Introduction to Solder Paste Printing
Solder paste printing is a crucial step in the Surface Mount Technology (SMT) assembly process. It involves depositing solder paste onto the printed circuit board (PCB) pads, where electronic components will be placed and soldered. The quality of the solder paste printing process directly affects the reliability and functionality of the final assembled PCB.
What is Solder Paste?
Solder paste is a mixture of tiny solder particles suspended in a flux medium. The solder particles are typically made of a tin-lead (SnPb) alloy or lead-free alloys such as tin-silver-copper (SAC). The flux medium serves several purposes:
- It helps to clean the surfaces of the PCB pads and component leads, removing any oxides or contaminants.
- It protects the solder particles from oxidation during the reflow process.
- It helps to evenly distribute the solder particles across the PCB pads.
The composition of solder paste can vary depending on the specific application and the desired properties of the solder joint. Some common solder paste alloys and their melting temperatures are listed in the table below:
Alloy | Composition | Melting Temperature (°C) |
---|---|---|
Sn63Pb37 | 63% Tin, 37% Lead | 183 |
Sn96.5Ag3.0Cu0.5 | 96.5% Tin, 3.0% Silver, 0.5% Copper | 217-220 |
Sn99.3Cu0.7 | 99.3% Tin, 0.7% Copper | 227 |
Solder Paste Properties
The performance of solder paste is dependent on several key properties:
-
Particle Size Distribution: The size of the solder particles in the paste affects the printing process and the final solder joint quality. Smaller particles allow for finer pitch components and more precise printing, while larger particles are better suited for larger components and pads.
-
Viscosity: The viscosity of the solder paste determines how easily it can be printed onto the PCB pads. The viscosity should be low enough to allow for easy printing, but high enough to prevent the paste from slumping or spreading after printing.
-
Flux Activity: The flux in the solder paste helps to remove oxides and improve wetting during the soldering process. The activity level of the flux should be chosen based on the specific application and the cleanliness of the PCB and components.
-
Solder Loading: The solder loading refers to the percentage of solder particles in the paste by weight. Higher solder loading allows for more solder to be deposited on the pads, which can be beneficial for larger components or pads.
Solder Paste Printing Process
The solder paste printing process involves several steps, each of which must be carefully controlled to ensure consistent and high-quality results.
Step 1: Stencil Alignment
The first step in the solder paste printing process is to align the stencil with the PCB. The stencil is a thin metal sheet with apertures that correspond to the PCB pads. It is placed over the PCB and aligned using fiducial marks or other alignment features.
Step 2: Solder Paste Application
Once the stencil is aligned, the solder paste is applied to the top surface of the stencil. The paste is typically applied using a squeegee or a paste dispenser. The squeegee is used to spread the paste across the stencil, forcing it through the apertures and onto the PCB pads.
Step 3: Stencil Removal
After the solder paste has been applied, the stencil is carefully removed from the PCB. The solder paste should remain on the PCB pads in the desired pattern.
Step 4: Inspection
After the stencil is removed, the PCB is inspected to ensure that the solder paste has been properly applied. This can be done visually or using automated inspection equipment. Common defects to look for include:
- Insufficient solder paste
- Excessive solder paste
- Bridging between pads
- Misaligned or missing solder paste deposits
If any defects are found, the PCB may need to be cleaned and the printing process repeated.
Factors Affecting Solder Paste Printing Quality
Several factors can affect the quality of the solder paste printing process, including:
Stencil Design
The design of the stencil is critical to the success of the solder paste printing process. The aperture size, shape, and spacing should be carefully chosen based on the PCB layout and the components being used. Some guidelines for stencil design include:
- Aperture size should be slightly larger than the PCB pad to allow for some overprinting
- Aperture walls should be tapered to facilitate paste release
- Apertures should be spaced far enough apart to prevent bridging
- Stencil thickness should be chosen based on the desired solder paste volume
Squeegee Pressure and Speed
The pressure and speed of the squeegee during the printing process can affect the amount and distribution of solder paste on the PCB pads. Too much pressure can cause overprinting or damage to the stencil, while too little pressure can result in insufficient solder paste. Similarly, too high of a squeegee speed can cause inconsistent printing, while too low of a speed can result in excessive solder paste.
Solder Paste Properties
As mentioned earlier, the properties of the solder paste itself can affect the printing process. The particle size distribution, viscosity, flux activity, and solder loading should all be chosen based on the specific application and the desired properties of the solder joint.
Environmental Conditions
Environmental conditions such as temperature and humidity can also affect the solder paste printing process. High temperatures can cause the solder paste to dry out or slump, while high humidity can cause the paste to absorb moisture and become sticky or clumpy. It is important to maintain consistent environmental conditions in the printing area to ensure consistent results.
