Introduction to Immersion Silver
Immersion silver is a popular surface finish for printed circuit boards (PCBs) that provides excellent solderability, conductivity, and shelf life. This RoHS-Compliant finish has gained significant traction in the electronics industry due to its compatibility with lead-free soldering processes and its ability to meet stringent environmental regulations. In this comprehensive article, we will delve into the intricacies of immersion silver PCB finishes, exploring their benefits, applications, and key considerations for manufacturers and designers.
The RoHS Directive and Its Impact on PCB Finishes
The Restriction of Hazardous Substances (RoHS) Directive, introduced by the European Union in 2006, has revolutionized the electronics industry by limiting the use of six hazardous materials in electrical and electronic products. These restricted substances include lead, mercury, cadmium, hexavalent chromium, polybrominated biphenyls (PBB), and polybrominated diphenyl ethers (PBDE). The directive aims to minimize the environmental impact of electronic waste and promote the development of eco-friendly alternatives.
As a result of the RoHS Directive, lead-based solders and finishes have been largely phased out, paving the way for lead-free alternatives like immersion silver. PCB manufacturers have had to adapt their processes and materials to comply with these regulations while maintaining the performance and reliability of their products.
The Immersion Silver Process
Immersion silver is an electroless plating process that deposits a thin layer of silver onto the copper surface of a PCB. The process involves the following steps:
- Cleaning: The PCB is thoroughly cleaned to remove any contaminants or oxide layers from the copper surface.
- Microetching: A mild etching solution is applied to the PCB to create a uniform surface texture and improve silver adhesion.
- Pre-dip: The PCB is immersed in a pre-dip solution to prevent oxidation and ensure consistent silver deposition.
- Silver Immersion: The PCB is immersed in the immersion silver solution, where silver ions replace copper ions on the surface through a displacement reaction.
- Rinsing: The PCB is rinsed with deionized water to remove any residual chemicals.
- Drying: The PCB is dried using hot air or nitrogen to prevent water spots and ensure a clean, uniform surface finish.
The resulting immersion silver layer is typically 0.1 to 0.3 μm thick and provides excellent solderability and conductivity.
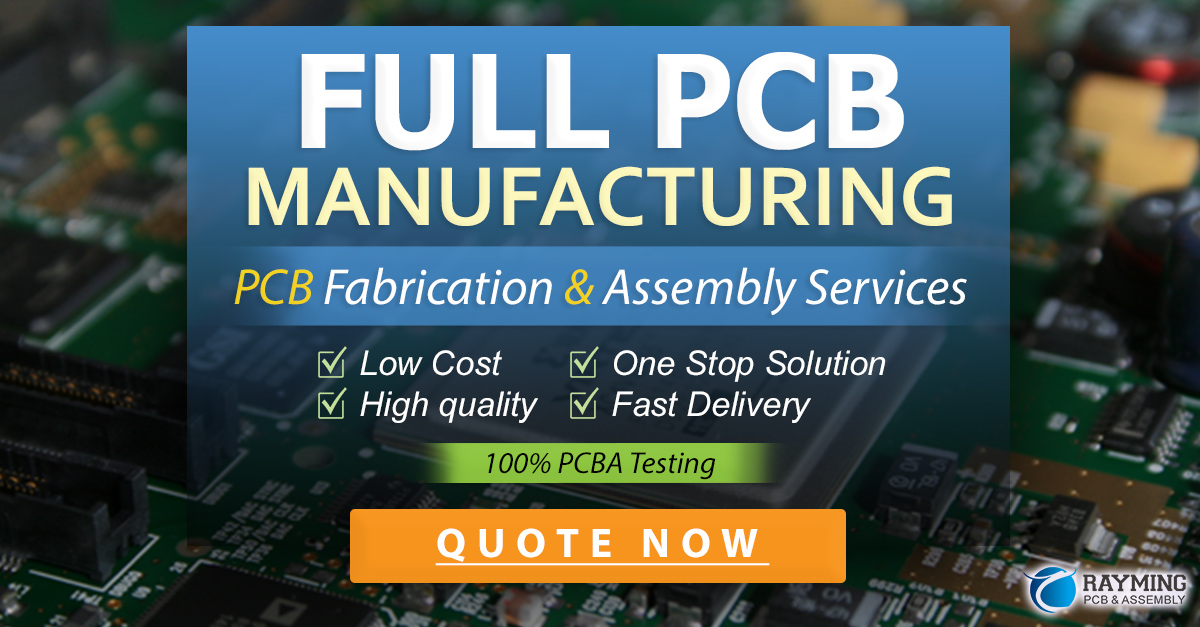
Benefits of Immersion Silver PCB Finishes
Excellent Solderability
Immersion silver offers superior solderability compared to other lead-free finishes like Organic Solderability Preservatives (OSP) and Electroless Nickel Immersion Gold (ENIG). The silver layer provides a flat, uniform surface that promotes strong solder joint formation and minimizes the risk of defects like bridging or voiding.
Extended Shelf Life
PCBs with immersion silver finishes have an extended shelf life of up to 12 months, depending on storage conditions. The silver layer acts as a barrier against oxidation and contamination, ensuring that the PCB remains solderable even after prolonged storage.
RoHS Compliance
As a lead-free and RoHS-compliant finish, immersion silver enables PCB manufacturers to meet strict environmental regulations and cater to markets that demand eco-friendly products.
