What is Soldering Flux and Why is it Used?
Soldering flux is a chemical cleaning agent used in the process of soldering electronic components onto printed circuit boards (PCBs). Its primary purpose is to remove oxidation and other contaminants from the metal surfaces being soldered, allowing for a stronger and more reliable connection.
Flux comes in various forms, including liquid, paste, and solid. It is typically applied to the PCB before soldering, either by brush, pen, or as a core within the solder wire itself.
The main functions of soldering flux include:
- Removing oxides and contaminants from the metal surfaces
- Preventing oxidation during the soldering process
- Improving the wetting characteristics of the solder
- Facilitating the flow of molten solder
- Enhancing the strength and reliability of the solder joint
Without flux, the solder may not adhere properly to the metal surfaces, resulting in weak or faulty connections.
Types of Soldering Flux
There are several types of soldering flux, each with its own characteristics and uses. The most common types include:
Rosin Flux
Rosin flux is the most widely used type of flux in electronics soldering. It is made from the sap of pine trees and is available in various grades, from non-activated (R) to fully activated (RA). Rosin flux is generally considered safe and easy to use, and it leaves a minimal residue that is typically non-corrosive.
Water-Soluble Flux
Water-soluble flux, also known as organic acid flux, is a more aggressive type of flux that provides excellent cleaning action. It is often used in industrial settings where a higher level of cleanliness is required. Water-soluble flux residue must be removed after soldering, as it can cause corrosion if left on the PCB.
No-Clean Flux
No-clean flux is designed to leave minimal residue that does not require cleaning after soldering. This type of flux is popular in high-volume production environments, as it eliminates the need for a separate cleaning step. However, no-clean flux may not provide the same level of cleaning action as other types of flux.
Why is it Important to Remove Flux Residue?
While flux is essential for successful soldering, it is equally important to remove any residue left behind after the soldering process. Flux residue can cause several issues if not properly cleaned, including:
-
Corrosion: Some types of flux, particularly water-soluble flux, can be corrosive if left on the PCB. Over time, this can lead to the deterioration of solder joints and other components.
-
Electrical interference: Flux residue can be conductive, which may cause short circuits or other electrical issues.
-
Aesthetics: Flux residue can give the PCB an unsightly appearance, which may be undesirable for certain applications.
-
Contamination: In some cases, flux residue can contaminate other components or materials used in the manufacturing process.
To ensure the long-term reliability and performance of the PCB, it is crucial to remove flux residue thoroughly after soldering.
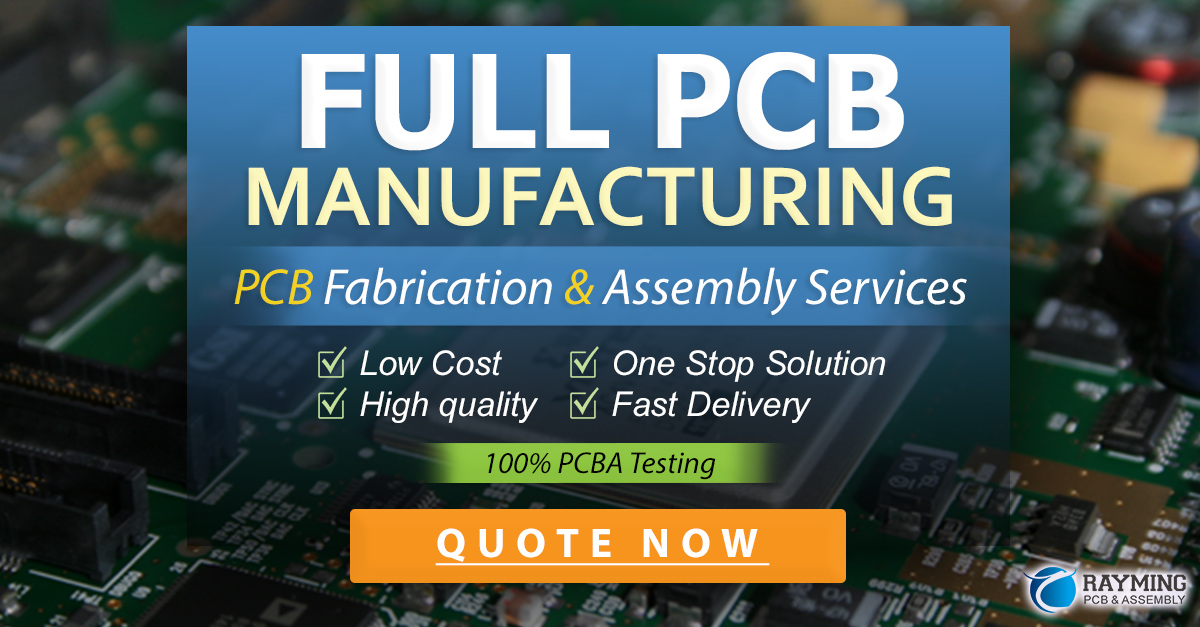
Methods for Removing Soldering Flux
There are several methods for removing soldering flux, each with its own advantages and disadvantages. The most appropriate method will depend on the type of flux used, the size and complexity of the PCB, and the available resources.
