Introduction to Halogen-Free PCBs
In recent years, there has been a growing concern about the environmental impact of electronic waste and the potential health hazards associated with the use of certain materials in the production of printed circuit boards (PCBs). One of the most significant developments in this area has been the introduction of halogen-free PCBs, which are designed to minimize the use of harmful substances and reduce the environmental impact of electronic devices.
What are Halogens?
Halogens are a group of chemical elements that include fluorine, chlorine, bromine, and iodine. These elements are highly reactive and are commonly used in the production of a wide range of products, including plastics, Flame Retardants, and electronic components. However, halogens can also be harmful to human health and the environment, particularly when they are released into the atmosphere or come into contact with water.
The Risks of Halogenated Materials in PCBs
Traditionally, PCBs have been manufactured using a variety of halogenated materials, including brominated flame retardants (BFRs) and polyvinyl chloride (PVC). These materials are used to improve the fire resistance and durability of PCBs, but they can also pose significant risks to human health and the environment.
When halogenated materials are exposed to high temperatures or come into contact with water, they can release toxic substances into the air and water supply. These substances can accumulate in the environment and in the bodies of humans and animals, leading to a range of health problems, including cancer, reproductive disorders, and developmental issues.
The Benefits of Halogen-Free PCBs
To address these concerns, many manufacturers have begun to produce halogen-free PCBs, which are designed to minimize the use of harmful substances and reduce the environmental impact of electronic devices. Halogen-free PCBs offer a range of benefits over traditional PCBs, including:
Reduced Environmental Impact
Halogen-free PCBs are manufactured using materials that are less harmful to the environment than traditional PCBs. These materials are designed to break down more easily in the environment and are less likely to release toxic substances into the air and water supply.
Improved Safety
Halogen-free PCBs are also safer for humans and animals than traditional PCBs. By minimizing the use of harmful substances, halogen-free PCBs reduce the risk of exposure to toxic chemicals and the potential for long-term health problems.
Enhanced Durability
Despite the absence of halogenated materials, halogen-free PCBs are still designed to be highly durable and resistant to damage. Many halogen-free PCBs are manufactured using high-quality materials that are able to withstand extreme temperatures, moisture, and other environmental factors.
Compliance with Environmental Regulations
Halogen-free PCBs are also designed to comply with a range of environmental regulations and standards, including the Restriction of Hazardous Substances (RoHS) directive and the Waste Electrical and Electronic Equipment (WEEE) directive. By meeting these standards, halogen-free PCBs help to ensure that electronic devices are safe for use and do not pose a risk to the environment.
Materials Used in Halogen-Free PCBs
Halogen-free PCBs are manufactured using a variety of materials that are designed to minimize the use of harmful substances and reduce the environmental impact of electronic devices. Some of the most common materials used in halogen-free PCBs include:
Polyphenylene Oxide (PPO)
Polyphenylene oxide (PPO) is a high-performance thermoplastic that is commonly used in the production of halogen-free PCBs. PPO is known for its excellent electrical properties, high heat resistance, and good dimensional stability, making it an ideal material for use in electronic components.
Polyethylene Terephthalate (PET)
Polyethylene terephthalate (PET) is another common material used in halogen-free PCBs. PET is a thermoplastic polymer that is known for its excellent mechanical and electrical properties, as well as its resistance to moisture and chemicals. PET is also recyclable, making it an environmentally friendly choice for PCB production.
Polyimide (PI)
Polyimide (PI) is a high-performance polymer that is commonly used in the production of halogen-free PCBs. PI is known for its excellent thermal and mechanical properties, as well as its resistance to chemicals and moisture. PI is also able to withstand high temperatures, making it an ideal material for use in high-performance electronic devices.
Liquid Crystal Polymer (LCP)
Liquid crystal polymer (LCP) is a high-performance thermoplastic that is commonly used in the production of halogen-free PCBs. LCP is known for its excellent electrical properties, low moisture absorption, and high heat resistance, making it an ideal material for use in electronic components.