Cost-Effectiveness
Compared to other lead-free finishes like ENIG, immersion silver is a more cost-effective option. The process requires fewer chemicals and less processing time, resulting in lower production costs.
Compatibility with Multiple Soldering Processes
Immersion silver is compatible with various soldering processes, including wave soldering, reflow soldering, and hand soldering. This versatility makes it suitable for a wide range of applications and manufacturing requirements.
Applications of Immersion Silver PCB Finishes
Consumer Electronics
Immersion silver is widely used in consumer electronics, such as smartphones, tablets, laptops, and gaming consoles. These devices require high-density interconnects and reliable solder joints to ensure optimal performance and longevity.
Automotive Electronics
The automotive industry has stringent requirements for PCB finishes due to the harsh operating conditions and long product lifecycles. Immersion silver provides the necessary solderability, reliability, and durability for automotive electronic components, such as engine control units, infotainment systems, and safety devices.
Medical Devices
Medical devices demand high reliability and long-term stability to ensure patient safety and effectiveness. Immersion silver PCB finishes are used in various medical applications, including diagnostic equipment, monitoring systems, and implantable devices.
Industrial Equipment
Industrial equipment, such as process control systems, automation devices, and power electronics, requires robust and reliable PCBs. Immersion silver finishes provide the necessary solderability and durability to withstand harsh industrial environments.
Key Considerations for Immersion Silver PCB Finishes
Design Guidelines
When designing PCBs with immersion silver finishes, it is essential to follow appropriate design guidelines to ensure optimal performance and manufacturability. Some key considerations include:
- Maintaining adequate pad sizes and spacings to accommodate the silver layer thickness
- Avoiding overly fine pitch components that may be challenging to solder
- Ensuring proper solder mask alignment and coverage to prevent silver migration
Process Control
Immersion silver plating requires strict process control to achieve consistent and high-quality results. Manufacturers must monitor and maintain key parameters, such as solution composition, temperature, pH, and immersion time, to ensure uniform silver deposition and prevent defects like discoloration or excessive silver growth.
Storage and Handling
To maintain the solderability and shelf life of immersion silver PCBs, proper storage and handling practices must be followed. PCBs should be stored in a cool, dry environment with minimal exposure to humidity, ultraviolet light, and contaminants. When handling PCBs, operators should wear gloves to prevent skin oils and salts from contaminating the silver surface.
Compatibility with Other Components
When using immersion silver PCBs in assemblies, it is crucial to consider the compatibility of the finish with other components and materials. For example, some connectors and switches may have specific plating requirements that may not be compatible with immersion silver. Designers should consult with component manufacturers and conduct compatibility tests to ensure proper functionality and reliability.
Frequently Asked Questions (FAQ)
1. How does immersion silver compare to other lead-free PCB finishes?
Immersion silver offers several advantages over other lead-free finishes, such as ENIG and OSP. It provides superior solderability, extended shelf life, and cost-effectiveness. However, ENIG may be preferred for applications that require gold wire bonding, while OSP may be suitable for short-term storage and quick assembly.
2. Can immersion silver be used for High-frequency PCBs?
Yes, immersion silver is suitable for high-frequency PCBs due to its low electrical resistance and smooth surface finish. The thin silver layer minimizes signal loss and distortion, making it an excellent choice for high-speed digital and RF applications.
3. How does the thickness of the immersion silver layer affect solderability?
The optimal thickness of the immersion silver layer is typically between 0.1 and 0.3 μm. Thinner layers may not provide adequate protection against oxidation and may result in reduced solderability over time. Thicker layers, on the other hand, may lead to excess silver growth and potential issues with fine-pitch components.
4. Can immersion silver PCBs be reworked or repaired?
Yes, immersion silver PCBs can be reworked or repaired using standard soldering techniques. However, the rework process may expose the underlying copper, requiring the application of a fresh silver layer or the use of a solderable coating to prevent oxidation and ensure reliable solder joints.
5. How can I ensure the quality and consistency of immersion silver PCBs from my supplier?
To ensure the quality and consistency of immersion silver PCBs, it is essential to work with a reputable and experienced supplier who follows strict process controls and quality assurance procedures. Request documentation, such as plating thickness measurements, solderability test results, and ionic contamination reports, to verify the conformance of the PCBs to your specifications. Regular audits and on-site inspections can also help maintain a high level of quality and consistency.
Conclusion
Immersion silver PCB finishes have emerged as a popular and reliable choice for RoHS-compliant electronics manufacturing. With its excellent solderability, extended shelf life, and cost-effectiveness, immersion silver offers numerous benefits for a wide range of applications, from consumer electronics to automotive and medical devices.
By understanding the intricacies of the immersion silver process, its advantages, and key considerations for design and manufacturing, engineers and managers can make informed decisions when selecting PCB finishes for their products. As the electronics industry continues to evolve and environmental regulations become more stringent, immersion silver is poised to remain a preferred choice for PCB finishes in the years to come.
Finish | Thickness (μm) | Shelf Life (months) | Solderability | Cost |
---|---|---|---|---|
Immersion Ag | 0.1 – 0.3 | 12 | Excellent | $ |
ENIG | 3 – 8 | 12+ | Great | $$$ |
OSP | 0.2 – 0.5 | 6 | Good | $ |
HASL | 1 – 20 | 12+ | Great | $ |
Table: Comparison of common PCB finishes
No responses yet