What is PCB impedance?
PCB impedance refers to the opposition to the flow of electrical current in a printed circuit board (PCB). It is a critical factor in the design of high-speed digital and RF circuits, where signal integrity and electromagnetic compatibility (EMC) are of utmost importance. Impedance is measured in ohms (Ω) and is composed of two components: resistance and reactance.
Resistance
Resistance is the opposition to the flow of direct current (DC) in a circuit. It is determined by the material properties and geometry of the conductors in the PCB. Factors that affect resistance include:
- Conductor material (e.g., copper, gold, silver)
- Conductor thickness
- Conductor width
- Conductor length
Reactance
Reactance is the opposition to the flow of alternating current (AC) in a circuit. It is determined by the capacitance and inductance of the conductors in the PCB. Factors that affect reactance include:
- Dielectric Constant of the PCB substrate
- Spacing between conductors
- Frequency of the signals
- Length of the conductors
Why is PCB Impedance Control Important?
PCB impedance control is critical for several reasons:
-
Signal Integrity: Impedance mismatches can cause reflections and distortions in high-speed signals, leading to errors and reduced performance.
-
EMC: Poor impedance control can result in increased electromagnetic interference (EMI) and reduced electromagnetic compatibility (EMC), which can cause problems with nearby electronic devices.
-
Power Efficiency: Impedance mismatches can result in power loss and reduced efficiency, which can be problematic in power-sensitive applications such as mobile devices and IoT sensors.
-
Reliability: Proper impedance control can help ensure the long-term reliability of the PCB by reducing stress on components and minimizing the risk of failures due to signal integrity issues.
How to Control PCB Impedance
There are several techniques that can be used to control PCB impedance:
Trace Width and Spacing
One of the most effective ways to control impedance is by adjusting the width and spacing of the traces on the PCB. The characteristic impedance of a trace is determined by its geometry and the properties of the surrounding Dielectric Material.
The characteristic impedance of a microstrip trace (a trace on the outer layer of the PCB) can be calculated using the following formula:
Z0 = 87 / √(εr + 1.41) * ln(5.98 * h / (0.8 * w + t))
Where:
– Z0 is the characteristic impedance in ohms
– εr is the dielectric constant of the substrate
– h is the thickness of the substrate in mils
– w is the width of the trace in mils
– t is the thickness of the trace in mils
For a stripline trace (a trace embedded in the inner layers of the PCB), the characteristic impedance can be calculated using:
Z0 = 60 / √εr * ln(4 * h / (0.67 * π * (0.8 * w + t)))
By adjusting the width and spacing of the traces, designers can achieve the desired characteristic impedance for their circuits.
Dielectric Materials
The choice of dielectric material can also have a significant impact on PCB impedance. Different materials have different dielectric constants, which affect the capacitance and characteristic impedance of the traces.
Some common PCB substrate materials and their dielectric constants are:
Material | Dielectric Constant (εr) |
---|---|
FR-4 | 4.2 – 4.5 |
Rogers 4003 | 3.38 |
Rogers 4350 | 3.48 |
Polyimide | 3.5 |
Teflon | 2.1 |
By selecting a substrate material with the appropriate dielectric constant, designers can help ensure proper impedance control in their PCBs.
Terminations
Terminations are another important tool for controlling PCB impedance. When a signal reaches the end of a trace, it can reflect back and cause distortions if the impedance is not properly matched. Terminations are used to absorb these reflections and maintain signal integrity.
There are several types of terminations commonly used in PCB design:
-
Series Termination: A resistor is placed in series with the signal source to match the impedance of the trace. This type of termination is simple and effective, but can limit the rise time of the signal.
-
Parallel Termination: A resistor is placed in parallel with the load to match the impedance of the trace. This type of termination allows for faster rise times, but consumes more power than series termination.
-
Thevenin Termination: A combination of series and parallel resistors is used to match the impedance of the trace. This type of termination provides a compromise between rise time and power consumption.
-
AC Termination: A capacitor is placed in series with a resistor to provide frequency-dependent impedance matching. This type of termination is useful for high-frequency signals.
The choice of termination depends on the specific requirements of the circuit, such as rise time, power consumption, and signal frequency.