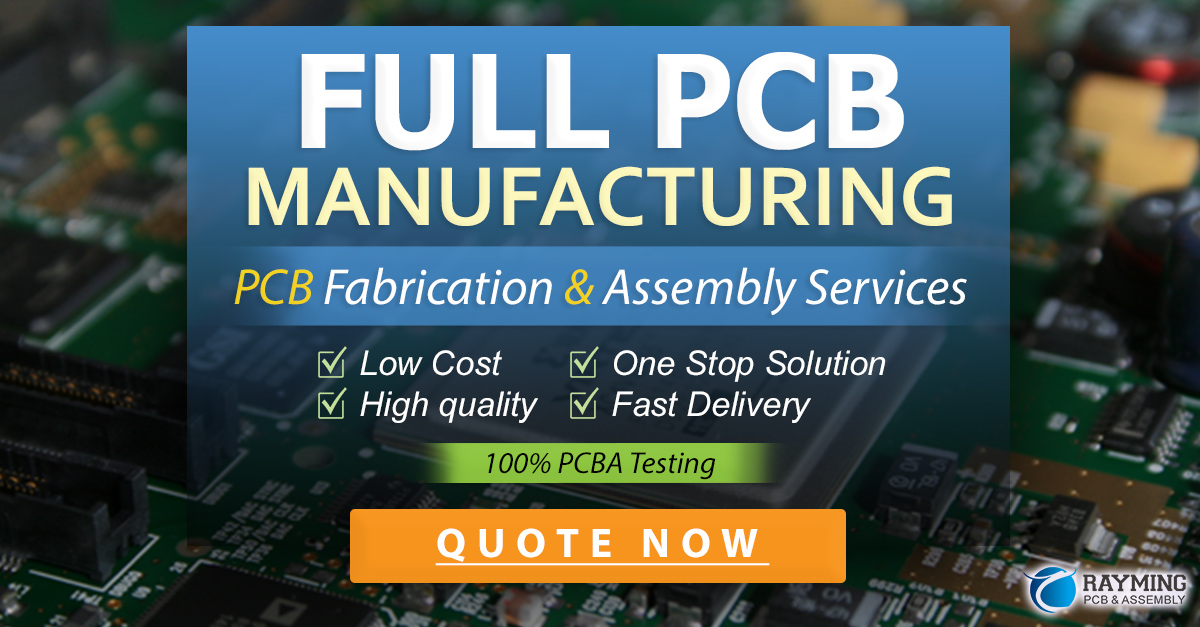
Applications of Halogen-Free PCBs
Halogen-free PCBs are used in a wide range of electronic devices and applications, including:
Consumer Electronics
Halogen-free PCBs are commonly used in the production of consumer electronics, such as smartphones, tablets, and laptops. These devices are subject to strict environmental regulations and must be designed to minimize the use of harmful substances.
Automotive Electronics
Halogen-free PCBs are also used in the production of automotive electronics, such as engine control units, infotainment systems, and safety features. These components must be able to withstand extreme temperatures and environmental conditions, making halogen-free PCBs an ideal choice.
Medical Devices
Halogen-free PCBs are increasingly being used in the production of medical devices, such as implantable devices and diagnostic equipment. These devices must be designed to minimize the risk of exposure to harmful substances and ensure patient safety.
Industrial Equipment
Halogen-free PCBs are also used in the production of industrial equipment, such as automation systems, control panels, and power supplies. These components must be able to withstand harsh environmental conditions and provide reliable performance over an extended period of time.
Challenges and Considerations
While halogen-free PCBs offer a range of benefits over traditional PCBs, there are also some challenges and considerations that must be taken into account when designing and manufacturing these components. Some of the most significant challenges and considerations include:
Material Selection
Selecting the right materials for halogen-free PCBs can be challenging, as these materials must be able to provide the necessary performance and durability while also meeting environmental regulations and standards. Manufacturers must carefully consider the properties of each material and select the best option for each specific application.
