
- Avoid placing vias under components
- Maintain adequate spacing between vias
- Use via-in-pad design when necessary
Soldermask and Silkscreen
Soldermask Design Considerations
Soldermask helps protect the PCB from oxidation and prevents solder bridging. Consider these factors when designing soldermask:
- Minimum soldermask aperture: 0.1 mm
- Soldermask expansion: 0.05 mm
- Soldermask color (green, red, blue, etc.)
Silkscreen Design Guidelines
Silkscreen provides important information about component placement and orientation. Follow these guidelines:
- Minimum silkscreen line width: 0.15 mm
- Minimum silkscreen text height: 1.0 mm
- Keep silkscreen away from solderable pads
Panelization and Breakaway Tabs
Panelization Techniques
Panelization allows multiple PCBs to be manufactured on a single panel, reducing costs and increasing efficiency. Consider these techniques:
- Tab-routed panels
- Scored panels
- V-groove panels
Breakaway Tab Design
Breakaway tabs help secure the PCBs within the panel during manufacturing. When designing breakaway tabs, keep these factors in mind:
- Tab width: 2.0 mm to 3.0 mm
- Tab spacing: 25 mm to 50 mm
- Use mouse bites or perforations for easy separation
Frequently Asked Questions (FAQ)
1. What is the minimum recommended trace width for a PCB?
The minimum recommended trace width depends on the current carrying capacity and manufacturing capabilities. For most standard PCB designs, a minimum trace width of 0.2 mm is sufficient. However, for high-current applications or advanced manufacturing processes, wider traces may be necessary.
2. How do I determine the appropriate via size for my PCB design?
The appropriate via size depends on factors such as the number of layers, the required current carrying capacity, and the manufacturing capabilities of your PCB fabricator. As a general rule, use the smallest via size that meets your design requirements and is compatible with your manufacturer’s capabilities. Consult with your PCB fabricator for specific recommendations.
3. Can I use different soldermask colors in my PCB design?
Yes, you can use different soldermask colors in your PCB design. While green is the most common color, other options such as red, blue, yellow, and black are available. Keep in mind that some colors may have a higher cost or longer lead time. Consult with your PCB fabricator for available options and any associated costs or limitations.
4. What is the purpose of panelization in PCB manufacturing?
Panelization is the process of grouping multiple PCBs onto a single panel for manufacturing. This technique helps reduce costs and increase efficiency by allowing multiple boards to be fabricated, assembled, and tested simultaneously. Panelization also simplifies handling and transportation of the PCBs throughout the manufacturing process.
5. How can I ensure my PCB design is compatible with DFM principles?
To ensure your PCB design is compatible with DFM principles, follow these best practices:
- Choose components that are readily available and have standard package sizes.
- Maintain appropriate spacing between components, traces, and vias.
- Use standard via sizes and placement techniques.
- Adhere to recommended soldermask and silkscreen design guidelines.
- Consider panelization and breakaway tab design for efficient manufacturing.
By following these guidelines and consulting with your PCB fabricator early in the design process, you can create a PCB design that is optimized for manufacturability, reliability, and cost-effectiveness.
Conclusion
Designing a PCB with DFM principles in mind is essential for ensuring a smooth and cost-effective manufacturing process. By paying attention to component selection and placement, trace routing and spacing, via design, soldermask and silkscreen considerations, and panelization techniques, you can create a PCB design that is optimized for manufacturability and reliability. Always consult with your PCB fabricator early in the design process to ensure compatibility with their specific manufacturing capabilities and guidelines. By following these best practices and maintaining open communication with your manufacturing partners, you can streamline the PCB design and fabrication process, ultimately leading to a successful product launch.
No responses yet