Differential Pairs
Differential signaling is a technique where two complementary signals are transmitted on adjacent traces. This approach offers several advantages over single-ended signaling, including improved noise immunity and reduced EMI.
To maintain the benefits of differential signaling, it is important to ensure that the two traces in a differential pair have well-controlled impedance. This can be achieved by carefully routing the traces to maintain a consistent spacing and by using appropriate terminations.
The characteristic impedance of a differential pair can be calculated using:
Zdiff = 2 * Z0 * (1 - Kx) / (1 - Kx * tanh(Kx * l / h))
Where:
– Zdiff is the differential characteristic impedance in ohms
– Z0 is the characteristic impedance of a single trace in ohms
– Kx is the coupling factor between the traces (typically 0.6 to 0.8)
– l is the length of the traces in mils
– h is the spacing between the traces in mils
By properly designing differential pairs, designers can achieve high-speed, low-noise signaling in their PCBs.
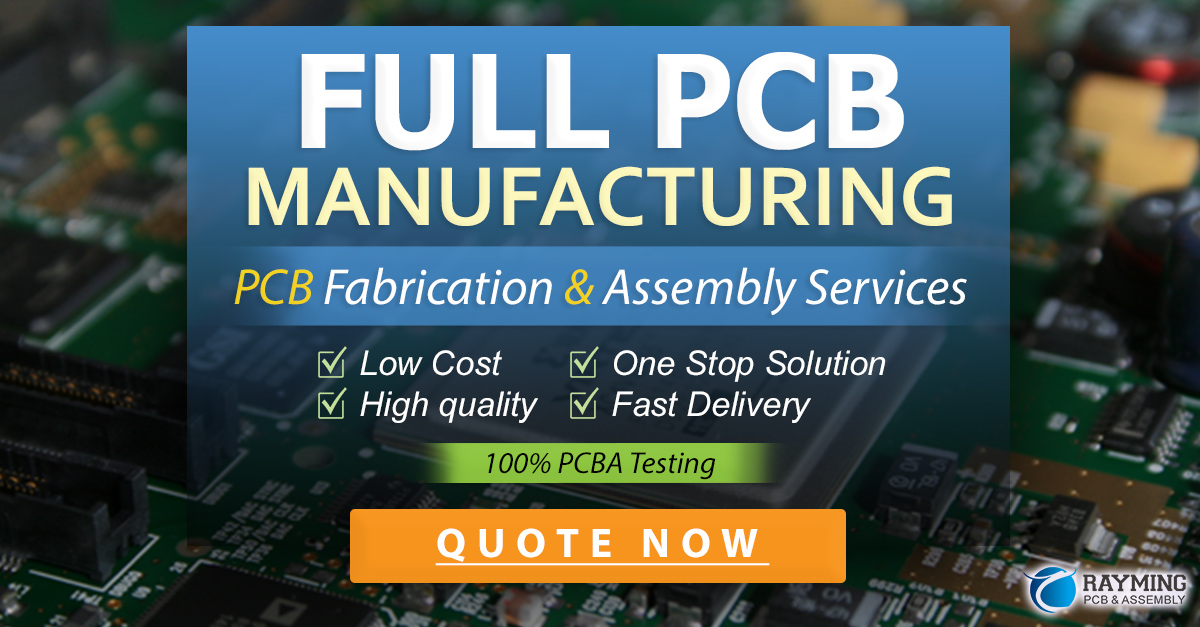
PCB Impedance Control Techniques
In addition to the basic techniques described above, there are several more advanced methods for controlling PCB impedance:
Impedance Matching Networks
Impedance matching networks are circuits designed to match the impedance of a source to the impedance of a load. These networks can be used to improve power transfer, reduce reflections, and maintain signal integrity.
There are several types of impedance matching networks, including:
- L-Network: A simple network consisting of a series inductor and a shunt capacitor or a series capacitor and a shunt inductor.
- Pi-Network: A network consisting of two shunt components and one series component, arranged in a pi configuration.
- T-Network: A network consisting of two series components and one shunt component, arranged in a T configuration.
- Stub Matching: A technique where a short or open-circuited transmission line (stub) is used to cancel out reflections.