Solvent Cleaning
Solvent cleaning involves using a chemical solvent to dissolve and remove flux residue from the PCB. This method is highly effective and can be used with most types of flux. Common solvents used for flux removal include:
- Isopropyl alcohol (IPA)
- Acetone
- Denatured alcohol
- Commercial flux removers
To use this method:
- Choose an appropriate solvent based on the type of flux and the manufacturer’s recommendations.
- Apply the solvent to the PCB using a brush, spray bottle, or ultrasonic cleaner.
- Agitate the solvent to help dissolve the flux residue.
- Rinse the PCB with clean solvent to remove any remaining residue.
- Dry the PCB using compressed air or allow it to air dry.
Solvent cleaning is a versatile and efficient method for Removing Flux residue. However, it is important to use solvents in a well-ventilated area and to dispose of them properly, as they can be flammable and hazardous to the environment.
Aqueous Cleaning
Aqueous cleaning involves using water, often with added detergents or surfactants, to remove flux residue from the PCB. This method is particularly effective for water-soluble fluxes and is considered more environmentally friendly than solvent cleaning.
To use this method:
- Prepare a cleaning solution using deionized water and a suitable detergent or surfactant.
- Heat the solution to the manufacturer’s recommended temperature (typically between 140-180°F or 60-82°C).
- Immerse the PCB in the cleaning solution and agitate it to help dissolve the flux residue.
- Rinse the PCB with clean, deionized water to remove any remaining residue and detergent.
- Dry the PCB using compressed air or allow it to air dry.
Aqueous cleaning is an effective method for removing water-soluble flux residue. However, it may not be suitable for all types of PCBs, as some components or materials may be sensitive to water or high temperatures.
Abrasive Cleaning
Abrasive cleaning involves using a mechanical action to physically remove flux residue from the PCB. This method is less common than solvent or aqueous cleaning but may be useful in certain situations.
Abrasive cleaning techniques include:
- Scrubbing with a brush or abrasive pad
- Using an eraser or fibreglass pen
- Blasting with solid particles, such as baking soda or plastic beads
To use this method:
- Choose an appropriate abrasive material based on the type of flux and the PCB’s components.
- Apply the abrasive material to the PCB and gently scrub the affected areas.
- Remove any debris or residue using compressed air or a clean brush.
- Inspect the PCB for any damage or remaining residue.
Abrasive cleaning can be effective for removing stubborn flux residue, but it should be used with caution. Excessive or improper abrasive cleaning can damage the PCB or its components.
Factors to Consider When Choosing a Flux Removal Method
When selecting a method for removing soldering flux, there are several factors to consider:
-
Type of flux: The type of flux used will determine which cleaning methods are most appropriate. Water-soluble flux, for example, can be effectively removed using aqueous cleaning, while rosin flux may require solvent cleaning.
-
PCB components: Some components on the PCB may be sensitive to certain cleaning methods. For example, high temperatures used in aqueous cleaning can damage certain components, while abrasive cleaning can dislodge or scratch delicate parts.
-
Environmental considerations: Some cleaning methods, such as solvent cleaning, may have a higher environmental impact than others. It is important to consider the disposal of cleaning waste and to choose environmentally friendly options when possible.
-
Available resources: The available equipment, space, and personnel will influence the choice of cleaning method. For example, aqueous cleaning may require specialized equipment and a larger workspace compared to solvent cleaning.
-
Time and cost: The time and cost associated with each cleaning method should be considered, particularly in high-volume production environments. Some methods, such as no-clean flux, may be preferred to reduce cleaning time and costs.
By carefully evaluating these factors, manufacturers can choose the most appropriate flux removal method for their specific application, ensuring the production of high-quality, reliable PCBs.
Best Practices for Removing Soldering Flux
To achieve the best results when removing soldering flux, consider the following best practices:
-
Follow manufacturer guidelines: Always refer to the manufacturer’s recommendations for the specific flux and PCB-Material/”>PCB materials being used. They can provide guidance on the most appropriate cleaning methods and any necessary precautions.
-
Clean promptly after soldering: Flux residue is easier to remove when it is still fresh. Clean the PCB as soon as possible after soldering to prevent the flux from hardening or corroding the board.
-
Use appropriate cleaning materials: Choose cleaning solvents, detergents, and abrasives that are compatible with the type of flux and PCB components. Using inappropriate materials can lead to damage or poor cleaning results.
-
Ensure proper ventilation: When using solvent cleaning, ensure that the work area is well-ventilated to minimize exposure to fumes and prevent the buildup of flammable vapors.
-
Use the correct temperature: If using aqueous cleaning, maintain the cleaning solution at the manufacturer’s recommended temperature. Too low a temperature may not effectively remove the flux, while too high a temperature can damage components.
-
Agitate the cleaning solution: Agitating the cleaning solution, either manually or with an ultrasonic cleaner, can help to dissolve and remove flux residue more effectively.
