What is a BGA Package?
A Ball Grid Array (BGA) is a surface-mount package that utilizes an array of solder balls on the bottom side of the package to connect to the PCB. The solder balls are arranged in a grid pattern, allowing for a higher density of interconnects compared to other packaging technologies. BGAs are commonly used for integrated circuits (ICs) that require a large number of connections, such as microprocessors, field-programmable gate arrays (FPGAs), and application-specific integrated circuits (ASICs).
Types of BGA Packages
There are several types of BGA packages, each with its own unique characteristics and applications. Some of the most common types include:
1. Plastic BGA (PBGA)
Plastic BGAs are the most widely used type of BGA package. They consist of a plastic substrate with a die attached to the top side and solder balls on the bottom side. PBGAs are cost-effective and offer good thermal and electrical performance.
2. Ceramic BGA (CBGA)
Ceramic BGAs use a ceramic substrate instead of plastic, providing better Thermal conductivity and dimensional stability. CBGAs are more expensive than PBGAs but are preferred for high-reliability applications, such as aerospace and defense.
3. Tape BGA (TBGA)
Tape BGAs utilize a flexible tape substrate, which allows for thinner packages and improved electrical performance. TBGAs are commonly used in mobile devices and other space-constrained applications.
4. Fine-Pitch BGA (FBGA)
Fine-Pitch BGAs have a smaller ball pitch (the distance between the centers of adjacent solder balls) than standard BGAs, enabling higher pin counts and increased package density. FBGAs are used in high-performance applications that require a large number of interconnects.
Benefits of BGA in PCB assembly
BGA packages offer several advantages over other packaging technologies, making them an attractive choice for PCB assembly. Some of the key benefits include:
1. High Pin Count
BGAs allow for a large number of interconnects in a small package size, making them ideal for complex, high-density PCB designs. The ability to accommodate hundreds or even thousands of pins enables the use of advanced ICs with extensive functionality.
2. Smaller Footprint
Compared to other packaging technologies, BGAs have a smaller footprint for a given pin count. This space-saving characteristic is crucial in modern electronic devices, where miniaturization is a key driver.
3. Improved Electrical Performance
The short, uniform length of the solder ball connections in a BGA package results in improved electrical performance, including reduced inductance and resistance. This leads to faster signal transmission and lower power consumption.
4. Enhanced Thermal Management
BGAs provide better thermal management than other package types due to the large number of solder balls that act as thermal paths. This helps dissipate heat more efficiently, reducing the risk of thermal-related failures.
5. Increased Reliability
The solder ball connections in a BGA package are less susceptible to mechanical stress and thermal cycling than the leads in other package types. This increased reliability is particularly important in applications that are subject to harsh environmental conditions.
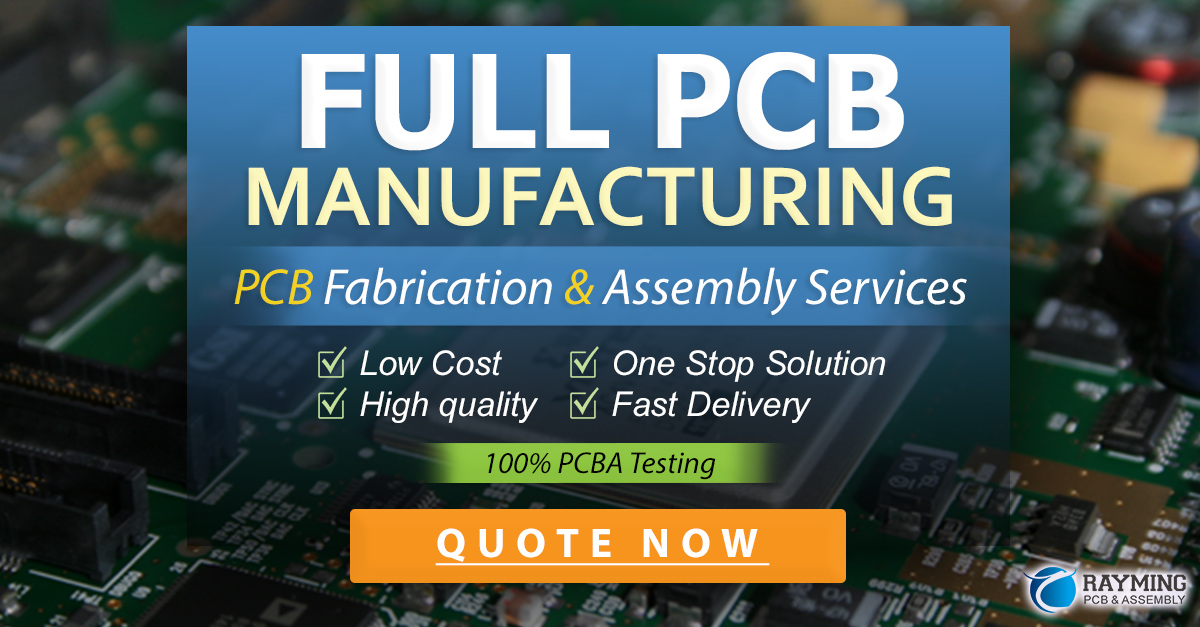
BGA Inspection Techniques
Ensuring the quality and reliability of BGA solder joints is critical in PCB assembly. Several inspection techniques are used to detect defects and verify the integrity of BGA connections:
1. X-Ray Inspection
X-ray inspection is the most common method for examining BGA solder joints, as it allows for non-destructive visualization of the connections beneath the package. Both 2D and 3D X-ray systems are used to detect defects such as voids, bridging, and insufficient solder.
