Introduction to Wire-to-Board Connections
In the world of electronics, connecting wires to circuit boards is a fundamental skill that every enthusiast and professional must master. Wire-to-board connections are essential for creating reliable and efficient electrical circuits, allowing signals and power to flow seamlessly between components. This comprehensive guide will walk you through the various methods and best practices for making secure and durable wire-to-board connections.
The Importance of Proper Wire-to-Board Connections
Proper wire-to-board connections are crucial for several reasons:
- Reliability: A well-made connection ensures that the electrical signal or power is transmitted consistently and without interruption.
- Durability: Secure connections can withstand the stresses of everyday use, such as vibrations, temperature fluctuations, and physical handling.
- Performance: High-quality connections minimize signal loss and interference, resulting in optimal circuit performance.
Types of Wire-to-Board Connections
There are several methods for connecting wires to circuit boards, each with its own advantages and applications. The most common types of wire-to-board connections include:
Through-Hole Soldering
Through-hole soldering is a traditional and widely used method for connecting wires to circuit boards. This technique involves inserting the wire through a pre-drilled hole in the board and soldering it in place.
Advantages of Through-Hole Soldering
- Strong mechanical connection
- Easy to inspect and repair
- Suitable for high-power applications
Disadvantages of Through-Hole Soldering
- Requires more board space compared to surface mount techniques
- Time-consuming process, especially for large numbers of connections
Surface Mount Soldering
Surface mount soldering is a more modern approach to wire-to-board connections. In this method, the wire is soldered directly to a pad on the surface of the circuit board, without the need for a through-hole.
Advantages of Surface Mount Soldering
- Saves board space
- Faster assembly process
- Allows for higher component density
Disadvantages of Surface Mount Soldering
- Requires specialized tools and skills
- More difficult to inspect and repair compared to through-hole connections
Crimping and Connectors
Crimping and connectors provide a solderless solution for wire-to-board connections. This method involves attaching a connector to the end of the wire and mating it with a corresponding connector on the circuit board.
Advantages of Crimping and Connectors
- Quick and easy assembly
- Allows for easy disconnection and reconnection
- Ideal for applications that require frequent wire removal or replacement
Disadvantages of Crimping and Connectors
- Requires additional components (connectors)
- May be more expensive than Soldering Methods
- Connectors can be bulky compared to soldered connections
Preparing the Wire for Connection
Before making a wire-to-board connection, it is essential to properly prepare the wire. This process involves stripping the insulation, tinning the wire, and ensuring the correct wire gauge is used.
Stripping the Wire
To strip the wire, use a wire stripper tool to remove a portion of the insulation at the end of the wire. The length of the stripped portion depends on the connection method and the size of the soldering pad or through-hole.
Tinning the Wire
Tinning the wire involves applying a small amount of solder to the exposed strands. This process helps to prevent the strands from fraying and makes it easier to create a secure connection. To tin the wire:
- Heat the soldering iron and apply a small amount of solder to the tip.
- Hold the wire in one hand and the soldering iron in the other.
- Touch the solder to the wire and the soldering iron simultaneously, allowing the solder to flow evenly over the strands.
Choosing the Right Wire Gauge
Selecting the appropriate wire gauge is crucial for ensuring a safe and reliable connection. The wire gauge refers to the diameter of the wire, with larger numbers indicating thinner wires. Consider the following factors when choosing the wire gauge:
- Current carrying capacity: Ensure the wire can handle the expected current without overheating.
- Voltage drop: Thicker wires minimize voltage drop over long distances.
- Mechanical strength: Thicker wires provide greater mechanical strength and durability.
Wire Gauge | Current Capacity (Amperes) | Resistance (Ohms/1000 ft) |
---|---|---|
20 | 5 | 10.15 |
18 | 7 | 6.385 |
16 | 10 | 4.016 |
14 | 15 | 2.525 |
12 | 20 | 1.588 |
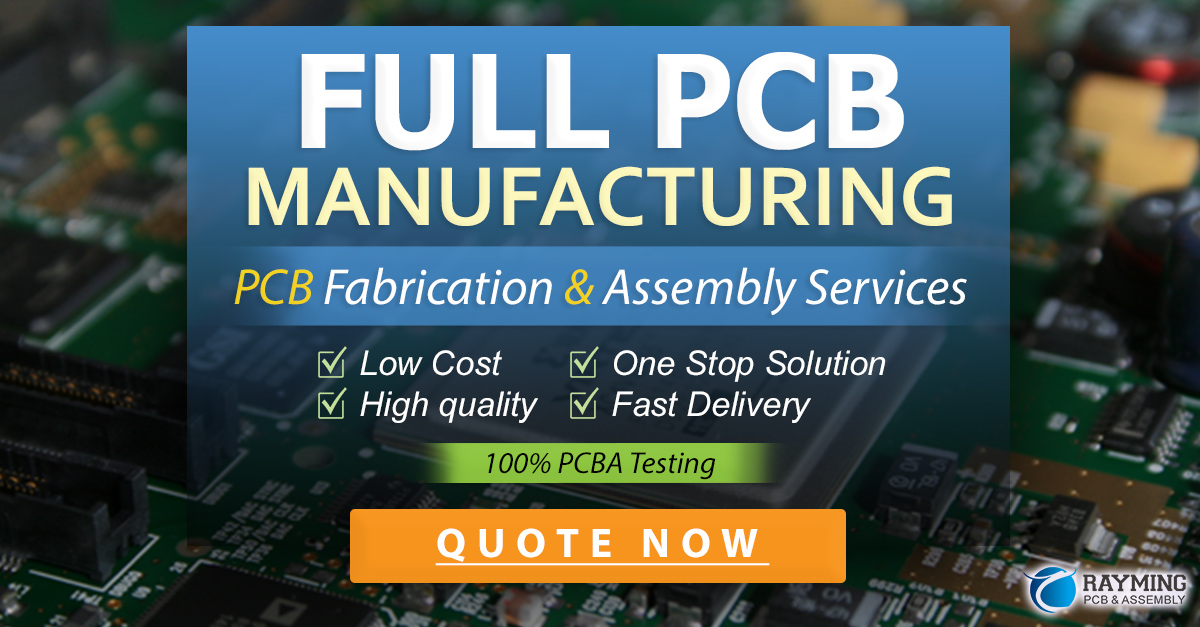
Making the Connection
With the wire prepared and the connection method chosen, it’s time to make the wire-to-board connection. Follow these step-by-step instructions for each connection method:
Through-Hole Soldering
- Insert the tinned wire into the through-hole.