-
Rinse thoroughly: After cleaning, rinse the PCB thoroughly with clean solvent or deionized water to remove any remaining residue and cleaning agents.
-
Dry the PCB: Use compressed air or allow the PCB to air dry completely before further processing or use. Moisture left on the board can lead to corrosion or electrical issues.
-
Inspect the PCB: After cleaning, inspect the PCB for any remaining flux residue, damage, or other issues. Address any problems before proceeding with further manufacturing steps.
-
Dispose of waste properly: Properly dispose of used cleaning solvents, detergents, and contaminated rinse water in accordance with local environmental regulations.
By following these best practices, manufacturers can ensure that their PCBs are effectively cleaned of flux residue, resulting in higher quality and more reliable products.
Common Challenges and Solutions in Flux Removal
Despite the various methods available for removing soldering flux, manufacturers may still encounter challenges in the process. Some common challenges and their solutions include:
- Stubborn or hard-to-remove flux residue:
-
Solution: Use a more aggressive cleaning method, such as a stronger solvent or abrasive cleaning. Alternatively, consider using a different type of flux that is easier to remove.
-
Damage to PCB components during cleaning:
-
Solution: Choose a gentler cleaning method, such as a milder solvent or lower temperature aqueous cleaning. Protect sensitive components with conformal coatings or masks before cleaning.
-
Incomplete removal of flux residue:
-
Solution: Increase the cleaning time, agitation, or temperature (within the manufacturer’s recommended limits). Ensure that the cleaning solution is fresh and not contaminated with dissolved flux.
-
Environmental concerns with solvent cleaning:
-
Solution: Switch to a more environmentally friendly cleaning method, such as aqueous cleaning or a biodegradable solvent. Ensure proper ventilation and disposal of cleaning waste.
-
High cost or time required for cleaning:
- Solution: Evaluate alternative flux types, such as no-clean flux, that may reduce or eliminate the need for cleaning. Invest in more efficient cleaning equipment, such as ultrasonic cleaners, to reduce cleaning time.
By addressing these challenges and implementing appropriate solutions, manufacturers can optimize their flux removal process, resulting in higher quality PCBs and improved production efficiency.
Frequently Asked Questions (FAQ)
- What happens if I don’t remove soldering flux from my PCB?
-
If soldering flux is not removed from a PCB, it can lead to various issues such as corrosion, electrical interference, and poor aesthetics. Over time, flux residue can degrade the performance and reliability of the PCB.
-
Can I use household cleaners to remove soldering flux?
-
It is not recommended to use household cleaners for removing soldering flux, as they may contain chemicals that can damage the PCB or its components. Always use cleaning agents specifically designed for electronic applications and follow the manufacturer’s guidelines.
-
How long does it take to remove soldering flux from a PCB?
-
The time required to remove soldering flux depends on the size and complexity of the PCB, the type of flux used, and the cleaning method employed. Simple PCBs cleaned with solvents may only take a few minutes, while larger boards or aqueous cleaning methods may require longer cleaning cycles.
-
Is it necessary to remove flux residue from a PCB if I used no-clean flux?
-
No-clean flux is designed to leave minimal, non-corrosive residue that does not require removal. However, in some cases, the residue may still interfere with the PCB’s performance or appearance. If required, no-clean flux residue can be removed using the same methods as other types of flux.
-
Can I reuse cleaning solvents for removing flux from multiple PCBs?
- Cleaning solvents can be reused for multiple PCBs, but their effectiveness may diminish over time as they become contaminated with dissolved flux and other residues. To ensure optimal cleaning performance, replace the solvent when it becomes visibly dirty or no longer effectively removes flux residue.
Conclusion
Removing soldering flux is a critical step in the PCB manufacturing process, as it ensures the long-term reliability, performance, and aesthetics of the finished product. By understanding the different types of flux, cleaning methods, and best practices, manufacturers can select the most appropriate approach for their specific application.
Whether using solvent cleaning, aqueous cleaning, or abrasive methods, it is essential to follow manufacturer guidelines, use compatible materials, and dispose of waste responsibly. By addressing common challenges and implementing effective solutions, manufacturers can optimize their flux removal process, resulting in higher quality PCBs and improved production efficiency.
As the electronics industry continues to evolve, it is crucial for manufacturers to stay informed about the latest developments in flux removal techniques and technologies. By adopting best practices and embracing innovation, they can remain competitive and deliver the high-quality PCBs demanded by today’s increasingly complex and demanding applications.
Flux Type | Cleaning Method | Advantages | Disadvantages |
---|---|---|---|
Rosin | Solvent | – Effective for most rosin fluxes – Fast and simple |
– Environmental concerns – Flammable solvents |
Water-Soluble | Aqueous | – Environmentally friendly – Effective for water-soluble fluxes |
– May damage sensitive components – Requires specialized equipment |
No-Clean | None (if needed, solvent or aqueous) | – Minimal residue – Reduces cleaning time and cost |
– May still require cleaning in some cases – Residue can affect performance |
No responses yet