The choice of impedance matching network depends on factors such as the Frequency Range, bandwidth, and power handling requirements of the circuit.
Equalization Techniques
Equalization is a signal processing technique used to compensate for the frequency-dependent attenuation and phase shift that occurs in transmission lines. By applying equalization to the signal, designers can improve the eye diagram and reduce bit error rates in high-speed digital circuits.
There are two main types of equalization:
-
Pre-Emphasis: A technique where the high-frequency components of the signal are boosted before transmission to compensate for the attenuation that occurs in the transmission line.
-
De-Emphasis: A technique where the low-frequency components of the signal are attenuated before transmission to reduce the intersymbol interference (ISI) caused by the limited bandwidth of the transmission line.
Equalization can be implemented using passive components, such as resistors and capacitors, or active components, such as op-amps and transistors.
Spread Spectrum Clocking
Spread spectrum clocking (SSC) is a technique used to reduce the peak electromagnetic emissions from a digital circuit by modulating the clock frequency. By spreading the energy of the clock signal over a wider frequency range, SSC can help designers meet EMC requirements while still maintaining good signal integrity.
There are two main types of SSC modulation:
- Center Spread: The clock frequency is modulated symmetrically around the nominal frequency, with the maximum deviation typically set to -0.5% to +0.5%.
- Down Spread: The clock frequency is modulated below the nominal frequency, with the maximum deviation typically set to -1% to 0%.
SSC can be implemented using a phase-locked loop (PLL) with a modulation input, or by using a spread-spectrum clock generator IC.
FAQ
Q1: What is the difference between microstrip and stripline transmission lines?
A1: Microstrip transmission lines are traces routed on the outer layers of a PCB, with a ground plane on one side. Stripline transmission lines are traces routed on the inner layers of a PCB, with ground planes on both sides. Microstrip lines have higher characteristic impedance and are easier to route, but are more susceptible to EMI. Stripline lines have lower characteristic impedance and are more immune to EMI, but require more complex routing.
Q2: What is the purpose of a via fence?
A2: A via fence is a row of closely spaced vias used to provide a low-impedance return path for high-speed signals. By placing a via fence along the edge of a signal trace, designers can reduce the loop area and minimize the inductance of the return path. This helps to maintain signal integrity and reduce EMI.
Q3: What is the difference between single-ended and differential signaling?
A3: Single-ended signaling uses one signal trace and one ground return path. Differential signaling uses two complementary signal traces and a ground return path. Differential signaling offers several advantages over single-ended signaling, including improved noise immunity, reduced EMI, and higher data rates. However, differential signaling requires more complex routing and termination techniques.
Q4: What is the purpose of a stitching capacitor?
A4: A stitching capacitor is a small capacitor placed between the power and ground planes of a PCB to provide a low-impedance path for high-frequency currents. By using stitching capacitors, designers can reduce the impedance of the power distribution network (PDN) and minimize the noise coupled to sensitive circuits. Stitching capacitors are typically placed near the power pins of ICs and other components.
Q5: What is the difference between AC and DC termination?
A5: AC termination uses a series resistor and capacitor to provide frequency-dependent impedance matching. DC termination uses a single resistor to provide a fixed impedance match. AC termination is useful for high-frequency signals, as it can provide a better match over a wider frequency range. DC termination is simpler and consumes less power, but may not provide adequate matching at high frequencies.
Conclusion
PCB impedance control is a critical aspect of high-speed digital and RF circuit design. By carefully controlling the impedance of traces, choosing appropriate dielectric materials, using terminations and equalization techniques, and applying advanced techniques such as spread spectrum clocking, designers can achieve good signal integrity, reduce EMI, and ensure the reliability of their PCBs.
However, impedance control is a complex topic that requires a deep understanding of transmission line theory, circuit design, and PCB manufacturing processes. Designers must carefully balance the trade-offs between signal integrity, power consumption, and manufacturing cost to achieve the best possible performance for their applications.
As data rates continue to increase and circuit geometries continue to shrink, the challenges of PCB impedance control will only become more critical. By staying up-to-date with the latest techniques and technologies, and by working closely with PCB manufacturers and signal integrity experts, designers can overcome these challenges and create high-performance, reliable PCBs for a wide range of applications.
No responses yet