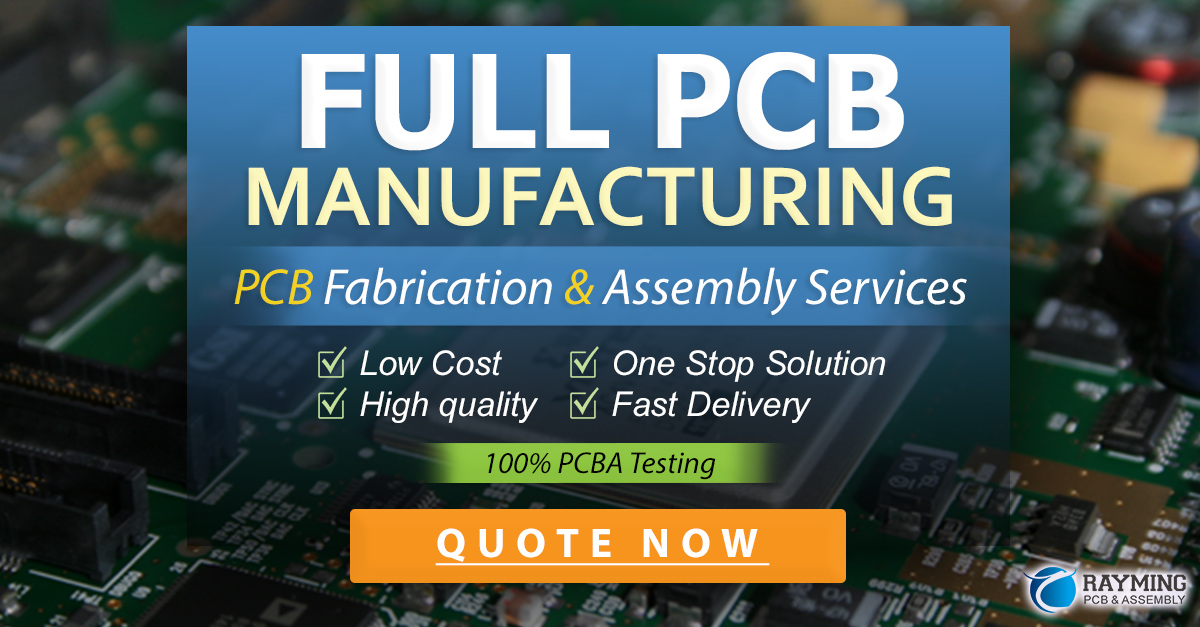
Best Practices for Solder Paste Printing
To ensure consistent and high-quality solder paste printing, there are several best practices that should be followed:
-
Use a high-quality stencil: The stencil should be made of a durable material such as stainless steel or nickel, and should be laser-cut or electroformed for precise aperture sizes and shapes.
-
Maintain consistent environmental conditions: The printing area should be kept at a consistent temperature and humidity level to prevent variations in solder paste properties.
-
Use the appropriate solder paste: The solder paste should be chosen based on the specific application and the desired properties of the solder joint.
-
Optimize the printing parameters: The squeegee pressure, speed, and angle should be optimized for the specific solder paste and PCB design.
-
Regularly clean and maintain equipment: The stencil, squeegee, and other printing equipment should be regularly cleaned and maintained to ensure consistent performance.
-
Inspect printed PCBs: Printed PCBs should be inspected for defects such as insufficient solder paste, bridging, or misalignment. Any defects should be corrected before the components are placed.
Troubleshooting Common Solder Paste Printing Issues
Despite best efforts, issues can still arise during the solder paste printing process. Some common issues and their potential solutions are listed below:
Issue | Potential Causes | Solutions |
---|---|---|
Insufficient solder paste | – Stencil apertures too small – Squeegee pressure too low – Solder paste too thick |
– Increase aperture size – Increase squeegee pressure – Use thinner solder paste |
Excessive solder paste | – Stencil apertures too large – Squeegee pressure too high – Solder paste too thin |
– Decrease aperture size – Decrease squeegee pressure – Use thicker solder paste |
Bridging between pads | – Stencil apertures too close together – Excessive solder paste |
– Increase spacing between apertures – Decrease solder paste volume |
Poor paste release from stencil | – Stencil aperture walls not tapered – Solder paste too thick |
– Use tapered aperture walls – Use thinner solder paste |
Inconsistent printing | – Squeegee speed too high – Inconsistent squeegee pressure |
– Decrease squeegee speed – Maintain consistent squeegee pressure |
Frequently Asked Questions (FAQ)
-
What is the difference between solder paste and solder wire?
Solder paste is a mixture of tiny solder particles suspended in a flux medium, while solder wire is a solid wire of solder alloy. Solder paste is used in SMT assembly for printing onto PCB pads, while solder wire is used in through-hole assembly for hand soldering. -
Can solder paste be reused?
No, solder paste should not be reused once it has been printed onto a PCB. The flux in the paste can become contaminated or degrade over time, leading to poor soldering results. -
How long can solder paste be stored?
Solder paste typically has a shelf life of 6-12 months when stored at the appropriate temperature and humidity levels. It is important to follow the manufacturer’s storage recommendations to ensure optimal performance. -
What is the difference between no-clean and water-soluble solder paste?
No-clean solder paste contains a flux that does not require cleaning after the soldering process, while water-soluble solder paste contains a flux that must be cleaned with water or a solvent. No-clean solder paste is more commonly used in SMT assembly due to its convenience and lower environmental impact. -
How often should the stencil be cleaned?
The stencil should be cleaned regularly to prevent solder paste buildup and ensure consistent printing results. The frequency of cleaning depends on the specific application and the volume of PCBs being printed, but a general guideline is to clean the stencil after every 10-20 prints or whenever print quality begins to degrade.
Conclusion
Solder paste printing is a critical step in the SMT assembly process that directly affects the quality and reliability of the final assembled PCB. By understanding the properties of solder paste, the factors that affect printing quality, and the best practices for printing, manufacturers can ensure consistent and high-quality results.
While solder paste printing can be challenging, following the guidelines and troubleshooting tips outlined in this article can help to minimize issues and improve overall process efficiency. As with any manufacturing process, continuous monitoring and improvement are key to achieving optimal results.
No responses yet