Overview of the PCB Manufacturing Process
The printed circuit board (PCB) manufacturing process is a complex, multi-step procedure that takes place inside specialized factories. The basic steps to manufacture a PCB include:
- Design and Engineering
- Plotting Film
- Inner Layer Processing
- Lamination
- Drilling
- Outer Layer Processing
- Solder Mask and Silkscreen
- Surface Finishing
- Electrical Testing
- Final Inspection and Shipping
Let’s dive deeper into each of these steps to understand exactly how PCBs are made from start to finish.
Step 1: PCB Design and Engineering
Designing the Circuit
The PCB manufacturing process begins with the design of the printed circuit board itself. An electronics engineer first creates a schematic diagram that defines the electrical connections and components required for the PCB to function as intended. This schematic is like a blueprint for the PCB.
PCB Layout
Using computer-aided design (CAD) software, a PCB designer then takes the schematic and creates the physical layout of the board. This PCB layout determines where the electrical components will be placed and how they will be connected with copper traces.
The designer must adhere to PCB design guidelines for things like:
- Board size and thickness
- Minimum trace width and spacing
- Drill hole sizes
- Component footprints
- Thermal considerations
Once the PCB layout is complete, a set of digital files called Gerber files are generated. These files contain all the data needed to physically fabricate and assemble the PCB, layer by layer.
Step 2: Plotting Film
Creating the Photomask
With the Gerber files, the PCB factory can create the photoplots (also called photomasks or film). These are plastic or glass sheets with the PCB pattern printed on them. There is one photoplot for each layer of the PCB.
The photoplots are made by converting the Gerber data into high-resolution images. A photoplotter machine prints these images onto plastic sheets using a laser or LEDs. The areas meant to be copper are left transparent, while the non-copper areas are printed in black.
Quality Check
After plotting, each photoplot is carefully inspected to ensure accuracy to the PCB design and check for any defects or scratches. Issues with the photomasks can create problems in the following manufacturing steps.
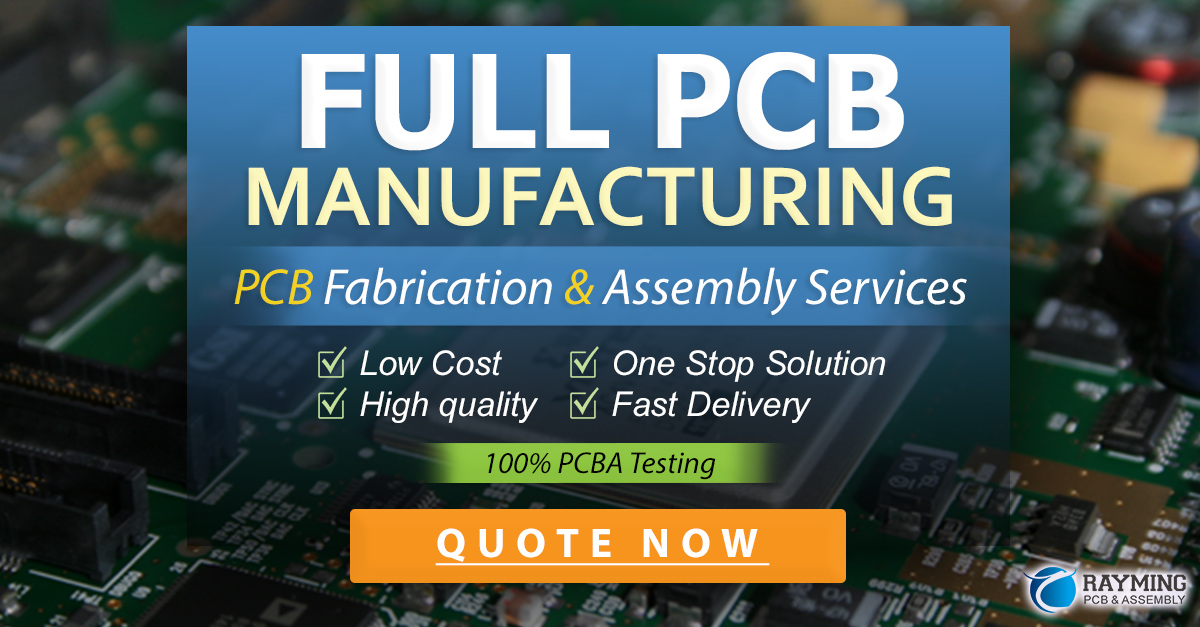
Step 3: Inner Layer Processing
Most PCBs have at least two layers, but complex designs may have 4, 8, 12 or more layers. For multi-layer PCBs, the inner layers are processed first before being laminated together.