Manufacturing Processes
Manufacturing halogen-free PCBs can also be challenging, as these components often require specialized equipment and processes. Manufacturers must ensure that their production processes are optimized for the specific materials and requirements of halogen-free PCBs, and must also be able to meet strict quality control standards.
Cost Considerations
Halogen-free PCBs can be more expensive to manufacture than traditional PCBs, due to the specialized materials and processes required. Manufacturers must carefully consider the cost implications of using halogen-free PCBs and ensure that they are able to provide a cost-effective solution for their customers.
Performance and Reliability
While halogen-free PCBs are designed to provide high performance and reliability, there may be some trade-offs in terms of electrical and mechanical properties compared to traditional PCBs. Manufacturers must carefully evaluate the performance and reliability requirements of each specific application and select the best materials and design options to meet these requirements.
The Future of Halogen-Free PCBs
As environmental regulations and consumer demand for sustainable products continue to grow, it is likely that the use of halogen-free PCBs will continue to increase in the coming years. Manufacturers will need to continue to innovate and develop new materials and processes to meet these demands, while also ensuring that their products are able to provide the necessary performance and reliability.
Some of the key trends and developments that are likely to shape the future of halogen-free PCBs include:
Advancements in Materials Science
As new materials and manufacturing processes are developed, it is likely that the performance and durability of halogen-free PCBs will continue to improve. Researchers are currently exploring a range of new materials, such as bio-based polymers and conductive inks, that could potentially be used in the production of halogen-free PCBs.
Increased Adoption of Sustainable Practices
As consumers and regulators continue to demand more sustainable products and practices, it is likely that the use of halogen-free PCBs will become increasingly common across a range of industries. Manufacturers will need to adopt sustainable practices throughout their supply chains and production processes to meet these demands.
Integration with Other Technologies
Halogen-free PCBs are likely to be increasingly integrated with other technologies, such as sensors, antennas, and power management systems, to create more advanced and sustainable electronic devices. Manufacturers will need to develop new design and integration strategies to ensure that these components are able to work together seamlessly.
Collaboration and Standardization
As the use of halogen-free PCBs becomes more widespread, it is likely that there will be increased collaboration and standardization across the industry. Manufacturers, suppliers, and regulators will need to work together to develop common standards and best practices for the design, production, and disposal of halogen-free PCBs.
FAQs
-
What are the benefits of using halogen-free PCBs?
Halogen-free PCBs offer several benefits, including reduced environmental impact, improved safety, enhanced durability, and compliance with environmental regulations. -
What materials are commonly used in halogen-free PCBs?
Common materials used in halogen-free PCBs include polyphenylene oxide (PPO), polyethylene terephthalate (PET), polyimide (PI), and liquid crystal polymer (LCP). -
In what applications are halogen-free PCBs commonly used?
Halogen-free PCBs are commonly used in consumer electronics, automotive electronics, medical devices, and industrial equipment. -
Are halogen-free PCBs more expensive than traditional PCBs?
Yes, halogen-free PCBs can be more expensive to manufacture than traditional PCBs due to the specialized materials and processes required. -
What are some of the challenges associated with manufacturing halogen-free PCBs?
Some of the challenges associated with manufacturing halogen-free PCBs include material selection, specialized manufacturing processes, cost considerations, and potential trade-offs in performance and reliability.
Conclusion
Halogen-free PCBs represent a significant step forward in the development of sustainable and environmentally friendly electronic devices. By minimizing the use of harmful substances and reducing the environmental impact of electronic waste, halogen-free PCBs are helping to create a more sustainable future for the electronics industry.
While there are certainly challenges and considerations associated with the design and manufacture of halogen-free PCBs, the benefits of these components are clear. As environmental regulations and consumer demand for sustainable products continue to grow, it is likely that the use of halogen-free PCBs will become increasingly common across a range of industries and applications.
Ultimately, the success of halogen-free PCBs will depend on the ability of manufacturers, suppliers, and regulators to work together to develop innovative solutions and best practices that meet the evolving needs of the electronics industry. By prioritizing sustainability, performance, and reliability, the industry can continue to drive progress and create a more sustainable future for all.
No responses yet