- Hold the wire in place with one hand and the soldering iron in the other.
- Touch the soldering iron to the pad and the wire simultaneously.
- Apply solder to the joint, allowing it to flow evenly around the wire and pad.
- Remove the soldering iron and let the joint cool.
Surface Mount Soldering
- Position the tinned wire on the soldering pad.
- Hold the wire in place with tweezers or a clamp.
- Touch the soldering iron to the wire and pad simultaneously.
- Apply solder to the joint, allowing it to flow evenly around the wire and pad.
- Remove the soldering iron and let the joint cool.
Crimping and Connectors
- Strip the wire and insert it into the connector.
- Use a crimping tool to secure the wire in the connector.
- Ensure the wire is fully inserted and the crimp is tight.
- Plug the connector into the corresponding socket on the circuit board.
Best Practices for Wire-to-Board Connections
To ensure reliable and long-lasting wire-to-board connections, follow these best practices:
Use the Right Tools
Invest in high-quality tools, such as soldering irons, wire strippers, and crimping tools. Proper tools make the connection process easier and more precise.
Keep the Work Area Clean
A clean work area is essential for making good connections. Remove any dirt, grease, or debris from the circuit board and wire before making the connection.
Use Flux for Soldering
Flux helps to remove oxides and impurities from the metal surfaces, allowing the solder to flow more easily and create a stronger bond. Apply a small amount of flux to the soldering pad and wire before soldering.
Avoid Overheating
Excessive heat can damage the wire, insulation, and Circuit board components. Use the appropriate soldering iron temperature and work quickly to minimize heat exposure.
Inspect the Connection
After making the connection, visually inspect the joint to ensure it is secure and free of any defects, such as bridging or cold solder joints.
Troubleshooting Common Issues
Even with the best practices, issues can arise when making wire-to-board connections. Here are some common problems and their solutions:
Cold Solder Joints
A cold solder joint occurs when the solder fails to bond properly with the wire and pad. Symptoms include a dull, grainy appearance and poor electrical conductivity. To fix a cold solder joint:
- Reheat the joint with the soldering iron.
- Apply additional flux and solder if necessary.
- Ensure the wire and pad are heated evenly and the solder flows smoothly.
Bridging
Bridging occurs when solder inadvertently connects two or more pads or traces on the circuit board. To remove a solder bridge:
- Use solder wick or a desoldering pump to remove the excess solder.
- If necessary, use a soldering iron to carefully separate the connected pads or traces.
Damaged Insulation
If the wire insulation is damaged during the connection process, it can lead to short circuits and other issues. To prevent this:
- Use heat shrink tubing or electrical tape to cover any exposed wire.
- Exercise caution when stripping the wire and avoid nicking the insulation with the wire stripper.
FAQ
-
What is the best soldering iron temperature for making wire-to-board connections?
The ideal soldering iron temperature depends on the type of solder and the size of the connection. Generally, a temperature between 600°F and 700°F (315°C and 370°C) is suitable for most applications. -
How much insulation should I strip from the wire?
The amount of insulation to strip depends on the connection method and the size of the soldering pad or through-hole. As a general rule, strip just enough insulation to allow the wire to fit securely in the connection point, usually about 1/4 inch (6mm). -
Can I use any type of wire for circuit board connections?
While you can use various types of wire, it’s essential to choose a wire that is appropriate for your application. Consider factors such as current carrying capacity, voltage rating, and insulation material when selecting a wire. -
How do I know if my soldered connection is strong enough?
A well-soldered connection should be shiny, smooth, and have a concave profile. You can gently tug on the wire to ensure it is securely attached to the pad. If the connection is dull, grainy, or easily separates from the pad, it may be a cold solder joint that requires reheating. -
Can I reuse a wire that has been previously soldered?
Yes, you can reuse a wire that has been previously soldered. However, ensure to remove any old solder and debris from the wire before making a new connection. If the wire is excessively oxidized or the insulation is damaged, it’s best to use a new wire.
Conclusion
Connecting wires to circuit boards is a critical skill for anyone working with electronics. By understanding the various connection methods, proper wire preparation techniques, and best practices, you can create reliable and durable wire-to-board connections. Whether you choose through-hole soldering, surface mount soldering, or crimping and connectors, always prioritize safety, precision, and attention to detail. With practice and patience, you’ll be able to master the art of wire-to-board connections and take your electronics projects to the next level.
No responses yet