Copper Cladding
The base material of a PCB is a thin, insulating board made of fiberglass or epoxy resin. For the inner layers, this base material comes pre-cladded with a thin layer of copper foil on both sides.
Applying the Resist
The copper-cladded board is covered with a light-sensitive film called photoresist. This photoresist is applied evenly across both sides of the board and then dried in an oven to harden it.
Exposing the Pattern
Next, the photomask for the inner layer is placed over the photoresist-covered board. This stack-up is then exposed to intense UV light. The UV light passes through the transparent areas of the photomask and chemically hardens the photoresist underneath. The black areas of the photomask block the UV light, leaving that photoresist unhardened.
Developing
After UV exposure, the board is “developed” by spraying it with an alkaline solution. This solution dissolves away the unhardened photoresist, exposing the bare copper underneath. The hardened photoresist remains, protecting the copper that will form the traces. This process is similar to developing a photograph.
Etching
The board is then put through an etching machine which sprays it with a chemical, typically an acidic cupric chloride solution. This etchant dissolves away all the exposed, unprotected copper, while the copper under the hardened photoresist remains untouched. What’s left is the copper trace pattern of the inner PCB Layer.
Stripping and Inspecting
Finally, the hardened photoresist is stripped off, revealing the complete copper pattern. The inner layer is inspected for any defects or irregularities before proceeding.
This entire process is repeated for every inner layer of the PCB. The number of inner layers can vary from just two to a dozen or more, depending on the complexity of the design.
Step 4: Lamination
With the inner layers complete, they need to be fused together into a single, solid board. This is done through a process called lamination.
Preparing the Stack-up
The inner layers are stacked in their proper sequence with insulating layers, called prepreg, between each one. Prepreg is a fiberglass fabric pre-impregnated with a resin that hardens when heated.
Copper foils are placed on the top and bottom of this stack to form the outer layers. This entire stack-up is then placed between two steel plates.
Lamination Press
The stack-up is placed into a lamination press. This machine applies intense heat and pressure to the stack. The heat causes the prepreg resin to melt and flow, while the pressure forces any air pockets out.
As the press cools, the resin hardens, fusing all the layers together into a solid board. The steel plates ensure the board remains flat during this process.
Preparing for Drilling
After lamination, the excess copper foil is trimmed off the edges of the board and it’s checked for any defects. The laminated board is now ready for drilling.
Step 5: Drilling
With the layers fused together, the next step is to drill holes through the board. These holes allow components to be mounted and electrically connected to the different layers.
Drilling Machine
The drilling is done by a computer-controlled drill machine. This machine reads drill files from the PCB design data that specify the size and location of each hole.
The drill bit sizes can range from 0.3mm to over 6mm, depending on the component requirements. High-speed steel or tungsten carbide drill bits are used to ensure clean, precise holes.
Deburring and Cleaning
After drilling, any burrs around the hole edges are removed in a deburring machine. The holes are then cleaned using a high-pressure water jet or a chemical desmear process to remove any debris.
Step 6: Outer Layer Processing
With the holes drilled, the outer layers of the PCB can be processed. This follows similar steps to the inner layer processing.
Copper Plating
First, the entire board, including the inside of the drilled holes, is plated with a thin layer of copper. This ensures electrical connectivity between the layers.
Applying the Resist
Like with the inner layers, a photoresist is applied to the outer layers and then hardened.
Exposing and Developing
The outer layer photomasks are aligned precisely with the drilled holes and then exposed to UV light. The photoresist is then developed, exposing the copper that needs to be etched away.
Plating and Etching
The exposed copper is plated with additional copper, followed by a thin layer of tin. This tin serves as an etch resist. The photoresist is then stripped away, and the board is etched. The tin protects the traces during etching and is then stripped off, leaving the final outer layer copper patterns.