2. Automated Optical Inspection (AOI)
AOI systems use cameras and image processing algorithms to inspect the surface of the PCB, including the BGA package. While AOI cannot directly inspect the solder joints beneath the package, it can detect surface-level defects such as misalignment, missing components, and solder defects on exposed pads.
3. Boundary Scan Testing
Boundary scan testing, also known as JTAG testing, is a functional test method that uses dedicated hardware and software to verify the connectivity and functionality of BGA devices. This technique is particularly useful for detecting open and short circuits in BGA connections.
4. Thermal Imaging
Thermal imaging can be used to detect thermal-related issues in BGA packages, such as hot spots caused by poor solder connections or inadequate thermal management. Infrared cameras are used to visualize the temperature distribution across the PCB and identify areas of concern.
Conclusion
BGA packages have revolutionized PCB assembly by offering high pin counts, smaller footprints, and improved electrical and thermal performance. With various types of BGA packages available, designers can choose the most suitable option for their specific application. However, the complexity of BGA solder joints requires specialized inspection techniques to ensure quality and reliability. By understanding the benefits and challenges associated with BGA in PCB assembly, manufacturers can leverage this technology to create advanced, high-performance electronic devices.
Frequently Asked Questions (FAQ)
1. What is the difference between a BGA and a QFN package?
A BGA package has an array of solder balls on the bottom side for connection to the PCB, while a Quad Flat No-lead (QFN) package has exposed pads on the bottom side. QFNs have a smaller footprint but lower pin counts compared to BGAs.
2. Can BGA packages be reworked?
Yes, BGA packages can be reworked, but it requires specialized equipment and expertise. Rework typically involves removing the defective package, cleaning the site, and soldering a new package in place. Proper temperature control and alignment are critical to ensure a successful rework.
3. What are the challenges associated with BGA assembly?
Some of the challenges associated with BGA assembly include:
– Ensuring proper alignment of the package to the PCB
– Controlling the reflow temperature profile to achieve reliable solder joints
– Inspecting the solder joints beneath the package for defects
– Reworking defective packages without damaging the PCB or neighboring components
4. How does the ball pitch affect BGA assembly?
A smaller ball pitch in BGA packages, such as those found in Fine-Pitch BGAs, requires tighter placement accuracy and more precise control of the reflow process. Smaller pitches also make inspection and rework more challenging, as the solder joints are closer together.
5. What is the role of underfill in BGA assembly?
Underfill is an epoxy material that is applied between the BGA package and the PCB after soldering. It helps to distribute mechanical stress, improve thermal management, and protect the solder joints from environmental factors. Underfill is particularly important in applications subject to high stress or thermal cycling.
BGA Package Type | Substrate Material | Key Characteristics | Typical Applications |
---|---|---|---|
Plastic BGA (PBGA) | Plastic | Cost-effective, good thermal and electrical performance | Consumer electronics, telecommunications |
Ceramic BGA (CBGA) | Ceramic | High thermal conductivity, dimensional stability | Aerospace, defense, high-reliability applications |
Tape BGA (TBGA) | Flexible tape | Thin profile, improved electrical performance | Mobile devices, space-constrained applications |
Fine-Pitch BGA (FBGA) | Various | Smaller ball pitch, higher pin counts | High-performance computing, networking equipment |
Table 1: Comparison of common BGA package types
Inspection Technique | Capability | Limitations |
---|---|---|
X-Ray Inspection | Non-destructive visualization of solder joints beneath package | Cannot detect surface-level defects |
Automated Optical Inspection (AOI) | Detects surface-level defects, such as misalignment and solder defects on exposed pads | Cannot directly inspect solder joints beneath package |
Boundary Scan Testing | Verifies connectivity and functionality of BGA devices | Requires dedicated hardware and software |
Thermal Imaging | Detects thermal-related issues, such as hot spots caused by poor solder connections | Cannot directly detect solder joint defects |
Table 2: Comparison of BGA inspection techniques
No responses yet