Step 7: Solder Mask and Silkscreen
Applying Solder Mask
A solder mask is a protective coating applied to the outer layers of the PCB. It prevents solder from bridging between traces and pads during assembly.
The solder mask is applied as a liquid or dry film and then exposed and developed like the photoresist. It’s typically green, but can be other colors as well.
Silkscreen
The silkscreen is the white text and symbols you see on a PCB. It’s used to identify components, test points, and other features. The silkscreen is printed onto the solder mask using a silkscreen printer and then cured.
Step 8: Surface Finishing
The exposed copper pads on the PCB need a surface finish to protect them from oxidation and to enhance solderability during assembly. There are several types of surface finishes, including:
- HASL (Hot Air Solder Leveling)
- ENIG (Electroless Nickel Immersion Gold)
- OSP (Organic Solderability Preservative)
- Immersion Silver
- Immersion Tin
The choice of surface finish depends on the requirements of the components being used and the end-use environment of the PCB.
Step 9: Electrical Testing
Before the PCBs are shipped, they undergo rigorous electrical testing to ensure they function as intended. There are several types of tests:
Bare Board Testing
This tests for any shorts or opens in the PCB traces before components are assembled. It can be done with a flying probe tester or a bed-of-nails tester.
In-Circuit Testing (ICT)
After components are assembled, an ICT tests each component and verifies it’s correctly connected. This uses a bed-of-nails fixture to access test points on the board.
Functional Testing
This tests the complete functionality of the assembled PCB. It verifies that the board performs as intended in its end-use application.
Step 10: Final Inspection and Shipping
Visual Inspection
Before shipping, each PCB undergoes a final visual inspection. This checks for any visible defects, such as scratches, discoloration, or missing components.
Packaging and Shipping
The finished PCBs are then packaged for shipping. They’re typically placed in anti-static bags to protect them from electrostatic discharge (ESD) during transport. They may also be placed in vacuum-sealed moisture barrier bags if they’re being shipped to a high-humidity environment.
The packaged PCBs are then shipped to the customer or to the next stage of the product assembly process.
Frequently Asked Questions (FAQ)
1. How long does it take to manufacture a PCB?
The lead time for PCB manufacturing can vary depending on the complexity of the design, the number of layers, and the quantity ordered. Simple 2-layer PCBs can be manufactured in as little as 24 hours, while complex multi-layer boards can take several weeks.
2. What’s the difference between a prototype PCB and a production PCB?
Prototype PCBs are typically made in small quantities (1-100) to test and validate a design before mass production. They may be manufactured with different processes or materials compared to production PCBs to reduce cost and lead time. Production PCBs are made in larger quantities (100+) once the design is finalized and are manufactured with the processes and materials intended for the end-use product.
3. What are the most common PCB Materials?
The most common base material for PCBs is FR-4, which is a flame-retardant fiberglass-reinforced epoxy laminate. Other common materials include polyimide for high-temperature applications, Rogers materials for high-frequency RF applications, and aluminum for high-power LED applications.
4. What’s the smallest feature size that can be manufactured on a PCB?
The smallest feature size on a PCB is typically determined by the line width and spacing of the copper traces. Most PCB manufacturers can achieve a minimum line width and spacing of 3-4 mils (0.003-0.004 inches) with standard processes. More advanced processes can achieve 2 mils or less.
5. How are PCBs inspected for quality?
PCBs are inspected at various stages throughout the manufacturing process. This includes visual inspections for defects, automated optical inspection (AOI) to check for missing or misplaced components, x-ray inspection to check for internal defects, and electrical testing to verify functionality. The specific inspection methods used will depend on the PCB design and the quality requirements of the end customer.
Conclusion
The PCB manufacturing process is a complex, multi-step process that requires precision and attention to detail at every stage. From the initial design to the final inspection, each step plays a critical role in ensuring the quality and functionality of the end product.
By understanding this process, you can better appreciate the technology that goes into the electronic devices we use every day. The next time you look at a PCB, remember the journey it took through the factory to arrive in your hands.
No responses yet